Сварочные работы. Практический справочник Кашин Сергей
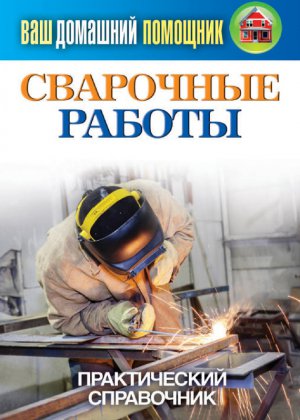
Рис. 15. Обозначение пространственных положений швов: 1 – потолочное; 2 – горизонтальное; 3 – вертикальное сверху вниз; 4 – нижнее; 5 – наклонное для угловых и тавровых соединений; 6 – вертикальное снизу вверх
7. По роду тока, его полярности и номинальному напряжению холостого хода источника переменного тока, что отображено в табл. 6. Таблица 6. КЛАССИФИКАЦИЯ СВАРОЧНЫХ ЭЛЕКТРОДОВ ПО РОДУ ТОКА И СВЯЗАННЫМ С НИМ ХАРАКТЕРИСТИКАМ
Для работы с разными материалами предназначаются определенные типы электродов (табл. 7).
Таблица 7. ОБЛАСТЬ ПРИМЕНЕНИЯ НЕКОТОРЫХ МАРОК ЭЛЕКТРОДОВ
Электродные покрытия многофункциональны, поскольку:
– делают горение сварочной дуги стабильным;
– защищают сварочную ванну от кислорода и азота, содержащихся в атмосферном воздухе;
– нейтрализуют некоторые примеси;
– улучшают свойства металла шва, вводя в него легирующие вещества;
– дают такие виды шлаков, физические свойства которых должны способствовать нормальному образованию сварного шва и обеспечивать комфортное манипулирование электродом.
К покрытию предъявляются определенные требования, в частности:
– металл, газы и шлаки не должны вступать в реакции, которые могут привести к появлению в сварном шве пор;
– материалы, из которого состоят покрытия, должны поддаваться измельчению и не должны взаимодействовать с жидким стеклом или друг с другом в замесе;
– состав покрытий должен быть таким, чтобы не нарушать санитарно-гигиенические условия труда при изготовлении электродов и в процессе сварки.
Нанесение покрытия на электрод возможно двумя способами – опрессовкой и окунанием (в последние годы чаще всего применяется первый вариант).
Обмазка, которая наносится на электроды, содержит целый ряд компонентов, а именно:
1) шлакообразующие, к которым относятся марганцевая руда, каолин, мел, титановый концентрат, полевой шпат, рутил, кварцевый песок, доломит, мрамор. Их функции:
– защита металла сварочной ванны и капель электродного металла от воздействия содержащихся в атмосферном воздухе кислорода и азота;
– снижение скорости охлаждения металла шва;
– рафинирование и удаление неметаллических примесей и включений;
2) раскисляющие, среди которых представлены марганец, алюминий, титан, кремний, графит и другие элементы, отличающиеся большим сродством к кислороду, чем железо. Их функция – раскисление (восстановление) металла сварного шва. Данные вещества включаются в электродное покрытие в составе ферросплавов;
3) газообразующие, в задачу которых входит создание защитной газовой оболочки вокруг дуги. В процессе сгорания они выделяют большое количество газов, которые и создают необходимую среду. Это органические вещества – древесная мука, целлюлоза, декстрин, крахмал;
4) легирующие, которые должны придать металлу шва заданные физико-механические свойства (повышенную сопротивляемость коррозии, износо– и жаростойкость, особую механическую прочность). Легирующими элементами являются хром, молибден, марганец, никель, титан и др.;
5) стабилизирующие (или ионизирующие), т. е. элементы с невысоким потенциалом ионизации, благодаря которому поддерживается устойчивое горение сварочной дуги и облегчается ее возбуждение. Данную группу элементов составляют калий, натрий и кальций;
6) связующие (клеящие), которые в соответствии с собственным названием связывают компоненты покрытия как друг с другом, так и со стержнем электрода. Чаще всего используется жидкое стекло (калиевое или натриевое), хотя с этой целью также применяются декстрин, желатин и др.
