Гравировальные работы. Техники, приемы, изделия Подольский Юрий
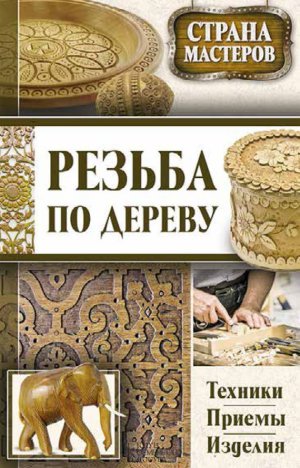
Абразивный инструмент изготавливается из абразивных материалов и предназначен для механической обработки металла и других материалов. Его можно разделить на два основных типа: жесткий (шлифовальные круги, головки, сегменты и бруски) и гибкий (шлифовальная шкурка и изделия из нее – ленты, диски и др.).
Для изготовления шлифовальных кругов и другого инструмента применяют электрокорунд, карбид кремния, карбид бора, синтетические и природные алмазы. Абразивный инструмент выпускается на керамической, бакелитовой, вулканитовой, силикатовой, глифталевой и магнезиальной связках, скрепляющих отдельные абразивные зерна.
Электрокорунд нормальный получил наибольшее применение; он выпускается трех марок: Э2, Э4, Э5. Цифры после буквы означают содержание окиси алюминия Аl2О3 соответственно 92, 94 и 95 %.
Электрокорунд белый марок Э8, Э9 содержит 98–99 % окиси алюминия и на 30–40 % превосходит по качеству электрокорунд нормальный, так как включает в себя меньше примесей. В последнее время промышленностью выпускается электрокорунд белый повышенного качества марки Э9А.
Монокорунд марок М7, М8 отличается высокой прочностью и более высокими режущими свойствами. Он содержит 97–98 % окиси алюминия. Применяется такой абразив для обработки весьма прочных сталей.
Карбид кремния – абразив, используемый для чистовой заточки твердосплавного инструмента.
Карбид бора используется в виде порошка для доводки и притирки.
Синтетические алмазы, применяемые для заточки инструментов, выпускаются нескольких марок:
• АСО (зерно № 4–25) – алмаз синтетический обычной прочности;
• АСР (зерно № 5–32) – алмаз синтетический повышенной прочности;
• АСВ – алмаз синтетический высокой прочности;
• АСК – алмаз синтетический кристаллический;
• АСС – алмаз синтетический кристаллический сортированный.
Шлифовальные круги из электрокорунда и карбида кремния изготавливают диаметром 3–1100 мм, толщиной 0,5–200 мм, диаметр посадочных отверстий – 1–305 мм; из алмазных зерен – диаметром 6–300 мм, толщиной рабочего кольца 1,5–5 мм, шириной 3–20 миллиметров.
Шлифовальная шкурка и изделия из нее выпускаются на основаниях из ткани и бумаги, с режущими зернами из электрокорунда, карбида кремния, стекла и кремния. Применяется для ручных и механизированных шлифовальных работ. В зависимости от требуемой прочности изготавливается на основаниях из бязи, саржи, полудвунитки или бумаги. Наиболее прочной основой является саржа. Связующим средством для наклеивания абразивного материала обычно служит клей из кожи и костей, но в последнее время его место занимают синтетические клеи. Величина зерен абразива определяет тонкость шлифовальной шкурки.
Эластичный полировальный круг, фетровый круг применяются для полирования гладких, ровных и выпуклых поверхностей. Размеры кругов определяются внешним диаметром. В центре круга имеется отверстие для крепления (с помощью фланцев и гайки) на вал станка.
На вращающийся круг наносят полировочную пасту, которая прочно удерживается частицами фетра. Круги из фетра являются высококачественным, стойким в эксплуатации полировальным инструментом.
Войлочный круг применяется для шлифования и полирования изделий. В первом случае используются круги из волос и шерсти животных, во втором – мягкие из чистой шерсти.
Волосяной круг (дисковые щетки) имеет деревянную основу, на которой по всей окружности укреплены торчащие волосяные кисти. Применяется для полирования изделий сложной конструкции. Эластичность дисковых щеток зависит от толщины и длины волоса. Крепится на станке так же, как войлочный и фетровый.
Матерчатый круг служит для заключительного полирования. Представляет собой выкроенные из материала (бязь, полотно, фланель) диски, сшитые концентрическими швами между собой. Чем чаще строчки швов, тем жестче круг. Матерчатые круги хорошо удерживают пасту и полируют поверхность любого вида. Долговечны в работе.
Нитяной круг (пушок) применяется для наведения блеска на поверхность изделия. Похож на волосяной круг, но вместо волосяного имеет нитяной покров. Является мягким и тонким полирующим инструментом.
Все вышеперечисленные шлифовально-полировальные круги относятся к инструменту для механической отделки изделий.
Для полирования и шлифования вручную применяется следующий инструмент. Наждачные бруски и шлифовальные напильники по форме и действию напоминают обычные слесарные напильники, но изготавливаются из дерева и оклеиваются наждачной бумагой, или же абразивный материал укрепляется непосредственно на дереве. Используются для обработки ровных плоскостей.
Точильный камень (брусок) представляет собой плоский камень прямоугольного сечения длиной 200–300 мм. При обработке на бруске изделие равномерными движениями перемещают вперед и назад по плоскости до тех пор, пока поверхность детали не будет обработана. Направление шлифования необходимо менять, чтобы не допустить образования царапин и рисок на поверхности.
Напильники из карбида кремния (карборунда) – стержнеобразные камни длиной 150 мм с разнообразными формами сечения: круглой, полукруглой, треугольной, квадратной. Имеют различную зернистость. При работе их используют как напильники, но смачивают водой, чтобы микростружка не забивала их поры.
Шлифовальные угли – приготовленные особым способом древесные угли. Изготавливают в виде брусков квадратного сечения. Используют для окончательной шлифовки металла.
