Строительство нефтяных и газовых скважин Новиков А.
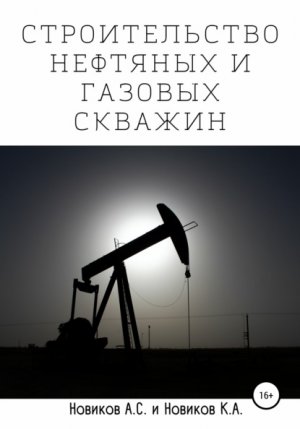
c. Наращивание/разборка бурильной колонны свечами и одиночными трубами;
d. Свинчивание/развинчивание бурильных труб, докрепление/раскрепление резьбовых соединений переводников и шаровых кранов;
e. Подача бурильных труб к стволу/удаление от ствола вертлюг. Проведение операций по спуску обсадных колонн в скважину.
f. Промывка скважины и одновременное проворачивание бурильной колонны.
g. Задание и обеспечение величин крутящего момента и частоты вращения, их измерение и вывод показаний на дисплей шкафа управления, выносной дисплей, пульт управления и на станцию геолого-технических исследований.
h. Дистанционное управление.
i. Герметизация внутритрубного пространства шаровыми кранами.
Преимущества СВП – экономия времени в процессе наращивания труб при бурении, коме того:
• Уменьшение вероятности прихватов бурового инструмента;
• Расширение/проработка ствола скважины при спуске и подъеме инструмента;
• Повышение точности проводки скважин при направленном бурении;
• Повышение безопасности буровой бригады;
• Снижение вероятности выброса флюида из скважины через бурильную колонну;
• Облегчение спуска обсадных труб в зонах осложнений за счет вращения и промывки;
• Повышение качества керна.
Согласно требований правил в НГДП, буровые установки должны оснащаться верхним приводом при: [25]
1. Бурении скважин с глубины более 4500 м;
2. Вскрытии пластов с ожидаемым содержанием в пластовом флюиде сероводорода свыше 6 (объемных) процентов;
3. Наборе угла с радиусом кривизны менее 30 м в наклонно-направленных скважинах;
4. Бурении горизонтального участка ствола скважины длиной более 300 м в скважинах глубиной по вертикали более 3000 м.
Верхний силовой привод должен быть совместим со средствами механизации спускоподъемных операций. Управление исполнительными механизмами и приводом силового блока должно осуществляться с пульта управления, расположенного компактно с пультами управления другим оборудованием буровой установки (лебедкой, автоматическим ключом и др.). Элементы верхнего привода (направляющие балки, модуль исполнительных механизмов и т. д.) не должны создавать помех для ведения других технологических операций. Грузоподъемность верхнего привода должна соответствовать грузоподъемности буровой установки. Конструкция верхнего привода должна предусматривать наличие системы противофонтанной арматуры, датчиков положения исполнительных механизмов, скорости вращения стволовой части и момента вращения. Технические характеристики верхнего привода ИПВЭ-250 приведены в таблице 2.
Таблица 2. Технические характеристики верхнего привода ИПВЭ-250
Предназначены для свинчивания и развинчивания бурильных, обсадных, насосно-компрессорных труб и штанг.
• Машинные ключи подвешиваются горизонтально на стальных канатах диаметром не менее 12,8 мм, и оборудуется контргрузами для легкости регулирования высоты, либо пневмоцилиндрами.
• Машинный ключ, кроме рабочего каната, оснащается страховым канатом диаметром не менее 18 мм, который одним концом крепится к корпусу ключа, а другим – к основанию вышки. Страховой канат должен быть длиннее рабочего на 5–10 см. Машинные ключи должны проходить периодическую проверку методами дефектоскопии.
Таблица 3. Техническая характеристика подвесных машинных ключей
На практике для спуска обсадных колонн используют УМК-1, с добавочным шарниром.
Для насосно-компрессорных труб в основном используются ключи КТГУ. Им пользуются как при ручной работе, так и при помощи механизмов АПР 2ВБ и др.
На практике, на износ сменных элементов ключа, кроме сухарей, мало обращают внимания. За счет частого приложения значительных усилий, сменные элементы ключа имеют остаточную деформацию (удлиняются), и при работе ключа проскальзывают на замке трубы. Использование лома для фиксации ключа на замке трубы, часто приводит к травмам и смертельным случаям персонала буровой бригады.
Ключи шарнирные для бурильных геологоразведочных труб выпускаются для труб диаметром от 33,5 мм до 63,5 мм. Ключи шарнирные для труб нефтяного сортамента выпускаются размерами от 34,5 мм до 243 мм.
Штропы – предназначены для подвески элеватора на крюк талевой системы. Конструктивно это замкнутая стальная петля овальной формы, сильно вытянутая по оси. Изготавливаются цельнокатаными и сварными. Штропы различают:
• Буровые нормальные ШБН;
• Буровые укороченные ШБУ;
• Эксплуатационные ШЭ.
Выпускаются грузоподъемностью от 10 до 320 т.
Элеватор предназначен для захвата колонны труб под муфту, либо под хомут при отсутствии муфты, либо под проточку (УБТ).
При бурении нефтяных и газовых скважин применяют двухштропные элеваторы. Корпус элеватора выполняется литым или кованым. Элеваторы могут быть как для бурильных так и для обсадных труб. Выпускаются диаметрами от 60 мм до 478 мм. Грузоподъемность до 320 т. Для спуска и подъема УБТ, при отсутствии проточки на теле УБТ применяют специальные клинья. Однако, высокая аварийность с ручными клиньями, ограничивает их применение.
