Строительство нефтяных и газовых скважин Новиков А.
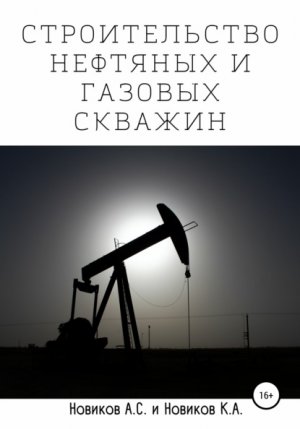
Рис. 5.19. Керноотборочный снаряд
Таблица 14. Типоразмеры устройств для отбора керна Российских производителей [7]
Современные керноприемные устройства выпускаются трех типов:
• Для отбора керна из массива плотных пород;
• Для отбора керна в трещиноватых, перемятых породах;
• Для отбора керна в сыпучих породах.
Керноприемное устройство первого типа – снаряд «Недра», где грунтоноска вращается с корпусом, жидкость отводится от керноприемника при помощи шара (КД11М190/80).
Керноприемное устройство второго типа имеет вращающуюся независимо от корпуса грунтоноску (СК164/80).
Керноприемное устройство третьего типа – обеспечивает герметизацию керна за счет эластичного керноприемника.
В основном используется снаряд «Недра» и «Кембрий», он может быть собран из нескольких секций по 7 метров. Модификация «Недра» СКУ122/52, СКУ138/67, СКУ203/100.
Керноприемные устройства для турбинного бурения выпускают в четырех моделях: КТДЗ-240; КТДЧС-240; КТДЧС-195 и КТДЧС-172. КТД – колонковое турбинное долото. При турбинном бурении формирование и хранение керна затруднено, его диаметр мал, процент выноса низок, поэтому при отборе керна обычно переходят на роторный способ. [9]
За рубежом широко применяют эффективные устройства фирм «Нортон кристенсен», «ДБС», «Диамнт Борт». Например, в мировой практике широко известно керноотборное устройство с несъемным керноприемником серии 250П (рисунок 5.20), с помощью которого успешно отбирали керн на ряде нефтяных месторождений в России. Устройство состоит из предохранительного переводника 1 с крупной ленточной резьбой 2 для отсоединения в случае прихвата корпуса 6. Керноприемник 8, имеющий шариковый обратный клапан 5, подвешен на шаровой опоре 3. Корпус имеет два стабилизатора 4 и 7. Нижняя часть имеет кернорватель 9. Разрушение породы производится бурильной головкой 10. Как видно из рисунка 62 керноотборное устройство 250П близко по конструкции к устройству серии «Недра». Сообщается, что после некоторой модернизации с помощью 250П возможен отбор иентированного керна. Фирма «Нортон Кристенсен» выпускает также керноотборное устройство серии 300 со съемным керноприемником (рисунок 5.21). Устройство включает грибообразную головку 1 для захвата и подъема керноприемника 5. Керноприемник подвешен в корпусе 4 на шаровой подвеске 2. Верхняя часть керноотборника снабжена дренажным шаровым клапаном 3. В устройстве имеется так же кернорватель 6 и бурильная головка 7. Фирмой ДБС, разработано керноотборное устройство для отбора керна из высокопористых нефтенасыщенных пород (рисунок 64). Специалисты фирмы считают, что без изоляции керна, при доступе к нему бурового раствора на водной основе, а также при извлечении керна из керноприемной трубы, в воздух испаряется до 50 % нефти, содержащийся в порах керна. А это приводит к тому, что в геологических материалах появляется неверная информация о продуктивности изучаемого нефтеносного пласта. Во время рейса с отбором керна происходит отток из керна нефти и воды в губчатый пористый материал 10, находящийся в алюминиевой втулке 9. При подъеме керноотборного устройства, с забоя до устья, происходит падение давления от пластового до атмосферного, при этом газ, находящийся в образце породы, увеличивается в объеме, стремясь вытолкнуть нефть и воду в губчатый материал. [26]
Рис. 5.20. Керноотборное устройство с несменным керноприемником серии 250П
Рис. 5.21. Керноотборное устройство серии 300 со съемным керноприемником
Колонковый снаряд наклонно-направленных скважин используются для отбора керна в наклонных скважинах (угол наклона более 45 градусов). Он отличается от стандартного снаряда конструкцией. Опора керноприемника может удерживать его в нормальном рабочем состоянии при больших углах.
Керноприемник центрируется в корпусе и не вращаться вместе с корпусом.