К шлифующим порошковым материалам относятся пемзовая мука, трепел и венская известь.
Пемзовая мука применяется для предварительной грубой обработки больших поверхностей. Представляет собой размолотый пемзовый камень, приготовленный в виде кашицы. При смешивании с водой используется для жесткой шлифовки, при смешивании с маслом – для тонкой.
Трепел служит для шлифовки и полирования ювелирных изделий. Приготавливают его тем же способом, что и пемзовую муку. Кашицу наносят на обрабатываемую поверхность с помощью фланелевой тряпочки или кисти и продольными либо круговыми движениями прошлифовывают изделия. Для этой же цели применяют и порошок венской извести.
Шлифовальные и полировальные деревянные палочки изготавливают из твердой и вязкой древесины бересклета. Из брусков вырезают нужной формы стержень, который используют при отделке труднодоступных углублений изделия. Стержень обмакивают в кашицу из шлифующего порошка, частички абразива прилипают к нему, а при обработке вдавливаются в древесину, что способствует удержанию шлифующего вещества на инструменте.
Натянутая нить служит для полирования звеньев цепочек и мелких отверстий. Для крупных отверстий используют пучок сплетенных нитей, который смазывают полирующим веществом (жирный трепел), надевают на крючок, пропускают через отверстие, туго натягивают и водят по нему обрабатываемую деталь.
Полировник (гладило, лощильник) изготавливают из высококачественной закаленной стали. Кромка рабочего конца должна иметь закругленную, хорошо отполированную поверхность (см. рис. 24). Полировник часто имеет деревянную рукоятку. Полирование гладилом обеспечивает изделию высокий блеск. Поверхность металла уплотняется и наклепывается, что повышает твердость и долговечность изделия. Перед началом работы изделие обезжиривают, чтобы не засаливать гладило, и смачивают мыльным раствором с нашатырным спиртом для уменьшения трения. Затем с равномерным давлением проводят по поверхности штрих за штрихом. Вторичную полировку производят в противоположном направлении, чтобы избежать образования полос. При полировании гладилом отсутствуют потери металла. Недостатки метода: длительность процесса, необходимость наличия высокой квалификации и опыта у работающего.
Полировочный камень дает более высокое качество полировки, чем металлические полировники. В качестве такого камня используют гематит, форма и размеры которого соответствуют форме и рабочей части металлического гладила. К деревянной рукоятке камень обычно крепят с помощью латунной трубки.
Химическая отделка металлов
Химическая отделка изменяет и обогащает однообразный цвет металлов. Сущность ее заключается в следующем: под действием различных химических веществ на поверхности металла происходит реакция с образованием новых химических соединений, которые прочно соединяются с основным металлом и придают ему различные оттенки или новый цвет. В большинстве случаев образующиеся соединения являются окислами (кислородные соединения) или другими химическими образованиями (сернистые и хлористые соединения). В первом случае процесс называют оксидированием, во втором – патинированием. С помощью химической отделки получают защитные пленки, обладающие декоративно-антикоррозийными качествами и значительно расширяющие цветовой тон изделий. Но самой первой операцией в любом случае остается обезжиривание обрабатываемой поверхности.
Обезжиривание металлической поверхности
Металлическая деталь, находясь на воздухе, неизбежно покрывается жировыми пятнами: стоит дотронуться руками, а при обработке это происходит всегда, даже на самой блестящей полированной поверхности остается жир, препятствующий нанесению покрытия или рисунка.
Обезжиривают металлическую поверхность с помощью растворителей: ацетона, уайт-спирита и др. Смочив ватные тампоны или куски ветоши растворителем, протирайте ими поверхность до тех пор, пока на тампонах не перестанет откладываться грязь. Небольшие предметы целесообразно погружать несколько раз в любое растворяющее жир вещество: эфир, бензин, хлористый этил и т. п. Большие металлические предметы кипятят 15–30 мин в разбавленном растворе едкого натра (1 часть едкого натра на 10 частей воды), а затем ополаскивают в нескольких водах. Предметы из цинка, олова, которые в крепком щелоке могут испортиться, кипятят в 10 %-м водном растворе соды или поташа. Так как под влиянием воздуха эти предметы покрываются слоем окиси, их погружают для нейтрализации в 10 %-й раствор какой-нибудь кислоты. Из-за выделяющихся при этом газов работать нужно в хорошо проветриваемом помещении. Затем предметы ополаскивают в нескольких водах и высушивают.
В случае если нужна более тщательная очистка, прибегают к специально приготовленным растворам.
Так, стальные детали можно полностью обезжирить в растворе, состоящем из 1 л. чистой воды, 20 г. кальцинированной соды, 1 г. грамма хромпика. Налейте в эмалированную кастрюлю воды и растворите в ней соду и хромпик. Нагрев раствор на малом огне до температуры 80–90 °С, опустите в него деталь. Обработка длится 10–20 мин. Все это время раствор слегка помешивают.
Медь и медные сплавы можно обезжиривать гашеной известью, натерев ею 2–3 раза требующие очистки детали.
Состав раствора для обезжиривания алюминия и его сплавов: 50–60 г. соды кальцинированной, 50–60 г. тринатрийфосфата, 20–30 г. жидкого стекла на 1 л. воды. Продолжительность обработки – 3–5 мин при температуре 56–60 °С.
Поверхность металла в обычных условиях, помимо жировых пятен, всегда покрыта тонкой пленкой окислов, препятствующих сцеплению декоративного слоя или защитного покрытия с металлом. Обезжиривающие растворы ее не удаляют, поэтому сразу же после обезжиривания деталь надо обработать еще одним специальным раствором. Этот процесс называют декапированием – очисткой металла.
Состав декапирующего раствора для стали: 30–50 г. серной кислоты или 25–45 г. соляной кислоты на 1 л. воды.