§ 6. Буровые насосы, механизмы очистки раствора
Буровые насосы предназначены для промывки скважины (Рис. 2.8.) [9] В настоящее время промышленностью выпускаются насосы двухцилиндровые и трехцилиндровые поршневые и плунжерные, быстроходные одностороннего действия. Способны производить промывку скважины при высоких давлениях в широком диапазоне подачи.
Забор бурового раствора производится из мерных емкостей циркуляционной системы, может подаваться посредством подпорного насоса. Далее насос, рис 2.8. под давлением подает раствор через систему трубопроводов высокого давления – манифольдов в колонну бурильных труб. Рабочее давление создаваемое буровыми насосами может варьироваться до 30 МПа в зависимости от диаметра подобранных поршней и оборотов насоса. Приводится буровой насос от двигателя внутреннего сгорания через понижающий редуктор, или от электродвигателя.
Рис. 2.8. Буровой насос
Буровой насос состоит из:
• Механическая часть;
• Гидравлический блок;
• Основание насоса;
• Всасывающий коллектор;
• Выкидной фланец;
• Компенсатор;
• Предохранительный узел;
• Приводное колесо;
• Система омыва (охлаждения) штоков.
Механическая часть состоит из корпуса, в котором установлен коленвал с зубчатыми шестернями. На шатунных шейках коленвала установлены шатуны. Поступательное движение от шатунов передается к ползунам (крейцкопфам). К крейцкопфу крепится полушток, а к полуштоку – шток поршня. Гидравлическая часть представляет собой два или три (в зависимости от вида насоса) гидравлических блока, каждый гидравлический блок состоит из металлической отливки с каналами для бурового раствора, имеет всасывающую и выкидную полость с соответствующими клапанами и поршень смонтирован на шоке. Всасывающий коллектор представляет собой трубопровод, через который происходит засасывание бурового раствора поршнем через всасывающие клапана. К выкидному фланцу подсоединяется манифольд. Компенсатор служит для сглаживания пульсации давления в выкидном коллекторе, которое получается в результате поочередной работы поршней. Компенсатор имеет внутри резиновый баллон заполненный инертным газом (азотом) под давлением от 2 до 5 Мпа. Предохранительный узел представляет собой металлический корпус с установленным внутри предохранительным клапаном отрегулированным на определенное давление срабатывания. Служит для сброса бурового раствора в мерные емкости при аварийном повышении давления.
Система омыва штоков представляет собой следующее: насос приводимый электродвигателем забирает жидкость (масло или воду) из специальной емкости установленной под буровым насосом и подает её на движущиеся штока поршней, жидкость омывая штока и одновременно охлаждая их сливается обратно в емкость, цикл повторяется. [9]
Главный параметр насоса – мощность.
Nг = P*Q/7,5 л. с (2.1)
Где:
P-давление развиваемое насосом, кг/см2;
Q-расход жидкости, л/с;
Буровой раствор, выполняя одну из своих основных функций – вынос шлама и очистку забоя, раствор при этом загрязняется, теряя свои заданные свойства, удовлетворяющие условиям бурения скважины:
• Меняется плотность бурового раствора;
• • Ухудшаются фильтрационные свойства;
• Изменяются реологические константы раствора.
Без восстановления заданных свойств раствора дальнейшее безаварийное углубления скважины невозможно. Химическая обработка такого раствора неэффективна. Для восстановления свойств бурового раствора в циркуляционной системе имеются механизмы и устройства для: очистки бурового раствора – вибросита, Рис 2.8, это первая ступень очистки, удаляет 10–20 % шлама размером более 75–100 мкм. Очистная и пропускная способность вибросит определяется площадью ситовой поверхности, размером ячейки ситовой кассеты и виброускорением. Прямоугольное вибросито предназначено для очистки бурового раствора от частиц выбуренных пород при бурении нефтяных, газовых и других скважин, и эффективно удаляет шлам из системы циркуляции.
Рис. 2.8. Вибросито
Постоянное накопление шлама в растворе ведет к увеличению плотности и высокому содержанию твердой фазы. Абразивные частицы, находясь в растворе при циркуляции, ведут к износу оборудования. Высокое содержание твердой фазы уменьшает механическую скорость бурения, а высокая плотность может привести к интенсивным поглощениям бурового раствора, что может привести к аварии. Для регулирования содержания твердой фазы и уменьшения плотности бурового раствора можно использовать следующие способы:
• Разбавление раствора водой;
• Замещение части бурового раствора более легким
• Осаждение частиц шлама в отстойниках очистка с помощью механических средств.
