Система технического обслуживания и ремонта энергетического оборудования: Справочник Ящура Александр
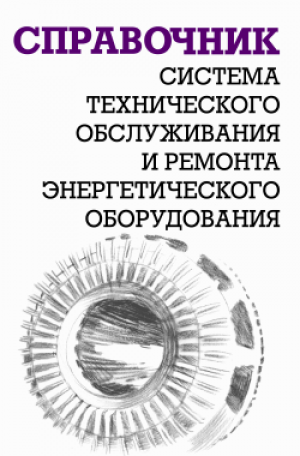
6.4.8. Цель обследования – проверка соблюдения предприятием или организацией требований правил, постановлений, приказов и указаний Ростехнадзора и его местных органов, а также выполнения мероприятий по котлонадзору, разработанных во исполнение указаний директивных органов.
6.4.9. Цель технического освидетельствования – проверка технического состояния объекта, его соответствия правилам и определение возможности дальнейшей эксплуатации.
6.4.10. Обследования и технические освидетельствования объектов котлонадзора, зарегистрированных в местных органах Ростехнадзора, проводят инспекторы Ростехнадзора. Котлы, сосуды обследуют не реже одного раза в год, трубопроводы пара и горячей воды – не реже одного раза в 3 года, вновь установленные сосуды обследуют не позднее, чем через 6 месяцев после ввода их в эксплуатацию.
6.4.11. При наличии на предприятии надлежащего надзора со стороны администрации за безопасной эксплуатацией сосудов по решению местного органа Ростехнадзора их можно обследовать выборочно, обследуя каждый сосуд не реже одного раза в 3 года.
6.4.12. Для проверки выполнения предприятиями отдельных требований правил котлонадзора, указаний органов Ростехнадзора, мероприятий по результатам расследований аварий производят целевые обследования.
6.4.13. Обследование проводят в присутствии представителя технической администрации предприятия и лиц, осуществляющих надзор за объектами и ответственных за их безопасную эксплуатацию. Для участия в обследовании в зависимости от его характера приглашают технических инспекторов профсоюза, инженерно-технических работников вышестоящих организаций, работников, осуществляющих надзор за объектами на аналогичных предприятиях, и представителей других организаций.
6.4.14. При периодических обследованиях проверяют: организацию и эффективность осуществления технического
надзора за безопасной эксплуатацией объектов;
организацию обучения, аттестации и проведения проверки знаний обслуживающего персонала;
проведение проверки знаний руководящими и инженерно-техническими работниками норм и инструкций по технике безопасности;
наличие и содержание требуемой правилами НТД;
соответствие технического состояния и обслуживания объектов требованиям правил;
выполнение мероприятий по обеспечению безопасной эксплуатации объектов, разрабатываемых во исполнение решений и указаний директивных органов;
выполнение постановлений, приказов и указаний Ростехнадзора, его региональных и местных органов, а также ранее выданных предписаний.
6.4.15. По результатам обследования инспектор или группа инспекторов, проводивших обследование, составляют акт-предписание. В паспорте каждого обследованного объекта должна быть сделана запись: «Произведено обследование», поставлены подпись и дата.
6.4.16. Акт-предписание вручают руководителю предприятия (директору, главному инженеру), а его копии представляют местному органу Ростехнадзора для контроля выполнения указанных в нем мероприятий.
6.4.17. Если при обследовании выявлены нарушения, не требующие немедленной остановки объекта, указывают срок их устранения. По возможности выявленные нарушения должны быть устранены в период обследования. В зависимости от результатов обследования проводят обсуждение на совещании руководящих и инженерно-технических работников результатов обследования; инструктивную беседу с обслуживающим персоналом по вопросам предупреждения аварий и несчастных случаев при эксплуатации объектов; внеочередную проверку знаний обслуживающего персонала и т. д.
6.4.18. Если при обследовании выявлены повторные нарушения, по которым ранее выдавались предписания, инспектор (руководитель группы) обязан потребовать от руководителя предприятия издания приказа о наказании лиц, допустивших нарушения, и проведении мероприятий по предотвращению подобных случаев в дальнейшем.
6.4.19. Местными органами Ростехнадзора может быть проведена внеочередная проверка знаний руководящих и инженерно-технических работников предприятия, а также могут быть наложены штрафы на должностных лиц, виновных в неоднократном нарушении правил, норм и инструкций по безопасному ведению работ.
6.4.20. При выявлении нарушений, создающих непосредственную угрозу аварий, эксплуатацию объекта запрещают наложением пломбы. Объект может быть запрещен к дальнейшей эксплуатации также и в том случае, если истек срок очередного освидетельствования или обслуживание объекта не обеспечено подготовленным персоналом или отсутствует предусмотренный надзор за его эксплуатацией.
6.4.21. Разрешение на пуск в работу остановленного объекта может быть выдано инспектором (руководителем группы) Ростехнадзора по письменному ходатайству предприятия после устранения нарушений и издания приказа о мероприятиях по недопущению подобных нарушений в дальнейшем. Инспектор обязан проверить на месте устранение нарушений и согласовать с руководством местного органа Ростехнадзора выдачу разрешения на пуск объекта в работу.
6.5. Расследование и учет аварий и инцидентов
6.5.1. Основными задачами расследования, учета и анализа нарушений нормального режима работы оборудования являются:
тщательное, технически квалифицированное установление причин и всех виновников нарушений;
разработка мероприятий по восстановлению работоспособности поврежденного оборудования, предупреждению подобных нарушений в его работе, повышению ответственности эксплуатационного и другого персонала предприятий, на которых произошло нарушение, а также имевшего отношение к нарушению персонала других предприятий;
оценка экономических последствий (ущерба) потребителя и (или) энергоснабжающей организации;
получение и накопление полной и достоверной информации о нарушениях нормального режима работы оборудования.
6.5.2. Каждая авария и инцидент в работе должны быть тщательно расследованы с установлением причин и виновников и разработкой конкретных противоаварийных мероприятий по предупреждению подобных случаев.
6.5.3. Подробное описание порядка учета и расследования аварий приведено в Приложении 9.
6.5.4. Кроме аварий и инцидентов на производстве могут иметь место несчастные случаи. Порядок расследования несчастных случаев на производстве установлен Трудовым кодексом Российской Федерации.
Часть II
ТИПОВЫЕ ОПЕРАЦИИ И РАБОТЫ, НОРМАТИВЫ ТЕХНИЧЕСКОГО ОБСЛУЖИВАНИЯ И РЕМОНТА ОБЩЕПРОМЫШЛЕННОГО ОБОРУДОВАНИЯ
Во второй части справочника приведены типовые работы и нормативы периодичности, продолжительности и трудоемкости ТО и ремонта основных видов общепромышленного оборудования: металлорежущих станков, деревообрабатывающего оборудования, кузнечно-прессового оборудования, специальных гидравлических прессов, литейного электропечного оборудования, подъемно-транспортного оборудования, компрессорно-насосного оборудования, оборудования вентиляции и кондиционирования воздуха, дробильно-размольного оборудования, подвижного состава автомобильного транспорта, дорожно-строительных и сельскохозяйственных машин.
Рекомендации по составу ремонтно-профилактических операций составлены с учетом рекомендаций заводов-изготовителей и действующих регламентов на предприятиях различных отраслей промышленности и сфер производства. Численные значения нормативов периодичности, продолжительности и трудоемкости ТО и ремонты приняты как средневзвешенные величины для предприятий, работающих в нормальных условиях производства ремонтно-профилактических работ.
7. МЕТАЛЛОРЕЖУЩЕЕ, ДЕРЕВООБРАБАТЫВАЮЩЕЕ И КУЗНЕЧНО-ПРЕССОВОЕ ОБОРУДОВАНИЕ
Металлорежущее, деревообрабатывающее и кузнечно-прессовое оборудование по месту применения сосредоточено преимущественно в механических и ремонтно-механических цехах (участках) предприятий с близкими условиями эксплуатации. Ремонтно-профилактические работы для этих видов оборудования также достаточно общие, поэтому целесообразно рассмотреть их в одном разделе.
Станки и машины металлообрабатывающие, металлорежущие (токарной группы, сверлильно-расточной группы, зубообрабатывающие, фрезерные, строгальные и долбежные, болто-пазонарезные, станки отрезные, специальные и специализированные) отнесены к седьмой амортизационной группе со сроком полезного использования свыше 15 до 20 лет включительно.
Станки и машины металлообрабатывающие кузнечно-прессовые (прессы механические, прессы гидравлические, автоматы кузнечно-прессовые, молоты, машины и вальцы ковочные, машины гибочные правильные, ножницы) относятся к шестой амортизационной группе со сроком полезного использования свыше 10 до 15 лет включительно.
Станки деревообрабатывающие (строгальные, фрезерные, шипорезные, шлифовальные, полировальные, сверлильные, пазовые и долбежные) также относятся к шестой амортизационной группе со сроком полезного использования свыше 10 лет до 15 лет включительно.
Станки металлообрабатывающие других групп, в том числе газопламенной обработки, нанесения металлопокрытий, газотермического напыления, системы гибкие производственные (роботы) относятся к третьей амортизационной группе со сроком службы свыше 3 до 5 лет включительно. В эту же группу включены станки круглопильные, ленточные и лобзиковые.
7.1. Техническое обслуживание
7.1.1. Типовая номенклатура операций ТО металлорежущего, деревообрабатывающего и кузнечно-прессового оборудования представлена в табл. 7.1.
Таблица 7.1
7.2. Текущий ремонт
Типовая номенклатура работ текущего ремонта по типам металлорежущего, деревообрабатывающего и кузнечного оборудования приведена в табл. 7.2.
Таблица 7.2
7.3. Капитальный ремонт
Типовая номенклатура ремонтных работ капитального ремонта по типам металлорежущего, деревообрабатывающего и кузнечно-прессового оборудования приведена в табл. 7.3.
7.4. Нормативы периодичности, продолжительности и трудоемкости ремонта
Нормативы периодичности, продолжительности и трудоемкости ремонта металлорежущего, деревообрабатывающего и кузнечно-прессового оборудования приведены в табл. 7.4.
* Для полуавтоматов трудоемкость капитального ремонта увеличивается на 35 %.
8. ЛИТЕЙНОЕ ЭЛЕКТРОПЕЧНОЕ ОБОРУДОВАНИЕ
В раздел включено следующее литейное оборудование: электропечи, электропечные агрегаты и механизмы, которые относятся к пятой амортизационной группе со сроком полезного использования свыше 7 до 10 лет включительно.
8.1. Техническое обслуживание
Техническое обслуживание электропечей, электропечных агрегатов и оборудования производится в соответствии с требованиями технической документации заводов-изготовителей в процессе нерегламентированного обслуживания.
