Гравировальные работы. Техники, приемы, изделия Подольский Юрий
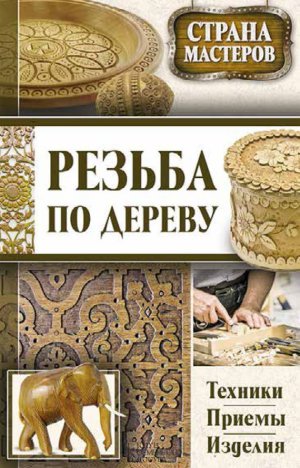
Некоторую особенность имеет прием ручного гравирования при снятии большого количества металла и последующем оконтуривании выступающих над общим фоном пуансона (клейма) рабочих частей букв, знаков и т. д. Для этого кистью правой руки с зажатым в ней инструментом совершают частые пружинящие движения с проталкиванием штихеля вперед. Большой палец должен упираться в край заготовки и несколько ниже гравируемой площадки так, чтобы нижняя грань полотна штихеля могла беспрепятственно скользить по его подушке на том уровне, который удобен для выполнения гравирования. С целью предупреждения срывов и соблюдения точности выполнения гравирования относительно линий разметки в процессе удаления лишнего металла штихель проталкивают вперед небольшими участками.
Острый штихель легко режет металл на глубину 0,1–0,2 мм при нормальном режиме работы. Во время работы следует постоянно следить за состоянием режущей кромки острия штихеля.
При доводке затупившихся рабочих поверхностей штихеля оселок смачивают керосином.
Сечку, слегка наклоненную хвостовиком вниз, удерживают и направляют пальцами левой руки (рис. 28, а), а правой с помощью граверного молоточка наносят легкие удары по тыльной части сечки, подбирают и выбирают лишний металл в гравируемой детали. На рис. 28, б показан способ прорезки (подсечки) сечкой канавки на гравируемой детали, зажатой в тисках. В этих случаях пальцы левой руки прижимают сечку к детали, а правой рукой гравировальным молоточком наносят легкие удары по тыльной части сечки, выбирая лишний металл. В процессе удаления металла с заготовки необходимо следить за тем, чтобы режущая кромка сечки была всегда острой и не соскальзывала с вырубаемой канавки или выемки и не портила гравируемой детали.
Рис. 28. Приемы вырубки сечкой канавок в гравируемой детали: а – выборка металла; б – прорезка канавки
Изготовление резинового штемпеля
В граверной практике нередко приходится изготавливать различные печати и штемпели. Поскольку металл для таких изделий подходит плохо, материалом здесь служит резина.
Выбранную заготовку из куска прочной и достаточно эластичной резины обрезают ножом по размеру будущего штемпеля и приклеивают клеем 88Н к массивной деревянной колодке, чтобы обеспечить безопасность в процессе работы с острым режущим инструментом. Затем, загрунтовав белилами или любой другой краской рабочую поверхность резиновой заготовки, заранее обработанную абразивными материалами и доведенную до идеально ровного состояния, карандашом по краске вычерчивают текст. Надпись на заготовке штемпеля должна быть выполнена в зеркальном (обратном) отображении (рис. 29, д), т. е. читаться не слева направо, а справа налево. Тут же по торцам заготовки проводят и линии, определяющие глубину выборки резины из пробельных участков как внутри букв, так и между ними. Для предупреждения стирания линий загрунтованную поверхность можно слегка закрепить быстросохнущим лаком.
Рис. 29. Вырезание по резине: а – плоские ножи; б – просечка; в – радиусный нож; г – скальпель; д – текст, размеченный на резиновой заготовке; е – выполнение надрезов сверху; ж – выборка просечкой внутренней части буквы О
Следующий этап – подготовка соответствующего инструмента. Резину обрабатывать не так легко, как кажется на первый взгляд. Для этого требуется особый инструмент (рис. 29, а – г).
Вырезая мелкие тексты и рисунки, опытные мастера предпочитают пользоваться лезвиями для безопасной бритвы, распилив их на удобные для работы кусочки. Для предупреждения порезов пальцев рук эти кусочки насаживают на удлиненные ручки-державки. Вырезание из резины необходимого контура рисунка или буквы ведется, как правило, не в продольном направлении, а сверху вниз. Так называемое надрезание (оконтуривание) следует производить на заранее выверенную глубину, чтобы при вырубке с торцов ненужных кусочков резины не вскрылись сквозные прорезы основания заготовки, влекущие за собой невозможность получения в дальнейшем качественного отпечатка.
Процесс вырезания, например, слова «ОТК» начинают с того, что плоским ножом сверху вниз (рис. 29, е) надрезают контуры у букв К и Т до отчерченной на торце заготовки линии. То же самое проделывают плоским и полукруглым (радиусным) ножами при оконтуривании буквы О. Внутреннюю часть буквы О выбирают трубчатой просечкой меньшего диаметра (рис. 29, ж). При этом следует отметить, что после поперечной просечки резиновой заготовки на глубину до отчерченной линии на торце сразу же настраивают инструмент на подрезку в продольном направлении, толкая его к центру буквы. Это дает возможность срезать (выбрать) всю внутреннюю часть без применения других инструментов.
Убедившись, что контуры надрезаны у всех букв и на одну глубину, приступают к отделению пробельных участков. Для этого скальпелем и плоскими ножами различной конфигурации, способными добраться до нужных участков, производят подрезку с торцов. Чтобы не испортить товарного вида изделия, при вырезании букв следует стараться избегать недорезов и подрывов на пробельных (нерабочих) участках, так как подобные неровности на резине чрезвычайно трудно заглаживать.
Таушировка (инкрустация)
Таушировка, она же инкрустация или насечка, – своеобразный древний прием украшения драгоценными металлами бронзовых и стальных предметов, преимущественно доспехов и оружия. В настоящее время этот способ применяют для декорирования цветными и драгоценными металлами художественных и бытовых изделий. Сущность процесса насечки заключается в том, что наружную поверхность инкрустируемого предмета специальным образом насекают (отсюда и название) и полученные щели набивают цветным или драгоценным металлом в виде узора или рисунка. В одних случаях это тончайший орнамент из завитков и стилизованных растений, в других – изображения животных, птиц или человека. Иногда методом насечки осуществляют надписи на металле, орнаментированные в той или иной манере.
Долгое время об инкрустации древних мастеров можно было судить лишь по описаниям. Только после раскопок так называемых шахтовых гробниц в Микенах удалось обнаружить бронзовые кинжалы, отделанные золотом и серебром. Однако для инкрустирования изделий тогда применяли не только золото и серебро, но и другие металлы. В I тысячелетии до н. э., когда железо было большой редкостью, бронзовые изделия инкрустировали вставками из железа. Дагестанские мастера из селения Кубачи, художественное оружие которых пользовалось успехом в разных странах, инкрустировали с большой любовью также металлические предметы домашнего обихода. При обучении технике насечки кубачинские мастера вместо серебра использовали сурьму и олово, а вместо золота – латунь, только после этого они доверяли успешно освоившим мастерство драгоценные металлы. Старые мастера порой говорили: «У хорошего мастера и латунное изделие дороже золотого». В Эрмитаже хранятся изготовленные из латуни и бронзы в XIX веке подносы, кувшины, светильники, ступки, украшенные золотой и серебряной насечкой. С успехом инкрустировали бытовые предметы также тульские мастера.
И сейчас, кроме насечки золотом, серебром и драгоценными сплавами, широко применяют и обычные цветные металлы и их сплавы. В частности, весьма оригинально смотрится насечка алюминием по стали. Алюминиевая проволока хорошо держится в углублении, легко полируется и образует красивый светлый рисунок на темном стальном фоне, несколько напоминающий насечку серебром. Но поскольку насечка по металлу – техника трудоемкая, она постепенно стала применяться все реже и реже и в настоящее время встречается лишь у отдельных мастеров.