На практике обычно используют комбинацию из нескольких способов. Наиболее эффективным является способ очистки буровых растворов с помощью механических средств. [9] Он позволяет снизить влияние выбуренной породы на свойства раствора и как следствие сохранить его качество. Для этого применяют ряд механических средств, позволяющих сократить время взаимодействия и количество частиц в буровом растворе. Эти установки условно можно разделить по глубине очистки раствора от выбуренной породы, т. е. по размеру частиц удаляемых на конкретной установке. Средства тонкой очистки представлены более широким спектром механических средств: сито-гидроциклонные сепараторы, песко и илоотделители, деканторные центрифуги и т. п. Деление гидроциклонных сепараторов производится условно по диаметру внутренней цилиндрической части гидроциклона и по способности отделения частиц на пескоотделители и илоотделители. Центрифуги делятся на прямоточные и противоточные (характер движения жидкости внутри барабана), по отношению диаметра барабана к его длине, по скорости вращения барабана (высокоскоростные и низкоскоростные). Набор средств для очистки бурового раствора подбирается исходя из условий бурения и поставленных задач. Порядок прохождения раствора по установкам определяет схему циркуляции раствора и ступенчатость системы. Гидравлическая очистка промывочных жидкостей от шлама осуществляется в гидроциклонах и центрифугах. В основу гидроциклонного разделения твердых частиц и жидкости заложен принцип использования центробежных сил, возникающих в аппарате при прокачке через него жидкости. Гидроциклон (рис. 2.9.) представляет собой корпус 1, состоящий из верхней короткой цилиндрической части и нижней удлиненной конусной части. Из внутренней полости сосуда через верхнюю крышку выводится выходной патрубок 3, Конус заканчивается внизу выпускным каналом с песковой насадкой 4. Жидкость со взвешенными в ней твердыми частицами через сужающийся входной патрубок 2 С некоторым перепадом давления тангенциально вводится во внутреннюю цилиндрическую полость гидроциклона и приобретает вихревое движение. Под действием центробежных сил более крупные и тяжелые частички породы отбрасываются к стенкам гидроциклона и в результате сложного взаимодействия тангенциальных, радиальных и осевых сил сползают в нижнюю коническую часть аппарата. Здесь в первый момент работы аппарата накапливается некоторая часть песка до образования так называемой шламовой «постели», играющей роль гидравлического затвора на выходе гидроциклона. После образования «постели» вновь поступающий песок с частью жидкости сбрасывается через песковую насадку 4. Очищенная жидкость по внутреннему спиральному потоку поднимается через выходной патрубок 3. Окружная скорость вращательного движения жидкости в гидроциклоне приближенно определяется выражением: = A/R, где А – постоянная величина для данного гидроциклона, R – расстояние от оси гидроциклона. [9]
Рис. 2.9. Схема гидроциклона
1 – корпус;
2 – входной патрубок;
3 – выходной патрубок;
4 – песковая насадка.
Пескоотделители: Пескоотделители являются гидроциклонными сепараторами твердых частиц удаляющими частицы размером более 74 мкм, т. е. песок (абразивные частицы). Название «пескоотделитель» говорит само за себя: этот тип оборудования удаляет твердые частицы «песчаного» размера из буровых растворов. Для того чтобы производить более эффективное удаление твердых абразивных частиц, после вибросит обязательно устанавливают пескоотделитель.
Илоотделители: Илоотделители являются гидороциклонными сепараторами твердых частиц и удаляющие ил из бурового раствора. В зависимости от диаметра циклона зависит и тонкость очистки бурового раствора.
Центрифуга: Декантирующая центрифуга имеет цилиндрический конусообразный барабан (см рис. 2.10.) относительно большим соотношением длины и диаметра. Особенностью конструкции является встроенный внутри барабана шнековый конвеер, предназначенный для постоянной выгрузки отсепарированной твердой фазы. Скорость вращения барабана колеблется в пределах от 1000 до 4000 оборотов в минуту, позволяющая развивать силу “д” от 500 до 4000. Технологическая жидкость 3 подается в цилиндрическую секцию, где она образует слой вокруг стенок. Толщина этого слоя зависит от расположенных в концевой части порогов, через которые осветленная жидкость сливается под действием центробежной силы. Твердые частицы, как более тяжелые, собираются у стенки барабана и откуда они непрерывно выводятся с помощью шнекового конвейера и поднимаются вверх по конической части – намыву (пляжу) – и далее наружу через выгрузные отверстия 5, расположенные в суженной части конуса барабана.
Рис. 2.10. Декантирующая центрифуга
Технические характеристики оборудования для очистки бурового раствора отечественного производства. Для химической обработки бурового раствора и приготовления раствора в циркуляционной системе предусмотрены механизмы и оборудование для быстрого приготовления раствора – глиномешалки, гидроворонки, дозировочные емкости для ввода жидких реагентов. Кроме того, циркуляционная система позволяет иметь необходимое количество раствора, заданных свойств, для обеспечения предупреждения и ликвидации нефтегазопроявлений и фонтанов.