Перечень типовых операций для каждой группы оборудования указывается в ПТЭ предприятия. Примерный перечень типовых операций ТО по наименованиям оборудования приведен ниже.
8.1.1. Смесители. Очистка рабочих поверхностей смесителя от смеси и грязи. Обдувка воздухом траверсы, разжимающего устройства, редукторов, прибора системы регулирования формуемости смеси, панели управления. Проверка: состояния отвалов, скребков, плужков и штырей катков, при необходимости – регулировка, замена. Проверка состояния защитных кожухов, ограждений, ограничителей и т. п. Проверка работы смесителя и редукторов на шум и вибрацию. Проверка и регулировка натяжения ремней. Проверка состояния и работы муфты, электромагнитов. Проверка уровня масла в редукторах; при необходимости – пополнение. Подтяжка крепежных деталей и замена изношенных дефектных деталей отвалов, скребков, плужков, вкладышей, пальцев и резиновых вкладышей муфт, втулок, осей, штоков, валов, шпилек, гаек, винтов и др. Осмотр и устранение утечек в цилиндрах, редукторе, в мерном бачке, в запорном кране, смазочных устройствах, трубопроводах и пневмоаппаратуре. Зачистка забоин, царапин, задиров и заусенцев. Проверка работы и регулировка: механизма загрузки сухих и мокрых компонентов; механизма выгрузки смеси и отбора проб; механизма открывания и закрывания разгрузочных люков, загрузочных и дозирующих устройств; пневмоцилиндров; системы вентиляции; прибора формуемости смеси; устройств смазочной системы; ограничителей, переключателей и упоров; клиноременных передач; оградительных устройств в соответствии с требованиями техники безопасности. Регулировка зазоров между днищем чаши и нижней кромкой отвала; между боковой кромкой скребка тумбы и обкладкой тумбы (для смесителей с вертикально вращающимися катками).
8.1.2. Формовочные машины. Проверка и подтяжка крепежных деталей механизмов, подверженных вибрации и ударным нагрузкам. Пополнение разделительной жидкостью емкостей опрыскивания моделей. Проверка неисправности защитных кожухов, ограждений, ограничителей. Регулировка механизма вытяжки. Проверка крепления и работы электромагнитов, состояния моделей, втулок, штырей, рабочих поверхностей опок. Проверка и подтяжка креплений цилиндров и поршней, прессовых траверс и колодок, протяжных рамок и подъемных шрифтов, кронштейнов, поворотных столов, перекидных рычагов, валов. Проверка работы: встряхивающего механизма на частоту ударов в минуту, высоту подъема стола; прессового механизма на усилие прессования; поворотного механизма на надежность и скорость поворота. Проверка состояния соединений элементов пневмосистемы: цилиндров и аппаратуры управления; воздухораспределителей и клапанов, труб и шлангов; аппаратуры управления и исполнительных органов. Проверка работы и регулировка механизмов поворота траверсы и скребка, зажимов опоки, вибраторов. Проверка работы механизма поворота стола, стоек, серег, рычагов, цапф и пневмоцилиндра. Смена изношенных и поломанных деталей. Проверка исправности ограничителей, переключателей, клапанов, упоров и др. В процессе проверок производятся необходимые регулировки, предусмотренные руководством по эксплуатации и ТУ проверяемой машины. Проверка состояний всей гидросистемы и смазочных устройств: наличие масла в резервуарах, лубрикаторах, в колпачковых и капельных масленках и других смазочных точках. Устранение утечек; регулировка подачи масла к трущимся поверхностям механизмов.
8.1.3. Стержневые машины. Очистка от грязи и масла всех узлов и механизмов машины. Внешний осмотр на отсутствие поломок и утечек в гидро– и пневмооборудовании, системе водоохлаждения и системе газового нагрева с устранением выявленных неисправностей; спуск конденсата из влагоотделителей. Проверка состояния конечных выключателей, их регулировка и устранение неисправностей. Проверка состояния стержневой оснастки. Проверка и подтяжка крепежных деталей, подверженных вибрации и периодическим нагрузкам. Проверка состояния оградительных устройств и защитных кожухов, устранение неисправностей. Регулировка работы зажимных устройств, досылателей и фиксаторов. Проверка состояния: уплотнений пескодувной гильзы, шиберного устройства и пескодувной насадки; диафрагмы клапанов вдува и выхлопа; элементов органов управления (переключателей, кнопок управления, сигнальных ламп и др.); деталей шиберного устройства, клапанов вдува и выхлопа, вибропитателя. Проверка уровня масла в баках, резервуарах и других емкостях; проверка наличия масла в маслораспреде-лителях и капельных масленках и смазочного материала в колпачковых масленках; проверка поступления масла в места назначения. Проверка состояния: системы газового нагрева стержневых ящиков, системы электронагрева стержневых ящиков; трубчатых электронагревателей; пирометрической системы контроля и поддержания заданной температуры нагрева стержневых ящиков. Проверка и подтяжка креплений в зажимных устройствах, фиксаторах, цепных передачах рольгангов. Проверка величины щелей пескодувной гильзы и ее замена при величине щелей более 0,5 мм. Проверка состояния поверхностей шибера и надувной плиты; при наличии забоин, задиров, рисок глубиной 0,3 мм и более произвести замену или ремонт. Осмотр и проверка состояния роликов и их крепления на рольгангах; замена роликов, имеющих дефекты (износ по периметру, эксцентриситет и др.). Проверка и подтяжка болтовых соединений, замена ослабленных или изношенных крепежных деталей. Проверка состояния цилиндров, штоков, фланцевых соединений и других деталей пневмогидросистемы, поддающихся наружному осмотру. Проверка действия предохранительных и автоматических устройств. Выявление дефектов, требующих устранения при ближайшем плановом ремонте.
8.1.4. Выбивные решетки. Осмотр состояния привода. Проверка: состояния упругих опор и крепежных деталей вибратора; температуры нагрева корпусов подшипников; подтяжка крепления полотна колосниковых секций решетки; уровня масла (для жидких ванн) в вибровозбудителе; подтяжка всех крепежных деталей. Замена изношенных крепежных деталей. Проверка состояния и подварка полотна колосниковых секций и корпуса решетки. Проверка состояния: электропроводки; подшипниковых узлов и валов. При наличии утечек масла заменить уплотнения и манжеты.
8.1.5. Пескометы. Очистка от грязи, смеси и масла. Проверка крепления ковша и дуги. Проверка зазора между верхней кромкой ковша и дугой. При установке нового ковша зазор не должен превышать 0,5–0,7 мм. Проверка натяжения клиноременных передач, каната механизмов подачи и цепи привода ленты питателя. Проверка работы: механизмов перемещения тележки и моста (для пескометов мостового типа); механизмов поворота большого и малого рукавов, гидросистемы; головки (на холостом ходу); плавности хода тележки механизма подачи. Проверка и подтяжка крепежных деталей ротора метательной головки. Очистка приямков от формовочной смеси и смазывание открытых зубчатых передач. Проверка работы пескометной головки при вытянутых в одну линию рукавах, а также при расположении оси малого рукава под углом 90° относительно большого рукава (провисание не должно превышать 5 мм). Проверка вертикальности осей поворота большого и малого рукавов. Проверка состояния элементов сочленения малого рукава пескомета с большим и большого с центральной поворотной осью. Проверка углов поворота большого и малого рукавов. Проверка смазочной системы: количества и состояния масла в редукторах; подачи масла во все смазочные точки согласно паспорту машины; наличие смазки в подшипниковых узлах. Проверка состояния открытых зубчатых передач. Проверка действия автоматических и предохранительных устройств. Проверка и регулирование муфт и тормозных устройств. Проверка состояния фундамента и фундаментных болтов. Проверка состояния конвейерных лент.
8.1.6. Дробеметные камеры и барабаны. Проверка правильности настройки сепаратора. Проверка работы затворов и путевого выключателя скипового подъемника. Проверка состояния шпинделя рабочего колеса, быстроизнашивающихся деталей. Проверка возможного засорения системы циркуляции дроби в местах затворов, патрубке, наличия крупных кусков металла на сепараторе барабанного сита. Осмотр и проверка состояния узлов и механизмов: дробеметного аппарата, пластинчатого и винтового конвейеров, сепаратора, элеваторов, скипового подъемника, двери, затворов дроби. Проверка состояния сварных швов. Проверка состояния защитной облицовки камеры торцовых дисков и двери. В случае предельного износа производится частичная замена или ремонт. Проверка мест соединений системы циркуляции дроби с целью устранения утечек дроби. Проверка работы пылеотсасывающей системы. Проверка и подтяжка разъемных соединений трубопроводов для устранения утечки воздуха. Проверка состояния и замена быстроизнашивающихся деталей дробеметного аппарата. Проверка состояния ленты или цепей ковшового элеватора. Проверка состояния питателей и барабанного сита сепаратора, смена сетки. Проверка работы механизмов вращения стола, тарелок передвижения тележки и скипового подъемника. Проверка и регулирование натяжения цепных и клиноременных передач. Проверка исправности смазочной системы, проверка количества масла в редукторах и качества подачи масла во все смазочные точки согласно карте смазывания. Регулирование подшипников, проверка уплотнений и замена изношенных сальников и манжет. Проверка состояния: оградительных устройств; органов управления. Проверка действия автоматических и предохранительных устройств. Выявление дефектов, требующих устранения при ближайшем плановом ремонте.
8.1.7. Машины литья под давлением. Очистка поверхности машины от металлических брызг и грязи. Проверка состояния гидросистемы (утечки недопустимы). Проверка состояния смазочной системы. Проверка усилия запирания. Проверка работы системы нагрева и охлаждения. Контроль затяжки крепежных деталей крышек, фланцев и всех соединений гидравлической системы. Особое внимание обратить на стыки, расположенные вблизи печей и пресс-формы. Подтяжка крепежных деталей, замена изношенных и сломанных деталей крепления шлангов, крестовины к штоку гидроцилиндра, неподвижной траверсы к станине машины, планок траверсы прессующего поршня, электродвигателя и насоса, штанг концевых выключателей. Проверка состояния соединений элементов гидравлики. Проверка наличия масла во всех точках трущихся соединений. Регулировка элементов гидросистемы: устранение утечек, при наличии вибрации трубопровода подтяжка крепления трубопроводов или крепление дополнительными стяжками; при наличии вспенивания масла или вибрации насоса проверка всасывающей линии гидронасоса. Проведение лабораторного анализа качества масел на соответствие паспортным физико-химическим показателям. Проверка и регулировка клапанов вентилей (с полной ревизией запорной арматуры системы подачи азота). Разборка и промывка фильтра. В случае наличия осадка в гидробаке промывка внутренней поверхности баков, аккумуляторов, трубопроводов, агрегата впрыскивания. Проверка работы системы нагрева и охлаждения масла (допускаемый нагрев не более 50 °C). Проверка соединения прокладок, манжет, колен и других уплотнительных соединений на герметичность. Проверка контрольно-измерительных приборов (манометров, реле давления и пр.), а также электрической аппаратуры (реле времени, автоматов и пр.). Проверка состояния системы охлаждения пресс-формы и прессующего плунжера. Наружный осмотр на отсутствие задиров, забоин, вмятин, износов на направляющих колонках, салазках, штоках, элементах механизма запирания. Проверка соосности стакана и плунжера. Смена быстроизнашивающихся деталей; плунжера, телескопов, стакана, литниковой втулки и других вышедших из строя деталей. Проверка и регулировка плавности хода (отсутствия рывков, ударов и заеданий). Проверка исправности ограничителей, упоров, предохранительных устройств, ограждений, предохранительного щита. Проверка состояния устройств управления работой машины: рукояток, тяг, рычагов, кнопок и т. д. Проверка сопротивления заземления машины. Проверка параллельности подвижной и неподвижной траверс.