Владимир Иванович Даль, большой знаток всевозможных ремесел, упоминает о том, что «в Сибири делают и медную насечку, насекая винтовки медной проволокой». Разумеется, это была насечка медью по железу, точнее по стали, из которой изготавливают обычно металлические части винтовки.
При насечке на поверхности основного металла делают углубления, которые сформированы так, чтобы можно было вложить и вковать в них более мягкий металл. Художественный эффект насечки заключается в различии цвета основного и вкованного металла. Они образуют на готовом изделии единую поверхность, и создается впечатление, будто на основном нарисован орнамент из цветного металла.
К материалу, применяемому для насечки, предъявляют такие требования:
• вкладка и основа должны иметь различные, желательно контрастные, цвета;
• вкладка должна быть мягче, чем основа.
Особенно хорошие результаты получаются, когда серебро или золото таушируют в сталь. Кроме того, для насечки по стали в качестве вкладки можно применять медь, латунь, мельхиор, железо, олово, свинец. Допустимо также использовать бронзу или латунь как основу, которая может быть украшена серебром или медью.
Несколько слов о применяемых инструментах. Поскольку работать придется с металлами с различной твердостью, нужно изготовить инструменты, имеющие разный угол заточки клиновидной режущей рабочей части зубилец и конусной – штихелей и сечек. Угол заточки инструментов для работы по твердой стали, а также бронзе и чугуну примерно будет равен 70°, для стали, имеющей небольшую твердость, – 60°, для латуни и меди – 45° и для алюминия – 35°.
С правой стороны на верстаке мастер постоянно держит два молотка: одним работает с зубильцами и чеканами, другой использует при вбивании металла в углубления и проковке элементов инкрустации. Ко второму молотку предъявляется очень важное требование: необходимо, чтобы рабочая поверхность бойка была тщательно отполирована и закалена. Он не должен оставлять на инкрустации царапин, вмятин и других механических повреждений, удалить которые часто бывает не так-то просто. Молоток, имеющий хорошо отполированный боек, одновременно уплотняет и выглаживает металл, облегчая последующую шлифовку и полировку.
Изделия или отдельные их детали в зависимости от формы и размеров либо закрепляют в тисках, либо кладут на массивную стальную плиту, укрепленную в толстом кряже. Используют также любые другие наковальни, всевозможные оправки из массивного металла. Например, кольцо или перстень насаживают на массивный стальной стержень, который закрепляют в тисках. Отдельные небольшие плоские предметы закрепляют мастикой на деревянной подложке, которую фиксируют в шаровых тисках, а те, в свою очередь, располагают на кожаной гравировальной подушке.
Инкрустация делится на два основных вида: плоскую и рельефную. В плоской инкрустации все вставные элементы находятся заподлицо с поверхностью изделия, в то время как у рельефной они несколько выступают, образуя небольшие бугорки. В одном изделии возможно сочетание этих двух видов насечки.
Поскольку плоская насечка более проста в исполнении, с нее и следует начинать осваивать приемы работы. Нет необходимости сразу же пытаться украсить какое-то изделие. Прежде всего нужно понять сущность технологии таушировки.
Небольшие кусочки металла толщиной не менее 3 мм вполне пригодны для упражнений. Сначала орнамент рисуют на бумаге в натуральную величину, после чего переносят на поверхность основного металла.
Для гарантированной устойчивости и качественной фиксации вкладка должна расширяться книзу, т. е. в сечении иметь форму трапеции. Такой же формы должно быть и углубление в основном металле. Чтобы получить необходимые углубления, применяют следующие технические приемы.
Положите стальную пластину на наковальню и установите зубильце на контур рисунка. Нанесите по нему несколько сильных и равномерных ударов. Как только зубило войдет в металл примерно на глубину 0,5–0,8 мм, нужно передвинуть, вновь нанести такое же число равномерных ударов (рис. 30, а). При этом зубило войдет в металл на ту же глубину, что и в первом случае. Таким образом, полученное углубление в металле будет иметь на всем протяжении одинаковую глубину. На первых порах число ударов можно подсчитать. В дальнейшем необходимость в этом отпадет, так как основным ориентиром будет ритмичное постукивание, за которым мастер ведет контроль как бы автоматически, не задумываясь над этим, поскольку все его внимание должно быть уделено точной и плавной стыковке получаемых зубилом углублений.
При погружении зубильца или чекана в металл образуются не только углубления. Часть металла под действием клина вытесняется и приподнимается по краям канавки над инкрустируемой поверхностью. Приподнятые острые кромки металла называют гартом или облоем. Именно облой и используют для закрепления металлических вставок. После проковки инкрустируемой поверхности они зажимают вставленную в канавку проволоку. Для того чтобы лучше прижать материал и этим повысить удерживаемость вкладки, шероховатым чеканом проводят по краю вертикальных стенок канавки.
Но такое крепление не очень прочное, так как после шлифовки и полировки часть прокованного облоя снимается. Чтобы повысить прочность вставных элементов инкрустации, на дне канавки насекают острым зубильцем дополнительно две канавки (рис. 30, б). Одну из них делают с наклоном вправо, другую – влево. Обработанные таким образом углубления в сечении будут представлять собой расширяющийся книзу трезубец. Забитый в такое углубление мягкий металл благодаря этому прочно соединится с основой.
Рис. 30. Таушировка: а – формирование канавки с помощью зубильца или чекана; б – нанесение дополнительных бороздок зубильцем; в – гравирование канавок шпицштихелем; г – выполнение канавок флахштихелем и болтштихелем; д – скашивание стенок шпицштихелем; е – вколачивание вкладки в канавки
Есть и другой способ дополнительного крепления элементов вставок в углублениях. Дно канавки насекают сечкой с остро отточенной рабочей частью, имеющей в сечении четырехугольник или треугольник. При такой обработке на дне канавки образуются углубления с облоем в виде острых заусенцев. При выполнении этой операции сечку наклоняют то в одну, то в другую сторону относительно поверхности обрабатываемого изделия.
Углубления под инкрустацию на небольших металлических предметах могут быть выполнены гравировальными инструментами (рис. 30, в – д). Контурный и обронный виды гравировки, имеющие при гравировании самостоятельное значение, здесь становятся первой подготовительной стадией инкрустирования. Но выполненная резцами или зубильцами гравировка требует дополнительной обработки. В контурных углублениях с помощью шпицштихеля скашивают с одной и другой стороны стенки так, чтобы в сечении вместо прямоугольника была трапеция. Стенки углублений скашивают также в других гнездах-углублениях, имеющих самую разную конфигурацию, например лепестка, цветка, всевозможных геометрические фигур.
Контурную резьбу, предназначенную специально для инкрустирования, можно выполнять сразу шпицштихелем, ориентируясь на линии рисунка, нанесенного на поверхность металла. Все линии рисунка гравируют шпицштихелем так, чтобы полотно клинка было наклонено под небольшим углом вправо. Затем, ориентируясь на тот же контур и держа штихель под тем же наклоном, гравируют в обратном направлении. Если посмотреть на полученную канавку в сечении, она будет похожа на ласточкин хвост.
Углубления для таушировки можно получить также химическим и электрохимическим методом. Сначала поверхность основного металла гравируют путем стандартного химического или электрохимического травления[7], после чего штихелем подрезают боковые стенки так, чтобы канавки имели трапециевидное сечение.
После этого можно приступать к собственно инкрустации. Если гнезда под инкрустацию выполнены на стальном предмете, для упражнений в таушировке можно использовать круглую медную или латунную проволоку.
Вместо проволоки применяют также нарезанные из листового металла узкие полоски с прямоугольным сечением. Всевозможные фигурные вставки вырезают из листового металла, толщина которого должна соответствовать глубине вырубленного в металле гнезда. Проволоку и пруток отжигают на огне до красного каления.
