Сварка Банников Евгений
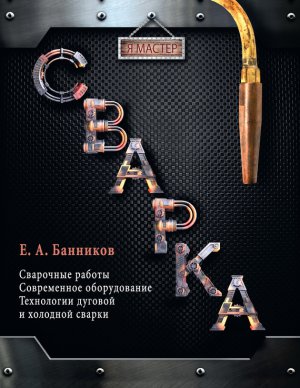
Короткое замыкание (рис. 4а) выполняется для разогрева торца электрода 1 и заготовки 2 в зоне контакта с электродом. После отвода электрода (рис. 4б) с его разогретого торца (катода) под действием электрического поля начинается термоэлектрическая эмиссия электронов 3.
Столкновение быстро движущихся по направлению к аноду электронов с молекулами газов и паров металла приводит к их ионизации 4. По мере разогрева столба дуги и повышения кинетической энергии атомов и молекул происходит дополнительная ионизация за счет их содарения. В результате дуговой промежуток становится электропроводным и через него начинается разряд электричества. Процесс зажигания дуги (рис. 4в) заканчивается возникновением устойчивого дугового разряда 6 с возникновением катодной области 5 и анодной области 7.
Рис. 4.
Схема процесса зажигания дуги
Возможно зажигание дуги без короткого замыкания и отвода электрода с помощью высокочастотного электрического разряда через дуговой промежуток, обеспечивающий его первоначальную ионизацию. Для этого в сварочную цепь подключают на короткое время источник высокочастотного переменного тока высокого напряжения (осциллятор).
В зависимости от длины дугового разряда различают:
• короткую дугу, если ее длина 2–4 мм;
• нормальную дугу, если ее длина 4–6 мм;
• длинную дугу, при ее длине более 6 мм.
Оптимальный режим сварки обеспечивается при короткой дуге. При длинной дуге процесс сварки протекает неравномерно, с неустойчивым горением и разбрызгиванием металла. Металл, проходя через дуговой промежуток, больше окисляется и азотируется.
Специалисты рекомендуют длину дуги определять по звуку, издаваемому ею при горении. Дуга нормальной длины издает менее громкий и равномерный звук. Длинная дуга издает неравномерный и потрескивающий, более громкий звук, что легко определяется опытным путем.
Различают технологические условия горения дуги, такие как зажигание, чувствительность к изменениям длины в определенных пределах, быстрое повторное зажигание после обрыва и необходимое проплавление металла.
Условия зажигания электрической дуги:
• наличие электрического источника питания дуги достаточной мощности, позволяющего быстро нагреть катод до высокой температуры при возбуждении дуги;
• наличие ионизации столба дуги (в электрод вводятся элементы с низким потенциалом ионизации или применяют осцилляторы для возбуждения дуги);
• стабилизация горения столба дуги (например, вводят дроссель в цепь питания). Зависимость напряжения дуги от тока в сварочной цепи называют статической вольт-амперной характеристикой дуги.
Вольт-амперная характеристика дуги имеет три области (рис. 5):
• падающая область I (при токах до 100 А);
• жесткая область II (при токах 100–1000 А);
• возрастающая область III (при токах свыше 1000 А).
Напряжение, необходимое для возбуждения дуги, зависит от рода тока (переменный или постоянный), дугового промежутка, материала электрода и его покрытия, свариваемого металла.
Дуга с падающей характеристикой (I) малоустойчива и имеет ограниченное применение, т. к. требует включения в сварочную цепь осциллятора.
Рис. 5.
Статическая вольт-амперная характеристика дуги
Самое широкое применение нашла дуга с жесткой (II) и возрастающей (III) характеристикой. Каждому участку дуги соответствует определенный характер переноса расплавленного электродного металла в сварочную ванну:
• I и II участок – крупнокапельный,
• III участок – мелкокапельный или струйный.
Для сохранения неизменного напряжения на дуге необходимо длину дуги поддерживать постоянной.
Материалы и оборудование для производства работ электродуговой сваркой:
• источник питания сварочной дуги;
• сварочный и питающий кабели, электрододержатель;
• принадлежности сварщика – спецкостюм, маска с защитным стеклом;
• сварочный стол или приспособления для сборки и фиксации деталей;
• инструменты для измерения и разметки;
• инструменты для зачистки швов и удаления шлаковой корки;
• средства пожаротушения.
Преимущества электродуговой сварки:
• высокая технологичность процесса;
• возможность автоматизации и механизации процессов сварки;
• меньшая по сравнению с газовой сваркой зона термического влияния;
• простота регулирования процесса сварки;
• дешевые расходные материалы (электроды);
• высокая скорость соединения деталей.
Недостатки электродуговой сварки:
• необходимость использования специальных сварочных трансформаторов или инверторов (преобразователей);
• энергозависимость (необходима электрическая сеть или генераторы);
• подготовка деталей для сборки (разделка кромок, фиксация элементов).