Продолжительность обработки разведенной серной кислотой 20–60 с, соляной кислотой – 15–40 секунд.
Медь и ее сплавы хорошо декапируются в 5 %-м растворе серной кислоты в течение 20–60 с, алюминий и его сплавы – в 10–15 %-м растворе азотной кислоты в течение 5–15 секунд.
Третья подготовительная работа – пассивирование, т. е. создание специальной защиты, при которой металл длительное время не окисляется. Пассивированные поверхности прекрасно сохраняют присущий металлам блеск.
Сталь хорошо пассивировать в 20–100 г. нитрита натрия, растворенного в 1 л. воды. Время обработки – 15–20 мин при температуре 30–40 °С.
Для меди и ее сплавов следует применять раствор: 100 г. хромпика калиевого и 15 г. серной кислоты на 1 л. воды. Обрабатывать 5–10 мин при температуре 45 °С.
Алюминий и его сплавы пассивируют в растворе, состоящем из 200 г. хромпика калиевого и 1 л. воды, в течение 5–10 минут.
Окрашивание металлов
Окрашивание металлов может быть произведено двумя путями: химическим и механическим. Химическая окраска металлов основана на изменении поверхности металлов путем образования:
• химических соединений;
• гальванических осаждений.
В любом случае после применения этих способов блестящая поверхность металла покрывается тончайшим инородным слоем; иначе говоря, меняется окраска верхнего слоя, но свойства металла не изменяются.
Механическое окрашивание металлов производится следующими методами:
• нанесением красок и бронзы в порошке, прилипание которых достигается соответствующими связывающими веществами, затем смазыванием лаковых красок;
• вколачиванием красящих порошков;
• обрызгиванием распыленными металлическими частицами под сильным давлением;
• наложением листового металла и т. п.;
• эмалировкой, т. е. покрыванием плавящейся, цветной, стеклянной эмалью;
• чернением, т. е. вплавлением соответствующего порошка черной эмали в гравированные или протравленные места;
• таушировкой, т. е. вколачиванием различно окрашенных проволок или металлических пластинок в протравленные углубления.
Химическому окрашиванию металлов в большинстве случаев стоит отдать предпочтение перед механическим, особенно в тех случаях, когда дело касается художественных произведений, так как химическое окрашивание не меняет металла, из которого сделан предмет.
Безусловно, перед тем как приступить к химическому окрашиванию, необходимо подлежащие окрашиванию предметы очистить от прилипшей к ним видимой и невидимой грязи, жира, слоев окиси и т. п. Предварительно к крупным предметам необходимо прикрепить (например, припаять) металлические проволочные захваты, потому что после обезжиривания к самим окрашиваемым изделиям нельзя больше прикасаться. Мелкие предметы можно держать деревянными щипчиками или пластмассовыми прищепками, но их пружины должны быть достаточно мощными, чтобы изделие, на обработку которого вы потратили столько труда, не выпало в самый неподходящий момент.
Для того чтобы достигнуть быстрого и равномерного покрытия в красильной ванне, рекомендуется непосредственно перед этим погрузить предметы в ванну из равных частей денатурированного спирта и воды. Подлежащие обезжириванию предметы, которые должны быть гальванизированы, кладут в ванну, содержащую достаточное количество каустической соды или поташа.
Полнейшего обезжиривания и полнейшей очистки металлических предметов, каковая требуется при подготовке к гальванической обработке, достигают еще и тем, что к раствору едких щелочей добавляют раствор перекиси водорода или такие вещества, которые в соединении с водой образуют перекись. Вследствие этого на металлической поверхности происходит сильное выделение кислорода, который механически отрывает все частицы жира и грязи и этим дает доступ раствору едких щелочей к самой металлической поверхности, а также переводит некоторые загрязнения в растворимые в щелочах кислоты.
Если желают окрасить предмет только частично или в нескольких местах, то части, которые должны остаться незакрашенными, покрывают битумным, асфальтовым или нитролаком, после чего предмет опускают в красильную ванну. После произведенной окраски лак удаляют скипидаром или ацетоном и покрывают, если нужно, уже окрашенные места лаком, чтобы окрасить неокрашенные места в другой цвет в новой красильной ванне. Таким образом можно выполнить красивые сложные рисунки. Очищенные вышеописанным способом металлические предметы опускают, не дотрагиваясь до них пальцами, в соответствующую красильную ванну и после этого тщательно ополаскивают, чтобы на них не осталось никаких следов красящей жидкости, которые могут вызвать появление пятен. Затем предметы в большинстве случаев насухо вытирают (лучше всего для этого применять чистые опилки) или, если нужно, высушивают в сушильне при 90–100 °С.
При окрашивании металлических изделий описываемыми способами нужно иметь в виду то обстоятельство, что краски после высушивания всегда кажутся темнее, чем на мокрых предметах.
Отделка изделий из меди
Оксидирование меди азотной кислотой. Это один из старых, простых и надежных способов придания меди черного цвета.
С помощью щетинной кисти на изделие наносят концентрированную азотную кислоту. При этом на поверхности изделия возникает бурная реакция с выделением ядовитого газа (работу необходимо производить в вытяжном шкафу, соблюдая меры предосторожности). Поверхность изделия приобретает зеленый, а затем черный цвет. После прекращения реакции изделие равномерно нагревают до полного испарения азотной кислоты, охлаждают, тщательно промывают в горячей воде, просушивают в древесных опилках и отшлифовывают нужные места пемзовым порошком. Кисть после нанесения кислоты сразу же промывают в проточной воде, чтобы продлить срок ее службы. Тампонами из ткани и ваты для нанесения кислоты на металл пользоваться не следует, так как они сразу же распадаются (сгорают) и загрязняют продуктами распада обрабатываемую поверхность.
От концентрации кислоты и продолжительности нагрева зависит цвет отделки (от коричневого, серого до черного). Отделка очень прочная.