Работа по заполнению углублений, выполненных чеканом, зубильцами и гравировальными инструментами (рис. 30, е), идет в следующей последовательности. Конец проволоки вставляют в конце углубления и крепят легким ударом молотка с полированным бойком. Затем укладывают проволоку на следующем участке и вновь ударяют молотком. Так проволоку или пруток постепенно вколачивают в углубления легкими ударами молотка. Когда все углубления будут заполнены до конца, более сильными ударами молотка выступающие элементы инкрустации проковывают так, чтобы они оказались заподлицо с поверхностью инкрустируемого предмета, особенно по краям, чтобы сгладить возможные неровности и гарантировать прочное закрепление. Мягкий металл вставок, как пластилин, наполнит прорезанные и выбитые в металле углубления, вклинившись в них так, что выковырять его можно только с большим трудом, разрушив всю инкрустацию. Большое значение для прочного сцепления металлов имеют заусенцы на дне углублений. Они врезаются в мягкий металл вставок, затем при проковывании загибаются – и эти крючки надежно удерживают элементы вставок.
Ту же роль заусенцы, полученные с помощью острых сечек, играют при инкрустировании плоскими фигурными вставками, розетками, лепестками, бутонами фигур человека и животных. На дне гнезда, вырубленного в изделии по форме вставного элемента, насекаются канфарником[8] углубления под разными углами.
Если углубления сделаны зубилом, поступают следующим образом: после того как проволока на небольшом участке уложена в канавку, проходят шероховатым чеканом по основному металлу с обеих сторон рядом с вложенной проволокой. Благодаря этому выступы (облой), располагающиеся по краям углубления, прижимаются к вкладке с обеих сторон. Затем чеканом еще раз обрабатывают основной металл вокруг вкладки и окончательно прижимают вложенную проволоку.
После полного заполнения рисунка вкладкой поверхность изделия шлифуют и полируют. Если в качестве основы используют сталь, то ее тонируют в сине-серый цвет. Иногда насечку на изделии дополнительно рассекают туповатым зубилом. Эта операция придает изделию своеобразный вид.
Механическое гравирование
Механизация граверных работ возможна при использовании специального оборудования и применении усовершенствованного инструмента. При этом можно за одну установку обрабатывать деталь, гравировать, сверлить и фрезеровать сопряженный профиль канта или каналов, расположенных на поверхности детали. В промышленности такие работы проводят на копировально-фрезерном станке с пантографом. Нужный текст и узор набирают из трафаретов, которые закрепляют на копирном столе станка. Плечи пантографа настраивают в нужном масштабе с учетом размера шаблонов, деталь (заготовку) закрепляют в рабочем поле станка и приступают к фрезерованию. Выборка металла получается в результате своевременного опускания и подъема резца в шпинделе пантографа и одновременных задержек копировального пальца в нужных местах трафаретов.
Для мелкосерийной и кустарной работы промышленные станки малоприменимы. Они громоздки, потребляют много электроэнергии, а изготовление шаблонов для штучной работы попросту нецелесообразно. К тому же недостатком гравировки на станке с пантографом является то, что в переходах линий (особенно в острых углах) получаются скругления от вращающегося резца и для получения острых углов требуется их дополнительная подрезка и опиловка.
Работа на настольном копировально-фрезерном станке
На рис. 31 изображен настольный вариант копировально-фрезерного граверного станка. Он предназначен в основном для выполнения на изделиях крупных надписей и рисунков как в стационарных, так и в походных условиях, имеет небольшие габаритные размеры и малую массу, что позволяет транспортировать его к месту работы в чемодане.
На таком станке можно производить различные операции по обработке поверхностей изделий из органического стекла, всевозможных пластмасс, металлов и их сплавов.
Копирование на данном станке осуществляется с помощью шиберной системы. Станок состоит из двух плит (шиберов), станины в виде швеллера, шпинделя с приводом от электродвигателя через гибкий вал и линейки с пазом для набора и установки шрифта. Плиты соединены между собой и со станиной роликами таким образом, что при передвижении копировального пальца (щупа) по копиру или шаблону верхняя плита, несущая копировальный палец и шпиндель, постоянно скользит по верхнему поперечному пазу нижней плиты. Одновременно приходит в движение и нижняя плита, скользя по направляющим станины в продольном направлении – то слева направо, то справа налево.
Рис. 31. Настольный копировально-фрезерный станок «Малыш»: 1 – шиберы; 2 – электропривод; 3 – станина; 4 – линейка для набора трафаретов; 5 – копировальный палец (щуп); 6 – шпиндель с резцом
Копирование осуществляется вручную в результате движения плит, которые повторяют рисунок, вычерчиваемый копировальным пальцем, скользящим по канавкам копира. Отличительной особенностью конструкции является копирование как надписей, так и различного рода изображений без какого-либо искажения в масштабе 1:1. Такое устройство позволяет успешно производить операции гравирования на деталях любых размеров и наносить надписи высотой шрифта 6 мм и более. С целью изменения размеров шрифта пользуются несколькими наборами копировальных планок разных по высоте шрифтов.
В комплект станка входят электродвигатель с гибким валом, дополнительные верхняя и нижняя плиты, крепежные винты и струбцины. Наличие дополнительных шиберов, отличающихся габаритами и массой, позволяет использовать станок как для выполнения мелких граверных операций, так и для гравирования надписей на нестандартных изделиях со сравнительно большими поверхностями, т. е. оформлять всевозможные вывески и мемориальные доски.
Граверный станок «Малыш» имеет простую конструкцию, и для умелого специалиста изготовить такой станок даже своими силами не составит особого труда, тем более что материалом для конструкции может служить толстое органическое стекло, которое, как известно, легко поддается всем видам механической обработки.
Работа на станке заключается в следующем. Станок устанавливают на стол или верстак, на рабочей плите закрепляют пластину для гравирования, набирают шрифт и, взявшись обеими руками за ручки, смонтированные на верхней плите (шибере), приводят в действие копировальное устройство.
Плавными движениями заставляют скользить копировальный палец по углубленному контуру знака или буквы, выгравированному на копировальной планке. Одновременно с этим, нажимая большими пальцами на гашетки, опускают шпиндель вниз, подводя резец к обрабатываемой поверхности.
Для гравирования на больших досках и плитах станок крепят к поверхности изделия струбцинами, предварительно установив его на разметку будущей строки. В этом случае рабочую плиту необходимо снять, чтобы освободить доступ резцу к обрабатываемой поверхности. Отвернув ограничительную гайку, ввинчивают втулку со шпинделем в шибер на величину подачи шпинделя, достаточную для обеспечения нормального режима гравирования. Затем, набрав в паз шрифтовой линейки первое слово из копировальных планок или букву, подсоединяют к хвостовику шпинделя гибкий вал от электродвигателя, вставляют резец и приступают к работе.
Выборку металла вращающимся резцом производят с постепенной вертикальной подачей шпинделя. Для наблюдения за поведением резца и правильностью установки копировального устройства относительно разметки в шибере и станине предусмотрены смотровые окна (для конструкции из оргстекла окна не нужны). Установка копировального устройства на линию разметки осуществляется передвижением шрифтовой линейки в вертикальном направлении и набора шрифта вдоль паза шрифтовой линейки в горизонтальном направлении.
При использовании станка для гравировки пуансонов и деталей с выступающими частями, превышающими величину наименьшего хода шпинделя вверх, применяют подкладную раму. Подкладная рама снабжена подъемным механизмом, позволяющим поднимать и опускать рабочую плиту (столик). В этом случае рабочая плита снимается со станины граверного станка и крепится на подкладной раме.