Электрошлаковая сварка (ЭШС)
При электрошлаковой сварке основной и электродный металлы расплавляются теплотой, выделяющейся при прохождении электрического тока через шлаковую ванну. Шлак представляет собой расплавленный, обладающий электропроводностью флюс. Процесс электрошлаковой сварки (рис. 6) начинается с образования шлаковой ванны (4) в пространстве между кромками основного металла (1) и формирующими устройствами (3) типа ползунов или пластин, охлаждаемыми водой, путем расплавления флюса электрической дугой, возбуждаемой между сварочной проволокой (2) и вводной планкой (6).
После накопления определенного количества жидкого шлака дуга шунтируется шлаком и гаснет, а подача проволоки и подвод тока продолжаются. При прохождении тока через расплавленный шлак, являющийся токопроводящим электролитом, в нем выделяется теплота, достаточная для поддержания высокой температуры шлака – до 2000 °C и расплавления основного металла и электродной проволоки. За счет разницы в плотности электродный металл (плотность жидкого металла значительно больше плотности компонентов шлака) опускается на дно расплава, образуя металлическую ванну (5), а расплавленный флюс находится в верхней части расплава, образуя шлаковую ванну (4).
Шлаковая ванна, находясь сверху, защищает жидкий металл от окисления воздухом.
В начальном и конечном участках образуются дефекты. В начале шва – непровар кромок, а в конце шва – усадочная раковина и неметаллические соединения.
Наиболее экономически выгодным является применение электрошлаковой сварки при изготовлении толстостенных конструкций в тяжелом машиностроении, для изготовления ковано-сварных и лито-сварных конструкций, таких как станины и детали мощных прессов и станков, коленчатые валы судовых двигателей, роторы и валы гидротурбин, котлы высокого давления.
Рис. 6.
Схема процесса электрошлаковой сварки:
1 – кромки основного металла;
2 – сварочная проволока;
3 – формирующиеся устройства;
4 – шлаковая ванна;
5 – металлическая ванна;
6 – водная планка.
Технологические возможности ЭШС позволяют сваривать детали толщиной от 30–40 до 3000 мм. Для сварки используют проволоку, плавящиеся мундштуки, пластинчатые электроды, ленточные электроды. В качестве источников питания применяют специальные сварочные трансформаторы с жесткой внешней характеристикой, напряжением 30–55 В и токами от 50 А до 3000 А.
Аппараты для ЭШС условно разделяют на следующие типы:
• рельсовые аппараты, перемещающиеся по направляющим рельсам;
• безрельсовые аппараты, перемещающиеся непосредственно по изделию;
• аппараты подвесного типа, не имеющие ходового механизма, что делает их простыми и портативными.
Оборудование, необходимое для ЭШС:
• специальные сварочные аппараты;
• аппаратные шкафы;
• аппараты для подачи электродной проволоки или ленты;
• устройства для формирования сварочного шва;
• устройства фиксации и перемещения изделий.
Преимущества ЭШС:
• возможность получения за один проход сварных соединений практически любой толщины, от 25 и до 3000 мм;
• отсутствие необходимой специальной подготовки кромок свариваемых деталей;
• расход флюса в десятки раз меньший, чем при обычной электродуговой сварке;
• возможность применения электродов самой различной формы;
• улучшенная макроструктура шва (высокая однородность металла сварной ванны);
• высокая производительность процесса;
• сокращенный расход электроэнергии;
• малая зависимость зазора между соединяемыми деталями от толщины свариваемого металла и отсутствие подрезов;
• использование ЭШС для переплавки стали из отходов и получения отливок;
• возможность регулирования процесса при токах сварки от 0,2 А/мм2 и до 300 А/мм2 по сечению электрода;
• надежная защита сварочной ванны от воздуха;
• возможность получения за один проход швов переменной толщины.
Недостатки ЭШС:
• возможность сварки только в вертикальном или почти вертикальном положении свариваемых плоскостей (с отклонением от вертикали не более 30°);
• высокая степень перемешивания основного и электродного металлов;
• наличие крупнозернистой структуры в металле шва и в переходной зоне;
• необходимость изготовления и установки перед сваркой технологических деталей (планки, формирующие устройства, стартовые карманы);
• недопустимость остановки электрошлакового процесса до окончания сварки, т. к. при этом образуются неустранимые дефекты.
Электронно-лучевая сварка (ЭЛС)
Электронно-лучевая сварка основана на использовании энергии, высвобождаемой при торможении потока ускоренных электронов в свариваемых материалах.