8.1.8. Кокильные машины. Очистка поверхности машин от металлических брызг и грязи. Осмотр и проверка состояния механизмов, замена неисправных деталей. Проверка и подтяжка креплений машины; замена ослабленных, изношенных и неисправных крепежных деталей. Проверка состояния сети питания машины рабочей жидкостью, подтяжка соединений трубопроводов. Регулировка клапанов и вентилей. Проверка смазочной системы (проверка подачи масла во все смазочные точки согласно карте смазки). Проверка состояния поверхности роликов. Проверка состояния износа поверхности скалок, рельсов, штанг, толкателей, фланцевых соединений. Проверка состояния поверхностей стержней. Регулировка тяг, связанных с гидроцилиндрами перемещения стержней и подвижной плиты поддона. Проверка состояния пружин. Проверка поворота диска в механизме выталкивания. Проверка работы шарниров, роликов, рычага возврата выталкивателей. Замена пальцев и втулок шарнирного соединения. Проверка состояния уплотнений: сальников, прокладок, манжет, колец и других деталей. Смена быстроизнашивающихся деталей: втулок, вкладышей и др. Проверка состояния устройств системы управления работой машины: педалей, рукояток, тяг, рычагов, кнопок и др. Проверка состояния, ремонт и установка ограждения и других устройств обеспечения безопасности работы машины.
8.1.9. Центробежные машины. Проверка наличия подачи смазочного масла во все точки смазочной системы. Проверка утечек воздуха. Проверка нагрева: масла в масляных резервуарах (допускаемый нагрев не более 50 °C), насосов, подшипниковых узлов карусели. Проверка исправности предохранительных и тормозных устройств, обеспечивающих безопасность работы. Проверка наличия посторонних шумов и вибрации при работе механизмов, вызванных неисправностью элементов машины и электропривода. Проверка состояния направляющих, шпинделя и опорных, нажимных роликов. Регулировка клапанов и вентилей. Проверка подачи масла во все смазочные точки. Проверка системы водоохлаждения. Проверка на герметичность гидросистемы привода перемещения корпуса и общей системы. Проверка всех уплотнений, замена манжет, прокладок. Проверка состояния деталей цилиндров подрыва и выталкивания отливок. Проверка исправности ограничителей, упоров, предохранителей. Проверка состояния, ремонт и установка ограждения и других устройств обеспечения безопасности работы машины.
8.2. Текущий ремонт
При текущем ремонте выполняются операции ТО и нижеследующие работы по типам машин.
8.2.1. Смесители. Разборка узлов горизонтального или вертикального вала, промывка и замер износа, зачистка втулок и осей валов. Втулки заменяются при их износе. Проверка износа втулок рычагов и осей катков. Регулировка и при необходимости замена подшипников качения. Проверка износа обечайки и днища чаши. Замена кольцевых вставок днища чаши. Замена катка и резиновой облицовки (для центробежных смесителей). Проверка крепления обечайки. Замена отвалов, скребков и плужков. Замена регулировочных болтов и перенарезка резьб. Проверка состояния кронштейнов. Разборка и проверка состояния деталей механизма нагрузки. Разборка, зачистка поршней, осей, пальцев, а также смена сальников, уплотнений и всех крепежных деталей. Проверка состояния деталей шнековых дозаторов. Замена ремней клиноременной передачи и проверка допустимых отклонений размеров канавок шкивов. Проверка состояния и замена элементов муфт. Проверка: состояния крепежных тумб и рам к фундаменту; состояния фундамента (при необходимости – ремонт); всех соединений воздухопроводов; особое внимание обратить на целостность шлангов и их крепление, а также клапанов, с целью устранения утечек сжатого воздуха из пневмосистемы; параллельности промежуточного вала и быстроходных валов редуктора; на соосность выходного вала редуктора и вертикального вала; параллельности осей вращения шкивов и смещения осей канавок шкивов. Испытание машины на холостом ходу и под нагрузкой с проведением необходимых регулировочных работ.
8.2.2. Формовочные машины. Разборка и ремонт встряхивающего механизма. Промывка и очистка, замер и дефектация деталей. Замена колец, пружин, уплотнений и других деталей, подверженных износу. Зачистка задиров поршней и цилиндров с последующим шлифованием. При короблении встряхивающего стола производят строгание его поверхностей, при наличии трещин – заварку. Проверка состояния анкерных болтов крепления станины и выверка станины по уровню. Проверка и замена при износе деталей амортизаторов. Зачистка задиров и регулирование направляющих планок, штырей и втулок встряхивающего механизма. Разборка вытяжного механизма с дефектацией деталей. Зачистка задиров поршня и цилиндра.
8.2.3. Стержневые машины. Осмотр и промывка резервуаров и емкостей; очистка, промывка или замена фильтров. Выпуск отработанного и заливка нового масла (если текущий ремонт совпал с графиком смены масла). Проведение лабораторного анализа качества масла на соответствие паспортным физико-химическим показателям. Разборка механизма подъема и прижима стержневого ящика к насадке, механизма дутья с клапанами вдува и выхлопа, шиберного устройства, вибропитателя и других узлов и механизмов, подверженных наибольшему износу; дефектация деталей, замена изношенных деталей разобранных узлов и механизмов. Выявление дефектов, требующих устранения при последующем капитальном ремонте с записью в предварительной ведомости дефектов. Проверка на прямолинейность рабочей поверхности направляющих (отклонение не должно превышать 0,2 мм на длине 1000 мм). Проверка на параллельность рабочей поверхности поворотной рамы и опорной поверхности фланца крепления пескодувной насадки (1 мм на длине 1000 мм). Разборка и ремонт пневмогидравлических цилиндров с заменой изношенных деталей, уплотнений и других резинотехнических изделий.
8.2.4. Пескометы. Слив масла, промывка масляных резервуаров и гидросистемы. Осмотр и протирка всей машины. Разборка пескометной головки и замена изношенных деталей. Балансировка ротора пескометной головки. Проверка состояния колес, тормозов, приводных цепей, редуктора и других сборочных единиц тележки передвижения пескомета. Проверка состояния механизмов поворота большого и малого рукавов. Проверка рельсового пути: стыковых соединений, креплений и состояния пути. Выверка рельсов в горизонтальной плоскости по уровню. Проверка правильности соединения концов ленты и перетяжка ленты при необходимости. Проверка соединения большого и малого рукавов, подтяжка крепления тяг и рамы конвейеров. Проверка состояния гидрооборудования, подтяжка соединений и уплотнений. Проверка исправности ограничителей упоров переключателей. Выявление дефектов, требующих устранения при ближайшем плановом ремонте, с записью в предварительной ведомости дефектов. Испытание машины на холостом ходу и под нагрузкой.
8.2.5. Выбивные решетки. Проверка состояния и замена изношенных деталей вибровозбудителя. Добавление густого смазочного материала. Проверка состояния и подтяжка фундаментных болтов. Замена секций полотна решетки. Восстановление разрушенных мест боковин, колосниковых секций, опорных балок. Проверка работоспособности решетки.
8.2.6. Дробеметные камеры и барабаны. Проверка состояния узлов, подверженных наибольшему износу: внутренней облицовки камеры, торцовых дисков и двери, пластинчатого и винтового конвейеров, сепаратора с заменой изношенных деталей. Разборка дробеметного аппарата с заменой (при износе) рабочего колеса и быстроизнашивающихся деталей, проверка состояния подшипников, балансировка рабочего колеса дробеметного аппарата. Промывка деталей разобранных узлов. Подтяжка ленты пластинчатого конвейера, клиновых ремней дробеметного аппарата, ленты элеваторов и цепных передач. Замена изношенных (поврежденных) крепежных деталей. Проверка параллельности валов элеватора. Проверка состояния рельсового пути, стыковых соединений, креплений; выверка рельсов в горизонтальной плоскости по уровню.
8.2.7. Кокильные машины. Очистка и промывка поверхностей механизмов машины. Промывка, протирка деталей разобранных узлов. Замена быстроизнашивающихся деталей: втулок, вкладышей, осей. Замена всех уплотнений: манжет, колец, сальников, прокладок и грязесъемников. Измерение величины износа и проверка состояния направляющих, втулок, скалок, штанг, штоков, роликов. При наличии отклонений провести ремонтные работы или замену. Регулировка тяг, штанг, проверка осадки пружин. Разборка шарнирного механизма и проверка выработки втулок и пальцев (допустимый зазор между втулкой и пальцем – в соответствии с допусками по чертежу). Во всех гидро– и пневмоцилиндрах проверка наличия утечек. Проверка герметичности в местах соединений трубопроводов; устранение течи рабочей жидкости по всей длине сети питания машины, в местах уплотнений и соединений трубопроводов, ниппелей и сливных пробок. Ремонт, регулирование и замена ограничителей, упоров. Проверка работы органов управления, защитных, предохранительных устройств и блокировок. Проверка прямолинейности установочных поверхностей плит для крепления кокилей в различных направлениях. Проверка параллельности установочных плит для крепления кокилей. Проверка перпендикулярности плиты поддона и боковых установочных поверхностей плит для крепления кокилей. Ремонт или замена оградительных устройств, обеспечение их функции в соответствии с правилами техники безопасности. Проверка работы клапанов и вентилей. При наличии отклонений – заменить. Испытание машины на холостом ходу и под нагрузкой.