Электрод при сварке расплавляется с образованием металла и шлака. Последний должен обладать определенными свойствами:
1) физическими, к которым относятся:
– температура плавления;
– температурный интервал затвердевания;
– теплоемкость;
– теплосодержание;
– способность растворять окислы, сульфиды и др.;
– вязкость;
– плотность;
– газопроницаемость;
– коэффициенты линейного и объемного расширения;
2) химическими, а именно способностью:
– раскислять и легировать металл сварочной ванны;
– связывать окислы в легкоплавкие соединения.
От физических свойств шлаков во многом зависят сам процесс сварки и образование сварного шва. Электродные покрытия дают шлаки такой плотности, которая ниже плотности металла сварочной ванны. Благодаря этому шлаки всплывают и ровным слоем покрывают поверхность шва. Кроме того, поскольку температурный интервал их затвердевания ниже температуры кристаллизации расплавленного металла сварочной ванны, это позволяет газам свободно выделяться из нее.
Электродные покрытия, расплавляясь, дают шлаки двух видов:
– «длинные», в состав которых входит большое количество кремнезема. Поскольку при охлаждении их вязкость возрастает медленно, электроды с таким покрытием не применяются для выполнения вертикальных и потолочных швов, так как на этих плоскостях сварочная ванна долго сохраняет жидкое состояние;
– «короткие», вязкость которых при охлаждении нарастает быстро, что не позволяет жидкому металлу шва стекать. Они, в отличие от предыдущих, пригодны для сварки в любых пространственных положениях. Электроды с рутиловым и основным покрытием образуют шлаки именно такого типа.
Шлаковая корка, которая появляется на поверхности сварного шва, будет хорошо отделяться от металла, если коэффициенты линейного расширения шлака и металла будут различны.
В технической документации согласно ГОСТу 946675 указаны марка, диаметр и группа электрода (например, УОНИ-13/45-3,0–2 ГОСТ 9466-75), на упаковочной таре сведения о материале представлены более подробно. Структура условного обозначения электродов имеет вид дроби (в числителе – паспортные данные, в знаменателе – код) и включает одиннадцать обозначений (рис. 16).
Рис. 16. Схема условного обозначения электродов: 1 – тип электрода; 2 – марка электрода; 3 – диаметр электрода; 4 – назначение электрода; 5 – коэффициент толщины покрытия; 6 – группа индексов, характеризующих металл; 7 – вид покрытия; 8 – допустимые пространственные положения; 9 – род тока; 10 – стандарт на структуру условного обозначения (ГОСТ 9466-75); 11 – стандарт на тип электрода (ГОСТ 9476-75, ГОСТ 10051-75, ГОСТ 10052-75)
Например,
Данная надпись расшифровывается так:
– Э46 А – тип электрода (отличительные особенности: улучшенная пластичность, повышенная вязкость металла шва, прочностная характеристика – 460 МПа);
– УОНИ-13/45 – марка электрода;
– 3,0 мм – диаметр электрода;
– У – назначение электрода (для сварки углеродистых и низколегированных сталей);
– Д – толщина покрытия (толстое);
– 2 – номер группы;
– Е432 (5) – группа индексов (характеристика металла шва по ГОСТу 9467-75);
– Б – вид покрытия (основное);
– 1 – допустимые пространственные положения (в любых положениях);
– 0 – род тока (постоянный обратной полярности).Флюсы
Сварочный флюс представляет собой сложное по химическому составу вещество, которое может иметь форму порошка, гранул или жидкой пасты. Необходимость его применения продиктована тем, что при расплавлении он начинает выделять газы, которые, как в оболочку, заключают фронт работ (зону действия электрода, сварочной дуги и свариваемого металла), защищая его от атмосферного воздуха.
Подобная изоляция дает возможность получить наилучший по своим характеристикам сварной шов и делает его более эргономичным (гладким, с правильными ровными краями), не требующим дополнительной обработки. Кроме того, флюс, предупреждая разбрызгивание металла, защищает сварщика, что важно с точки зрения соблюдения требований техники безопасности.
Наименование марки флюса обязательно включает в себя буквенное обозначение, указывающее создателя данного материала, и цифровое – порядковый номер. Например, флюсы, в названии которых имеется аббревиатура «АН» – «Академия наук» (АН-348 А, АН-20 и др.), указывают на то, что они разработаны в Институте электросварки им. Е. О. Патона; аббревиатура «ФЦ» принадлежит НПО ЦНИИТМАШ.