Преобразование кинетической энергии электронов в тепловую энергию характеризуется высоким к.п.д. При электронно-лучевой сварке в качестве источника нагрева используется поток электронов, движущихся в высоком вакууме. Для сварки необходимо получить свободные электроны, сконцентрировать их и сообщить им скорость с целью увеличения энергии. Электронный луч, используемый для нагрева металла при сварке, создается в специальном приборе – электронной пушке.
Электронная пушка (рис. 7, 8) представляет собой устройство, с помощью которого получают электронные пучки с малым диаметром пятна и высокой плотностью энергии в нем. Пушка имеет катод (1), который нагревается до рабочей температуры с помощью нагревателя. Катод размещен внутри прикатодного электрода (2). На некотором расстоянии от катода находится ускоряющий электрод (3) с отверстием – анод. Прикатодный и ускоряющий электроды имеют форму, обеспечивающую такое строение электрического поля между ними, которое фокусирует электроны в пучок диаметром dkp, равным диаметру отверстия в аноде. Положительный потенциал ускоряющего электрода может достигать нескольких десятков киловольт, поэтому электроны, эмитированные катодом, на пути к аноду приобретают значительную скорость и энергию.
После ускоряющего электрода электроны движутся равномерно. Электроны имеют одинаковый заряд, поэтому они отталкиваются друг от друга. Вследствие этого диаметр пучка увеличивается, а плотность энергии в пучке уменьшается.
Для увеличения плотности энергии в пучке после выхода электронов из анода их фокусируют магнитным полем в специальной магнитной линзе (4). Сфокусированный поток электронов, попадая на поверхность свариваемых кромок, тормозится. При этом кинетическая энергия превращается в теплоту, идущую на разогрев металла (6) при сварке. Для перемещения луча по поверхности свариваемого изделия на пути электронов помещают магнитную отклоняющую систему (5), позволяющую устанавливать электронный луч точно по линии стыка свариваемых кромок.
Рис. 7.
Схема устройства формирования электронного луча
Для обеспечения свободного движения электронов от катода к аноду и далее к изделию, для предотвращения «отравления» катода, а также для устранения возможности возникновения дугового разряда между электродами в камере электронно-лучевой установки создается высокий вакуум – примерно 10–4 мм рт. ст.
Движение электронов в вакууме не сопровождается световыми эффектами, и потому луч не виден, но место воздействия луча на свариваемый материал можно наблюдать по свечению металла за счет его разогрева.
Электронно-лучевая сварка позволяет сваривать тугоплавкие металлы, которые обычными методами не свариваются, например вольфрам, молибден, ниобий, тантал.
Высокая концентрация теплоты в пятне фокуса позволяет сверлить лучом такие материалы, как сапфир, рубин, алмаз, стекло.
Незначительная ширина зоны теплового воздействия дает возможность резко уменьшить деформацию заготовок. Кроме того, за счет вакуума в камере обеспечиваются зеркальная поверхность соединения и дегазация расплавленного металла.
Малый объем литого металла и кратковременность теплового воздействия обеспечивают незначительные термические деформации свариваемых деталей, что позволяет выполнять сварные швы вблизи металлокерамических и металлостеклянных спаев, чувствительных к термоударам.
Рис. 8.
Конструкция современной сварочной электронно-лучевой пушки:
1 – катод; 2 – управляющий электрод;
3 – анод; 4 – изолятор;
5 – фокусирующая линза.
Электронно-лучевые пушки можно разделить на типы:
• низковольтные пушки с ускорением электронов до энергии 20–30 кэВ;
• с промежуточным ускоряющим напряжением – 30–100 кэВ;
• высоковольтные пушки с энергией ускорения 100–200 кэВ.
Оборудование для ЭЛС:
• высоковольтный выпрямитель;
• стабилизатор ускоряющего напряжения;
• блок накала катода;
• модулятор;
• источник питания электромагнитных линз;
• электронно-лучевая пушка;
• вакуумная камера с вакуумной системой и люками загрузки;
• механизмы перемещения свариваемых деталей.
Преимущества ЭЛС:
• высокий к.п.д. установок ЭЛС, т. к. до 99 % кинетической энергии электронов, используемой для нагрева свариваемых деталей, переходит в тепловую энергию;
• температура в зоне сварки достигает 5000–6000 °C;
• при сварке электронным лучом теплота выделяется только в зоне сварки;
• за счет более интенсивного выделения теплоты в глубине зоны сварки получается кинжальное проплавление с отношением глубины к ширине до 20:1;
• высокая удельная мощность луча до 5–105 Вт/см2 и выше;
• фокусировка луча до диаметра 0,001 см;
• электронный луч используют для сварки, сверления, фрезерования практически любых современных материалов;
• широкий диапазон толщин заготовок (от 0,02 до 100 мм);
• высокая степень автоматизации сварочного процесса.