Дегазаторы Служат для удаление воздуха, газа из раствора, [9]. Кислые газы, такие как двуокись углерода, могут привести к понижению рН раствора и вызвать его флокуляцию. Снижение гидравлической мощности вследствие присутствия в растворе газа отрицательно сказывается на всем процессе бурения. Оптимизированные программы бурения требуют, чтобы на долоте срабатывалось до 65–70 % гидравлической мощности. Но снижение объемного коэффициента полезного действия насоса в результате газирования бурового раствора влечет за собой существенное уменьшение подачи насосов. Газ из пласта попадает в буровой раствор в результате отрицательного дифференциального давления между скважиной и пластом либо вследствие высокой скорости бурения, когда пластовый газ не успевает оттесниться фильтратом от забоя и стенок скважины и попадает в поток раствора вместе с выбуренной породой. Газ в буровом растворе может находиться в свободном, жидком и растворенном состоянии. По мере перемещения потока раствора к устью пузырьки свободного газа увеличиваются в объеме в результате снижения давления, сливаются друг с другом, образуя газовые пробки, которые прорываются в атмосферу. Свободный газ легко удаляется из раствора в поверхностной циркуляционной системе путем перемешивания в желобах, на виброситах, в емкостях. При устойчивом газировании, например во время бурения при несбалансированном давлении, свободный газ удаляют из бурового раствора с помощью газового сепаратора. Пузырьки газа, которые не извлекаются из бурового раствора при перепаде давления между ними и атмосферой, оказываются вовлеченными в буровой раствор, и для их удаления требуется дополнительная энергия. Полнота дегазации бурового раствора зависит от его плотности, количества твердой фазы, вязкости и прочности структуры. Существенную роль играют также поверхностное натяжение жидкости, размер пузырьков и силы взаимного притяжения. В связи с высоким поверхностным натяжением трудно поддаются дегазации буровые растворы на углеводородной основе, а также растворы, содержащие в качестве регулятора водоотдачи крахмал. Некоторые углеводороды, проникая из пласта в буровой раствор при повышенных температуре и давлении, остаются в жидком состоянии. Попадая в другие термодинамические условия, например в поверхностную циркуляционную систему, они превращаются в газ и заметно изменяют технологические свойства бурового раствора. Некоторые газы при повышенных температуре и давлении проникают в межмолекулярную структуру бурового раствора и вызывают едва заметное увеличение его объема. Наиболее опасны в этом отношении растворы на углеводородной основе, в которые может проникать большое количество пластового газа. Попадающий в циркуляционный поток газ приводит к изменению всех технологических свойств бурового раствора, а также режима промывки скважины. Кроме очевидного уменьшения плотности раствора изменяются также его реологические свойства – по мере газирования раствор становится более вязким, как и всякая двухфазная система. Пузырьки газа препятствуют удалению шлама из раствора, поэтому оборудование для очистки от шлама работает неэффективно. Кислые газы, такие как двуокись углерода, могут привести к понижению рН раствора и вызвать его флокуляцию. Обнаружить вовлеченный таким способом в буровой раствор природный газ очень трудно. Растворы, газированные сероводородом, создают особенные трудности при дегазации:
• Система дегазации должна быть весьма эффективной, так как при объемной концентрации 0,1 % сероводород – опасный яд;
• Сероводород взрывоопасен даже при объемной концентрации 4,3 % (для сравнения, нижний предел взрываемости метана 5 %);
• Сероводород растворим в буровых растворах, его растворимость в воде приблизительно пропорциональна давлению;
• Сероводород обладает высокой корродирующей способностью.
Различная степень газирования бурового раствора требует применения разного оборудования для дегазации. Свободный газ удаляется достаточно просто. Поток раствора из межтрубного пространства поступает в сепаратор, где газ отделяется от раствора и направляется по отводной линии на факел. Оставшийся в растворе свободный газ удаляется в атмосферу окончательно на виброситах или в емкости для сбора очищенного от шлама раствора. Газ, проникший в молекулярную структуру раствора, извлечь значительно труднее. Для этого требуется не только затратить некоторую энергию, но и часто необходимо применять понизители вязкости и поверхностного натяжения, если используется недостаточно совершенная система дегазации. Обычная схема дегазации бурового раствора при интенсивном поступлении газа (например, при несбалансированном давлении в скважине): Газожидкостный поток из скважины, дойдя до вращающегося превентора, через регулируемый штуцер и герметичные манифольды поступает в газовый сепаратор, где из раствора выделяется основной объем газа. Очищенный от свободного газа раствор поступает на вибросито и собирается в первой емкости циркуляционной системы. Дальнейшая очистка раствора от газа осуществляется с помощью специального аппарата-дегазатора. Окончательная дегазация происходит в промежуточных емкостях циркуляционной системы с помощью механических перемешивателей. Газовый сепаратор (рис. 2.11), используемый в качестве первой ступени очистки бурового раствора от газа представляет собой герметичный сосуд сравнительно большого объема, оборудованный системой манифольдов, клапанов и приборов.
Рис. 2.11. Сепаратор СРБ-2
Буровой раствор из скважины через вращающийся превентор и регулируемый штуцер по закрытому манифольду поступает по тангенциальному вводу в полость газового сепаратора, где скорость потока резко снижается. В результате действия инерционного и гравитационного полей происходит интенсивное выделение из бурового раствора газа, который скапливается в верхней части сепаратора и отводится по трубопроводу на факел. Буровой раствор, очищенный от свободного газа, собирается в нижней части газосепаратора, откуда он подается по линии для очистки от шлама на вибросито. Современные газовые сепараторы, имеющие вместимость 1–4 м3, рассчитаны на давление до 1,6 МПа и устанавливаются непосредственно над первой емкостью циркуляционной системы. Они оборудуются предохранительным клапаном, регулятором уровня бурового раствора поплавкого типа и эжекторным устройством для продувки и очистки сепаратора от накопившегося шлама. Однако при наличии в растворе токсичного газа, например сероводорода, поток из сепаратора по закрытому трубопроводу сразу подается на дегазатор для очистки от газа. В этом случае только после окончательной дегазации раствор очищают от шлама. В качестве второй, а иногда и единственной ступени очистки раствора от газа обычно применяют дегазаторы, которые условно классифицируют на следующие типы: по величине давления в камере – на вакуумные и атмосферные; по способу подачи газированного бурового раствора в камеру – на гравитационные, эжекционные и центробежные. При центробежной подаче бурового раствора используют, как правило, самопродувающиеся центробежные насосы. В вакуумных дегазаторах иногда применяют самозаполняющиеся центробежные насосы. Наибольшее распространение в отечественной и зарубежной практике получили вакуумные дегазаторы с эжекционной и центробежной подачей газированного бурового раствора. Разрежение в полости таких дегазаторов создается вакуумным насосом и эжектором. Газированный раствор подается в камеру дегазаторов обычно за счет разности давлений между атмосферой и вакуумированной камерой. Это не самый эффективный, но очень надежный способ подачи бурового раствора в дегазатор. Обычно центробежные насосы для этой цели непригодны вследствие способности «запираться» газовыми пробками. Степень вакуума в камере дегазаторов – наиболее важный технологический фактор дегазации и определяется не только разрежением в камере эжектора и техническими возможностями вакуум-насоса, но и, прежде всего, высотой всасывающей линии. Она должна быть такой, чтобы в камере дегазатора обеспечивался вакуум 0,03 МПа. Другим важным фактором, влияющим на глубину дегазации бурового раствора в дегазаторе, является длительность нахождения раствора в камере. Чем выше скорость циркуляции раствора в камере дегазатора, тем меньше времени раствор находится в ней и, следовательно, хуже дегазируется. Для улучшения дегазации необходимо уменьшать скорость циркуляции бурового раствора. Так, при циркуляции 24 л/с дегазация каждой порции раствора в аппаратах вакуумного типа будет длиться 25 с, а при 48 л/с – около 12 с. практически полная дегазация бурового раствора в аппаратах вакуумного типа происходит за 10–20 с. [9] Обычно с помощью газового сепаратора удается выделять из бурового раствора десятки кубических метров газа в минуту. Дегазатор – технологическая установка для дегазации бурового раствора, выполняющая следующие функции:
1. Восстановление удельного веса буровых промывочных растворов после их грубой очистки от выбуренной породы;
2. Выделение из бурового раствора попутных газов и направление их в газовоздушную линию использование либо в качестве первой ступени очистки раствора от газа, либо в качестве второй ступени после газового сепаратора (в случае метода бурения при равновесном и несбал ансированном давлении в скважине).