Работа бормашиной
Как говорилось выше, гравировальные станки хороши для тех случаев, когда изделия выпускаются партиями или являются однотипными (например, вывески, текст которых можно легко набрать из кассы трафаретов). В частной, тем более в любительской практике их использование не имеет большого смысла. Зато широкой и заслуженной популярностью пользуются универсальные устройства, известные как прямые шлифмашинки, многофункциональные электроинструменты или электрограверы. Пожалуй, самым популярным подобным инструментом является изделие компании «Dremel», чье название стало нарицательным для устройств данного вида. Однако задолго до появления подобной продукции на прилавках наших магазинов и профессиональные граверы, и народные умельцы использовали для гравирования стоматологическое оборудование – всем известные бормашины.
«Dremel» («Дремель») – торговая марка ручного электро– и пневмоинструмента и принадлежностей к ним. Происходит от фамилии американского изобретателя и промышленника Альберта Дж. Дремеля, разработавшего первые модели высокоскоростного роторного ручного инструмента и основавшего в 1932 году «Dremel Company» для производства такого инструмента. В 1993 году торговая марка была приобретена фирмой «Bosch», производство по состоянию на 2008 год осуществляется инструментальным подразделением этой фирмы «Robert Bosch Tool Corporation». Главный офис компании по производству инструмента под маркой «Dremel» располагается в Маунт-Проспект, штат Иллинойс, США.
Бормашина – весьма простой инструмент. Она состоит из мотора, муфты, гибкого вала и наконечника, в цанговом зажиме которого крепится зубной бор, служащий режущим инструментом, фреза того или иного типа, абразивный камень, металлическая щетка или отрезной диск (рис. 32). Подобное же устройство имеют и вышеописанные электрограверы, поэтому для единообразия все их будем называть бормашинами.
Рис. 32. Бормашины: а – многофункциональное устройство фирмы «Dremel»; б – гибкий вал с наконечником; в – зубной бор со сточенным кончиком шарика
Основной узел в данном случае – гибкий вал с наконечником, который передает вращение от электродвигателя к закрепленному в цанговом зажиме бору. Имея такой вал, можно, в принципе, зажать его ось непосредственно в патрон электродрели или шуруповерта. Подобный комплект позволит справиться с простейшими граверными работами. Однако качество их будет невысоким. Дело в том, что частота вращения у большинства дрелей (а также распространенных бытовых электродвигателей) не превышает 3,5 тысячи оборотов в минуту (об/мин), тогда как электрограверы позволяют работать со скоростью до 30–37 тысяч об/мин, а некоторые бормашины – до 400 тысяч об/мин. Именно высокооборотистый привод позволяет качественно работать по металлу, тогда как низкоскоростная машинка годится только для уверенной работы по пластмассам и кости.
Бормашины широко используют для написания адресов (дарственных надписей) на различных материалах, а также для написания всевозможных поздравлений на посуде, чего невозможно добиться штихелем. Бормашиной можно наносить надписи в самых труднодоступных местах, она применима как для плоскорельефного, так и для обронного гравирования, где требуется выборка большого количества металла. Но мы сосредоточим внимание только на плоскорельефном гравировании. Сюда входит выполнение надписей различного характера как прямым шрифтом, так и рукописным на незначительную глубину.
Перед тем как приступить к работе, привод электрогравера или прямой шлифмашинки лучше подвесить – это сглаживает вибрацию. К тому же лежащий на столе работающий электроинструмент может свалиться на пол, потянув за собой гибкий вал и испортив тем самым работу. В комплекте с гравером иногда есть стойка-кронштейн для крепления его в подвешенном состоянии.
Бор вставляют в наконечник с гибким шлангом и обводят им контуры изображения. После нанесения основных контуров рисунка выполняют более мелкие детали. Тени выполняют последними, их можно изобразить в виде штриховки линиями, кружками, клеточками.
Борами можно выполнять объемные, рельефные и контурные работы. Для написания текстов применяют в основном шаровидные боры. С целью достижения отчетливой проработки деталей букв граверы, как правило, у такого бора стачивают кончик шарика (рис. 32, в).
У каждого мастера свои излюбленные методы работы. Для начала вы можете попробовать следующую технологию выполнения надписи. Для первой проработки контура закрепляете в цанге самый тонкий бор и проходите им всю надпись, не задерживаясь на утолщениях и завитушках, так чтобы толщина букв выглядела одинаковой. Затем этим же бором выполняете утолщения шрифта, как правило, внутри буквы. Проверяете и подправляете завитушки и украшения шрифта.
Теперь смотрим, что получилось. Линии полученной надписи шероховатые, скорее напоминают борозды, особенно там, где прорабатывались утолщения или проводили бором несколько раз. Для исправления этого берем бор или абразивную насадку немного большего диаметра и проводим по местам утолщения, тем самым выравнивая верхний слой. Абсолютной гладкости без длительной тренировки достичь довольно сложно, но вид в любом случае получится уже совсем другой, а это главное.
Приемы написания знаков, букв и цифр вращающимся бором, особенно если его обороты незначительны, не соответствуют тем, которыми мы привыкли пользоваться при письме авторучкой или карандашом. При нанесении на изделие того или иного знака либо изображения следует начинать гравирование вертикальных линий сверху вниз, а горизонтальных – справа налево, т. е. против направления вращения инструмента. Чем выше скорость привода, тем более гладкой будет выгравированная канавка. Правда, при высоких скоростях удержать инструмент так, чтобы глубина гравировки получалась постоянной, нелегко. Ко всему нужна привычка, так что регулярные тренировки на обрезках различных материалов – залог успеха вашей работы. Возьмите небольшую пластинку и проведите по ней гравером тонкие линии, завитушки, эллипсы и круги. Когда рука натренируется, можно приступать к выполнению рисунка, при этом рука будет двигаться так же легко, как и с карандашом.
Общее правило – чем тверже материал, тем выше должна быть скорость инструмента. Например, для работы по оргстеклу (плексигласу) не следует выставлять скорость выше 8000 об/мин, так как на высоких скоростях плексиглас будет сильно плавиться и может даже налипать на бор. В случае если производится матирование того же плексигласа абразивной насадкой (точильным камнем), можно выставить скорость вращения на уровне 15 000 об/мин. При работе с медью или алюминием скорость должна быть выше, а при гравировке по стали вам, скорее всего, потребуется установить максимальную скорость вращения бора.
При покрытии фона на большой площади независимо от того, бором вы это делаете или абразивной насадкой, необходимо наносить полоски в одном направлении, иначе рисунок будет смотреться некрасиво. Также одно из основных условий получения достойного результата – отсутствие небрежности и спешки. Важно не прикладывать слишком больших усилий и не пытаться вогнать в материал насадку. Помните, что машина должна выполнить всю работу, а не вы!
И еще одна важная особенность при работе с металлом. При проведении линии, будь то надпись или рисунок, важно направление движения руки, угол наклона насадки. При этом на поверхности выгравированной в металле канавки создаются ворсинки, которые играют, блестят, переливаются на свету. Под разными углами освещения эффект будет разным. Поэтому положение руки при выполнении надписи всегда должно быть одинаковым. В большинстве случаев это же относится и к рисунку. Однако с этим эффектом можно поэкспериментировать, создавая гравированные изображения, которые по-разному выглядят в зависимости от направления источника света.
Желательно, чтобы во время гравирования рука плавно скользила по поверхности стола или обрабатываемого материала. Для этого можно надеть перчатку или проложить ткань между рукой и столом (заготовкой).
Технология выполнения надписей на подарках достаточно проста. Она состоит из следующих операций:
• выборки материала бором;
• втирания краски-основы в гравировку;
• засыпки и растирания бронзовой пудры по поверхности надписи.
Для втирания в гравировку обязательно следует брать густотертую масляную краску – цинковые или свинцово-цинковые белила. Любая другая краска для этих целей непригодна. Втирать краску нужно пальцем или тампоном круговыми движениями, давая тем самым возможность краске заполнить все углубления.
Убедившись, что краска втерта достаточно прочно и надпись ясно читается, излишек краски стирают с поверхности изделия ветошью без ворса. Те же манипуляции проделывают и после растирания бронзовой пудры.