Патинирование серной печенью. Серную печень получают из поташа (К2СО3) и серы (S), которые берут в соотношении 1:1. Компоненты хорошо перемешивают, помещают в металлическую посуду и подогревают при постоянном помешивании до расплавления, т. е. получения темно-коричневой вязкой массы. Последнюю выливают на лист жести, дают остыть, разбивают на мелкие кусочки и укладывают в стеклянный сосуд с хорошо притертой пробкой. Хранят в темном месте.
Подготовленное изделие, отбеленное в 10–15 %-й смеси азотной и серной кислот и промытое (обязательно для всех видов химической отделки), помещают в раствор (серная печень – 12–15 г, аммиак – 15 г, вода – 1 л).
Процесс протекает при комнатной температуре. При появлении черного цвета изделие извлекают из ванны, промывают, просушивают в древесных опилках, дают высохнуть и обрабатывают латунной крацовкой или абразивными порошками.
Цвет от красно-бурого до темно-бурого получают смачиванием изделия в растворе 2–3 г. серной печени на 1 л. воды (раствор хранят не более суток); цвет старой меди – в растворе 12 г. серной печени и 15 г. аммиака на 1 л. воды. После патинирования изделие протирают порошком пемзы до тех пор, пока не получат нужный цвет.
Прочие способы патинирования. Цвет от светло-коричневого до черного получают при отделке меди сернистым аммонием (20 г. сернистого аммония на 1 л. воды). Изделие нагревают и опускают в ванну с раствором, большие изделия поливают сверху и протирают щетинной кистью. Работу производят в вытяжном шкафу. Интенсивность цвета зависит от температуры. Затем изделие промывают и сушат.
Светло-бурый или каштановый цвет изделие приобретает в растворе 20 г. сульфата меди, 25 г. сульфата никеля, 12 г. хлората калия и 7 г. перманганата калия на 1 л. воды. Процесс протекает 0,5–2 мин в нагретом до кипения растворе. Изделие погружают в раствор несколько раз и прочищают щеткой до получения желаемого цвета, затем промывают и сушат в опилках.
Цвет медной зелени получают в растворе 120 г. тиосульфата натрия и 40 г. уксуснокислого свинца на 1 л. воды. Температура раствора до 60 °С. Процесс окрашивания хорошо наблюдается и протекает быстро. После появления зелено-голубой окраски изделие промывают и сушат. Цвет в зависимости от выдержки – от светло-голубого до серовато-белого.
Глубокий черный цвет образуется в результате обработки изделия в растворе 50 г. каустической соды и 14–16 г. персульфата калия на 1 л. воды. Раствор нагревают до температуры 60–65 °С. Время обработки – 3–5 мин. Очищение пемзой выпуклых частей изделия придает ему декоративность.
Отделка изделий из латуни
Химическая обработка придает латуни разнообразные цветовые тона: от желтых, оранжевых, красных до голубых, фиолетовых, синих и черных, причем на одном изделии можно получить переходные тона различных цветовых оттенков.
Патинирование смесью растворов гипосульфита натрия и уксуснокислого или азотнокислого свинца. Позволяет получить на поверхности латунного изделия радужные оттенки: желтый, оранжевый, малиновый, фиолетовый, синий, черный.
Для этого в 1 л. горячей воды растворяют 130 г. гипосульфита натрия, в другом сосуде в 1 л. воды растворяют 35 г. уксуснокислого или азотнокислого свинца. Раствор смешивают, подогревают до температуры 80–90 °С и опускают в него протравленное и промытое изделие. Поверхность последнего быстро окрашивается в желтый, оранжевый, красно-малиновый, сменяющийся фиолетовым, цвета. При дальнейшей выдержке фиолетовый цвет переходит в синий, серый и черный. Затем реакция прекращается. Тона быстро сменяют друг друга, поэтому при получении необходимого тона изделие нужно вынуть из раствора, промыть и просушить.
Если изделие вынимать медленно, цвета будут плавно переходить друг в друга.
Патинирование с помощью гипосульфита натрия и азотной кислоты. Предварительно нагретое латунное изделие опускают в раствор (40–60 г. гипосульфита натрия и 4–5 г. азотной кислоты на 1 л. горячей воды) и наблюдают за потемнением его поверхности, которая приобретает серовато-синие или коричневато-фиолетовые оттенки. При появлении нужного цвета изделие вынимают, промывают в горячей воде. Пемзовым порошком протирают выпуклые места, вновь промывают холодной водой и просушивают в опилках. Раствор очень быстро теряет свои свойства (срок действия 15–20 мин). Данная окраска получается непрочной и нуждается в защитном покрытии. Работу производят в защитных перчатках в вытяжном шкафу.
Оксидирование азотной кислотой. Латунные изделия, покрытые слоем кислоты, при нагревании окрашиваются в голубовато-зеленый цвет. Образуется азотнокислая медь. С ростом температуры медь разлагается и на поверхности изделия появляется налет черного цвета. Изделие охлаждают, промывают, высушивают, шлифуют нужные места. Оксидирование азотной кислотой дает очень прочную оксидную пленку.
Прочие способы. Желто-бурый цвет получают при обработке изделия в растворах: первый (по 60 г. серной печени и шлипсовой соли на 10 л. воды), второй (6 г. сульфата меди и 12 см3 серной кислоты на 10 л. воды). Изделие при постоянном покачивании опускают в первый раствор, промывают и переносят во второй. Процесс повторяют до получения желаемого цвета, затем изделие промывают и сушат.
Темно-бурый цвет получают в растворе 30 г. сульфата меди, 15 г. хлората калия и 10 г. перманганата калия на 1,5 л. воды. Температура раствора – 100 °С. Для получения золотистой окраски погруженное в ванну изделие протирают щеткой. По окончании процесса его промывают и сушат.