Рис. 2. 12. Дегазатор ДВС-3
В конструктивном и технологическом плане дегазаторы делятся на:
• Вакуумные
• Центробежно-вакуумные
• Атмосферные
Дегазаторы вакуумного типа по механизму работы делятся на дегазаторы Циклического и Непрерывного действия [9]
1.1. Вакуумные дегазаторы циклического действия представляют собой автоматизированные установки, в основе которых двухкамерная герметичная ёмкость. Камеры включаются последовательно при запуске золотникового устройства; Таким образом, производительность по раствору достигает 25–60 л/с. Дегазаторы вакуумного типа с механизмом непрерывного действия представлены горизонтальными цилиндрическими ёмкостями с наклонными пластинами, располагающимися в верхних частях этих ёмкостей.
Механизм работы: буровой раствор аэрируется, под действием вакуума поступает в камеру и там дегазируется, образуя тонкий слой на пластинах цилиндрических ёмкостей.
2.2. В основе дегазатора центробежно-вакуумного типа – цилиндрический вертикальный корпус. Дегазируемый буровой раствор разбрызгивается на стенки этого корпуса (раствор поступает в подводящий трубопровод под действием вакуума). Производительность этого механизма доходит до 50,5 л/с;
3.3. В атмосферном дегазаторе буровой раствор выделяется радиально на стенки цилиндрической вертикальной камеры.
В результате удара и распыления выделившийся газ уходит в атмосферу либо отсасывается воздуходувкой. Атмосферным механизмом производительность дегазатора может доходить до 38 л/с; Среди вакуумных дегазаторов наибольшее применение находит Дегазатор нефтегазовый самовсасывающий ДВС-3.
В результате на вторую ступень дегазации – в дегазатор – поступает буровой раствор с содержанием газа не более 20 %. Некоторые типы вакуумных дегазаторов обеспечивают скорость извлечения газа 0,1–0,25 м3/мин, пропуская буровой раствор объемом 1–3 м3/мин. В худшем случае остаточное содержание газа в буровом растворе после обработки в дегазаторе не превышает 2 %. Типичным представителем дегазаторов вакуумного типа, используемых в отечественном бурении, является дегазатор типа ДВС рис. 2.15. Вакуумный дегазатор представляет собой двухкамерную герметичную емкость, вакуум в которой создается насосом. Камеры включаются в работу поочередно при помощи золотникового устройства. Производительность дегазатора по раствору достигает 45 л/с, остаточное газосодержание в растворе после обработки не превышает 2 %. Привод вакуумного насоса осуществляется от электродвигателя мощностью 22 кВт. Центробежно-вакуумный дегазатор ЦВА состоит из цилиндрического вертикально установленного корпуса, внутри которого с высокой частотой вращается вал с ротором, подобным рабочему колесу центробежного насоса с загнутыми назад лопатками. Поступающий в ЦВА газированный буровой раствор интенсивно разбрызгивается ротором тонким слоем внутри корпуса и дегазируется. Дегазированный раствор перекачивается обратно в ЦС с помощью осевого насоса, а выделившийся из раствора газ отводится вентилятором по отводным каналам наружу. [9] Центробежно-вакуумный аппарат типа ЦВА обеспечивает не только эффективную дегазацию буровых растворов, но и интенсивное перемешивание входящих в него жидких и твердых компонентов В используемых в зарубежной практике атмосферных аппаратах дегазация бурового раствора происходит в результате турбулизации тонкого плоского потока. Обычно раствор в дегазатор такого типа поступает при подаче насоса примерно 35 л/с, чтобы скорость течения на входе в дегазатор составляла примерно 1 м/с. В камере дегазатора имеется система наклонных плоских перегородок, по которым стекает, периодически завихряясь, буровой раствор. Толщина слоя раствора на перегородках 10–15 мм, а длина пути раствора 3,5 м. Дегазаторы такого типа недостаточно эффективны при использовании растворов с повышенными значениями плотности, вязкости и СНС. Исследования показали, что даже при многократной дегазации таких растворов полного удаления газа из раствора достичь не удается. Отечественной промышленностью широко используется вакуумный дегазатор ДВС. Есть случаи, когда раствор из скважины выходит газированный, но это не работа пласта и утяжеление раствора приводит к поглощению промывочной жидкости с последующим газопроявлением. В этом случае решением может быть использование вышеперечисленных средств дегазации раствора (скважины на газовом месторождении Адамташ в Узбекистане).