8.2.8. Центробежные машины. Подетальная разборка механизма выталкивания отливок и механизма вращения изложницы, подверженных наибольшему изнашиванию. Промывка, протирка и дефектация деталей механизма выталкивания отливок и вращения изложницы. Замена быстроизнашивающихся деталей: втулок, осей, колец. Замена всех уплотнений: манжет, колец, сальников и т. д. Проверка состояния и замена дефектных роликов. Проверка уплотнения подшипников, при необходимости – замена. Заполнение подшипниковых узлов пластичным смазочным материалом. Проверка системы охлаждения металлических форм. Замена сальников или арматуры. Проверка смазочной системы и состояния масла. Проверка состояния деталей гидро– и пневмоаппаратуры. Проверка герметичности в местах соединений трубопроводов; устранение течи жидкости по всей длине сети питания машины, в местах уплотнений и соединений трубопроводов, ниппелей и сливных пробок. Замена уплотнений, утративших герметичность. Проверка затяжки крепежных деталей крышек, фланцев, всех соединений гидро– и пневмосистемы. Настройка гидро– и пневмоаппаратуры машины. Испытание гидросистемы машины. Проверка состояния шпинделя. Замена подшипников шпинделя. Проверка состояния клиноременной передачи. Замена клиновых ремней. Разборка шарнирного механизма и проверка выработки втулок и пальцев. Ремонт, регулирование и замена ограничителей, упоров, предохранителей. Проверка работы электро-, пневмо-, гидрооборудования. Проверка норм точности машины по ТУ. Испытание машины на холостом ходу и под нагрузкой.
8.2.9. Машины литья под давлением. Центровка подвижной траверсы относительно колонн. Проверка зазора между втулками подвижной траверсы и колоннами (допуск не должен превышать размера, установленного в соответствии с чертежами). Проверка параллельности подвижной и неподвижной траверс. Проверка зазоров на гайках передвижения траверс. Проверка горизонтальности установки машины на фундаменте (необходимая точность установки в обоих направлениях 0,5 мм на 1000 мм). Подтяжка фундаментных болтов. Разборка шарнирного механизма и проверка износа втулок и пальцев (допустимый зазор между втулкой и пальцем в соответствии с чертежами. Не допускается использование втулок и пальцев, имеющих следы задиров глубиной более 0,3 мм). Замена уплотнений и грязесъемников механизма прессования. Проверка соосности прессующего штока относительно прессующего стакана. Проверка наличия утечек в гидроцилиндрах. При наличии утечек провести осмотр и заменить уплотнения. Проверка перпендикулярности прессующего гидроцилиндра относительно неподвижной траверсы. Проверка плоскостности плиты станины. Проверка параллельности подвижной и неподвижной траверс. По усмотрению механика проводятся работы по отдельным или всем пунктам осмотра. Сборка отремонтированных устройств и механизмов. Испытание машины на холостом ходу и под нагрузкой. Испытание гидросистемы при давлении выше рабочего на 25 %.
8.3. Капитальный ремонт
При капитальном ремонте выполняются все работы текущего ремонта; дополнительно производятся нижеследующие работы по наименованиям оборудования.
8.3.1. Смесители. Слив масла из емкостей. Полная подетальная разборка и дефектовка агрегатов, узлов и деталей. При необходимости восстановить или заменить: подшипники, валы, втулки, штоки, поршни, гильзы цилиндров, уплотнения, крепежные детали, кронштейны, анкерные болты, стойки и рамы, обечайку и днище чаши, ободы катков, пружины, рычажные механизмы. Поверхности бункеров, дверей, люков и резервуаров выправить, подвергнуть пескоструйной обработке в местах наличия коррозии, затем грунтовать и закрасить. Бункеры, резервуары, емкости и т. д. из коррозионно-стойкой стали при отсутствии значительного износа рихтовать. Восстановить фундамент. Восстановление или замена элементов: пневмооборудования, смазочного оборудования, электросистемы, таблиц, указателей, номеров, надписей. Испытание под нагрузкой и сдача в эксплуатацию.
8.3.2. Формовочные машины. Полная подетальная разборка всех узлов и механизмов машины. Промывка, протирка деталей узлов и механизмов. Ремонт встряхивающего, прессового, поворотного, вытяжного механизмов, механизмов поворота траверсы и скребка, захватаопок. Заменавыбракованныхосновныхдеталей: встряхивающих и поворотных столов, цилиндров и поршней, прессового цилиндра, рычагов и кронштейнов, колонок, штырей, цапф, валов, осей. Замена поршневых колец, манжет, воротников, втулок, гильз, штоков, скалок. Замена всего комплекта амортизаторов. Ремонт зажимных приспособлений, механизма фиксации. Замена выбракованных муфт, зубчатых колес, шестерен, реек. Замена элементов гидро– и пневмооборудования, смазочной системы, ремонт трубопровода и элементов его соединений. Ремонт или замена оградительных и защитных устройств в соответствии с требованиями техники безопасности. Сборка, монтаж и испытание отремонтированных узлов и механизмов на холостом ходу и под нагрузкой. Проверка состояния фундамента и его ремонт. Замена деревянного настила. При наличии трещин отбивка цемента и заливка высокопрочными марками цемента. Полная замена смазочного материала. Шпатлевка, окраска всех необработанных поверхностей.
8.3.3. Стержневые мельницы. Полная подетальная разборка всех узлов и механизмов машины. Промывка, протирка и осмотр всех деталей. Составление и уточнение дефектно-сметной ведомости. Полная замена всех изношенных крепежных деталей. Ремонт механизма подъема стержневого ящика, механизма прижима стержневого ящика к насадке (или механизма опускания насадки), механизма разборки стержневого ящика, механизма дутья с клапаном вдува и выхлопа, механизма перемещения траверсы и других механизмов, подверженных износу. Ремонт шиберного устройства, вибропитателя и других узлов. Замена основных выбракованных деталей: пескодувной гильзы, надувных плит с вентами, цилиндров и поршней, рычагов, кронштейнов, колонок, цапф, валов, осей и др. Ремонт и замена приспособлений зажима и фиксации, цепных и зубчатых передач конвейеров и их элементов. Ремонт пневмогидравлического оборудования и системы водоснабжения с заменой элементов пневмогидравлической аппаратуры; ремонт трубопроводов и устранение утечек по всей длине сети питания. Ремонт и замена элементов смазочной системы. Ремонт электрооборудования с заменой элементов электроаппаратуры и трубчатых электронагревателей, системы нагрева стержневых ящиков. Ремонт газовой системы нагрева стержневых ящиков с заменой элементов газовой аппаратуры; ремонт трубопроводов и устранение утечек. Ремонт пирометрического оборудования системы контроля и поддержания заданной температуры нагрева стержневых ящиков. Ремонт или замена оградительных и защитных устройств в соответствии с требованиями техники безопасности. Проверка установки машины и состояния фундамента. Проверка, подтяжка или замена фундаментных болтов; исправление фундамента путем подливки цементного раствора. Полная замена масла: выпуск отработанного и заливка нового масла. Проведение лабораторного анализа качества масла на соответствие паспортным физико-химическим показателям. Сборка машины из отремонтированных узлов и механизмов. Проверка правильности взаимодействия узлов и механизмов машины. Окраска наружных нерабочих поверхностей машины с подшпатлевкой; восстановление поврежденных таблиц, надписей, указателей и др. Испытание машины на холостом ходу и под нагрузкой. Проверка соответствия машины паспортным данным и нормам точности, указанным в руководстве по эксплуатации.
8.3.4. Пескометы. Полная подетальная разборка всех узлов и механизмов машины. Промывка, протирка и осмотр всех деталей. Составление дефектно-сметной ведомости. Полная замена всех изношенных крепежных деталей. Полная разборка метательной головки с заменой кожуха, замена головки. Балансировка ротора метательной головки в собранном виде. Разборка редукторов с заменой червячной пары, шестерен, подшипников, втулок, прокладок и других деталей. Разборка механизма передвижения с заменой скатов, осей, цепной передачи, подшипников и других деталей. Проверка сварных швов и заварка трещин. Сборка отремонтированных узлов и механизмов. Слив масла из резервуаров и промывка системы трубопроводов. Монтаж и настройка гидроаппаратуры согласно гидросхеме и паспортным данным. Проверка правильности работы основных органов пескомета раздельным или комбинированным пуском механизмов; обкатка машины на холостом ходу. Шпатлевка и окраска всех необработанных поверхностей по ТУ для отделки нового оборудования. Для стационарных пескометов проверка состояния и ремонт фундамента (подтяжка или замена фундаментных болтов, исправление фундамента путем подливки цементным раствором). Для передвижных пескометов – проверка состояния и замена отдельных участков рельсового пути, замена деталей стыковых соединений и рельсовых креплений, выверка рельсов в горизонтальной плоскости по уровню. Испытание машины под нагрузкой.
8.3.5. Выбивные решетки. Полная подетальная разборка всех узлов. Промывка, протирка и осмотр всех деталей. Составление дефектно-сметной ведомости. Замена изношенных деталей (валов, подшипников, болтов, муфт и т. д.). Ремонт или замена боковин, опорных балок, колосниковых секций. Полная замена смазочного материала. Проверка состояния фундамента и установка опорной рамы. Окраска решетки, восстановление табличек, надписей, указателей.
8.3.6. Центробежные машины. Подетальная разборка всех узлов и механизмов машины. Очистка от грязи, промывка, протирка и осмотр всех деталей. Составление дефектно-сметной ведомости. Замена или ремонт всех изношенных и имеющих дефекты деталей. Проверка состояния фундаментных болтов и фундамента (при необходимости замена фундаментных болтов и фундамента). Промывка гидросистемы. Замена масла. Проведение капитального ремонта электросистемы. Сборка и проверка правильности взаимодействия всех механизмов электро-, гидро-, пневмооборудования в работе на холостом ходу. Испытание под нагрузкой.
8.3.7. Дробеметные камеры и барабаны. Полная подетальная разборка всех узлов и механизмов. Промывка, протирка и осмотр всех деталей. Замена дробеметного аппарата. Балансировка ротора дробеметного аппарата в собранном виде. Полная замена всех изношенных крепежных деталей. Полная замена деталей дробеструйного аппарата: шлангов, пружин, клапанов, прокладок и других деталей. Полная разборка элеватора: замена подшипников, ковшей, валов, втулок и других деталей, а также замена изношенных частей оградительного кожуха. Полная разборка шнека с заменой секций и подшипников. Полная разборка механизмов поворота стола и вращения тарелок. Разборка элеватора с заменой изношенных ковшей и заклепок (болтов), замена или ремонт ленты элеватора. Разборка винтового конвейера с заменой секций. Полная разборка механизма передвижения тележки; замена изношенных опорных колес, тросов, барабана, натяжных роликов, других деталей. Полная разборка подвижного пода, полная замена изношенных пластин конвейера, боковых дисков, звездочек, цепей и других деталей. Разборка скипового подъемника, замена блоков тросов, опорных роликов, направляющих швеллеров, заварка и исправление рамы. Полная разборка редукторов с заменой червяков, шестерен, подшипников, втулок, прокладок и других деталей. Замена изношенных ремней и шкивов всех клиноременных передач. Ремонт запорных и шарнирных устройств, крышек, листовой брони, выправка дверей. Окраска всех необработанных поверхностей согласно ТУ для отделки нового оборудования. Испытание машины на холостом ходу и под нагрузкой.