Колонковый снаряд с наружным выпускным каналом отличается от стандартного снаряда тем, что специальное соединение выпускного канала устанавливается между разъединительным переходником и вертлюгом.
При колонковом бурении внешний выпускной канал позволяет выпускать буровой раствор из керноприемника в кольцевое пространство, тем самым уменьшая сопротивление вхождению керна в керноприемник.
Это позволяет увеличивать вынос керна. Данный колонковый снаряд может использоваться при отборе керна в мягких и разрушенных пластах или при высоком давлении бурового раствора. Герметизированный колонковый снаряд BQX 180101 специально разработан для отбора керна в мягких или рыхлых пластах для увеличения выноса керна. Данная новая конструкция имеет уникальное отличие – она оснащена системой управления подъемом для поднятия керноприемника. Рис. 5.22
Рис. 5.22. Керноотборное устройство для отбора керна из высокопористых нефтенасыщенных пород
После завершения отбора кернорватель выводится наверх и отрывает керн, а затем закрывает нижнюю часть керноприемника. Во время колонкового бурения кернорватель укрывается за внешней стенкой керноприемника, что способствует беспрепятственному входу керна в керноотборник.
После завершения отбора керна кернорватель выходит наверх для плотного закрытия керноприемника для избежания потерь керна при подъеме.
Керноприемным или колонковым инструментом принято называть инструмент, обеспечивающий прием, отрыв от массива горной породы и сохранение керна в процессе бурения, во время транспортирования по скважине, вплоть до его извлечения на поверхность для исследования. От конструкции керноприемных устройств, качества их изготовления, сборки и правильной эксплуатации зависят результаты работ по отбору и исследованию керна и эффективность бурения скважины, особенно разведочной. [26]
Во избежание получения искаженных или вовсе неверных геологических, химических и иных данных о буримых породах необходимо нередко применять такие керноприемные устройства, которые обеспечивают не только высокий процент выноса керна, но и не нарушенную структуру породы, защищают керн от промывочной жидкости, производят на него минимальное разрушающее действие.
§ 25. Долота для специальных целей
К специальным долотам можно отнести: фрезерные, зарезные, пилотные, вставные, эксцентричные, торцовые, пикообразные. [9]
Фрезерные долота – очень просты в изготовлении, надежны в работе, используются как для бурения скважины, так и для разбуривания металла на забое. Недостатки: низкая механическая скорость проходки, неэффективны в крепких породах, глинах, большой крутящий момент.
Зарезные долота – внешне похожи на торцевые долота, рабочая часть долота (торец) имеет выгнутую форму с невысокой цилиндрической частью, имеющую форму козырька, армируется материалом "Славутич".
Вставные долота – применяются при бурении вставными турбобурами без подъема бурильной колонны. Это двухшарошечные долота с раздельными лапами. В транспортном положении одна шарошка располагается над другой. Верхняя лапа неподвижно закреплена, нижняя лапа закреплена шарнирно на системе подвижных деталей. Под давлением жидкости поршень поднимает вверх нижнюю лапу. Лапы запираются в коническом раструбе. Осевая нагрузка передается через конический раструб, а вращающий момент, через поверхности фигурного паза неподвижных деталей в месте шарнирного соединения с верхней лапой. Смена долота производится тартальным канатом при помощи овершота и обратной промывки, совместно с ротором турбины.
Пикообразные долота – изготавливают двух типов: Ц – для разбуривания цементных пробок; Р – для расширения ствола скважины. Предусмотрено выпускать от 94,4 мм до469,9 мм.
Пилотные долота, расширители – производят разрушение горного массива уже ослабленного бурением расширяемой скважины. В этом массиве уже развиты зоны разрушения, трещины, вскрыты поверхности, а так же при бурении скважин большого диаметра и при неэффективном разрушении пород долотами большого диаметра.
Расширители можно классифицировать по виду, форме рабочих органов, по способу крепления рабочих органов, типу этих органов. Применяют два типа расширителей: шарошечные и лопастные. Шарошек может быть одна и более, могут быть одноярусные и многоярусные. Всего выпускается семь размеров от 243 до 1350 мм.
Глава 6. Режим бурения скважины
Выбор способа бурения зависит от ряда факторов: организационных, технико-экономических.
Организационные – это отдаленность района работ от баз производственного обеспечения, наличия запчастей и ремонтного оборудования, квалификации персонала баз производственного обеспечения.