Как уже упоминалось, бормашина незаменима при гравировке по стеклу, которое штихелем можно только расколоть. Для такой работы существуют определенные правила.
Для нанесения надписи на стекло к нему с обратной стороны прикрепляют бумагу с надписью для гравировки, а с лицевой стороны смазывают растительным маслом, которое во время резания стекла алмазным бором предотвращает распыление стеклянной пыли и позволяет считывать текст.
Рисунок или надпись можно и перевести непосредственно на стекло. Делают это так. Чистую поверхность стекла протирают тампоном, смоченным раствором канифоли в спирте или ацетоне. После того как покрытие подсохнет, через копировальную бумагу переводят рисунок. Пропущенные места подрисовывают простым мягким карандашом.
Гравируют рисунок, держа стеклянный предмет в левой руке, упирая его в край стола или положив на него. Прорабатывают рисунок, начиная снизу, так чтобы пыль летела вниз и не забивала рисунок. При гравировке следят, чтобы линии были достаточно заглублены, а толщина их соответствовала задуманному рисунку.
Иногда для подчеркивания каких-либо деталей бывает необходимо заматировать их. Для этого накладывают на нужное место кусок наждачной бумаги средней зернистости и пальцем слегка натирают это место, вращая бумагу. Маленькие участки матируют палочкой, на торец которой приклеивают наждачный порошок.
Рисунок на отгравированной стеклянной поверхности можно тонировать. Для этого в гравировку затирают масляную художественную краску темных тонов.
Фарфоровые изделия гравируют так же, как и стеклянные. В гравировку в этом случае обязательно затирают краску. Популярна и так называемая штриховая роспись фарфоровых изделий алюминием и другими металлами. Этот процесс имеет название «натирание металлами».
Натирание алюминием проводят, применяя все ту же бормашину. Рабочим инструментом является диск из листового алюминия, зажатый в специальной оси от шлифовальных кругов для бормашин. Толщина диска – 0,3–0,5 мм, диаметр – 10–20 мм. Желательно применять диск с крупным диаметром (около 20 мм), так как он дает более четкую и однородную линию штриха.
Вращающийся алюминиевый диск, касаясь поверхности фарфора, разрушает глазурь. Разрушение глазури происходит за счет окиси алюминия, имеющейся на поверхности диска. В неровности затираются мелкие частицы алюминия.
Как уже было сказано, натирание производят и другими металлами и сплавами, например медью и латунью. Но медь и латунь быстро окисляются на поверхности фарфора, и со временем вместо блестящего получается темный штрих, как бы затертый черной краской. Алюминиевый штрих остается блестящим неограниченно долго.
При натирании чистую поверхность фарфора покрывают суспензией титановых белил. Для ее приготовления берут жидкий столярный клей и в нем замешивают сухие титановые белила. Этой суспензией покрывают поверхность фарфора. С помощью копировальной бумаги переводят рисунок, подрисовывая неясные места мягким карандашом.
Рисунок прорабатывают алюминиевым диском. Правила нанесения штрихов остаются такими же, как и для гравирования стекла абразивами. Если плоскость диска совпадает с линией штриха, получают тонкую линию, если не совпадает – толстую.
При необходимости получают и крупный участок поверхности, покрытый алюминием. Для этого вращающимся диском быстрыми движениями водят по этой поверхности.
После нанесения всего рисунка титановые белила удаляют тампоном, смоченным горячей водой.
Подобную технику используют и в том случае, если нужна надпись временного характера на стекле. Используя дюралюминиевые диски, гравер механически наносит на стекло слой металла. Выполненную таким образом надпись можно смыть серной кислотой.
Рисунки на стекле и фарфоре должны быть четкими, с минимальным количеством штрихов и, конечно, красивыми.
При натирании фарфора алюминием желательно выбирать изделие, окрашенное в темные тона, тогда рисунок будет выразительнее.
Художественное травление металла
Художественное травление металла издавна известно оружейных дел мастерам. Оно заменило один из трудоемких процессов – ручную гравировку, не опустив при этом планку качества.
Техникой травления сравнительно легко можно на любом металле воспроизвести рельефный или углубленный орнамент, сюжет, текст. Даже для таушировки можно использовать этот метод, при котором образуются канавки для запрессовки проволоки или металлических контрастирующих полосок. Требуется только небольшая доводка – расширение днища канавок, что значительно экономит время по сравнению с выполнением этих углублений техникой гравировки.
Существует два способа травления – химический и гальванический. Второй более эффективен и менее вреден: раствор электролита не выделяет ядовитых газов, которые неизбежны при химическом способе.
Химическое гравирование металлов
Сущность технологического процесса изготовления художественных изделий методом химического травления (рис. 33) состоит в следующем: металлическое объемное изделие или пластину покрывают слоем кислото– и щелочеупорного лака. После высыхания лака на его поверхности прочерчивают тонким резцом линии рисунка, предварительно переведенные с помощью копировальной бумаги на поверхность лаковой пленки. После этого с поверхности изделия тщательно удаляют лаковую стружку и погружают его в травильный раствор. При травлении не защищенные лаком участки металла будут растворяться, образуя на поверхности канавки-штрихи, идентичные рисунку.
По окончании травления лак с поверхности изделия удаляют органическим растворителем. Продолжительность травления определяют визуально.
Рис. 33. Схема процесса химического травления: 1 – травильная жидкость; 2 – слой лака; 3 – изделие; 4 – корпус ванны
Строго говоря, химическое гравирование можно производить двумя способами: либо покрыть веществом, на которое действует протрава, все линии и поверхности рисунка, либо, наоборот, защитить от действия кислот все промежутки, оставляя линии и поверхности рисунка свободными. Если затем погрузить изделие в состав для травления, то в первом случае рисунок получится слегка рельефным, а во втором – углубленным. Первый способ применяют в цинкографии для изготовления клише, с которого затем печатают бумажные оттиски. Вторым же способом проводят художественное гравирование металлических поверхностей.
Процесс химического травления несложен, но художественное исполнение гораздо труднее, так как требует тщательной, кропотливой работы по созданию композиции рисунка и четкого переноса его на подготовленное изделие. К тому же как ни проста на первый взгляд технология травления, начинающие часто терпят неудачу, в особенности при травлении тонких рисунков.
Прежде чем наносить предохраняющее покрытие, обрабатываемую поверхность следует тщательно очистить от тонкого налета ржавчины, жира и иной грязи. Поверхность изделия зачищают, шлифуют, полируют, обезжиривают, промывают и просушивают. Приставший к поверхности жир можно удалить промыванием в спирте или бензине, прокаливанием или провариванием в подогретом до 50 °С 10 %-м растворе едкого натра в течение 5 мин. Затем изделие на 1–2 мин переносят в 15 %-й раствор серной кислоты и хорошо промывают в горячей воде, чтобы покрывной лак прочно держался на поверхности металла и в процессе травления не отслаивался.
После этого обрабатываемую поверхность можно отполировать, если форма предмета позволяет, а назначение его не противоречит этой операции. Но подобная предварительная полировка не обязательна. До вычищенной поверхности нельзя дотрагиваться пальцами, так как на них всегда есть некоторое количество жирового вещества, а на жир протрава не действует.
Когда протравливаемая поверхность вычищена уже настолько, что имеет свежий металлический блеск, приступают к нанесению предохранительного покрытия. В качестве покрытия для химического гравирования применяют битумный, нитролак или лак следующего состава: 6 г. канифоли, 10 мл этилового спирта, 10 капель нашатырного спирта. Если в этот лак добавить 2–3 кристаллика сухих фиолетовых чернил, то его можно использовать для нанесения рисунка на металлическую поверхность с помощью рейсфедера. В этом случае после травления рисунок будет выпуклым, а не в виде канавок, как в случае прочерчивания рисунка на сплошной лаковой поверхности. Чернила служат для визуального контроля над процессом нанесения лаковых штрихов: прозрачный лак контролировать трудно.