Недостатки ЭЛС:
• наличие специального оборудования требует подготовки высококвалифицированных кадров;
• наличие рентгеновского излучения при взаимодействии электронного луча со свариваемым материалом требует защиты оператора;
• высокая температура накала катода до 1700–2400 °C снижает срок службы катодов.
Плазменная сварка
Плазма (от греч. plasma, букв. – вылепленное, оформленное) – частично или полностью ионизированный газ, в котором плотности положительных и отрицательных зарядов практически одинаковы.
Термин «плазма» ввели в 1929 г. И. Ленгмюр и Л. Тонкс. Большой вклад в развитие учения о плазме внесли советские ученые – Л. Д. Ландау, А. А. Власов, А. Д. Сахаров, американские ученые И. Е. Тамм, Л. Спитцер.
Современные ученые выделяют плазму как четвертое состояние вещества, наряду с газом, жидкостью и твердыми телами. В состоянии плазмы находится большая часть вещества Вселенной – звезды, звездные атмосферы, межзвездная среда. Около Земли плазма существует в виде солнечного ветра, проявления которого мы наблюдаем в виде полярных сияний.
При сильном нагревании любое вещество испаряется, превращаясь в газ. Если увеличивать температуру и дальше, резко усилится процесс термической ионизации, т. е. молекулы газа начнут распадаться на составляющие их атомы, которые затем превратятся в ионы. Ионизация газа, кроме того, может быть вызвана его взаимодействием с электромагнитным излучением (фотоионизация) или бомбардировкой газа заряженными частицами.
Свободные заряженные частицы, особенно электроны, легко перемещаются под действием электрического поля. Поэтому в состоянии равновесия пространственные заряды входящих в состав плазмы отрицательных электронов и положительных ионов должны компенсировать друг друга так, чтобы полное поле внутри плазмы было равно нулю. Именно отсюда вытекает необходимость практически точного равенства плотностей электронов и ионов в плазме – ее квазинейтральности. Нарушение квазинейтральности плазмы в объеме, ею занимаемом, ведет к немедленному появлению сильных электрических полей пространственных зарядов, тут же восстанавливающих квазинейтральность.
Принято выделять два типа плазмы:
• низкотемпературная плазма с температурой внутри её ниже 105 К;
• высокотемпературная плазма с температурой выше 106–108 К.
На сегодняшний день плазму получают следующими способами:
• электрическим разрядом в газах (дуговой, искровой, тлеющий);
• в процессах горения и взрыва.
Плазма обладает так называемыми коллективными процессами. Ее можно рассматривать как упругую среду, в которой легко возбуждаются и распространяются различные шумы, колебания и волны. Причем плазма обладает наличием собственных колебаний и волн. Таким образом, плазма резко отличается от газов. Например, электропроводность полностью ионизированной плазмы превосходит электропроводность серебра. Поэтому плазму можно рассматривать как идеальный проводник.
Плазменная технология подразумевает различные методы обработки и получения материалов с использованием плазменной струи или плазменной дуги.
Наиболее широкое распространение получили атмосферные (при нормальном давлении) плазменные методы обработки материалов – резание, напыление, наплавка, сварка, выращивание монокристаллов.
В 1980-х годах эффективное развитие получили ионно-плазменные технологии. Процессы обработки материалов с помощью ионно-плазменной технологии реализуются в вакууме с помощью плазменных ускорителей. Благодаря этому удается наносить сверхтвердые, жаростойкие, коррозионно-стойкие покрытия.
Плазму получают в специальных устройствах – плазмотронах. Плазмотрон – устройство для создания плотной (с давлением порядка атмосферного) низкотемпературной плазмы (до 104 К) с помощью электрического разряда в газах, дающее плазменный поток.
Принцип работы плазмотрона заключается в следующем: холодный газ непрерывным потоком продувают через область, где горит стационарный разряд. Газ нагревается, ионизируется, превращается в плазму, которая истекает в виде плазменной струи.
На практике применяют следующие виды плазмотронов, работающих:
• на дуговом разряде;
• пеннинг-разряде;
• ВЧ и СВЧ-разрядах (высоко– и сверхвысокочастотных);
• с ионизацией газа электронным пучком;
• фокусировкой оптического разряда с помощью лазера.
Наибольшее практическое применение получили плазмотроны на дуговом электрическом разряде. Дуговой плазмотрон может работать на постоянном или переменном токе. Мощность дуговых плазмотронов – от 102 до 107 Вт.
Температура на срезе сопла – 3000–20 000 °C. Скорость истечения струи 1–104 м/с, промышленный к.п. д – 50–90 %. Плотность тока в плазмотронах достигает 100 А/мм2.
В качестве плазмообразующего газа используют аргон (температура плазмы – 15000–30000 °C), азот (температура плазмы – 10000–15000 °C) или смесь газов