Технико-экономические – это величина рейсовой скорости проходки, геологические условия проводки скважины, себестоимость одного метра проходки. В тех случаях, когда, за счет увеличения механической скорости проходки, сокращается время строительства скважины, несмотря на более высокую себестоимость 1 м проходки при использовании ВЗД, сокращение срока ввода скважины в эксплуатацию, является определяющим.
§ 26. Выбор режим бурения скважины, факторы режима бурения
Процесс бурения скважины, включает одновременно приложение ряда отдельных факторов для преодоления сопротивления пород их разбуриванию. Получение эффективной максимальной скорости проходки, возможно, когда каждый отдельный фактор имеет свое оптимальное значение, уравновешенное относительно других факторов, составляющих процесс бурения и обусловленное характером разбуриваемых пород и сопротивлением, которое они представляют долоту. Проектные режимы бурения не учитывают всех факторов, поэтому каждому пропластку режим бурения подбирается индивидуально, причем важным фактором является непрерывность подачи долота с подобранным режимом (в основном нагрузка на долото). Коммерческая скорость бурения линейно зависит от механической скорости проходки (при мех скорости более 1 м/час) Рис. 62. [55]
Рис. 6.1. Изменение коммерческой скорости бурения от изменения механической скорости проходки и статей баланса календарного времени
Так как характеристики горных пород, определяющие их сопротивление разбуриванию или влияющие на него, изменяются в широких пределах, то эти факторы также должны изменяться в достаточно широких пределах, чтобы при подборе режима бурения можно было удовлетворить требования, возникающие при экстремальных значениях характеристик горных пород. Необходимыми условиями являются также: высокая квалификация и опыт бурильщиков, которые должны быстро изменять эти факторы, посредством имеющегося оборудования и КИП. Способность быстро распознавать необходимость таких изменений является критерием квалификации бурильщика и инженера по бурению. Правильность выбранного решения гарантирует уменьшения рисков аварий с долотом.
Факторами режима бурения являются тип и размер долота, осевая нагрузка на долото, скорость его вращения, количество и качество закачиваемого в скважину промывочного раствора. В дальнейшем будем считать, что квалификация персонала достаточная. [54]
Оборудование и инструмент. Все наземное оборудование и инструмент должны быть подобраны с таким расчетом, чтобы каждый фактор режима бурения, возможно, было изменять в таком диапазоне значений, который определяется изменением свойств бурильных пород. Чтобы различные факторы режима бурения можно было применять в разных комбинациях и изменять их в требуемых диапазонах значений, на скважине должна быть установлена уравновешенная буровая установка достаточной мощности. Для увеличения производительного времени бурения оборудование должно быть хорошего качества. Органы управления должны обеспечивать регулирование режима бурения с минимальной затратой времени.
Долота.
Глины, вязкие сланцы, рыхлые песчаники, мел, соль, ангидриты, сланцы, эффективно разбуриваются долотами PDC и диапазон применения долот PDC быстро расширяется. Крепкие и абразивные породы с большей эффективностью разбуривают долотами шарошечного типа и алмазными. За редким исключением длина зубьев шарошечных долот обратно пропорциональна твердости пород, а число зубьев прямо пропорциональна твердости пород. В долотах всех типов имеет большое значение конструкция насадок в промывочных отверстиях, очень важна центрация долота относительно оси скважины, это снижает радиальные биения долота.
Осевая нагрузка на долото.
Осевая нагрузка на долото должна обеспечивать эффективное внедрение последнего в разбуриваемую породу. Практически во всех случаях величина осевой нагрузки пропорциональна или почти пропорциональна твердости или прочности на сжатие горной породы. При бурении лопастными долотами мягких пород осевая нагрузка снижается до минимальной величины. При бурении крепких пород шарошечными долотами осевая нагрузка увеличивается до максимально допустимой величины. При бурении долотами ИСМ, PDC и алмазными, осевая нагрузка на долота минимальная. Но нагрузка не должна превышать 75 % веса тяжелого низа в КНБК.
На практике в Западной Сибири принято иметь в компоновке низа бурильной колонны 12 м УБТ, нагрузка на долото создается весом бурильного инструмента.
На рис. 6.2 показана зависимость механической скорости проходки от длины УБТ, увеличение длины УБТ до 50 м, привело к увеличению механической скорости проходки на 23 %.
Рис. 6.2. Зависимость механической скорости проходки от длины УБТ
Влияние на механическую скорость проходки, увеличение длины УБТ свыше 50 м, не исследовано [55]. При бурении горизонтальных скважин нагрузка на долото создается весом бурильных труб, находящимися над двигателем, УБТ, если включают в КНБК, то размещают в вертикальной части ствола. Возникающие при этом проблемы:
• Баклинг эффект;
• Не доведение нагрузки на долото.