Для коричневого цвета потребуется раствор 50 г. медного купороса и 5 г. марганцовокислого калия на 1 л. воды; для темно-коричневого до черного – раствор 20 г. бертолетовой соли и 25 %, или 40 г, нашатырного спирта на 1 л. воды. Температура – 70–80 °С. Продолжительность обработки – 5–7 минут.
Оливковый и коричневый цвета получаются в растворе 50 г. бертолетовой соли, 40 г. азотнокислой меди и 80 г. хлористого аммония на 1 л. воды. Температура – 60–70 °С. Изделия выдерживают в растворе до получения желаемого цвета, затем промывают и сушат.
Бархатисто-черный цвет придает раствор хлористой сурьмы, которую наносят кистью на поверхность изделия и натирают жесткой щеткой. В зависимости от концентрации раствора и времени обработки создаются цвета от светло-серого до черного. Работу выполняют в резиновых перчатках. Изделие промывают в теплой воде и сушат в опилках. Отделка очень прочная, выдерживает шлифование и полирование.
Отделка изделий из алюминия
Алюминий и его сплавы по химической природе значительно отличаются от других металлов и сплавов, наиболее часто применяемых в промышленности, как бы находясь на границе между металлами и неметаллами. Вследствие этого химические приемы обработки, пригодные для многих цветных металлов, при отделке алюминия не годятся.
Тонирование графитом. Наиболее простой и декоративный прием отделки чеканных и гравированных рельефов, с его помощью хорошо выявляются все детали и изделие приобретает законченный вид. Процесс сводится к следующему: отполированную поверхность изделия покрывают тонким слоем восковой мастики (можно использовать растительное масло) и припудривают порошкообразным графитом. Чистой ветошью мастику с графитовой пудрой равномерно растирают по всей плоскости рельефа. Ветошь впитывает излишки графита и мастики, поэтому по необходимости ее заменяют чистой и продолжают тонирование до получения равномерного светло– или темно-серого цвета. Выступающие части рельефа высветляют и протирают ветошью, смоченной в бензине или растворителе. Затем шерстяной тряпочкой, натертой пастой ГОИ, полируют эти места, т. е. получают мягкий переход от светлого к темному. Тонирование изделий графитовой пудрой гасит излишние блики на полированном рельефе, ярче проявляет декоративные качества алюминия.
Чернение маслом. Изделие полируют, протирают бензином, удаляя остатки полировочной пасты и других загрязнений, а затем кистью, смоченной в льняном или другом растительном масле, равномерно покрывают поверхность. Пластину ставят в горизонтальное положение и с обратной стороны начинают подогревать ее паяльной лампой. Подогревать следует равномерно по всей площади и не задерживать пламя на одном месте, так как металл может расплавиться и работа будет испорчена. После испарения масла рельеф (в зависимости от продолжительности нагрева) приобретает светло– или темно-коричневый цвет. При светлой окраске металл просвечивает сквозь пленку тонировки, а при более продолжительной выдержке при нагреве пленка получается глухой. Черное тонирование с последующей полировкой делает алюминиевые изделия похожими на серебряные.
Химических методов чернения алюминия практически почти не существует, потому что как поделочный материал его начали применять гораздо позже других металлов.
Отделка стальных изделий
Воронение стальных изделий. Красивый синий и синевато-черный тон с металлическим блеском образуются при оксидировании стальных изделий в растворе 400 г. едкого натра, 600 мл воды и по 10 г. калийной селитры и азотнокислого натрия. Изделие погружают в нагретый до 100 °С раствор, выдерживают до необходимого оттенка и прокаливают до получения равномерной окраски по всей поверхности.
Существует и другой способ. Изделие погружают в расплавленную (310–350 °С) натриевую селитру. Через 3–5 мин на поверхности образуется тонкая, но очень прочная пленка синего цвета. Для получения синего цвета составляют два раствора: 140 г. гипосульфита на 1 л. воды; 35 г. уксуснокислого свинца на 1 л. воды. Перед употреблением их смешивают и нагревают до кипения. Отполированные и обезжиренные изделия погружают в этот раствор и держат до образования желаемого цвета. Затем промывают в горячей воде, сушат и слегка протирают тряпочкой, смоченной касторовым или чистым машинным маслом.
Черной или темно-синей окраски достигают следующим образом. Тщательно отполированное и обезжиренное в щелочах изделие промывают и прогревают при температуре 60–70 °С, помещают в муфельную печь и нагревают до 320–325 °С. Ровная окраска зависит от равномерного прогрева. Обработанное изделие быстро протирают тряпкой, смоченной в конопляном масле, снова слегка прогревают и вытирают насухо. Антикоррозийная стойкость изделия невелика из-за очень тонкой (доли микрона) оксидной пленки.
Светлые и темно-серые тона образуются при обработке стали слабым раствором азотной кислоты (1 ч. кислоты на 10 ч. воды). При продолжительном нахождении в растворе изделие начинает разрушаться, так как скорость реакции прогрессирует за счет выделения теплоты.
Черно-коричневый оттенок можно получить следующим образом. Готовое изделие покрывают маслом или олифой и нагревают до 300–400 °С. Равномерная тонировка достигается равномерным нагревом.
Чернение стальных изделий. Очищенное и отшлифованное изделие погружают в ванну с концентрированным раствором гидрата оксида нитрита и нитрата натрия, нагретым до 129 °С. Время обработки – 7–10 мин. Затем изделие промывают и сушат.
Отделка изделий из серебра
Существует целый ряд рецептов для химической отделки изделий из серебра. Приведем наиболее простые.