8.3.8. Машины литья под давлением. Полная подетальная разборка всех узлов и механизмов машины. Промывка, протирка, осмотр и замеры износа всех деталей машины. Составление полной дефектно-сметной ведомости. Полная замена всех изношенных крепежных деталей. Замена изношенных деталей и узлов клапанных и распределительных коробок: насоса, золотников, клапанов, седел, манжет, прокладок, пружин, толкателей, пробок. Замена втулок, поршней и втулок подвижной плиты формодержателя. Замена деталей клинового и коленчато-рычажного механизма запирания пресс-формы: клиньев, вкладышей, пальцев втулок и других деталей. Заварка трещин станины. Шлифование внутренних и наружных рабочих поверхностей цилиндров, имеющих выработку, риски и царапины, с последующим хромированием. Разборка трубопроводов с промывкой и продувкой, замена отдельных участков трубопроводов, уплотнений, ниппелей и других деталей. Проверка параллельности и плоскостности основания станины. При наличии отклонений следует провести восстановительные работы согласно чертежу. Проверка правильности установки станины на фундаменте (необходимая точность установки в обоих направлениях 0,1 мм на 1000 мм). Проверка состояния фундамента. Проверка, подтяжка и замена фундаментных болтов. Исправление фундамента согласно ТУ на изготовление фундамента. Монтаж отремонтированных механизмов на станине. Монтаж и настройка гидроаппаратуры согласно гидросхеме и ТУ. Проверка правильности взаимодействия узлов и механизмов машины. Проверка перпендикулярности прессующего гидроцилиндра относительно неподвижной траверсы. Проверка соосности прессующего штока относительно прессующего стакана. Проверка параллельности подвижной и неподвижной траверс. Обкатка на холостом ходу: раскрытие, закрытие пресс-формы и холодное прессование. Полная окраска всех наружных нерабочих поверхностей машины. Восстановление таблиц и надписей. Испытание машины под нагрузкой. Проверка соответствия машины паспортным данным. Приемка в соответствии с ТУ и ГОСТ.
Примечание. В содержание типовых работ, выполняемых при ремонтах механической части машины для литья под давлением, не включены операции по ремонту оснастки (пресс-форм) и насосной установки.
8.3.9. Кокильные машины. Полная подетальная разборка всех узлов и механизмов машины. Очистка от грязи, промывка, протирка и осмотр всех деталей. Составление дефектно-сметной ведомости. Дефектация и замена изношенных крепежных деталей. Восстановление базовых деталей: подкокильных плит, станины, стоек, корпуса поддона, плиты поддона. Заварка трещин станины машины. Проверка на плоскостность рабочих поверхностей подкокильных плит; при отклонении – фрезеровка (для машин, предназначенных дли отливок из черных металлов). Замена штоков, поршней, колен, цилиндров, не подлежащих восстановительному ремонту. Замена деталей гидрораспределительной аппаратуры; манжет, прокладок, пружин, толкателей, пробок и распределительных коробок электроаппаратуры. Замена втулок, вкладышей, грязесъемников, штанг, осей, серег, роликов. Ремонт и замена всех оградительных устройств и защитных приспособлений. Сборка машин из отремонтированных узлов и механизмов. Проверка прямолинейности установочных поверхностей плит для крепления кокилей. Шпатлевка, грунтовка и окраска всех наружных нерабочих поверхностей машины, восстановление таблиц и надписей. Проверка состояния фундаментов, исправление фундамента путем подливки цементного раствора, проверка и замена фундаментных болтов. Проверка правильности взаимодействия всех рабочих механизмов машины. Проверка электро-, гидро-, пневмооборудования в пооперационном, полуавтоматическом и автоматическом режимах.
8.4. Нормативы периодичности, продолжительности и трудоемкости ремонта
Нормативы периодичности, продолжительности и трудоемкости ремонтов литейного электропечного оборудования приведены в табл. 8.1.
Таблица 8.1
9. ДРОБИЛЬНО-РАЗМОЛЬНОЕ И СОРТИРОВОЧНОЕ ОБОРУДОВАНИЕ
Дробильно-размольное и сортировочное оборудование отнесено к шестой амортизационной группе со сроком полезного использования свыше 10 до 15 лет включительно.
Занятое на дроблении, размоле и грохочении оборудование работает в интенсивном износном режиме, испытывает высокие знакопеременные нагрузки. Срок службы рабочих тел этого оборудования не превышает 34 560 часов, после чего требуется проведение капитального ремонта.
9.1. Техническое обслуживание
9.1.1. Техническое обслуживание дробильно-размольного оборудования производится в процессе его работы производственными рабочими при сдаче и приемке смен согласно инструкции по рабочему месту. Главным назначением ТО является обеспечение правильного режима эксплуатации. Практика показывает, что его нарушение приводит к повышенному износу и к аварийным поломкам отдельных частей оборудования.
9.1.2. Помимо очистки оборудования и смазки производится осмотр и контроль технического состояния механизмов и агрегатов, регулировка, устранение мелких неисправностей.
9.1.3. Техническое обслуживание оборудования входит в обязанности не только эксплуатационного персонала, но и дежурных ремонтников, мастеров смен, которые периодически контролируют визуально, на слух и при помощи измерительных инструментов работу наиболее ответственных агрегатов (электрических двигателей, редукторов, муфт) вплоть до их вскрытия во время коротких остановок оборудования.
Помимо технических осмотров, проводимых ремонтно-эксплуатационным персоналом, проводятся плановые остановки дробильно-размольных участков, при которых при помощи диагностических устройств контролируется исправность оборудования. Все выявленные неисправности устраняются немедленно, если это может привести к остановкам оборудования в процессе работы.
9.2. Текущий ремонт
9.2.1. Дробилки щековые. Осмотреть и при необходимости заменить заднюю распорную плиту, тяги, уплотнения и пружины к ним, верхнюю боковую броню, сухари распорных плит, подшипники качения привода, клиновые ремни, пружины, тяги. Произвести выверку осей и базовых поверхностей. Произвести регулировку и испытание.
9.2.2. Дробилки конусные. Произвести ремонт или замену распределительной плиты. Проверить и при необходимости заменить изношенную броню дробящего конуса, неподвижную броню и футеровку регулирующего кольца, коническую и цилиндрическую втулки эксцентрикового узла. Проверить работу системы смазки, при необходимости заменить масло. Заменить броню нижней части корпуса дробилки и броню привода, втулки и диски подпятника, шестерни приводного вала. Осмотреть и произвести ремонт зубчатого колеса эксцентрика. Заменить переднюю и заднюю втулки приводного вала. При необходимости заменить пружины и приводной вал. Произвести регулировку и испытание.
9.2.3. Дробилки молотковые и валковые. Заменить молотки (для сокращения продолжительности текущего ремонта ротор с изношенными молотками демонтируют и заменяют заранее собранным). Промыть и смазать подшипники качения. Проверить центровку ротора с валом электродвигателя. Проверить и при необходимости заменить клиновые ремни и колосниковые решетки. Заменить футеровку в зоне работы бил. Отремонтировать и сбалансировать ротор. Заменить уплотнения. Отремонтировать регулировочное устройство. Произвести регулировку и испытание.
9.2.4. Мельницы шаровые и стержневые. Произвести подтяжку крепления футеровки, ревизию маслостанции. Проверить и при необходимости произвести выборочную замену футеровочных плит, элементов решетки креплений. Заменить частично или полностью футеровку барабана и крышек, обтяжку футеровок и отдельные болты. Заменить или отремонтировать улитковый питатель. Произвести ревизию привода или его замену (при наличии сменного). Проверить соосность привода.
9.2.5. Мельницы роликомаятниковые. Подтянуть болты крепления мельницы. Заменить лемехи, размольное кольцо, лопасти. Промыть маслосистему. Заменить или восстановить приводной вал, малую коническую шестерню, втулки вертикального вала, втулки роликов, оси маятников и лемехов, большую коническую шестерню (работы выполняются по мере необходимости).
9.2.6. Грохоты ГНТ. Проверить и отрегулировать амплитуду и прямолинейность колебаний короба с рамой, равномерность зазоров между буферами упругих связей и отсутствие местных колебаний сит, деталей короба рамы и других элементов. Проверить и при необходимости заменить подшипники вибратора и пружины опор, погрузочное и разгрузочное сита.
9.2.7. Грохоты ГИЛ. Проверить и отрегулировать амплитуду и прямолинейность колебаний короба с рамой, зазоры между буферами упругих связей, отсутствие местных колебаний сит, деталей короба, рамы и других элементов. Проверить соединения загрузочной и разгрузочной течек, ванн, муфты и клиновых ремней, устранить выявленные неисправности. Заменить сита, полосы, нижние и верхние трубы в загрузке короба.
9.2.8. Грохоты ГСЛ. Проверить и отрегулировать амплитуду и прямолинейность колебаний короба с рамой, зазоры между буферами упругих связей и отсутствие местных колебаний сит, деталей короба, рамы и других элементов. Проверить состояние загрузочной и разгрузочной течек. Снять верхние и нижние сита. Устранить дефекты, обнаруженные в деталях и узлах короба. При необходимости заменить сита, полосы, угольники, планки и крепежные детали сит, пальцы вибратора. Произвести ремонт оградительных устройств и регулировку работы грохота.
9.3. Капитальный ремонт
При капитальном ремонте выполняются все работы текущего ремонта; кроме того, дополнительно нижеследующий объем ремонтных работ по типам оборудования.
9.3.1. Дробилки молотковые. Снять ограждения, клиновидные ремни привода, электродвигатель, шкивы, загрузочную течку, верхнюю часть корпуса, крышки и корпуса подшипников, сальниковые уплотнения, ротор, каретки, отбойный брус, втулку конусную, подшипники ротора. Разобрать на детали ротор, решетку подвесную, каретки, броню футеровочную. Очистить и разбраковать детали дробилки и детали крепления, дефектные заменить. Изготовить прокладки. Установить подшипники, втулку конусную, отбойный брус, каретки, сальниковые уплотнения, корпуса и крышки подшипников, верхнюю часть корпуса, загрузочную течку, шкивы, электродвигатель, клиновидные ремни, ограждения. Опробовать и сдать в эксплуатацию.