Циркуляционная система буровой установки предназначена для приготовления, очистки, хранения бурового раствора, регулирования свойств и циркуляции бурового раствора, обеспечивающей вынос выбуренной породы и подведение мощности к забойному двигателю и долоту. Наземная часть циркуляционной системы может быть разбита на подсистему нагнетания и регулирования подачи бурового раствора, и подсистему приготовления, утяжеления, очистки, регенерации и регулирования свойств бурового раствора и глушение скважины при ГНВП. Многократная замкнутая циркуляция дает значительную экономическую выгоду благодаря сокращению расхода химических компонентов и других ценных материалов, входящих в состав буровых растворов. Важно также отметить, что замкнутая циркуляция предотвращает загрязнение окружающей среды стоками бурового раствора, содержащего химически агрессивные и токсичные компоненты.
Циркуляционная система буровой установки играет первостепенную роль в борьбе с проявлениями. Емкостной парк, насосы и вертлюги должны соответствовать номинальной глубине бурящейся скважины. При отсутствии или поломке дегазатора для удаления газа из бурового раствора требуются достаточная площадь свободной поверхности бурового раствора в емкостях и система перемешивания для всего раствора. Необходимо иметь мощные мешалки в емкостях – механические, пропеллерного типа, по 2 в каждой ёмкости, производительное оборудование для приготовления раствора. Правильность выбора схемы и комплекта оборудования циркуляционной системы, качество монтажа (герметичность системы, исправность оборудования, соблюдение необходимых уклонов желобов, устройство ограждений, размещение датчиков) значительно влияет на величину производительного времени, качество и скорость обработки и утяжеления раствора. Недооценка значимости этого требования, негативно сказывается на сроках и качестве строительства скважины. Основные составные узлы ЦС:
• Блок очистки;
• Промежуточные и приемные емкости;
• Блоки приготовления и утяжеления буровых растворов и химреагентов;
• Желобная система;
• Насосный коллектор;
• Энергомодуль;
• Укрытие;
• Перемешиватели раствора (предпочтительны механические);
• Механизмы приготовления (гидромешалки, фрезерно струйные мельницы, гидроворонки – предпочтительны из-за высокой производительности);
• Доливная емкость;
• Ленточный транспортер;
• Шнековый транспортер;
• Кран-балка для перемещения контейнеров с сыпучими материалами.
Помещения циркуляционной системы оборудуются приточно-вытяжной вентиляцией. В районах Крайнего Севера, емкости для раствора оборудуются системой обогрева раствора. Автономность рабочих и запасных емкостей необходимо поддерживать профилактикой запорной арматуры, перемешивателей и чистотой емкостей, на запасных емкостях должна быть табличка с указанием типа раствора и его плотности, все емкости, кроме блока очистки должны быть снабжены мерными линейками, даже при наличие уровнемеров ГТИ. [90]
Из резервуаров подготовленный раствор направляется в подпорные насосы, которые впоследствии нагнетают его в буровые насосы (подпорные насосы можно заменить установкой подпорной емкости на высоте 1 м от уровня насосного коллектора, с закачкой в нее раствора центробежным насосом). В свою очередь буровые насосы направляют раствор (под высоким давлением) через нагнетательные линии, гибкий рукав и вертлюг, непосредственно в бурильную колонну. После этого буровой раствор, проходя через бурильную колонну, и забойному двигателю, проходит через долото. Раствор с высокой скоростью выходит из долота, тем самым очищая его и забой от выработанной породы. Оставшаяся часть энергии этого раствора уходит на подъем выбуренной породы, а также на преодоление сопротивлений, присутствующих в затрубном кольцевом пространстве. Отработанный раствор, который поднимается на поверхность, дегазируется, направляется в узел очистки, где из него удаляются частицы породы, песок, ил и прочие загрязнения. Затем предварительно очищенный раствор подается в подпорные насосы.
Системы для приготовления и очистки бурового раствора являют собой отдельные агрегаты, которые монтируются на желобной системе (над приемными резервуарами рабочих насосов). Нагнетательная линия включает в себя трубопроводы высокого давления, посредством которых раствор передается к стояку, а также к устью скважины. Линия оснащается специальной запорной арматурой, защитным клапаном и контрольно-измерительными приборами. Низконапорная часть циркуляционной установки оснащается устройствами, предназначенными для очистки раствора от выбуренной породы, газа, песка, а также смесительными устройствами, выполняющими функцию приготовления, утяжеления, восстановления и регулирования свойств рабочего раствора. Устройства соединяются с резервуарами посредством трубопроводов, оснащаются шиберными задвижками, а также перекачивающими и подпорными насосами. Циркуляционная система, с комплектом вышеперечисленного оборудования, может работать как со сбросом шлама в амбар, так и при без амбарной системе бурения.
В настоящее время самым эффективным устройством для приготовления и утяжеления раствора является гидроворонка (Рис 2.13).