Черный цвет с синим оттенком получают при обработке изделий в подогретом до 60–70 °С растворе серной печени. Время обработки 3–5 мин. Черный, серый, черный с синеватым оттенком цвета – в растворе 5 г. серной печени и 10 г. углекислого аммиака на 1 л. воды; глубокий черный цвет – в растворе 25 г. сернистого калия и 10 г. углекислого аммония на 1 л. воды; светло-коричневый цвет – в растворе 10 ч. медного купороса, 5 ч. нашатырного спирта и 100 ч. уксусной кислоты; черный с коричневатым или сероватым оттенком – в растворе 2 ч. медного купороса, 1 ч. азотно-кислого аммония, 2 ч. нашатырного спирта и 10 ч. уксусной кислоты; темно-коричневый тон – в растворе 20 г. сернистого аммония на 1 л. воды; от светло-серого до темно-голубого – в растворах 15 г. серной печени, 40 г. хлористого аммония или 1,5 г. серной печени и 10 г. углекислого аммония на 1 л. воды; зеленовато-серый цвет – в растворе 3 ч. концентрированной соляной кислоты и по 1 ч. йодистого калия и воды. При приготовлении последнего раствора йодистый калий вначале размешивают в воде, а затем полученную смесь вливают в кислоту.
Химическое пассивирование (получение бесцветной защитной пленки). Этот метод широко применяется в промышленности. На поверхности изделий образуется тонкая плотная и эластичная пленка, которая длительное время сохраняет блеск полированного металла. Состав раствора: на 1 л. воды 10 г. двухромовокислого калия и 1 г. окиси хрома. Температура раствора – 18–25 °С, время обработки – 1–2 с. Изделия быстро промывают и сушат.
Технология получения различных тоновых оттенков на поверхности серебряных изделий для всех растворов, приведенных выше, аналогична.
Чернение – вид декоративной отделки, заключающийся в наложении на поверхность изделий легкоплавкого сплава серебра, свинца и серы, а также других компонентов. Этот сплав называют чернью. Лучше всего поддаются чернению сплавы серебра и золота. В первом случае создается сильный цветовой контраст, что особенно украшает изделие. Медные заготовки также можно чернить таким способом, но коэффициенты усадки сплава черни и меди имеют небольшие различия, поэтому при остывании чернь крошится и отслаивается от поверхности чеканного или гравированного изделия. Чернь в основном применяют для отделки изделий из серебра.
Технология чернения заключается в следующем. На изготовленном изделии прорезают плоские канавки глубиной до 0,3 мм (техникой чеканки, гравированием, травлением или тиснением штампами). Эти углубления – места наложения черни.
Рецепты приготовления черни (компоненты даны в массовых частях):
• серебро – 3, медь – 2, свинец –2;
• серебро – 3, медь – 1, сера – 3;
• серебро – 1, медь – 2, олово – 3, бура – 6;
• серебро – 1, медь – 3, свинец –3, бура – 6;
• серебро – 2, медь – 4,5, свинец – 4,5, сера – 24, бура – 1;
• серебро – 2, медь – 5, свинец – 3, сера – 24, бура – 1;
• серебро – 1, медь – 2, свинец – 3, сера – 12, бура – 1;
• серебро – 1, медь – 5, свинец – 7, сера – 24, бура – 4;
• серебро – 1, медь – 4,5, свинец – 1,4, сера – 10,7, бура – 1;
• серебро – 1, медь – 2, свинец – 1,4, сера – 10,7, бура – 1;
• серебро – 9, медь –1, свинец – 1, сера – 30, висмут – 1.
Существует несколько способов приготовления черни. Различие их в том, что в одних случаях металлы вначале сплавляют между собой, а потом добавляют серу, в других вначале получают сернистые металлы и затем сплавляют.
Первый способ – в графитовом тигле под слоем буры сплавляют серебро с медью с добавлением нужного количества свинца или олова. Расплав очищают от шлака, вводят в него серу и другие компоненты, тщательно перемешивают, удаляя шлак. Чистый расплав выливают в воду и дают остыть; твердый сплав измельчают и повторяют плавку с добавлением буры и серы до образования однородной массы. Чернь считается качественной при трехкратном повторении плавки. Затем ее опять измельчают и просеивают через малое сито.
Второй способ – каждый из металлических компонентов (серебро, медь, свинец) смешивают с серой и выдерживают в муфельной печи при температуре 300–400 °С. Соотношение серебра и свинца с серой выражается как 5:1, меди с серой – 3:1. Сернистые соединения каждого металла измельчают и берут (в массовых частях): сернистого серебра – 1,1; сернистой меди – 4,5; сернистого свинца – 4,4. Смесь сернистых соединений плавят в тигле при температуре 800 °С. Не доводя до полного нагрева, в расплав вводят хлористый аммоний (1 ч. на 3,5 ч. расплава). Затем сплав выливают на подогретую чугунную плиту и дают остыть.
Состав (в массовых частях): серебра – 1, меди – 8, свинца – 4, серы – 3,5, хлористого аммония – 2,8.
Хорошо измельченный порошок черни разбавляют раствором буры, поташа и поваренной соли. В качестве флюса можно использовать нашатырный спирт. Полученную кашку накладывают на участки, подготовленные для чернения, и уплотняют шпателем, излишки убирают. Изделие просушивают, обжигают в муфельной печи при температуре 300–400 °С до полного расплавления черни и подвергают механической обработке (опиливают надфилями или напильниками излишки черни, шабрят, полируют). При образовании сколов или других дефектов плавку повторяют с добавкой черни.
Приложение: образцы графики для гравирования по металлу
Рис. 36. Свечи и дубовые листья
Рис. 37. Панно с растительным орнаментом
Рис. 38. Простые букеты
Рис. 39. Свеча
Рис. 40. Цапля
Рис. 41. На болоте
Рис. 42. Цветы
Рис. 43. Бабочка
Рис. 44. Розы
Рис. 45. Натюрморт со свечами
Рис. 46. Розы
Рис. 47. Свеча
Рис. 48. Эйфелева башня
Рис. 49. Двое
Рис. 50. Храм
Рис. 52. На берегу пруда
Рис. 51. Горная вершина
Рис. 53. Лебединое озеро
Вместо заключения: Техника безопасности при проведении слесарно-граверных работ
Случаи травматизма при проведении слесарно-граверных работ возникают вследствие недостатков в организации производства и незнания или несоблюдения основных правил техники безопасности. Гравер должен хорошо знать причины несчастных случаев во время работы и своевременно принимать соответствующие меры предосторожности. Чистота и порядок на рабочем месте, грамотное освещение последнего, правильное расположение инструмента также способствуют безопасному и продуктивному труду.