Эти проблемы решаются различными технологическими приемами.
Все прочие факторы режима бурения должны быть приложены в их максимальных значениях во взаимосвязи с типом и размером долота, и другими факторами, в соответствии со свойствами разбуриваемых пород.
Скорость вращения. При бурении в мягких глинах и песках скорость вращения не имеет первостепенного значения и вполне удовлетворительно применяют обороты ротора 100–150 об/мин. При бурении шарошечными долотами наиболее эффективна скорость вращения, обратно пропорциональная твердости пород. Но часто, увеличение скорости вращения и нагрузки на долото не дают увеличения скорости проходки из-за сильной осевой вибрации инструмента (на забое образуется рейка), что приводит к ускорению износа долота, преждевременную усталость металла и разрушение бурильного инструмента. Таким образом, минимальная осевая нагрузка на долото будет соответствовать максимальному числу оборотов и наоборот. Вышеизложенные положения справедливы для роторного способа бурения. При бурении забойным двигателем, число оборотов долота для данного двигателя, величина постоянная, можно варьировать только нагрузкой на долото, и оптимальная нагрузка выбирается по максимальной скорости углубления скважины.
Промывка скважины. В мягких породах основным условием получения максимальной механической скорости является подача промывочной жидкости с хорошей очисткой забоя и обеспечением высокой скорости восходящего потока в кольцевом пространстве, в то время как при бурении в крепких породах, можно предусмотреть подачу в меньших количествах. Это относится к роторному способу бурения. При бурении забойным двигателем, для устойчивой работы машинного агрегата необходима регламентированная подача.
§ 27. Общие параметры режима бурения в различных породах
Пласты, содержащие один литологический тип в природе встречаются очень редко. Глины могут включать в себя, пески, песчаники, аргиллиты, алевролиты и т. д. Тем не менее, правильный подбор долота и режимов бурения, с учетом преобладающей литологии. Позволит повысить эффективность работ. Рассмотрим некоторые встречающиеся при бурении скважин случаи. [54]
Глины:
a) Увеличение скорости вращения обычно сопровождаются увеличением скорости проходки (как правило, этот параметр влияет на скорость проходки в большей степени, чем нагрузка на долото);
b) Риск повреждения долота в этом случае минимален;
c) Подача насосов – проектная;
d) Значительный риск образования сальника на долоте и элементах КНБК, при отсутствии в растворе ингибитора глин и повышенной вязкости раствора.
Твердый чистый мел/известняк:
a) Максимальная скорость проходки достигается путем увеличения нагрузки на долото, вооружение раздавливает породу, скорость вращения должна быть максимально низкой (подбирается исходя из максимально достигнутой механической скорости проходки);
b) Подача насосов – проектная;
c) Элементы долота могут быть повреждены, при отсутствии в пласте песчаников абразивного износа долота не будет).
Твердые песчаники:
a) Максимальная скорость проходки достигается путем увеличения нагрузки на долото, вооружение раздавливает породу, скорость вращения должна быть максимально низкой (подбирается исходя из максимально достигнутой механической скорости проходки);
b) Элементы долота могут быть повреждены, абразивный износ долота будет значительный и чем выше скорость вращения тем больший износ долота по диаметру;
c) Подача насосов – проектная;
d) Низкая скорость вращения значительно снижает механическую скорость проходки, поэтому необходимо подобрать оптимальное сочетание параметров. Предпочтительно использовать алмазные долота в сочетании с турбобуром.
Известняки, доломиты:
a) Более восприимчивы к нагрузке на долото, чем обороты долота: Вероятность вертикальной вибраций велика, уход от вибраций изменение оборотов долота, снижение нагрузки приводит к резкому снижению механической скорости проходки;
b) Кремнистые включения, часто встречающиеся в известняках и доломитах, могут двигаться под долотом. Это может перегрузить элементы режущей структуры долота, приводя к скалыванию и слому вооружения;
c) Нельзя использовать чрезмерно высокие значения нагрузки и оборотов долота.
Пириты:
a) Пирит чрезвычайно абразивный и твердый минерал, в плане разрушения более предпочтительна высокая нагрузка и наименьшее число оборотов долота.
b) Кусочки пирита могут двигаться под долотом по забою. Это может перегрузить элементы режущей структуры долота, приводя к скалыванию и слому вооружения
c) Нельзя использовать чрезмерно высокие значения нагрузки и оборотов долота;
d) При потере диаметра долота, может скачкообразно увеличиваться момент на долоте, это причина подъема долота.