Рис. 2.13. Гидроворонка
Работает посредством создания вакуума, при истечении жидкости через насадку (опыт Паскаля). Условия эффективности работы гидроворонки: длина насадки должна быть меньше, либо равна трем диметрам насадки (Lнас. 3dнас.) При создании давления на насадке 100–120 атм, воронка может засасывать сыпучие материалы через гофрированный шланг.
§ 7. Противовыбросовое оборудование
Противовыбросовое оборудование (ПВО) предназначено для герметизации устья скважины при строительстве скважин и капитальном ремонте для предупреждения, и ликвидации нефтегазопроявлений и открытых фонтанов. Монтируется на устье скважины на обсадную колонну, спущенную до ожидаемого вскрытия горизонта содержащего углеводороды.
В состав оборудования входит (Рис. 2.14, 2.15) [9]: стволовая часть (превентора с переходными катушками), манифольд, трубопроводы, пульт управления с импульсными трубками, гидроуправляемые элементы. ПВО может герметизировать устье скважины, как с бурильными трубами, так и при их отсутствии. Станция управления предназначена для дистанционного управления превенторами. Управление осуществляется, как с основного, так и со вспомогательного пультов. Аббревиатура ПВО: ОП5–230/80х35А
ОП – оборудование противовыбросовое; 230 – диаметр проходного отверстия, мм; 35 – рабочее давление, МПа;
Рис. 2. 14. Превенторная установка
Рис. 2.15. Принципиальная схема монтажа ПВО
Превентор плашечный рис. 2.16 является основным герметизирующим устройством, который устанавливается на устье скважины для предотвращения выбросов и воздействия на скважину при проявлениях, им можно герметизировать скважину как при наличие в ней бурильных труб, так и при отсутствии в ней бурильных труб, так и при их отсутствии. Крепление превентора осуществляется с помощью комплекта резьбовых шпилек к фланцу ниже смонтированного узла (крестовины, катушки или другого превентора). Уплотнение фланцев осуществляется с помощью специального уплотняющего стального кольца.
Рис. 2. 16. Устройство плашечного превентора
По количеству секций превенторы плашечные изготавливаются:
1. Односекционные;
2. Двухсекционные;
3. Трехсекционные.
С помощью плашечных превенторов выполняют следующие операции:
• Герметизацию устья при наличие и отсутствии бурильного инструмента в скважине;
• Срезание труб (при установке превентора со срезающими плашками, закрытием плашек были перерезаны бурильные трубы диаметром 12712 мм, предотвращен открытый нефтегазовый фонтан в скважине 108 Тенгиз, при подъеме бурильных труб);
• Проворачивании и расхаживании колонны труб на гладкой части трубы по длине от муфты до муфты (при контролируемом давлении в камере закрытия);
• Разгрузка колонны труб на плашки и удержанием колонны плашками от выброса (при возрастании давления в скважине);
• Спуск м подъем части колонны при загерметизированном устье скважины в случае установки двух плашечных превенторов (метод шлюзования);
• Восстановление циркуляции промывочной жидкости с противодавлением на пласт;
• Быстрое снижение давления в скважине;
• Закачку раствора обратной циркуляцией (через затрубное пространство);
Устройство плашечного превентора показано на рис. 2. 19.[9]
Для работы превентора существует три вида плашек:
1. Трубные – для герметизации скважины при наличие в ней колонны труб;
2. Срезные – для геметизации как при наличие труб, так и при их отсутствии;
3. Глухие – для герметизации скважины при отсутствии труб.
Открытие и закрытие плашек осуществляется посредством гидравлической жидкости подаваемой под давлением в полости цилиндров. Также предусмотрена возможность закрытия плашек вручную, с помощью специального штурвала.
Превентор универсальный гидравлический (ПУГ) Как следует из названия, является универсальным герметизирующим устройством. Устанавливается на устье скважины, как правило поверх плашечного превентора, к которому крепится посредством резьбовых шпилек. Запирание и отпирание скважины производится только при помощи гидравлики. Превентор универсальный гидравлический является дополнительным средством герметизации скважины рис. 2.17.
Рис. 2.17. Устройство универсального превентора
Как правило он рассчитан на половину давления, выдерживаемого плашечным превентором.
Преветор универсальный гидравлический используется для:
• Герметизации устья при наличии бурильного инструмента в скважине, на любой части бурильной колонны (гладкая часть, замковые соединения) УБТ, квадрат и др.), обсадных или насосно-компрессорных труб;
• Герметизации устья при отсутствии бурильного инструмента в скважине расхаживания инструмента;
• Протаскивания инструмента с замковыми соединениями (при наличии на них фасок под углом 18°) на небольшой скорости (при контролируемом давлении в камере закрытия);
• Быстрого снижения давления в скважине.
Причем не требует в отличие от плашечного, подбора плашек, а может герметизировать скважину с трубами различного размера в определенном диапазоне.
1-верхний фланец;
2-верхняя секция корпуса;
3-Уплотнительный элемент корпуса;
4-Переходное кольцо;
5-Поршень;
6-Нижняя секция корпуса;
7-Нижний фланец.