Буквы «А» и «Ш» на конце указывают на крупную или мелкую грануляцию флюса соответственно. Предпринимались также попытки представить в названии флюса с помощью соответствующего индекса его состав (например, для основных флюсов – ОФ6, ОФ10, для кислого – КФ16, для нейтрального – НФ17 и др.), но они не были поддержаны разработчиками флюсов.
Применение флюсов представлено в табл. 8.
Таблица 8. СФЕРА ПРИМЕНЕНИЯ НЕКОТОРЫХ СВАРОЧНЫХ ФЛЮСОВ
Как и другие сварочные материалы, флюсы можно классифицировать по различным признакам.
1. По функциям. Флюсы должны:
– способствовать устойчивому горению сварочной дуги;
– предохранять металл сварочной ванны от воздействия атмосферного воздуха;
– снижать скорость охлаждения металла сварного шва, участвовать в его формировании, обеспечивать необходимое его качество за счет легирующих веществ, выполнять металлургические функции, т. е. давать шов соответствующего химического состава;
– восстанавливать окислы;
– разжижать и уменьшать температуру шлаков;
– снижать потери электродного металла.
2. По назначению. Флюсы используются для сварки:
– углеродистых и низколегированных сталей;
– высоколегированных сталей;
– цветных металлов и их сплавов.
3. По способу изготовления. Флюсы делятся на:
– плавленые (табл. 9). Для производства флюсов данной группы составляющие его компоненты (марганцевую руду, доломит, мел и др.) измельчают, смешивают в определенной пропорции и помещают в печь. Как только они расплавятся, массу выпускают в проточную воду, где та охлаждается и распадается на мелкие частицы. В заключение флюс сушат при температуре 300–350 °C и просеивают;
Таблица 9. ХИМИЧЕСКИЙ СОСТАВ НЕКОТОРЫХ ПЛАВЛЕНЫХ ФЛЮСОВ
– неплавленые (керамические) (табл. 10). Такие флюсы получают следующим образом: тщательно измельченные вещества соединяют в определенном соотношении и перемешивают с раствором жидкого стекла. Тестообразную массу, образовавшуюся после этого, пропускают сквозь сито с необходимым размером ячеек, затем полученные гранулы сначала высушивают в течение 15–20 минут при температуре 150 °C, а потом прокаливают при 300–350 °C.
Таблица 10. ХИМИЧЕСКИЙ СОСТАВ НЕКОТОРЫХ НЕПЛАВЛЕНЫХ ФЛЮСОВ
Неплавлеными керамическими флюсами легче легировать металл шва – достаточно добавить в их состав определенное количество легирующих компонентов в виде минеральных веществ, ферросплава.
Керамические флюсы, в отличие от плавленых, не столь требовательны к кромке свариваемых деталей и конструкций, т. е. они не слишком чувствительны к ржавчине, окалине и влаге, что важно при осуществлении работ под открытым небом.
4. По строению частиц. Различаются флюсы:
– стекловидные;
– пемзовидные;
– цементированные.
5. По степени легирования металла шва. По этому признаку флюсы делятся на:
– активные, которые, в свою очередь, подразделяются на слабо и сильно легирующие металл шва;
– пассивные, т. е. не взаимодействующие с металлом сварочной ванны.
6. По химическому составу. Флюсы бывают:
1) оксидными, в состав которых входят оксиды металлов. Кроме того, содержание фторидных соединений в них может достигать 10 %. По содержанию кремния и марганца флюсы подразделяются на:
– бескремнистые (количество кремнезема не превышает 5 %);
– низкокремнистые (менее 35 % кремнезема);
– высококремнистые (содержание кремнезема составляет 35–50 %);
– безмарганцевые (они имеют в составе менее 1 % марганца);
– марганцевые (на марганец приходится более 1 %), а именно: низко– (менее 10 %), средне– (10–30 %) и высокомарганцевые (более 30 %);
– легированные, которые включают чистые легирующие металлы или ферросплавы;
2) солеоксидными (смешанными), в которых преобладают соли, а не оксиды, как в предыдущей группе. Содержание кремния в них достигает 15–30 %, марганца – 1–9 %, фторида кальция – 12–30 %;
3) солевыми, основную часть в составе которых составляют хлориды и фториды кальция, натрия, бария и др. Они предназначаются для сварки активных металлов.