9.3.2. Дробилки валковые. Снять ограждения, соединительную муфту, ремни, крышу дробилки, крышки подшипников, подшипники, узлы и детали привода дробилки, узлы и детали внутренних устройств дробилки. Разобрать узлы дробилки на детали. Очистить и разбраковать детали, дефектные заменить. Очистить внутреннюю поверхность дробилки. Разбраковать детали крепления. Изготовить прокладки. Собрать и установить узлы внутренних устройств и привода, подшипники, крышки подшипников, крышку дробилки, ремни, соединительную муфту. Установить ограждения. Опробовать и сдать в эксплуатацию.
9.3.3. Дробилки щековые. Снять ограждения, ремни, шкивы, колпак, маховик, крышки подшипников, шатун, вал эксцентриковый, пружину, распорные плиты, ось подвижной щеки, подвижную щеку, боковые распорные клинья, подшипники. Очистить и разбраковать детали дробилки и детали крепления. Изготовить прокладки. Установить подшипники, боковые распорные клинья, подвижную щеку, ось подвижной щеки, распорные плиты, тяговую пружину, вал эксцентриковый, крышки шатуна и маховых подшипников, колпак, шкивы, ремни, ограждения. Опробовать и сдать в эксплуатацию.
9.3.4. Дробилки конусные. Снять ограждения, электродвигатель, приводные ремни, полумуфты, загрузочное устройство, кожух, стопорное устройство, распределительную плиту, головку, регулирующее кольцо, опорную чашу, эксцентрик, приводной вал, броню, пружину амортизаторов. Разобрать на детали узлы дробилки. Очистить и разбраковать детали дробилки и детали крепления, дефектные заменить. Изготовить прокладки, уплотнения. Собрать узлы дробилки из деталей. Установить загрузочное устройство, кольцо регулирующее, дробящий конус, опорную чашу, регулирующее кольцо, приводной вал, пружины амортизаторов, эксцентрик, распределительную плиту, стопорное устройство, электродвигатель, полумуфты, приводные ремни, ограждения. Опробовать и сдать в эксплуатацию.
9.3.5. Мельницы шаровые и стержневые. Отсоединить и снять ограждения, ремни, трубопроводы, редуктор, электродвигатель. Разъединить соединительную муфту. Извлечь приводной вал и спрессовать опорные подшипники и шестерню. Вынуть барабан шаровой мельницы. Спрессовать коренные подшипники и снять нижние половины корпусов подшипников. Отсоединить и снять венцовую шестерню и торцевые крышки барабана. Очистить внутреннюю поверхность мельницы. Промыть и разбраковать детали аппарата и крепления, дефектные заменить. Изготовить комплект прокладок. Провести ревизию редуктора. Установить и закрепить торцевые крышки барабана и венцовую шестерню. Установить корпуса подшипников и напрессовать подшипники на вал. Установить барабан. Собрать и установить приводной вал с шестерней. Соединить муфту, установить редуктор и электродвигатель. Надеть ремни. Установить трубопроводы и ограждения. Опробовать мельницу и сдать в эксплуатацию.
9.3.6. Мельницы маятниковые. Отсоединить и снять трубопровод, ограждение, крышку корпуса мельницы, кожух. Снять приводные ремни. Отсоединить сепаратор, питатель. Демонтировать конический редуктор привода с приводным валом. Разобрать корпус мельницы, вынуть детали внутренних устройств (крестовина, маятники, ролики, скребки, лемехи, червячный редуктор, система смазки, система привода маятников). Очистить, промыть и разбраковать детали мельницы и крепления, дефектные заменить. Провести ревизию червячного и конического редукторов. Изготовить комплект прокладок. Установить детали внутренних устройств, собрать корпус мельницы. Установить конический редуктор привода с приводным валом. Установить питатель, сепаратор, приводные ремни. Установить и закрепить кожух, крышку корпуса мельницы, ограждения, трубопровод. Опробовать мельницу и сдать в эксплуатацию.
9.3.7. Мельницы «Дезинтегратор». Отсоединить крышки смотровых люков, отсоединить и снять кожух, разъединить две муфты. Снять валы с дисками и роликоподшипниками, спрессовать две полумуфты, снять диски с валов. Очистить, промыть и протереть детали, разбраковать, дефектные заменить. Изготовить комплект прокладок. Провести ревизию и отбалансировать диск. Установить диски на валы, напрессовать две полумуфты, установить валы с дисками и роликоподшипниками. Соединить муфты, установить и закрепить кожух. Установить крышки смотровых люков. Опробовать дезинтегратор и сдать в эксплуатацию.
9.3.8. Мельницы «Дисмембратор». Снять ремни, шкив. Открыть крышку корпуса, снять подвижный и неподвижный диски с кулачками и ступицу. Вынуть вал, спрессовать подшипники. Вынуть барабан. Прочистить, промыть, протереть и разбраковать детали, дефектные заменить. Заменить кулачки, неподвижный диск, сетку дисмембратора, сухарь. Изготовить комплект прокладок. Установить барабан, напрессовать подшипники и установить вал. Установить ступицу, неподвижный и подвижный диски с кулачками. Закрыть крышку корпуса. Установить шкив, ремни. Опробовать дисмембратор и сдать в эксплуатацию.
9.3.9. Мельницы шахтная и коллоидная. Снять ограждение, разъединить полумуфты. Отсоединить и снять крышку, разобрать мельницу (снять билы, муфту сцепления, дверцы с мельницы), вынуть и разобрать ротор, вынуть вал редуктора. Разобрать маслонасос с трубомаслоприводом и фильтром. Очистить, промыть, протереть и разбраковать детали мельницы и крепления. Провести замену подшипников. Установить вал редуктора, собрать и установить ротор. Собрать мельницу, установить и закрепить крышку мельницы. Соединить полумуфты, установить ограждения.
9.3.10. Мельницы пятивалковые «Раймонд», мельница «Леше» и другие. Разъединить фланцевые стыки, снять маслопровод, гидропривод, балансир. Снять ограждение, ремень, питатель. Отсоединить и снять корпус мельницы. Разобрать мельницу, прочистить внутреннюю поверхность. Очистить, промыть и разбраковать детали мельницы и крепления. Провести ревизию редуктора. Собрать мельницу. Установить корпус мельницы, питатель, ремень и ограждение. Установить балансир, гидропривод, маслопровод. Соединить фланцевые стыки. Опробовать мельницу и сдать в эксплуатацию.
9.3.11. Мельницы мокрого помола. Снять трубную обвязку, арматуру, ограждения, клиновидные ремни, электродвигатель, шкив, редуктор, промежуточный и вертикальный валы, хомуты крепления бегунов, бегуны, поворотную чашу. Очистить и разбраковать детали, дефектные заменить. Провести ревизию редуктора. Установить поворотную чашу, бегуны, хомуты крепления бегунов, вертикальный и промежуточный валы, редуктор, шкив, электродвигатель, клиновидные ремни, ограждения, арматуру, трубную обвязку. Опробовать аппарат вхолостую и сдать в эксплуатацию.
9.3.12. Грохоты. Снять ограждения привода, ременную передачу и шкивы с валов вибратора и электродвигателя. Снять электродвигатель, кожухи вала и вибратора, фиксаторы и дебалансы, крышки подшипников. Спрессовать втулки и подшипники и вынуть вал привода вибратора с распорной трубой. Снять сита, прижимные планки и уплотнения. Разобрать подвески, снять короб и течки грохота. Очистить, промыть и разбраковать детали, дефектные заменить. Установить и закрепить короб, подвески, сетки на планки, прижимные планки, распорную трубу с валом привода вибратора. Напрессовать втулки и подшипники. Установить и закрепить кожух вала вибратора, шкивы на валы, электродвигатель, ременную передачу, ограждения и течки. Испытать грохот и сдать в эксплуатацию.
9.3.13. Измельчитель пластмасс роторный. Снять защитный кожух муфты, электродвигатель, направляющую и нижнюю части бункера, верхнюю крышку и решетку статора, ножи ротора и статора, крышку крепления ротора, ротор, крышки подшипников, стаканы, подшипники, нижнюю решетку статора, статор, электродвигатель, вентилятор, крыльчатку с вала. Очистить и разобрать детали, дефектные заменить. Отбалансировать крыльчатку. Установить крыльчатку на вал, вентилятор, электродвигатель, статор, нижнюю решетку статора, подшипники, стаканы, крышки подшипников, ротор, крышку крепления ротора, ножи ротора и статора, верхние решетку и крышку статора, нижнюю и направляющую части бункера, электродвигатель, защитный кожух муфты. Испытать измельчитель на холостом ходу и под нагрузкой, сдать в эксплуатацию.
9.4. Нормативы периодичности, продолжительности и трудоемкости ремонта
Нормативы периодичности, продолжительности и трудоемкости ремонта дробильно-размольного и сортировочного оборудования приведены в табл. 9.1.
Таблица 9.1
10. ЭЛЕКТРИЧЕСКИЕ МАШИНЫ
Указания по ТО и ремонту приведены для следующих типов электрических машин: асинхронные, синхронные и постоянного тока.
10.1. Техническое обслуживание
10.1.1. Операции ТО для всех типов электрических машин, являются подобными и выполняются, как правило, при регламентированном обслуживании.
10.1.2. При ТО производятся следующие работы: мелкий ремонт, не требующий специальной остановки машины и осуществляемый во время перерывов в работе технологических установок с целью своевременного исправления незначительных дефектов, в том числе: подтяжка контактов и креплений; смена щеток; регулировка траверс, устройств, обеспечивающих выходные параметры генераторов, умформеров и преобразователей; регулировка защиты; протирка и чистка доступных частей машины (наружных поверхностей, колец, коллекторов и т. д.); повседневный контроль выполнения ПТЭ и инструкций заводов-изготовителей, в частности, контроль нагрузки, температуры подшипников, обмоток и корпуса, а для машин с замкнутой системой вентиляции – температуры входящего и выходящего воздуха; контроль наличия смазки; проверка отсутствия ненормальных шумов и гула, а также отсутствия искрения на коллекторах и кольцах; повседневный контроль исправности заземления; отключение электромашин в аварийных ситуациях; участие в приемо-сдаточных испытаниях после монтажа, ремонта и наладки электрических машин и систем их защиты и управления.
10.1.3. Для взрывозащищенных электродвигателей дополнительно производится: проверка состояния взрывонепроницаемой оболочки; затяжка креплений болтов, гаек, охранных колец; проверка исправности вводных устройств, наличия элементов уплотнения и закрепления кабелей. Для электродвигателей, работающих в подземном варианте, производится: очистка дренажных отверстий во фланцах для выпуска масла и вывинчивание винтов нижних смазочных отверстий, проверка системы подвода и отвода воды; проверка наличия уплотнительных резиновых колец, заглушек и изоляторов, токоведущих зажимов вводных устройств и кабелей всех размеров.