Для алюминия используют так называемое «белое чернило», образующее устойчивую пленку. В его состав входят: 100 массовых частей клея 88, 90 массовых частей каолина и органический растворитель, например этиловый спирт, – до получения консистенции жидкой сметаны.
При нанесении предохранительного покрытия необходимо следить за тем, чтобы металлическая поверхность была совершенно сухой, иначе покрытие местами плохо пристает, а кислота может проникнуть до металла и протравить места, которые должны остаться нетронутыми.
Хорошую покрывную смесь для гравирования готовят следующим образом: расплавляют 1 часть асфальта (битума) и 2 части мастики, перемешивают и добавляют 2 части белого воска. По охлаждении этот состав формуют в шарики или конусы, которые заворачивают в тряпку из тонкого полотна. Состав наносят на поверхность следующим образом: обрабатываемый предмет подогревают и, слабо надавливая на поверхность, водят по ней равномерно массой, завернутой в тряпочку; при этом состав тает и просачивается сквозь тряпку, покрывая тонким слоем натираемую поверхность. Когда покрытие затвердеет, его покрывают как можно более тонким слоем свинцовых белил, мелко растертых и растворенных в гуммиарабике. На этот слой переводят рисунок.
При покрытии лаком всей поверхности изделия после высыхания защитного слоя его покрывают тонким слоем свинцовых белил или красят белой гуашью («белое чернило» в таком покрытии, разумеется, не нуждается). Затем отточенным карандашом или с помощью копировальной бумаги переводят на белую поверхность требуемый рисунок или надпись.
Все места, которые требуется вытравить, проскабливают после этого до поверхности металла. Тонкой и острой гравировальной иголкой можно воспроизвести даже тончайшую тушевку рисунка.
Если нужно протравить простую фигуру или надпись, предохранительное покрытие можно разбавить какой-нибудь жидкостью, например скипидаром, до консистенции густой масляной краски. По такому покрытию можно воспроизвести требуемый рисунок от руки иглой или даже стальным пером.
Для травления при химическом гравировании используют различные составы, в зависимости от вида металла.
Протравливаемый предмет опускают в кислото– и щелочеупорную посуду и заливают соответствующим растворителем. Такой посудой может служить глиняная глазурованная или пластмассовая кювета (ванночка). Если обрабатываемая поверхность представляет собой плоскость (пластину), то можно установить ее в горизонтальном положении, вылепить по краям бортик из воска или пластилина толщиной в палец и в полученную таким образом плоскую кюветочку налить соответствующую кислоту.
Таблица 2. Составы растворов для травления при химическом гравировании
Примечание: Ств – сталь высоколегированная, Ст – сталь углеродистая, М – медь, МС – сплавы меди, А – алюминий, AC – сплавы алюминия, Ц – цинк.
Если металл растворяется очень быстро, возникают следующие осложнения:
• кислота проникает под слой покрытия, и рисунок утрачивает четкий контур;
• повышение интенсивности действия кислоты приводит к разрушению покрывной смеси на больших участках изделия и к браку;
• невозможно надежно контролировать глубину травления.
Скорость процесса определяют по интенсивности выделения пузырьков газа, поднимающихся от мест травления. При бурном выделении пузырьков в травильный раствор следует добавить дистиллированную воду.
В процессе травления на поверхности изделия оседают пузырьки, которые могут задерживать процесс травления. Их необходимо удалять кисточкой или чистым гусиным пером. Для проверки глубины травления в ванну одновременно с изделием помещают контрольный образец из того же материала с фрагментом рисунка или простым узором. Образец вынимают, промывают в проточной воде и замеряют глубину рисунка. По ней судят о глубине и времени травления. Если необходима различная глубина травления, то изделие время от времени извлекают из ванны, промывают, просушивают и лаком покрывают те места, которые уже достаточно протравились. Затем травление продолжается.
Когда травление считают оконченным, предмет прополаскивают в чистой воде, а предохранительное покрытие удаляют нагреванием или смывают его скипидаром или соответствующим нанесенному лаку растворителем. Может случиться, что в углублениях останется некоторое количество протравы, которая со временем разъедает металлическую поверхность местами глубже, чем требуется. Во избежание этого промытый предмет кладут на несколько минут в известковую воду, которая нейтрализует остаток кислоты.
Гальваническое гравирование металлов
Второй способ травления несложен, требует наличия простого источника постоянного тока и позволяет производить гравирование на всех металлах и сплавах, даже на закаленной и нержавеющей стали. Способ этот похож на химическое гравирование, но имеет много преимуществ перед ним:
• травления гальваническим способом происходит быстрее;
• контуры вытравленного рисунка получаются более резкими и отчетливыми;
• в состав протравы не входят едкие кислоты.
Если рассмотреть через лупу рисунок, вытравленный химическим способом, то окажется, что края отдельных углубленных линий неровны и чем глубже линия, тем она шире протравлена. При гальваническом способе травления края отдельных линий получаются совершенно гладкими, а стенки углублений – вертикальными.
Изделие под электрохимическое гравирование подготавливают так же, как при химическом гравировании. Затем его помещают в электрохимическую ванну и в качестве анода подключают к положительному выводу источника тока (рис. 34, а). Обычно такой предмет подвешивают на проволоке, которая припаивается оловянным припоем к непокрытому месту изделия; место спайки покрывается лаком (для тяжелых предметов придется предусмотреть дополнительные подвесы из инертного материала). Отрицательный вывод подключают к катоду, представляющему собой свинцовую пластину[9]. Источник постоянного тока должен иметь рабочее напряжение 5–10 В. Составы электролитов для электрохимического гравирования и режимы обработки зависят от материала конкретного изделия.
Таблица 3. Составы электролитов для электрохимического гравирования
Примечание: Ст – сталь, М – медь, Л – латунь, А – алюминий и его сплавы.
Рис. 34. Гальваническое гравирование: а – обычный способ; б – полусухой способ; в – схема включения для переменного тока: 1 – корпус ванны; 2 – изделие (анод); 3 – подвес; 4 – раствор электролита; 5 – свинцовая пластина (катод); 6 – подводящие провода; 7 – выключатель; 8 – источник постоянного тока; 9 – покрытие (слой воска); 10 – слой ваты или ситца (пропитанный электролитом); 11 – источник переменного тока
Если различные части рисунка требуется протравить до различной глубины, то через некоторый промежуток времени предмет вынимают из ванны, споласкивают его и на места, которые не требуется вытравлять глубже, кисточкой наносят предохранительное покрытие, а затем снова вешают предмет в ванне и продолжают травление.
Добившись желаемого результата, ток отключают, проволоку отпаивают, изделие промывают скипидаром и приступают к окончательной отделке – шлифовке, полировке.
Электрогравирование можно осуществить и так называемым полусухим способом. Берут металлическую пластинку, на которой надо выгравировать рисунок, узор, надпись, с одной стороны к ней припаивают провод и подключают его к положительному полюсу источника постоянного тока, с другой – тщательно полируют поверхность. Затем пластинку нагревают до температуры 100–120 °С и натирают место, где будет рисунок, парафином, стеарином, воском или просто свиным салом так, чтобы это покрытие расплавилось и покрыло поверхность металла тонким ровным слоем.
Когда пластинка остынет, иглой процарапывают линии желаемого изображения и осторожно удаляют стружки покрытия. Затем на рисунок кладут ровный слой ваты или кусок ситца, сложенный втрое, смоченный в 30 %-м растворе поваренной соли, так, чтобы вата или ситец плотно прилегали к пластинке. На вату или ситец кладут другую металлическую пластинку, соединенную с отрицательным полюсом батареи. Проверяют, чтобы между пластинами не было прямого соприкосновения (чтобы исключить возможность короткого замыкания), и включают ток.