7. По химической активности. Это важная характеристика флюса, которая определяется по его суммарной окислительной способности. Показатель активности флюса – относительная величина Аф, значение которой варьируется от 0 до 1. По данному признаку различаются флюсы:
– высокоактивные (Аф больше 0,6);
– активные (Аф от 0,3 до 0,6);
– малоактивные (Аф от 0,1 до 0,3);
– пассивные (Аф меньше 0,1).
Для автоматической наплавки под флюсом используются те же составы, что и для сварки. Наибольшее распространение получили плавленые флюсы АН-348 А, АН-20, АН-60, 48-ОФ-6, АН-15 М, АН-25, ОСЦ-45, АН-22, АНФ-6 в комбинации с легированными проволоками.
Защитные газы
Чтобы получить качественный сварной шов при дуговой сварке, необходимо обеспечить защиту расплавленного металла сварочной ванны. Именно с такой целью используются защитные газы. Эта идея была высказана Н. Н. Бенардосом еще в 1883 г. и состояла в том, чтобы направить из сопла горелки на зону сварки струю газа, которая, как будто в оболочку, заключит зону сварки и предохранит ее от постороннего воздействия. Защита осуществляется тремя группами газов:
– инертными;
– активными;
– смесями активных газов с инертными или инертных с инертными.
Инертными называются газы, которые не вступают в химические реакции взаимодействия с металлом и неспособны растворяться в нем. К этой группе относятся аргон, гелий и их смеси, а для меди используется азот. В среде инертных газов сваривают активные металлы, например титан, алюминий и др. Применяют их и в тех случаях, когда хотят добиться высококачественного шва при соединении изделий и конструкций из хромоникелевых сталей.
Аргон представляет собой газ со следующими физическими характеристиками:
– бесцветный;
– без запаха и вкуса;
– неядовитый;
– невзрывоопасный.
Поскольку аргон примерно в 1,5 раза тяжелее воздуха, если производить сварочные работы в закрытом и непроветриваемом помещении, тогда возникает опасность удушья. В природе он встречается исключительно в свободном виде, его объемная концентрация в воздухе составляет приблизительно 0,93 %.
В промышленности в соответствии с ГОСТом 1015779 производится аргон трех сортов:
– высшего (доля аргона – 99,993 %);
– первого (99,987 %);
– второго (99,95 %).
Аргон транспортируется в жидком (плотность – 1392 кг/м3) или газообразном (плотность – 1,662 кг/м3) состоянии в специальных стальных баллонах объемом 40 л под давлением 15 МПа. Емкости окрашены в серый цвет с зеленой полосой. На них зеленой краской нанесена надпись «Аргон чистый».
Расход газа при сварке определяется диаметром электрода и, как правило, составляет 100–500 л/ч.
Гелий в качестве защитного газа применяется редко, поскольку, будучи дефицитным, имеет высокую стоимость. Поэтому чаще всего его вводят в виде добавки к аргону или используют для сварки:
– химически чистых и активных материалов и сплавов;
– сплавов на основе магния и алюминия;
– при необходимости обеспечить значительную глубину проплавления (это возможно за счет высокого значения потенциала ионизации газа) или особую форма сварного шва.
Физические свойства гелия:
– бесцветный;
– без запаха;
– неядовитый
– плотность – 0,18 кг/м3.
Гелий в 10 раз легче аргона, а объемное содержание этого газа в воздухе составляет 0,00052 %.
Промышленность поставляет гелий согласно ТУ 51-68975 трех марок – А, Б и В. Его транспортировка осуществляется в соответствии с ГОСТом 20461-75. При этом газ находится в стальных баллонах под давлением 15 МПа, которые окрашены в коричневый цвет, а на них нанесена белая надпись «Гелий».
Расход гелия в процессе сварки – 200–900 л/ч, потому что легкий гелий быстро улетучивается, а для создания надежной защиты сварочной ванны приходится увеличивать его подачу.