Основные требования ко всем видам применяемого инструмента: инструмент должен быть исправен, удобен в работе и не должен являться причиной различных травм. Поверхность бойка молотков должна быть слегка выпуклой и гладкой, без заусенцев и трещин. Ручки молотков изготавливают из сухого дерева твердых и вязких пород: клен, береза, вяз, кизил, рябина и др. Древесину подбирают без сучков, трещин и других дефектов, волокна должны быть направлены вдоль оси ручки. Последняя заклинивается заершенным клином из мягкой стали. Делать ручки из мягких или крупнослойных пород дерева (ель, сосна) запрещается.
На штихели, напильники, шаберы и другие инструменты с острыми концами должны быть насажены деревянные ручки с гладкой поверхностью. Шейку ручки скрепляют металлическим бандажным кольцом (для предотвращения раскалывания), которого не должны касаться хвостовики инструмента.
На ударной поверхности инструмента для чеканки и рубки металла (зубила, просечки, сечки, канфарники и др.) не допускаются заусенцы, выбоины, трещины, а тыльная часть инструмента не должна быть сбита или скошена. Длина инструментов должна обеспечивать безопасное удерживание их во время работы рукой (не менее 150 мм). Работа неисправным инструментом может стать причиной травматизма как самого работающего, так и окружающих.
Чеканы, зубила с очень «сухой» закалкой при работе разламываются и могут нанести ранения работающему. Представляет опасность также чрезмерно сильно или слабо натянутое полотно ножовочной пилы.
Применяемые для опиливания (срезания слоя металла) заготовок напильники не должны иметь загрязненных и затупленных поверхностей. Очищать напильник от приставших стружек и грязи следует только металлической щеткой. Мелкую металлическую стружку, накопившуюся при гравировании, нельзя сдувать с изделия, так как она может попасть в глаза. Удалять стружку нужно только с помощью небольшой щетки-сметки или же широкой щетинной кисти, сметая ее в коробку.
Ручки для напильников изготавливают из мягких пород дерева, чтобы они не раскалывались при насаживании на хвостовик напильника. Не допускается пользование напильником без ручки или с неисправной ручкой (расколотой или без насадного кольца).
Выполняя слесарные операции, детали надо прочно закрепить в тисках. Последние должны быть в полной исправности. При рубке и обработке листового металла следует пользоваться предохранительными очками и защитными брезентовыми рукавицами. При работе надфилями, шаберами, лобзиком необходимо беречь руки от уколов и порезов.
Следует знать и помнить, что металл, остывший до 400–500 °С, по внешнему виду не отличается от холодного, а прикосновение к нему может привести к серьезным ожогам.
При отделке готовых изделий шлифованием и полированием необходимо иметь вытяжные устройства для улавливания абразивной пыли и продуктов распада войлочных кругов, пропитанных полировочными пастами. Во время работы на заточных, шлифовальных и других станках необходимо следить за тем, чтобы рукава спецодежды (халата) были плотно застегнуты или закатаны, руки работающего не находились в опасной зоне работы движущихся деталей оборудования.
Даже при эпизодических занятиях в условиях домашней мастерской не следует пренебрегать индивидуальными средствами защиты. Так, для защиты глаз от стружек, мелких частиц твердых тел и мелких осколков применяют защитные очки открытого и закрытого типа. При работе с сухими сыпучими химическими веществами (приготовление растворов) пользуются техническими резиновыми перчатками. Для защиты органов дыхания от вредных веществ, присутствующих в атмосфере в виде паров, газов, пыли, дыма и тумана, служат респираторы. Кроме того, в слесарных мастерских или других местах проведения работ обязательно должна быть аптечка с медикаментами для оказания первой помощи пострадавшему.
В процессе механического гравирования, в особенности при работе с хрупкими материалами, такими как латунь марки ЛС59, необходимо надевать предохранительные очки, так как мелкая стружка с большой скоростью отлетает от вращающегося резца фрезы и может вызвать травму глаз.
Верстак, оборудование, детали очищают от опилок, пыли и стружки щетками. Разлитое на полу масло вытирают ветошью или засыпают это место песком, опилками и немедленно убирают их.
Заточный станок с абразивным кругом относят к категории оборудования с повышенной опасностью. Работать на нем без предохранительного кожуха категорически запрещается, так как может произойти разрыв абразивного круга. Станок должен быть оборудован устройством для отсоса абразивной пыли. В процессе работы глаза следует защитить прозрачным экраном или очками.
Для предохранения рук при заточке инструмента в качестве упора применяют регулируемый подручник. Зазор между краем последнего и рабочей поверхностью шлифовального круга должен быть не более 3 мм. Несоблюдение его приводит к заклиниванию обрабатываемой детали между подручником и кругом и к разрыву круга. Подручник крепят так, чтобы обрабатываемая поверхность соприкасалась с кругом на уровне горизонтальной оси или чуть выше.
Перед установкой на станок абразивный круг осматривают и простукивают киянкой – круг с трещиной издает глухой или дребезжащий звук. На плоской торцовой стороне круга указана допустимая окружная скорость. Круги диаметром 150 мм (окружная скорость 15 м/с и выше) предварительно испытывают на прочность при скорости, превышающей на 50 % рабочую. Круги диаметром 125 мм и более подлежат балансировке. Для проверки станок должен поработать вхолостую 5 минут.
Отбелку, обезжиривание, травление и отделку готовых изделий (оксидировка, патинирование) производят в вытяжных шкафах или под вытяжными зонтами, соблюдая все меры предосторожности при работе с кислотами, щелочами и другими химическими реактивами.