Через 10–15 мин, в зависимости от силы подаваемого тока, на металлической пластинке вытравится нарисованный вами на жировой поверхности рисунок или надпись. Если желательно протравить рисунок очень глубоко, надо дольше держать его под током. Схема подключения изделия при полусухом электрогравировании показана на рис. 34, б.
Когда будет закончен процесс травления, пластинку тщательно промывают водой, немного подогревают, снимают с нее слой жира и тщательно протирают тряпкой.
Выгравированный таким способом рисунок на алюминии получается нарисованным бархатисто-черными штрихами. На желтой латуни рисунок получается коричневатый.
Чем тверже металл, тем больше времени потребуется для его протравливания. Если на алюминии протравливание можно производить за 10–15 мин, то на латуни потребуется 40–45 мин. Величину тока подбирают опытным путем.
За неимением источника постоянного тока можно произвести электрогравирование и переменным током низкого напряжения и не особенно большой силы. Однако такой процесс гравирования будет проходить значительно медленнее. Это происходит, во-первых, потому, что переменный ток 50 раз в секунду меняет свое направление и эффект травления производится сразу на обе пластины; во-вторых, от переменного тока пластины быстро нагреваются и ток приходится часто выключать, чтобы жировой слой не растаял и не залил рисунка. Если это случится, придется все начинать сначала.
Электрогравирование переменным током можно несколько ускорить, если под напряжение одновременно класть две пластинки с рисунками, т. е. вместо свободной катодной пластины использовать еще одну пластину с рисунком.
Электрогравирование переменным током лучше производить при напряжении 2 В и никак не более 4 В. Держать под током пластины надо не более 5–7 мин, затем делать перерыв минут на пять и снова включать. Раствор соли следует брать 15 %-й, тогда он будет медленнее вскипать.
Схема включения для электрогравирования переменным током дана на рис. 34, в.
Способы отделки изделий
Для повышения художественной ценности, выразительности, антикоррозийной стойкости и износостойкости изделий, а также для придания им законченного вида применяют целый комплекс различных отделочных операций. Существует три вида отделки: механическая, химическая и электрохимическая (гальваническая).
Механическая отделка изделий
Шлифование – это чистовая обработка поверхностей деталей абразивными инструментами. Шлифование металлических деталей осуществляют на шлифовальных станках вращающимися абразивными кругами, сегментами или брусками.
Механический процесс шлифования можно проследить на примере работы шлифовального круга, который состоит из абразивного и связующего материалов (рис. 35). На войлочные или фетровые круги наклеивают абразивный порошок из корунда, наждака, жженой извести и др. Круг устанавливают на шлифовальный станок. Изделие прижимают к вращающемуся шлифовальному кругу, и остроугольные абразивные кристаллы действуют на его поверхность как зубья фрезы – снимают тонкий слой металла, устраняют неровности, бугорки, царапины. В процессе шлифования абразивные зерна по мере их затупления скалываются и выпадают из связующего вещества, обнажая новый слой незатупившихся. Таким образом происходит как бы самозатачивание круга. При очень прочном удержании связующим веществом абразивного материала круг быстро «засаливается» (забивается стружками пространство между зернами абразива) и его режущая способность резко снижается. Поэтому необходимо следить, чтобы зерна абразивного материала, затупившись, своевременно выпадали из круга и высвобождали новые зерна.
Глубина захвата резания и качество обработки зависят от величины кристаллов (зерен) абразивного материала, твердости и пластичности обрабатываемых изделий. Мягкие, пластичные металлы (медь, алюминий) быстро «засаливают» круг, поэтому его следует периодически очищать, а хрупкие и твердые вызывают преждевременное скалывание кристаллов, что ускоряет изнашивание круга.
Полирование является продолжением процесса шлифования, когда гладкую матовую поверхность изделия с помощью полировников или мелкозернистых полировочных абразивных паст доводят до зеркального блеска, т. е. достигается высокий класс чистоты. Это не всегда последний процесс отделки изделий. Иногда ювелирные изделия (кольца, серьги, кулоны) подвергаются дальнейшей отделке (золочение, серебрение), а полирование служит лишь подготовительной операцией, подобно шлифованию. Но при отделке оксидированных художественных изделий, выполненных техникой чеканки, художественной ковки, литьем, полировка является завершающей стадией отделки, когда надо подчеркнуть отдельные выпуклые формы, усилить их значимость, выразительность всей композиции.
Рис. 35. Схема процесса шлифования
В процессе полирования с поверхности обрабатываемых изделий не снимается стружка, как при шлифовании, а в результате обработки полировником под давлением сглаживаются микронеровности, что придает металлу глянцевый вид.
Под действием очень тонких зерен полировочных паст на жировой основе при полировании на полировочном круге в месте касания поверхности обрабатываемой детали с кругом металл сильно нагревается, его тягучесть и пластичность увеличиваются. Силы трения сдавливают мельчайшие неровности, заполняют ими микроуглубления без отделения стружки, сминают и разглаживают бугорки, в результате чего поверхность изделия получает зеркальный блеск.
Различают три вида полирования: ручное, механическое и электрохимическое.
Ручное полирование применяют при отделке изделий из драгоценных металлов с помощью специальных полировальников (см. рис. 24). Механическое производят на тех же станках, что и шлифование; отличие состоит лишь в более мягких кругах из шерстяной или хлопчатобумажной ткани, на которые наносят специальные полировочные пасты. Электрохимическое полирование – это анодное травление изделий в среде электролита под действием электрического тока. Последний способ имеет ряд преимуществ перед другими видами полирования: возможность обработки труднодоступных мест, сокращение потерь драгоценных металлов, равномерное сглаживание металла по всей поверхности, полное сохранение конфигурации изделия.
Крацевание – обработка изделий с помощью металлических щеток. Применяется как самостоятельный вид отделки художественного литья или как подготовительная операция перед химической либо гальванической отделкой. Крацевание производят вручную (ручными щетками) и на полировальных станках (стальными или латунными круглыми вращающимися щетками). Щетки изготавливают из стальной, латунной, нейзильберовой проволоки диаметром 0,15–0,25 мм. Изделия из твердых металлов (сталь, чугун) крацуют стальными жесткими щетками; из мягких (цинк, медь, алюминий и др.) – мягкими латунными щетками; из драгоценных металлов – тонкими нейзильберовыми щетками.
При крацевании изделие смачивают 3 %-м раствором поташа или специальным мыльным препаратом, что облегчает скольжение проволочек и предотвращает засаливание щетки. Чтобы избежать образования полос на поверхности изделия, направление движения щетки нужно многократно изменять.
Шабровкой называется срезание (соскабливание) тонких частиц металла с поверхности обрабатываемой детали с помощью шабера. Этот процесс можно сравнить с фугованием досок в столярной практике. Шабровка осуществляется ручными или механизированными инструментами – шаберами, которые представляют собой металлические стержни с режущей кромкой на концах. По форме режущей части различают шаберы плоские, трехгранные и фасонные; по конструкции – цельные и со вставными режущими пластинами. Применяют данный вид обработки для получения гладких, ровных и чистых поверхностей литых и ювелирных изделий; при гравировании на металле для удаления заусенцев (барб), а также для выравнивания зернистой поверхности металлической доски при гравировании в технике меццо-тинто и др.
При шабровке в одном направлении возникает волнистость, поэтому шабруют попеременно в двух взаимно перпендикулярных направлениях, что позволяет получать наиболее ровные поверхности. Толщина стружки при черновой шабровке – 0,02–0,05 мм, при чистовой – не более 0,01–0,02 миллиметра.
Галтование – это полирование давлением мелких изделий во вращающихся барабанах с мыльным раствором с помощью стальных шариков, конусов, цилиндриков.
