Практика дао Toyota. Руководство по внедрению принципов менеджмента Toyota Лайкер Джеффри
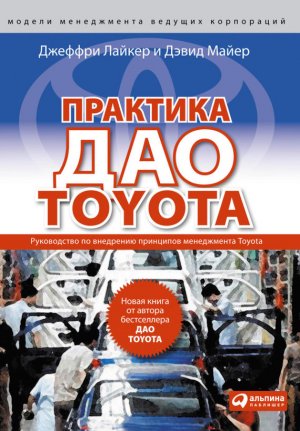
Читать бесплатно другие книги:
«… Но вот однажды … кто-то постучал в дверь моей прихожей. Я крикнул: кто там? – но ответа не послед...
«… Чиновник казенной палаты, вдовец, пожилой, женился на молоденькой, на красавице, дочери воинского...
«… – Ну и слух же у вас!– Зато я знаменитый живописец. И красив, как Леонид Андреев. На беду вашу за...
«Она вошла на маленькой станции между Марселем и Арлем, прошла по вагону, извиваясь всем своим цыган...
«Приехав в Москву, я воровски остановился в незаметных номерах в переулке возле Арбата и жил томител...
«… – Я прижался за елью, и они не видали меня, – горячо говорил Гришка, выкатывая глаза, – а я все в...