Перемежающиеся породы:
a) Наиболее встречающаяся ситуация при бурении скважин на нефть и газ, переслаивание глин, аргиллитов, мергелей, песчаников и т. д. Наиболее эффективны долота с твердосплавным вооружением, или долота PDC, адаптированные для пород средней твердости, при отсутствии или незначительном включении абразивных пород.
b) Режим бурения подбирается по максимально достигнутой механической скорости проходки.
c) Возможны все виды осложнений: сальникообразование, осыпи и обвалы пород, поглощения, прихваты, вибрации. [54]
§ 28. Практические приемы работы с долотами
Из всех существующих технологический операций, отработка долота, являясь приоритетным в технологии строительства скважин, выполняется силами буровой бригады/вахты. Поэтому для получения максимального эффекта отработки долот, необходимо глубокое понимание процесса и требований к этому процессу, как у инженера, так и у персонала буровой бригады. На практике, для рациональной отработки долота, получения максимальной эффективности его работы, существует большое количество приемов и условий, обязательных к выполнению. [54]
1. Изучение буровой площадки, проверка подготовленности персонала буровой бригады/вахты.
Это включает в себя:
• Оценка буровой установки и установленного оборудования;
• Квалификация персонала (определяется тестированием, проверкой документов).
2. Проверка состояния оборудования и факторов, влияющих на показатели работы долота:
a) Вибросита (тип, количество, размер ячеек);
b) Песко-илоотделители, центрифуги (тип, количество);
Неэффективная очистка может снизить механическую скорость проходки, за счет повышения содержания твердой фазы в растворе, привести к осложнениям (сальникообразование, прихваты инструмента, поглощения раствора);
c) Буровые насосы;
d) Циркуляционная система;
e) Наличие, правильность размещения и исправность датчиков ГТИ;
f) Тип, состояние и параметры бурового раствора, тип и количество ингибитора раствора;
g) Гидравлическая программа (реологические константы раствора, максимальные давления, подача раствора, тип, параметры и режим прокачки вязкоупругих пачек, для очистки ствола и для кольматации с добавкой наполнителя зон поглощения, наполнитель не должен забивать насадки долота, т. е. иметь меньший размер диаметра насадки);
Гидравлическая программа должна обеспечивать максимальную степень очистки забоя, вынос выбуренной породы с забоя, качество очистки достигается, при оптимальной гидравлической программе, различными технологическими приемами, конструктивными особенностями долота и режимом течения раствора.
h) Профиль скважины (при бурении горизонтального участка ствола, требования к КНБК, отличны от КНБК для вертикальной и наклонно-направленной скважины);
i) Привод долота (ротор, верхний силовой привод, ВЗД, роторная управляемая компоновка);
j) Показатели работы долота существенно зависят от вида привода долота. ВЗД имеет преимущество перед роторным способом бурения более высоким числом оборотов, но имеет свои ограничения, например при прохождении зон поглощения и небольшим ресурсом, по сравнению с роторным способом. Комбинация бурения управляемой роторной компоновкой и ВЗД значительно увеличивает механическую скорость проходки. Роторная управляемая система может обеспечить более точный контроль при наклонно-направленном и горизонтальном бурении по сравнению с забойным двигателем. Бурение горизонтальной скважины очень проблематично а при длине горизонтального ствола более 400 м и невозможно без применения верхнего силового привода. Вынос шлама и образование «дюн» зависят так же и от вращения бурильной колонны. Доведение нагрузки на долото в горизонтальной скважине, без вращения бурильных труб или применения спец оборудования (трактор) невозможно;
k) Наличие в КНБК калибраторов, центраторов, стабилизаторов их линейные размеры, расположение лопастей, влияют на качество бурения ствола скважины. При подготовке ствола скважины к спуску колонны, особенно большого диаметра, калибратор с прямыми лопастями обеспечивает цилиндрический ствол скважины в отличие от спирального калибратора, который благодаря своей спиральной форме, вписывается в пробуренный ствол, не всегда калибруя его;
l) Каротаж в процессе бурения (MWD/LWD), получение прямых данных о давлении пласта, литологии, вибрации в скважине, доведенной нагрузке на долото, позволяет правильно оценить правильность решений и действий по скважине.
m) Реализация гидравлической мощности на долоте, важный фактор высокой механической скорости проходки, обеспечивается правильным подбором насадок, расходом промывочной жидкости;
n) Подготовка долота к спуску, установка насадок, присоединение долота к бурильной колонне, спуск долота в скважину, должны выполняться строго по регламентам и инструкциям.