Этот вид отделки возник при дальнейшем развитии метода полирования стальными полировниками. Изделия укладывают в барабан, наполненный стальными шариками и мыльным раствором. При вращении барабана мелкие шарики и изделия непрерывно перемешиваются, шарики, перекатываясь по поверхности, сглаживают неровности и шероховатости. Шарики диаметром 1–5 мм изготавливают из хромистой стали и закаляют. Продолжительность обработки латунных штампованных изделий – 2–8 ч; бронзовых литых – 10–15 ч; изделий из ковкого чугуна – 24–48 ч; из серого чугуна – 70–80 часов.
Галтование значительно дешевле ручного полирования гладильником, но имеет ряд недостатков: применяется только в массовом производстве, когда в барабан одновременно можно заложить много однотипных предметов. Для полых и очень нежных изделий этот метод вообще непригоден, так как шарики могут повредить их. В этом случае вместо шариков в барабан иногда кладут обрезки замши, деревянные опилки, песок.
Пескоструйная отделка – обработка в пескоструйных аппаратах поверхности изделий сухим песком, который подается под давлением по резиновому шлангу с помощью сжатого воздуха. В результате отделки изделия приобретают мелкозернистую равномерно-матовую поверхность.
Пескоструйный аппарат представляет собой цилиндрический сосуд конусообразной формы с насадкой для гибкого шланга, к которому подключается сильный центробежный вентилятор. На цилиндре имеется смотровое окошко, которое позволяет следить за ходом рабочего процесса.
Нижняя часть сосуда заполняется мелким кварцевым песком, изделия загружаются через два боковых облицованных тканью отверстия. При включении вентилятора крупинки песка под действием сжатого воздуха с огромной скоростью подбрасываются вверх, обстреливают поверхность изделий, оставляя на ней крохотные вмятинки, тем самым создавая матовую бархатистость.
От размера крупинок зависит фактура изделия: для чеканных и штампованных из тонкого листового металла изделий – 0,05–0,15 мм; для поделочной стали и литья – 0,2–0,5; для крупных деталей экстерьерного декора из чугуна, бронзы, алюминия – 0,5–1,5 миллиметра.
Виброобработка – схожий с галтовкой процесс полирования в среде наполнителя, но не во вращающемся барабане, а в вибрирующем контейнере. Поверхность изделий сглаживается в результате взаимного трения. Процесс происходит в закрытом контейнере виброустановки, куда вместе с изделиями помещают наполнитель (стальные и стеклянные шарики, древесная мука) и моющий раствор (г/л): нашатырный спирт – 25–15; мыльная стружка – 15; моющее средство – 10; хлорная известь – 8; двууглекислый натрий – 7; хлористый натрий – 2. В контейнер вначале загружают стальные и стеклянные шарики, а после включения виброустановки – химические компоненты, древесную муку (10 г/л) и воду. После тщательного перемешивания наполнителя и моющего состава загружают изделия. Преимущество этого способа в том, что на полирование виброобработкой затрачивается значительно меньше времени, чем на галтование.
Шлифующие и полирующие материалы
Шлифование и полировка поверхности готовых изделий до зеркального блеска производится с помощью различных абразивных материалов, изготовленных из природных минералов, пород вулканического происхождения или окисей металлов с примесью специальных добавок.
Наждак – минерал темно-серого или черного цвета, состоящий из корунда (Al2О3), смешанного с магнетитом, гематитом, пиритом и кварцем. Глыбы минерала размалывают и полученный абразивный материал прессуют в шлифовальные круги или наклеивают на бумажную и тканевую основу (шлифовальные шкурки). Наждаком шлифуют металлы, драгоценные камни, стекло и другие материалы. Мелкозернистый мягкий наждак используют для полирования.
Карборунд (карбид кремния SiC) – бесцветный кристалл с алмазным блеском. Применяется как абразив, который получают нагреванием кокса и кварцевого песка с добавлением опилок и поваренной соли в электропечи при температуре 2000–4000 °С. Кристаллы соединяются керамическим раствором. Карборундом шлифуют стальные инструменты, драгоценные камни и другие твердые и хрупкие материалы.
Кварц (диоксид кремния SiO2) – минерал, составляющий до 12 % земной коры. Применяется в виде кварцевой муки или песка при изготовлении наждачной бумаги и в пескоструйных аппаратах; в виде порошка и паст – для чистки предметов домашнего обихода.
Трепел – легкая пористая осадочная порода желто-коричневого цвета. Смешивается с маслом и используется для полировки металлов драгоценных камней, стекла.
Пемза – пористая вулканическая порода (лава). Применяется для шлифовки. Кусковой или порошковой пемзой шлифуют предварительно смоченные водой мягкие металлы, камни, кость; кусковой нешлифованной пемзой очищают пробирный камень от штрихов металлических сплавов; порошковой пемзой протирают чеканные изделия, покрытые патиной.
Венская известь (жженая известь) изготавливается из минерала доломита. Неустойчива на воздухе, поэтому должна храниться в закрытых сосудах. Применяется для полировки мягких металлов, органического стекла и других материалов.
Магнезия (оксид магния MgO) – белый легкий порошок. Наиболее мягкое полировочное средство. Применяется в смеси с оксидом алюминия, венской известью и другими добавками в виде белой политуры.
Известь (углекислый кальций СаСО3) – отмученный натуральный мел. Используется как основа для различных полировочных паст и порошков.
Крокус (красная политура) – натуральный оксид железа с примесью глины или кремния. Полировальный порошок изготавливается из размолотого и промытого красного железняка или путем искусственного окисления железных опилок.
Оксид хрома (Cr2О3) – порошок серо-стального цвета. Образует зеленую политуру, которая используется для обработки твердых металлов.
Диоксид олова (SnО2) – серый, очень мягкий порошок мелкозернистого строения, получаемый при сжигании олова. Применяется как очень тонкое полировочное средство для изящных изделий.
Оксид цинка (ZnO) – получают при сжигании металла на воздухе. Применяется как тонкое полировочное средство для изящных изделий.
Корунд (оксид алюминия Al2О3) – минерал, природный безводный глинозем. Применяется для шлифования и полирования твердых металлов.
Гематит (оксид железа Fe2O3) – минерал серо-стального цвета. Используют для ручного полирования, подобно стальному полировальнику.
Мыльный корень (мыльник) служит для очистки изделий после протравливания, обезжиривания и покрытия металлами в гальванических ваннах. Отваром мыльного корня смачивают крацовочную щетку.
Шлифовальные и полировальные пасты содержат тонкие абразивные порошки, жировые связки и специальные добавки. Абразивными материалами являются оксиды хрома и кремния, крокус. Оксид хрома придает пастам зеленый цвет, оксид железа – красный, технический мел – белый. В качестве связок в пастах используют стеарин, парафин, техническое сало, церезин, воск. Специальными добавками служат двууглекислая сода и олеиновая кислота (вводятся для активизации процесса полирования), скипидар и керосин (для изменения вязкости).
При ручном и механическом полировании полируемые части промывают в растительном или техническом масле.
Оборудование и инструменты
Шлифование и полирование производят на станках быстровращающимися кругами из различных материалов и вручную – кательниками, брусками, полировниками из металла и другими приспособлениями.
Различают два основных типа приводных станков для шлифования и полирования: шлифовально-полировальный станок и электрическая бормашина с гибким валом.
Шлифовально-полировальный станок снабжен двигателем переменного тока с короткозамкнутым ротором. Мощность не менее 184 Вт; скорость вращения при полировании – 2800–3000 об/мин, при крацевании – 700–750 об/мин. Для того чтобы снизить скорость вращения и сохранить полную мощность двигателя, применяют редуктор с передаточным отношением 4:1. Шлифовально-полировальные инструменты крепятся на удлиненном с обеих сторон валу.
Бормашина с гибким валом применяется для тонких работ, где требуются более мелкие шлифовально-полировальные инструменты. Последние крепятся в зажимном патроне гибкого вала.