10.2. Текущий ремонт
10.2.1. Типовая номенклатура работ при текущем ремонте электрических машин включает в себя все операции ТО; кроме того:
электродвигатели асинхронные с короткозамкнутым ротором: частичная разборка электродвигателя; проверка исправности работы и крепления вентилятора; проточка шеек вала ротора и ремонт «беличьей клетки» (при необходимости); проверка зазоров; смена фланцевых прокладок и закладка смазки в подшипники качения; замена изношенных подшипников качения, промывка подшипников скольжения и, при необходимости, их перезаливка; восстановление заточек у щитов электродвигателя; сборка электродвигателя с испытанием на холостом ходу и в рабочем режиме; проверка креплений машины и исправности заземлений;
электродвигатели асинхронные с фазным ротором: разборка электродвигателя; устранение поврежденных мест обмоток статора и ротора без их замены; промывка механических узлов и деталей электродвигателя; замена неисправных пазовых клиньев и изоляционных втулок; пропитка и сушка обмоток; покрытие обмотки покрывным лаком; проверка исправности и крепления вентилятора; при необходимости – проточка шеек вала ротора, проверка зазоров, смена фланцевых прокладок, промывка и закладка смазки в подшипники качения, замена изношенных подшипников качения, промывка подшипников скольжения и при необходимости их перезаливка, восстановление заточек у щитов электродвигателя, проточка и шлифовка колец, при необходимости – их замена, регулирование и крепление траверсы щеткодержателя, ремонт щеточного механизма, замена щеток, сборка электродвигателя с испытанием на холостом ходу и в рабочем режиме, проверка креплений электродвигателя и исправности заземления;
электродвигатели асинхронные высоковольтные и синхронные: разборка электродвигателя и осмотр его деталей; ремонт изоляции обмоток, пропитка и сушка; замена неисправных клиньев, крепящих обмотку; замена износившихся бандажей, замена щеток, осмотр и проверка работы пусковых устройств электродвигателя; замер зазоров между ротором и статором; сборка электродвигателя и испытание (пробные пуски);
электрические машины постоянного тока: проверка доступных креплений, состояния коллектора и щеткодержателей; проверка состояния всего вспомогательного оборудования на машине; разборка электромашины; проверка состояния подшипников, шеек вала с измерением зазоров, изоляции подшипников, смена смазки; продороживание коллектора, снятие фасок пластин, шлифовка коллектора, ремонт щеткодержателей, замена изношенных щеток, проверка обмоток и бандажей с замером сопротивления изоляции; проверка состояния пазовых клиньев, бандажей, распорок уравнителей, нажимных планок, обмоткодержателей; проверка состояния паек якоря методом падения напряжения; восстановление лаковых покрытий обмоток и других частей; измерение зазоров междужелезного пространства и сборка машины; проверка состояния заземления корпуса машины; испытание в работе.
10.2.2. Для взрывозащищенных электродвигателей дополнительно производится проверка взрывозащитных поверхностей фланцев и их уплотнений, проверка качества уплотнения кабеля, соответствия размеров уплотнительного кольца диаметру расточки ввода; проверка сопротивления изоляции электродвигателя, состояния контактных колец, щеткодержателей и щеток (для электродвигателей с контактными кольцами), контроль ширины взрывонепро-ницаемых щелей (зазоров) между крышками и корпусом.
10.3. Капитальный ремонт
10.3.1. Типовая номенклатура работ при капитальном ремонте электрических машин включает в себя все операции текущего ремонта; кроме того:
электродвигатели асинхронные с короткозамкнутым ротором: полная разборка электродвигателя с полной или частичной заменой обмоток; проточка шеек вала или замена вала ротора; балансировка ротора; замена вентилятора и фланцев; сборка электродвигателя и испытание его под нагрузкой;
электродвигатели асинхронные с фазным ротором: полная разборка электродвигателя с полной или частичной заменой обмоток статора и ротора; замена при необходимости вала ротора; переборка колец; балансировка ротора; ремонт замыкающего и контактного устройств; замена вентилятора и фланцев; замена щеточного механизма; сборка и окраска электродвигателя и испытание его под нагрузкой;
электродвигатели асинхронные высоковольтные и синхронные: полная разборка электродвигателя и устранение обнаруженных дефектов; выемка ротора, ремонт ротора (железа ротора и обмотки или стержней клетки и контактных колец); ремонт подшипников; ремонт статора (железа статора и обмотки); замена (частичная или полная) обмоток (катушек полюсов) при необходимости; измерение и испытание электрической прочности изоляции обмоток; ремонт воздухоохладителя и системы охлаждения; сборка электродвигателя и испытание в рабочем режиме;
электрические машины постоянного тока: полная разборка электрической машины; промывка узлов и деталей; замена неисправных пазовых клиньев и изоляционных обмоток или их ремонт с последующей не менее чем двухкратной пропиткой; правка, проточка шеек или замена вала ротора и ремонт «беличьей клетки»; ремонт или изготовление подшипниковых щитов и фланцев; переборка контактных колец или коллектора; ремонт и регулировка щеточных механизмов; полная пропайка «петушков»; замена вентилятора и крепежных деталей; проверка крепления активного железа на валу и в статоре и его ремонт при необходимости; сборка и окраска электрической машины, испытание в соответствии с ГОСТ для новых машин. Для электромашин мощностью более 200 кВт – разборка машины с выемкой якоря или сдвигом магнитной системы, производство измерений и испытаний в целях выявления дефектов; чистка и пропитка, сушка и покраска обмоток; подтяжка и проточка коллектора, перезаклиновка якоря и замена стальных бандажей, перезаливка или замена подшипников; при необходимости – полная или частичная перемотка обмоток машины, переборка или замена коллектора; балансировка якоря; сборка машины; внешняя окраска, испытание машины на холостом ходу и под нагрузкой.
10.4. Нормативы периодичности, продолжительности и трудоемкости ремонта
Периодичность ремонта установлена для электрических машин, работающих в нормальных условиях эксплуатации. Нормативы периодичности, продолжительности и трудоемкости ремонта электрических машин приведены в табл. 10.1.
Трудоемкость ремонта в табл. 10.1 дана только на ремонт собственно электрических машин без учета ремонта пускорегулирующих устройств и регуляторов частоты вращения, напряжения и другой коммутационной аппаратуры, трудоемкость ремонта которых устанавливается отдельно.
Таблица 10.1
Примечания.
1. Для электрических машин, работающих в тяжелых условиях (горячие, химические, гальванические, деревообрабатывающие и т. п. цеха), а также используемых с длительными циклами непрерывных работ и с высокой степенью загрузки (приводы насосов, компрессоров, вентиляторов, кондиционеров, двигателей-генераторов, дробилок, мельниц, землесосов, умформеров и т. д.) капитальный ремонт следует планировать не реже чем через 17 280 ч, текущий – не реже чем через 4320 ч. Разрешается производить ремонт электродвигателей, конструктивно входящих в состав оборудования, в соответствии с периодичностью ремонта этого оборудования, если она не превышает значений, приведенных в табл. 10.1.
2. Трудоемкость и продолжительность простоя в ремонте асинхронных электродвигателей приведена для электродвигателей с короткозамкнутым ротором. Для электродвигателей с фазным ротором, взрывозашищенных, многоскоростных, погружных и крановых трудоемкость и продолжительность простоя в ремонте принимается с коэффициентом 1,3.
3. Нормативы трудоемкости ремонта приведены для электродвигателей с невсыпными обмотками исходя из обеспечения их готовыми секциями заводского изготовления. Для электродвигателей с всыпными обмотками трудоемкость принимается с коэффициентом 1,8.
4. Нормативы трудоемкости ремонта приведены для машин с частотой вращения 1500 об/мин. Для электрических машин с другими частотами вращения вводятся следующие коэффициенты: 3000 об/мин – 0,8; 1000 об/мин – 1,1; 750 об/мин – 1,2; 600 об/мин – 1,4; 500 об/мин – 1,5.
5. Трудоемкость ремонта высоковольтных электродвигателей приведена для напряжения 3,3 кВ. Для электродвигателей напряжением 6,6 кВ и более трудоемкость следует принимать с коэффициентом 1,3.
6. Для двух-, трех– и более машинных агрегатов, умформеров, двигателей-генераторов трудоемкость ремонта агрегата в целом принимается как сумма трудоемкостей ремонта всех входящих в состав агрегата машин (в том числе и привода), умноженная на коэффициент 1,6.
11. КОМПРЕССОРНО-ХОЛОДИЛЬНОЕ ОБОРУДОВАНИЕ И НАСОСЫ
В раздел включены компрессоры: воздушные, аммиачные, фреоновые, детандеры; вспомогательное оборудование; насосы: центробежные, поршневые, вихревые, вакуумные, разные.
Сроки полезного использования компрессоров установлены свыше 5 до 7 лет. Сроки полезного использования насосов: центробежные, поршневые и роторные – свыше 5 лет до 7 лет, артезианские и погружные – свыше 3 лет до 5 лет, грунтовые, песковые, шламовые, питательные – от 2 до 3 лет.
11.1. Техническое обслуживание
11.1.1. Техническое обслуживание компрессорно-холодильного оборудования и насосов предусматривает производство следующих работ: контроль отсутствия посторонних шумов и стуков, ненормальных вибраций. Контроль температуры подшипников, уровня, давления и температуры масла и охлаждающей воды, качества (цвета) масла, температуры и давления воздуха по ступеням. Проверка внешнего состояния оборудования, правильности работы, доступных для осмотра движущихся частей. Контроль исправного состояния и правильного положения запорной аппаратуры и предохранительных клапанов, соблюдения экономичных и безопасных режимов работы. Отключение неисправного оборудования.
11.1.2. Кроме того, по отдельным видам оборудования проводятся следующие работы:
компрессоры всех видов: очистка, промывка клапанов. Замена вышедших из строя пружин и пластин. Очистка клапанных коробок от нагара и грязи. Проверка клапанных гнезд и плотности закрывания клапанов. Проверка надежности крепления кольца и состояния деталей крейцкопфа, состояния поршня и штока, надежности крепления сальниковых и предсальниковых уплотнений, а также междуфланцевых прокладок. Осмотр и очистка лубрикатора, обратных клапанов в маслопроводе. Замена загрязненного масла, очистка и промывка масляных и воздушных фильтров. Проверка состояния фундамента, анкерных креплений, надежности шплинтовки шатунных болтов и болтов противовесов. Контроль величины зазоров в мотылевых подшипниках, а также зазоров, контроль которых предусмотрен заводской инструкцией при проведении осмотров данного вида компрессоров. Проверка состояния промежуточных и конечных холодильников, масловодоотделителей, установок осушки воздуха, ресиверов;
центробежные насосы: проверка осевого разбега и свободного вращения вала, соосности насоса с приводным электродвигателем, а также состояния пальцев соединительной муфты. Проверка работы приемного и обратного клапанов. Устранение течи между секциями в многоступенчатых секционных насосах. Подтяжка направляющих болтов;
поршневые паровые насосы: осмотр и проверка наружного механизма парораспределения, состояния всасывающих и нагнетательных клапанов. Перенабивка сальников. Очистка приемной сетки и проверка фланцевых соединений;
холодильные машины и агрегаты: проверка состояния конденсатора, испарителя, ресивера, маслоотделителя. Спуск масла и воздуха. Устранение неплотностей во фланцевых соединениях. Проверка уровня аммиака в вертикально-трубном и кожухотрубном испарителях. Проверка всей запорной и регулирующей арматуры. Очистка сетки грязеуловителя. Проверка состояния автоматических устройств и их регулировка. Проверка состояния щитов, работы насосов, компрессоров и состояния всех коммуникаций.