Для разных типов долот и привода долота существует разные методики разбуривания. Оснастку низа обсадной колонны можно разбуривать долотами с алмазосодержащим вооружением (долота PDC, импрегнированные, алмазные) в случае если, разбуриваемая оснастка состоит из пластмассовых, цементных и резиновых элементов. Латунные и алюминиевые элементы могут повредить долото, забить промывочные каналы, или поднимая куски алюминия в кольцевое пространство, заклинивая бурильную колонну. При цементирования, для предотвращения проворачивания продавочной пробки, необходимо на пробку закачать цемент, достигается стравливанием давления «СТОП» на 10–12 атм.
3.1. Процедура разбуривания оснастки:
a) Отбить забой с нагрузкой 1,5–2 т. Определить наличие не затвердевшего цемента;
b) С минимальной нагрузкой и 20–40 об/рот и максимальной подаче, начать разбуривание;
c) Через каждые 3–6 см проходки расхаживать инструмент на величину 1–1,5 м;
d) Если углубления нет повторить расхаживание на величину 1–1,5 м с промывкой;
e) Внимательно следить за давлением насосов, для контроля закупорки промывочных каналов;
f) При появлении вибраций изменить обороты ротора;
g) Не использовать автоматическую подачу долота;
h) Прикладывать минимальную нагрузку, следить за механической скоростью проходки, увеличивая нагрузку на долото до 3–4 т., не забывая о периодическом расхаживании инструмента;
i) Если в оснастке присутствует алюминий и появились заклинки при разбуривании, остановить циркуляцию для падения элементов на збойц и пытаться раздавить алюминиевые элементы долотом. [54]
При начале работы с новым долотом, очень важно правильно сформировать профиль забоя в соответствии с геометрией долота. От правильности выполнения формирования забоя, зависит работоспособность долота. Если новое долото значительно отличается от предыдущего геометрией, подход к забою необходимо производить с минимальной подачей насосов.
a) При вращении 40–60 об/мин нагрузить долото 1,5–2 т., начать углубление, для внедрения
вооружения в породу, подача раствора должна быть проектной;
b) Если нет углубления, увеличить нагрузку и пробурить на высоту долота с минимальной нагрузкой, при этом контактировать с породой будут только некоторые элементы вооружения, при большой нагрузке они могут разрушиться;
c) Постепенно увеличить нагрузку на долото до проектной;
d) Увеличить обороты ротора проектных значений, корректировать нагрузку по максимуму механической скорости проходки, при этом подача долота должна быть максимально непрерывной;
e) Избегать вибраций, при появлении вибраций, изменить обороты ротора, снижение нагрузки существенно снижает механическую скорость проходки;
f) При равенстве забойного и порового давления, механическая скорость проходки снижается и при уменьшении порового давления, и может снизиться до очень малых величин. [54]
Методика заключается в приложении нагрузки на долото при трех разных оборотах долота с блокировкой тормоза, после чего бурение осуществляется без подачи инструмента.
1. Выбрать три скорости вращения ротора например: 80, 120 и160 об/мин;
2. Установить минимальную скорость вращения и создать максимально разрешенную нагрузку на долото;
3. Затормозить лебедку и провести бурение без подачи инструмента;
4. Записать нагрузки с шагом 1 т. в порядке уменьшения до снижения механической скорости до минимальных значений, зафиксировать время в секундах, затраченное на бурение интервала нагрузок;
5. Произвести пробное бурение с 120 и 160 об/мин, в той же последовательности;
6. Проанализировать время, затраченное на бурении при трех значениях оборотах ротора. Наименьшее затраченное время в секундах, на бурение в диапазоне равных нагрузок, будет соответствовать максимальной скорости проходки. Но это не догма, всегда искать максимум механической скорости проходки и избегать вибраций. [54]
Глава 7. Забойные двигатели
§ 29. Общие сведения о забойных гидравлических двигателях
Турбобуры – это забойные гидравлические двигатели, предназначенные для бурения скважин в различных геологических условиях. Спускаются к забою на бурильных трубах. Энергия, необходимая для работы турбобура, доставляется потоком жидкости, подаваемой по трубам, установленными на поверхности насосами. Жидкость, отработанная в турбине подается в долото и, проходя через отверстия в долоте, попадает на забой, очищает его, вынося разбуренную породу на поверхность. Турбобур состоит из стопора с дисками и ротора с дисками. Лопатки ротора и статора имеет противоположные направления наклона, левое и правое. Схематически на Рис. 64 Изображены внешний вид турбобура и пары ротор-статор. [9]
Рис 7.1. Турбобур
Мощность на валу турбобура определяется
N = (QH/75) * (6.1)
Где: – Q – подача жидкости, л/с;
Н – перепад давления на турбобуре, кг/см2
– плотность жидкости, г/см3
– КПД турбобура.