Азот не является инертным газом (в природе это самый распространенный газ, в частности его содержание в воздухе составляет 78,09 %), но он так ведет себя по отношению к меди и ее сплавам (относительно других металлов и стали азот рассматривается как активный и часто вредный газ, поступление которого в сварочную ванну необходимо ограничивать). Поэтому его используют для сварки, наплавки и плазменной резки таких материалов.
Физические свойства азота:
– бесцветный;
– без запаха и вкуса;
– неядовитый;
– невзрывоопасный;
– плотность – 1,2506 кг/м3.
По ГОСТу 9293-74 агрегатное состояние азота при транспортировке – газ. Его перевозят в стальных емкостях объемом 40 л под давлением 15 МПа. Он поставляется четырех сортов, различающихся процентным содержанием азота:
– высший (99,9 %);
– I сорт (99,5 %);
– II сорт (99 %);
– III сорт (97 %).
Стальные емкости объемом 40 л содержат азот под давлением 15 МПа.
Из активных газов, т. е. взаимодействующих с металлом сварочной ванны и растворяющихся в нем, следует назвать углекислый газ, который применятся для защиты сварки в чистом виде или в смеси с аргоном. Помимо жидкого и газообразного состояния, углекислый газ бывает и твердым (сухой лед).
Физические свойства двуокиси углерода:
– бесцветная;
– неядовитая;
– с кисловатым запахом и вкусом;
– плотность – 1,98 кг/м3;
– температура сжижения – 78,5 °C.
Углекислый газ в 1,6 раза тяжелее воздуха, в котором на его долю приходится 0,03 %.
По ГОСТу 8050-85 двуокись углерода содержит водяные пары, количество которых зависит от сорта газа:
– в высшем – 0,037 г/см3;
– в I сорте – 0,184 г/см3.
Углекислый газ транспортируется и поставляется в сжиженном состоянии в емкостях объемом 40 л при максимальном давлении 20 МПа. Баллон покрыт черной краской и снабжен надписью желтого цвета «CO2 сварочный».
Углекислота производится двух сортов: высшего, чистота которого составляет 99,8 %, и I сорта чистотой 99,5 %.
Поступающий в зону сварки углекислый газ не относится к нейтральным и под воздействием высоких температур распадается на оксид углерода и кислород. Одновременно с этим происходит окисление расплавленного металла, который после кристаллизации дает достаточно пористый шов с низкими механическими характеристиками. Чтобы снизить окислительные свойства свободного кислорода и добиться качественного шва, используют электродную проволоку с повышенным содержанием кремния и марганца, которые действуют как раскислители.
Для удаления водяных паров, которые присутствуют в баллоне с газом, емкость следует поставить вентилем вниз и через 10–15 минут осторожно его открыть. А перед сваркой из установленного как положено баллона надо выпустить воздух.
На производстве часто применяют смеси газов, что значительно повышает качество сварного шва, и нередко технологические свойства смеси превосходят показатели чистых газов. Например, используются следующие смеси:
1. Углекислый газ с 2–5 % кислорода. Эта смесь, во-первых, способствует мелкокапельному переносу металла; во-вторых, примерно на 30 % снижает разбрызгивание и потери металла; в-третьих, обеспечивает формирование качественного сварного шва.
2. 70 % гелия и 30 % аргона. Данная смесь, во-первых, значительно повышает производительность при сварке алюминия; во-вторых, увеличивает необходимую в определенных случаях глубину проплавления; в-третьих, дает сварной шов хорошего качества;
3. 88 % аргона и 12 % углекислого газа. Эта смесь, во-первых, при сварке стали делает горение сварочной дуги стабильным; во-вторых, снижает разбрызгивание расплавленного металла; в-третьих, позволяет получить качественный шов, поскольку значительно уменьшает поверхностное натяжение расплавленной электродной проволоки.
Резюмируя сказанное, следует подчеркнуть достоинства сварки в среде защитных газов:
– наличие визуального контроля сварочного процесса;
– широкий выбор рабочих режимов;
– расширение номенклатуры свариваемых металлов;
– возможность механизировать процесс;
– создание лучших условий труда для сварщиков.