Сосуды с кислотами и растворами хранят в вытяжных шкафах. При работе с растворами кислот и щелочами следует соблюдать особую осторожность. Во время приготовления хлористого цинка обильно выделяются пары соляной кислоты и одновременно повышается температура раствора, поэтому последний надо готовить под колпаком вытяжной вентиляции или вне помещения, на открытом воздухе. Посуда должна быть фарфоровой или эбонитовой, но не стеклянной, так как от нагревания она может лопнуть. Кислоту необходимо лить в воду тонкой струей; переливать из бутылки с помощью сифонов или воздушных насосов. Нельзя смачивать или обливать азотной кислотой бумагу и дерево, так как они самовозгораются.
Работая с крепкими кислотами и щелочами, надо пользоваться спецодеждой (резиновыми перчатками и сапогами, прорезиненным фартуком и защитными очками); выполняя травильные работы и обезжиривание деталей – специальными клещами и пинцетами.
Применение электрического инструмента требует строжайшего соблюдения правил безопасности. Следует помнить, что безопасным для жизни человека считается напряжение не более 36 В (в помещениях без повышенной влажности с изолирующим полом). Переменный ток частотой 50 Гц, протекая через тело человека от руки к ногам, при силе тока 0,1 А может парализовать сердце (дыхание парализуется уже при токе 0,05–0,08 А, если действие тока продолжительно); 0,02–0,025 А – мышцы. По мере действия тока на организм электрическое сопротивление тела падает, а сила тока увеличивается. Если пострадавшему вовремя не оказать помощь, может наступить смерть.
Важнейшие условия безопасной эксплуатации электроустановок следующие:
• электрооборудование, электроинструменты должны содержаться в исправном состоянии;
• провода или кабели к переносному электроинструменту и электроприборам необходимо подвешивать так, чтобы они не касались влажных поверхностей – пола, стен, горячих труб;
• все доступные для прикосновения токоведущие части электрооборудования должны быть защищены кожухами;
• переносные понижающие трансформаторы присоединяются к сети напряжением 220 В с помощью штепсельной вилки и гибкого провода длиной не более 1,5 м, заключенного в общую оплетку или шланг. Корпус трансформатора и вторичная обмотка заземляются. Заземляющий провод соединяется с клеммой трансформатора прижимными резьбовыми контактами;
• при обнаружении каких-либо неисправностей работа с электроприборами должна быть прекращена.
Перед началом работы нужно убедиться в исправности инструмента, опробовав его действие вхолостую.
Средствами личной защиты от поражения током являются: диэлектрические перчатки, галоши или боты, резиновые коврики, слесарно-монтажный инструмент с изолирующими рукоятками, защитные очки, указатель напряжения (токоискатель). Кроме того, электроприборы в мастерской должны быть заземлены. Заземлению подлежат: корпуса стационарных электродвигателей, каркасы распределительных электрощитков при номинальном напряжении в сети выше 127 В, корпуса переносного электрооборудования, работающего при напряжении свыше 36 В, независимо от частоты электрического тока. Заземляющие проводники должны быть медными, сечение – не менее 1,5 мм. Присоединение заземляющих проводов к корпусам электроприборов осуществляется болтовым соединением или сваркой.
Заземление не требуется, если электрическая часть инструмента напряжением 220 В вмонтирована в пластмассовый корпус.
Электрические станки и инструмент должны удовлетворять следующим основным требованиям: быстро включаться и отключаться от электросети; быть безопасными в работе и иметь недоступные для случайного прикосновения токоведущие части. Перед началом работы с электроприборами проверяют: затяжку винтов, крепящих узлов и деталей; состояние проводов, целостность изоляции, исправность заземления. При прекращении подачи тока во время работы станки отключают от электросети. Запрещается: производить какой-либо ремонт при включенных электроприборах, разбирать их, ползоваться для чистки электроаппаратов, имеющих нагревательные элементы, спиртом, бензином или другими быстро воспламеняющимися веществами.
Включать электродвигатель следует только перед самым началом рабочей операции и обязательно отключать во время перерыва, независимо от его продолжительности. При переносе электроинструмента с одного рабочего места на другое необходимо следить за состоянием питающего шнура: не допускать его скручивания и натяжения.
Литература и другие источники
Бродерсен Г. Г. Золотая рецептура. – СПб.: Альфа, 1992.
Васильев А. В. В помощь граверу. – М.: Легпромбытиздат, 1990.
Газарян С. С. Прекрасное своими руками. – М.: Детская литература, 1979.
Григорьев С. П. Лекально-инструментальные работы. – М.: Машиностроение, 1976.
Григорьев С. П. Профильно-шлифовальные и лекально-граверные работы. – М.: Высшая школа, 1985.
Ерлыкин Л. А. Пионер-умелец. – М.: Детская литература, 1988.
Лямин И. В. Художественная обработка металлов. – М.: Машиностроение, 1978.
Симонович И. З., Мичник С. Д. Как мастерить сувениры. – Киев: Радянська школа, 1978.
Сухарев А. В. Энциклопедия мастера-любителя. – Минск: Беларусь, 2000.
Федотов А. И., Улановский О. О. Граверное дело. – Л.: Машиностроение, 1981.
Федотов Г. Я. Звонкая песнь металла. – М.: Просвещение, 1990.
Федотов Г. Я. Чеканка, басма, насечка. – М.: Знание, 1989.
Флеров А. В. Материаловедение и технология художественной обработки металлов. – М.: Высшая школа, 1981.
Хворостов А. С. Чеканка. Инкрустация. Резьба по дереву. – М.: Просвещение, 1977.
Чесноков Л. А. В мире увлечений. – Киев: «Реклама», 1986.
Шнейдер Г. А. Основы художественной обработки металла. – Минск: Вышэйшая школа, 1986.