Турбобуры выпускаются различных типов. Односекционные, двух и трех секционные, быстроходные, тихоходные. Отличительная особенность – большо число оборотов вала турбобура (500–1200 об/мин.), что не всегда отвечает требованиям режима бурения.
В НПО «Буровая техника» – ВНИИБТ созданы турбобуры нового поколения типа Т1, которые имеют улучшенную энергетическую характеристику и обладают высокой надежностью. Так, например, как видно из приведенных данных, в новом турбобуре Т1–195 достигнуто повышение момента силы его турбины на 37 % при снижении частоты вращения на 15 %. Помимо улучшения показателей работы долот, применение турбобура Т1–195 показало исключительно высокую его надежность. Две шпиндельные секции нового турбобура наработали в среднем по 350 часов, что в 3 раза больше, чем на серийных шпиндельных секциях. Наработка на турбинные секции превысила 1000 часов, что примерно в 2,5 раза больше, чем на серийных аналогах. Высокие результаты были достигнуты за счет усовершенствований конструкции турбины, осевой и радиальных опор, использования улучшенных материалов. [9]
Требования к эксплуатации турбобуров заключается в следующем:
1 – рекомендуется применять долота диаметром, соответствующим диаметру и мощности турбобура. Бурильные трубы необходимо применять с минимальными гидравлическими сопротивлениями. Насосы должны быть способны работать при давлении не ниже 150 кгс/см, для обеспечения работы турбобура. Давление в циркуляционной системе складывается из:
Рн = Рм + Рст + РТР + РД + Ртб + Ркп (6.2)
Где: Рн – давление на насосе, кгс/см2
• Рм – давление в манифольде, кгс/см2
• Рст – давление на стояке, кгс/см2
• РТР – давление в бурильных трубах, кгс/см2
• РД – давление на долоте, кгс/см2
• Ртб – давление в турбобуре, кгс/см2
• Ркп – давление в кольцевом пространстве, кгс/см2
Расчеты потерь в циркуляционной системе довольно неточны, а с учетом того, что буровой раствор принадлежит к неньютоновским жидкостям, задача усложняется. Существуют готовые таблицы значений гидравлических потерь в элементах циркуляционной системы. На практике, оперативный расчет давления на насосе можно произвести по эмпирической формуле:
Рн = 0,015L + 15 (7.3)
Где: L – глубина спуска инструмента без долота и турбобура, в м. Перепад давления на турбобуре, долоте – величины справочные.
Для улучшения работы буровых насосов и увеличения коэффициента наполнения насосов, последние должны устанавливаться под залив. Буровая должна быть оснащена средствами очистки бурового раствора, под квадратом установлен фильтр, при бурении с аэрацией над турбобуром устанавливается обратный клапан; эти меры нужны, чтобы не допустить шламования турбобура. При эксплуатации турбобура необходимо контролировать люфт вала шпинделя при каждой смене долота. Менять шпиндель при – Кш = 2 мм. Контроль износа секции турбобура заключается в замере люфта вала турбинной секции. При новом шпинделе люфт вала турбобура должен быть до 10±1 мм.
Винтовые двигатели – это обращенный насос Муано Рис. 66, который работает в режиме двигателя. В обрезиненном статоре вращается вал, который имеет эксцентриситет относительно статора. Состоит из неподвижного статора и планетарно движущийся ротор. Для передачи нагрузки на долото и вращающего момента секция соединена со шпинделем. Ротор изготавливается из нержавеющей или легированной стали с износостойким покрытием, внутренняя обкладка статора покрыта резиной. Направление винтовой поверхности – левое, что обеспечивает заворот реактивным моментом корпусных резьб ВЗД и бурильных труб. [15]
При циркуляции жидкости, в результате действия перепада давления на роторе двигателя вырабатывается крутящий момент, причем винтовые поверхности взаимно замыкаясь, разобщают область высокого давления и область низкого давления. Для создания в двигателе полостей, теоретически разобщенных от областей низкого и высокого давлений (шлюзов) необходимо и достаточно выполнение четырех условий:
1. Число зубьев Z1 наружного элемента (статора) должно быть на единицу больше числа зубьев Z2 внутреннего элемента (ротора): Z1 = Z2 + 1;
2. Отношение шагов винтовых поверхностей наружного элемента (статора) и внутреннего элемента (ротора) должно быть пропорционально отношению числа зубьев: Т/t = Z1/Z2;
3. Рабочая длина двигателя должна быть не менее шага винтовой поверхности наружного элемента: LT;
4. Профили зубьев наружного и внутреннего элементов должны быть взаимно огибаемыми и находится в непрерывном контакте между собой в любой фазе зацепления.