Источники питания
Качественного сварного шва невозможно добиться без обеспечения стабильного горения сварочной дуги, т. е. без устойчивого протекания сварочного процесса. В значительной степени это зависит от источника питания дуги, которая загорается при коротком замыкании – в момент контакта электрода с изделием. Это сопровождается выделением теплоты и быстрым повышением температуры в зоне контакта.
Для начала сварочного процесса требуется повышенное напряжение сварочного тока, но потом в результате эмиссии электронов с катода и развития объемной ионизации газов в сварочной дуге наблюдаются снижение сопротивления дугового промежутка и, как следствие, падение напряжения до того минимума, который необходим для устойчивого горения сварочной дуги.
Сварочная цепь переживает многократные и частые короткие замыкания, которыми сопровождается переход капель металла электрода в сварочную ванну. И в каждый такой момент напряжение достигает нулевой отметки. Одновременно с этим колеблется длина сварочной дуги. Чтобы она восстановилась, надо, чтобы напряжение поднялось до рабочего, т. е. до 25–30 В, причем в минимальный промежуток времени, иначе поддерживать горение сварочной дуги будет невозможно. Кроме того, надо иметь в виду, что при коротких замыканиях возникают большие токи, которые могут привести к перегреву проводки и обмотки источников тока. Таковы в общих чертах сварочный процесс и явления, которые ему сопутствуют.
Итак, электрическая сварочная дуга, по сравнению с другими потребителями электроэнергии, имеет ряд отличительных черт:
– необходимость более высокого напряжения для возбуждения сварочной дуги по сравнению с тем, которое требуется для ее поддержания;
– наличие в процессе горения сварочной дуги особого состоянии электрической цепи, которая претерпевает разрыв или короткое замыкание;
– колебания напряжения сварочной дуги и, соответственно, силы сварочного тока в связи с изменением длины дуги;
– падение напряжения между электродом и свариваемым изделиями до нуля при коротком замыкании, в момент которого происходит возбуждение сварочной дуги.
Специфическими особенностями сварочной дуги при ручной дуговой сварке (при других видах дуговой сварки они могут быть иными) обусловлены те требования, которые предъявляются к источникам питания, в частности:
– для возбуждения сварочной дуги нужно, чтобы напряжение холостого хода превосходило напряжение сварочной дуги в 2–3 раза (максимум напряжения холостого хода должен быть не более 80 и 90 В для источников питания постоянного и переменного тока соответственно), но при этом оставалось безопасным для сварщика (разумеется, при соблюдении им техники безопасности);
– изменение напряжения устойчивого горения дуги (рабочее напряжение), наблюдающееся при изменении ее длины (при увеличении последней напряжение должно возрастать, а при уменьшении – быстро снижаться), не должно приводить к большим изменениям силы сварочного тока и связанного с этим теплового режима сварки;
– в момент короткого замыкания сила тока должна быть ограничена определенным пределом, предотвращающим возгорание проводов. Достаточно, чтобы ток короткого замыкания превышал сварочный примерно в 1,1–1,5 раза, т. е. не более чем на 40–50 %. Источник тока должен быть рассчитан и выдерживать длительные короткие замыкания, иначе он не сможет защищать обмотку от перегрева и разрушения;
– промежуток, в течение которого напряжение после короткого замыкания восстанавливается, не должен быть длительным. Необходимо, чтобы после каждого короткого замыкания, т. е. при переносе капель расплавленного металла электрода на свариваемое изделие, на подъем напряжения от нуля до рабочего (25 В) затрачивалось не более 0,05 секунды, более длительный промежуток негативно сказывается на устойчивости сварочной дуги;
– источник тока должен быть мощным, чтобы обеспечивать выполнение сварочных работ и иметь соответствующую внешнюю характеристику;
– источник питания дуги должен быть оснащен устройством, регулирующим сварочный ток (предел регулирования должен составлять приблизительно 30-130 % от номинального сварочного тока), тем более что это требуется для осуществления сварки электродами различного диаметра.
Источники питания отличаются своими свойствами, для описания которых введены следующие параметры:
1. Внешняя статическая характеристика. Это зависимость между напряжением на выходных зажимах источника питания и величиной сварочного тока. Различаются несколько типов внешних вольт-амперных характеристик источников питания (рис. 17), в частности:
– крутопадающая;
– пологопадающая;
– жесткая;