11.2. Текущий ремонт
11.2.1. Текущий ремонт компрессорно-холодильного оборудования и насосов производится на месте установки данного оборудования; только оборудование малой массы ремонтируется в специализированных цехах (участках) предприятия.
11.2.2. Типовая номенклатура ремонтных работ при текущем ремонте включает в себя операции ТО, частичную разборку оборудования с ремонтом и заменой наиболее быстроизнашивающихся деталей. Кроме того, для отдельных видов оборудования в типовой объем работ при текущем ремонте включаются специфические для данного вида оборудования работы.
11.2.3. Компрессоры поршневые и ротационные: осмотр клапанов, пружин, воздушных коробок и очистка их от нагара и грязи. Проверка клапанов на плотность прилегания и протирка пластин. Проверка состояния клапанных гнезд. Промывка, чистка и (при необходимости) ремонт (замена) подшипников. Смена загрязненного масла, подтяжка болтов ползуна и кривошипа. Осмотр и протирка кранов, проверка прокладок между фланцами. Проверка обратных клапанов на маслопроводах. Проверка креплений всех движущихся частей компрессора. Осмотр валов, очистка и промывка воздушных, масляных фильтров. Замена клапана или клапанных пластин. Проверка крепления кривошипных противовесов, снятие крышек цилиндров, очистка их от нагара и зачистка поврежденных заеданием мест. Промывка, очистка рубашек цилиндров и промежуточных холодильников от ила и накипи. Очистка поршней от нагара. Проверка клапанов и замена изношенных частей. Замена рабочих лопаток и рабочих колец ротационных компрессоров. Шлифование крышек ротационных компрессоров. Очистка ротора от нагара в ротационных компрессорах, проверка и регулировка зазоров этих компрессоров. Проверка и регулировка вредных (мертвых) пространств поршневых компрессоров, проверка и смена негодных клапанных пружин. Проверка и регулировка регуляторов давления. Проверка шейки вала на конусность, эллиптичность и ремонт (при необходимости). Проверка цельности шпилек коренных подшипников, проверка шатунных болтов, проверка крепления поршневых гаек, крепящихся с поршнем. Очистка картера станины, проверка центровки компрессора с электродвигателем. Сборка и окраска.
11.2.4. Турбокомпрессоры и турбовоздуходувки: разборка ограничителя частоты вращения, разборка и очистка нагнетателя. Разборка картера и промывка его от нагара и грязи. Проверка состояния системы охлаждения, плотности присоединений с заменой прокладок. Смена масла.
11.2.5. Холодильные машины и агрегаты: вскрытие, внутренний осмотр и устранение обнаруженных дефектов в маслоотделителе, конденсаторе, ресивере и испарителе. Замена отдельных трубок в конденсаторе и испарителе. Полное удаление из конденсатора масла, загрязнений и водяного камня. Проверка ресивера и системы на герметичность. Замена крепежных деталей и прокладок. Проверка креплений корпусов к опорным конструкциям.
11.2.6. Центробежные насосы: отсоединение электродвигателя, отключение от сети. Разборка муфты, подшипников и секций насоса, осмотр и проверка всех деталей. Контроль осевого разбега ротора и зазоров в уплотнениях и подшипниках, проверка вала. Контрольная сборка ротора, снятие и посадка соединительной муфты с пригонкой шпонок и шпоночных пазов. Замена сальниковой втулки (рубашки на валу) без снятия и посадки других деталей, замена болтов соединительной муфты, замена дополнительного кольца (двух полуколец) насоса. Статическая балансировка рабочего колеса, центровка насоса с электродвигателем. Опробование насоса.
11.2.7. Поршневые насосы: осмотр и проверка наружного механизма парораспределения. Проверка плотности парозапорного вентиля, проверка и очистка приемной сетки, проверка фланцевых соединений, перенабивка сальников. Осмотр всасывающих и нагнетательных клапанов. Смена шпилек и гаек крышек цилиндров, зашлифовка царапин и рисок втулок. Выемка поршня, проверка креплений штока и соединения поршневых колец, смена и пришлифовка поршневых колец, перекрепление штока. Смена сальниковой втулки, переборка, притирка и опрессовка парозапорного вентиля и механизма передачи. Смена пальцев шарнирных соединений. Пришабровка и пришлифовка зеркала золотников. Смена шпинделя или седла, расточка гнезда парозапорного вентиля, смена креплений и фланцев паропровода. Смена или ремонт конденсационного горшка. Переборка приемного клапана. Очистка, промывка, опрессовка всасывающего трубопровода. Сборка и опробование насоса.
11.3. Капитальный ремонт
11.3.1. Капитальный ремонт включает в себя работы текущего ремонта, полную разборку оборудования, промывку, дефектовку деталей, замену негодных деталей.
После капитального ремонта оборудование, на которое распространяются требования Ростехнадзора, подвергается соответствующим испытаниям и предъявляется представителям Ростехнадзора. Кроме того, проводятся следующие работы по видам оборудования.
11.3.2. Компрессоры поршневые и ротационные: разборка коренных выносных подшипников, их перезаливка и подгонка. Разборка и снятие маховика, выемка коленчатого вала, расточка цилиндра. Замена поршня, снятие, очистка и замена сработавшихся поршневых колец. Проверка канавок и пригонка новых поршневых колец. Проверка поршневого и крейцкопфного пальцев на эллиптичность, конусность и их ремонт. Отсоединение штока от поршня и его шлифование на станке. Пригонка всех подшипников и их перезаливка. Проверка диаметра и длины штока, при необходимости – ремонт или замена его новым. Проверка правильности положения шатуна по отношению к валу и к поршню и устранение перекосов. Проверка и промывка керосином маслопроводов, масленок и изношенных деталей масляного насоса. Проточка и шлифование коренных и шатунных шеек коленчатого вала. Очистка от грязи и накипи всех охлаждающих поверхностей. Осмотр и проверка промежуточного и концевого холодильников и замена изношенных труб и змеевиков. Осмотр и очистка воздушного ресивера масловодоотделителей и конденсационных горшков и их ремонт. Очистка трубопроводов нагнетания от компрессора до ресивера от грязи, нагара и масла. Проверка, ремонт и испытание на плотность всей запорной арматуры. Проверка крепления станины, компрессора и состояния фундаментных болтов. Проверка и ремонт всех предохранительных клапанов и регуляторов давления. Сборка и окраска.
После капитального ремонта компрессор подвергается испытаниям по программе, обеспечивающей проверку качества проведенного ремонта, состояния системы контроля, регулирования производительности и аварийной защиты.
Все данные о проведенных ремонтах и результатах испытаний должны быть записаны в формуляр компрессора, а данные о ремонте и испытании воздухосборника – в паспорт воздухосборника.
11.3.3. Турбокомпрессоры и воздуходувки: полная разборка, замена дисков, проверка вала, его ремонт или замена. Ремонт нагнетателя и системы охлаждения. Динамическая балансировка ротора и крыльчатки.
11.3.4. Холодильные машины и агрегаты: полная разборка и ремонт с заменой трубных решеток и труб в конденсаторе и испарителе. Промывка и очистка маслоотделителя, грязеуловителя, маслосборника, промежуточного сосуда и циркуляционного насоса. Продувка охлаждающих батарей и их ремонт с заменой труб и фланцев. Очистка наружных поверхностей батарей от ржавчины и старой краски, просушка и окраска. Ремонт креплений батареи и опорных конструкций других аппаратов.
11.3.5. Насосы центробежные: полная разборка насоса, разборка ротора. Ремонт дисков и корпуса, замена изношенных дисков и других деталей. Замена подшипников, крепежных деталей и прокладок.
11.3.6. Насосы поршневые: расточка цилиндровых втулок, смена или ремонт поршней и плунжеров. Правка или замена штоков, полная переборка золотниковой коробки и ее ремонт. Замена поршневых колец, перезаливка или замена вкладышей подшипников.
11.4. Нормативы периодичности, продолжительности и трудоемкости ремонта
11.4.1. Периодичность текущего и капитального ремонтов компрессорно-холодильного оборудования и насосов в значительной степени зависит от назначения и вида энергоносителя. Для центробежных насосов периодичность ремонта приведена при перекачке ими холодной воды. При использовании центробежных насосов в других условиях периодичность ремонта следует принимать следующей:
для перекачки горячей воды Т = 2160 ч, K = 25 920 ч;
для перекачки агрессивных вод и бензина Т = 2160 ч, K = 17 280 ч;
для химически активных жидкостей и кислот Т = 1440 ч, K = 8640 ч.
11.4.2. Трудоемкость ремонта компрессорно-холодильного оборудования и насосов приведена в табл. 11.1 без учета трудозатрат на ремонт электрических и паровых машин и пусковой аппаратуры.
Таблица 11.1
П р и м е ч а н и я:
1. Нормы трудоемкости ремонта консольных насосов для кислот, щелочей, а также фарфоровых насосов принимаются с поправочным коэффициентом 1,2.
2. Нормы трудоемкости ремонта артезианских насосов увеличиваются на 5 % на каждую последующую ступень свыше шести ступеней для погружных насосов и трех ступеней для электронасосов над скважиной.
3. Трудоемкость ремонта многоступенчатых насосов с числом секций более трех увеличивается на 5 % на каждую последующую пару секций.
12. ОБОРУДОВАНИЕ ВЕНТИЛЯЦИИ И КОНДИЦИОНИРОВАНИЕ ВОЗДУХА
Включенное в раздел оборудование относится к пятой амортизационной группе со сроком полезного использования свыше 7 лет до 10 лет включительно.
Рекомендации по ремонту и ремонтные нормативы приведены применительно к указанным выше срокам службы оборудования.
12.1. Техническое обслуживание
12.1.1. При ТО оборудования систем вентиляции и кондиционирования воздуха проводятся следующие виды работ: повседневный надзор за работой оборудования и плановые осмотры оборудования.