Число оборотов составляет 100–300 об/мин, и чем больше заходность двигателя, тем выше развиваемый момент на валу: типы ВЗД зарубежных производителей приведены в таблицах
Конструктивная особенность ВЗД позволяет уменьшать длину и диаметр двигателя, не снижая мощности, что особенно актуально при бурении горизонтальных стволов скважин.
Различают четыре режима работы ВЗД:
1. холостой;
2. оптимальный (наиболее высокого КПД);
3. экстремальный (максимальной мощности);
4. тормозной (число оборотов = 0).
Рис. 7.2. Зависимость момента и частоты вращения вала ВЗД от кинематического соотношения рабочих элементов (D,Q,P-const)
Наиболее уязвимым узлом двигателя является соединение ротора двигателя с шпиндельной секцией. Механизм, соединяющий планетарно движущийся ротор с концентрично вращающимся валом, работает в тяжелых условиях. Помимо передачи крутящего момента и осевой нагрузки, этот узел должен воспринимать сложную систему сил в агрегате, характеризующейся непостоянной ориентацией ротора. Существует несколько решений:
1. Шарнирные соединения;
2. Торсион (Гибкий вал).
Торсион (гибкий вал) не нашел применения из-за их ненадежности при перекосе секций более 1030 '. [15]
Винтовой забойный двигатель представляет собой симметричный роторный агрегат с применением зубчатого косого зацепления, приводимый в действие за счёт давления подаваемой жидкости (Рис 66).
Конструктивно состоит из:
• Двигательного узла.
• Рабочей части.
Двигательная секция ВЗД – основной силовой компонент двигателя и поэтому определяет его основные технические характеристики, такие как мощность, крутящий момент, КПД и частота вращения ротора.
Ротор имеет конструкцию похожую на сверло, но с высокопрочным износостойким покрытием, так как предназначен для передачи крутящего момента. Его изготавливают из высокопрочной легированной стали.
Количество зубьев у него меньше на одну единицу, чем у статора. Двигательный узел выполняют с определённым натяжением зубчатого зацепления, который зависит от параметров рабочей жидкости, свойств эластомера, температуры эксплуатации, а также других характеристик. От того, насколько точно они будут подобраны зависит прочность двигателя в целом и его ресурс работы.
На ресурс работы рабочей пары влияют следующие факторы:
• Присутствие в рабочей жидкости абразивных твёрдых частиц и дополнительных примесей.
• Использование в составе жидкости веществ, которые разъедают эластомер или изменяют его механические свойства. К ним относятся: соли, жидкость с высоким содержанием нефтепродуктов, хлориды, кислоты и соли.
• Превышение допустимых норм по температурным условиям в точке забоя, которые могут влиять на эластомер.
• Недостаточный прогрев рабочей пары при старте двигателя.
• Использование неправильного натяжения статор-ротор.
Винтовой забойный двигатель состоит из следующих рабочих органов:
• шпиндельного узла;
• регулятора угла.
Рис. 7.3. Винтовой забойный двигатель
Где: 1 – осевой подшипник; 2 – радиальная опора; 3 – центратор; 4 – противоаварийный бурт
Шпиндельный узел является вторым по важности конструктивным элементом двигателя. Он предназначен для передачи крутящего момента от рабочей пары рабочему инструменту для разрушения плотных пород грунта. При этом он способен выносить значительные осевые нагрузки, вызванные не только необходимостью передачи крутящего момента, а и силу трения о стенки креплений при угловом или горизонтальном бурении.
Шпиндельный узел представляет собой корпус с двумя опорами (радиальной и осевой), на которых закреплён вал. Вращение ротора передаёт крутящий момент посредством торсиона или карданного вала на вал шпиндельного узла, который начинает вращаться и передавать момент уже рабочей части.
Данный узел может быть выполнен в двух конструктивных исполнениях:
Открытом, когда рабочие узлы смазываются рабочей жидкостью.