Принцип работы ПУГа в следующем. Через специальный канал к в нижней секции корпуса (на рисунке не показан) под поршень поступает гидравлическая жидкость под давлением, поршень двигается вверх и давит на резиновый элемент, резиновый элемент скользит направляющими полозьями (армированными стальными пластинами) по внутренней стенке верхней секции корпуса. Таким образом резиновый элемент сжимается в верхней части и герметизирует свою внутреннюю полость. [9]
В настоящее время для монтажа ПВО, согласно ГОСТ 13862 90, существует 10 схем. [71] Монтаж противовыбросового оборудования должен производится в соответствии со схемой обвязки устья скважины, которая определяется из геолого-технических условий; технической документацией (технический паспорт, технические условия или инструкция по эксплуатации); соответствующих правил; схем и ГОСТов при освоении, текущем и капитальном ремонте и в соответствии с положениями настоящей инструкции. Выбранная схема должна быть указана в плане работ на ремонт (освоение) скважины. В процессе работ допускается переход от одной схемы обвязки устья скважины противовыбросовым оборудованием к другой. Все изменения должны указываться в плане работ. К работе по монтажу и эксплуатации допускаются работники, прошедшие подготовку по курсу “Контроль скважины. Управление скважиной при ГНВП”.
Схема 2.1. и 2.2. – с механическим (ручным) приводом; – с гидравлическим приводом. В ОП для ремонта – привод механический или гидравлический, для бурения – гидравлический.
Рис. 2.18. Схема 1 согласно ГОСТ 13862 90
Рис. 2.19. Схема 2 согласно ГОСТ 13862 90
Рис. 2.20. Схема 3 согласно ГОСТ 13862 90
Рис. 2.21. Схема 4 согласно ГОСТ 13862 90
Рис. 2.22. Схема 5 согласно ГОСТ 13862 90
Рис. 2.23. Схема 6 согласно ГОСТ 13862 90
Рис. 2.24. Схема 7 согласно ГОСТ 13862 90
Рис. 2.24. Схема 8 согласно ГОСТ 13862 90
Рис. 2.25. Схема 9 согласно ГОСТ 13862 90
Рис. 2.26. Схема 2.1.0 согласно ГОСТ 13862 90
Схемы № 1. и № 2. используются, как правило, при ремонте скважин, так как имеют механический (ручной) привод плашечных превенторов и задвижек. Схемы № 3 и № 4 используются как при капитальном ремонте, так и при строительстве скважин и имеют дистанционное гидравлическое управление превенторами и устьевыми задвижками. Схемы с № 3 по № 10 имеют дистанционное гидравлическое управление превенторами и устьевыми задвижками. Используются, как правило, только при строительстве скважин. В случае отказа дистанционного гидравлического управления превентора и гидрозадвижки должны иметь ручное управление. Согласно требованиям Государственного общероссийского стандарта ГОСТ 13862–90 противовыбросовое оборудование имеет следующее условное обозначение: Оборудование ОП 3–230/8035 К2 ГОСТ 13862–90 расшифровывается следующим образом:
• ОП 3 – оборудование противовыбросовое по схеме № 3;
• 230 – условный проход превенторного блока, мм;
• 80 – условный проход манифольда, мм;
• 35 – рабочее давление, МПа (350 кгс/см2);
• К2 – для скважинной среды с содержанием СО2 и Н2 до 6 %.
• В зависимости от содержания углекислого газа (СО2) и сероводорода (Н2S) в эксплуатируемой среде (в промывочной жидкости) оборудование противовыбросовое выпускается в следующем коррозионностойком исполнении:
• К1 – для сред с объёмным содержанием СО2 до 6 %;
• К2 – для сред с объёмным содержанием СО2 и Н2S до 6 % каждого;
К3 – для сред с объёмным содержанием СО2 и Н2S до 25 %. [71]
§ 8. Талевые канаты
Важным элементом, существенно влияющим на безопасность работ, является талевая система, включающая в себя талевый канат. Поэтому особое внимание нужно уделять состоянию талевого каната, его эксплуатации. Стальные канаты отличаются друг от друга: используемыми марками стали и значениями временного сопротивления разрыву, видами покрытия, конструкциями, типом свивки проволок и прядей, рядом свивки прядей, видом свивки каната, направлением свивки. [33]
а) С одним органическим сердечником ЛК-О 6*19 = 114. ЛК-О тип свивки линейного касания с одинаковым типом проволок в каждом слое и отличными диаметрами проволок по слоям. 19-число проволок в пряди; 114 – общее число проволок в канате; 6-число прядей в канате.
б) С одним металлическим сердечником тросовой свивки ЛК-3 – 6*25 = 150; ЛК-3 – тип свивки (линейное касание с запоминающими проволоками). 6 – число прядей; 25 – число проволок в пряди. Сердечник 7*7 = 49 проволок.
ТК 18*19 = 342; ТК – тип свивки (точечное касание проволоки между слоями проволок в пряди). 18 – число прядей в канате; 19 – число проволок в пряди.
Талевые канаты должны поставляться (при весе более 700 кг) на деревянных или металлических барабанах. При весе 3000 кг деревянные барабаны должны иметь центральные металлические втулки. Диаметр бочки барабана должен быть не менее 15-ти кратного диаметра каната.
Каждый талевый канат должен сопровождаться сертификатом завода изготовителя.
При бурении на нефть и газ обычно нагрузка на канат делается с четырехкратным запасом прочности. Новые канаты, с целью увеличения сроков службы необходимо эксплуатировать с нагрузкой меньше максимально допустимой. После обтяжки, можно доводить нагрузку до максимальной.
Основные принципы, которыми нужно руководствоваться при выборе и эксплуатации талевого каната:
1. Диаметр каната и число струн, в оснастке выбирают с учетом максимально возможной рабочей нагрузки таким образом, чтобы обеспечить запас прочности не менее 4-х;
2. Число струи в оснастке определяют величинами расчетной нагрузки и необходимой скорости подъема инструмента;
3. Сорт стали для канатов выбирают с учетом обеспечения гибкости, износоустойчивости и наименьшей стоимости;