Практика дао Toyota. Руководство по внедрению принципов менеджмента Toyota Лайкер Джеффри
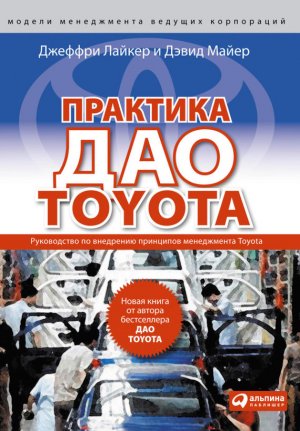
Итоговые результаты были поразительными. Диджироламо появился на заводе в качестве сэнсэя в ноябре 2000 года. Некоторое время ушло на решение вопросов стабилизации. В январе 2001 года началось развертывание бережливого производства, возглавляемое координационным комитетом в Смитвилле. К апрелю ситуация значительно улучшилась, и завод начал опережать плановые показатели, а директора других заводов Теппесо стали интересоваться, что происходит в Смитвилле. В течение первого года затраты на рабочую силу снизились на 39%, эффективность труда производственных рабочих возросла на 92%, общая производительность труда повысилась на 56%, объем запасов в денежном выражении сократился наполовину, что позволило высвободить 5 млн долл. наличными. Количество деталей с внешними дефектами снизилось с 638 до 44 на миллион, а время выполнения заказа сократилось вдвое. В 2002 году завод впервые получил от Toyota желанную награду за высокое качество продукции и услуг.
Если использовать терминологию, данную в этой главе при описании подходов к преобразованиям, завод в Смитвилле в течение первого года применял радикальную версию проектов кайдзен. Эти проекты шли беспрерывной чередой, один за другим. При этом созда-
вался поток, хотя в большинстве случаев он ограничивался отдельными ячейками. До начала года радикальных преобразований было введено несколько систем канбан, но основное внимание Диджироламо уделял стабильности и созданию ячеек. Его подход отличала ориентация на действия. Коренные преобразования осуществлялись быстро, сопротивление скептиков было сломлено как в Смитвилле, так и на других заводах Теппесо. Результаты были очевидны. Краткий обзор достижений приводится в таблице 19-2. Кроме того, успехи завода привлекли внимание генерального директора компании, который стал воспринимать внедрение бережливого производства как одно из приоритетных направлений. В то же время, если вспомнить о спирали непрерывного совершенствования (цикл, показанный на рис. 3-4, глава 3), работа, выполненная в масштабах завода, — стабилизация, создание потока, стандартизация — представляла собой лишь часть одного витка. Чтобы создать на заводе подлинную производственную систему Toyota, предстояло сделать еще очень и очень многое.
Таблица 19-2. Освоение бережливого производства в Смитвилле, результаты преобразований в течение 2001 года | |
---|---|
Общее количество персонала | -39% |
Персонал с установленным окладом | -12% |
Эффективность труда производственных рабочих | +92% |
Общая производительность труда | +56% |
Наличные запасы, в денежном выражении | -48% |
Средства, высвобожденные за счет сокращения объема запасов | $5 млндополнительно |
Площадь производственных помещений (при общей площади 200 ООО кв. футов) | Высвобождено 8% |
Количество внешних дефектов на миллион (показатель не входил в число целевых) | С 638 до 44 (-93%) |
Время выполнения заказа | 50% |
Качество и дисциплина поставок | Награда Toyota в 2002 году |
Как будет рассказано далее в этой главе, в течение следующих трех лет завод не сильно продвинулся в освоении бережливого производства, ряд созданных систем пришел в упадок. И тогда на заводе взялись за совершенствование потока создания ценности, начав с создания образцовой сборочной линии. Карта текущего состояния процесса, которая учитывала все преобразования, сделанные в ходе семинаров по кайдзен, показала, что изолированные сварочные ячейки занимаются выталкиванием продукции, что порождает огромный объем запасов. Была разработана карта будущего состояния. После внесения соответствующих изменений был сделан еще один скачок в повышении эффективности. Хотя радикальные изменения в ходе практических семинаров по кайдзен преобразили завод и позволили значительно повысить эффективность, они не обеспечили устойчивого изменения культуры и создания связанного потока.
Проекты кайдзен предполагают использование нескольких инструментов бережливого производства, предназначенных для решения конкретных задач совершенствования процесса. Многие методы решения проблем, описанные в главе 13, представляют собой подходы к совершенствованию процесса. В этой главе мы говорили, что существуют методы решения небольших, средних и крупных проблем. Проблемы среднего масштаба обычно решаются с помощью практических семинаров по кайдзен или проектов шести сигм (за пределами Toyota), как было показано на рис. 13-2. В таблицах 13-1, 13-2, 13-3 предст-йвлен широкий спектр подходов, применяемых в Toyota для совершенствования процессов. В числе этих подходов межфунк-циональные команды, кружки качества, рабочие группы, возглавляемые лидерами групп и др. Выбор методов зависит от характера проекта. Это может быть официальный проект, который передается межфункциональной команде. Работу могут поручить инженеру, который соберет специальную команду. Можно организовать семинар по кайдзен, которым займется рабочая группа при незначительной внешней поддержке.
Все эти виды работ по совершенствованию процесса в Toyota имеют ряд общих черт:
1.Как правило, задачи совершенствования конкретного участка определяются целями хосин канри (развертывания политики) для данного участка, при этом цели совершенствования на всех уровнях, вплоть до президента компании, связаны между собой.
2.Проекты по совершенствованию процессов включают этапы, описанные в главах 13-17. В окончательном виде их можно представить в виде отчета формата АЗ, которому посвящена глава 18. Независимо от того, где и в каком виде представлен такой отчет — на стене, на доске или на листе бумаги формата АЗ — он неизменно содержит одни и те же составляющие (формулировку проблемы, задачи совершенствования, рассмотренные альтернативы, избранные альтернативы, обоснование, результаты, дальнейшие действия).
3.Работа выполняется в соответствии с циклом «планируй — делай — проверяй — воздействуй».
4.Работа служит частью процесса обучения организации в целом, и важнейшие знания и опыт становятся достоянием всей организации.
При выполнении любой работы порой возникают чрезвычайно острые и болезненные проблемы, требующие безотлагательного решения, и тот, кому удается их устранить, неожиданно становится героем. Речь может идти об операции, которая представляет собой узкое место и постоянно препятствует выполнению графика. Это может быть важное оборудование, которое ломается в самый неподходящий момент. Возможно, дело в проблемах с качеством, из-за которых целые группы сотрудников вынуждены заниматься только инспекциями и переделкой.
Бережливое мышление и навыки решения проблем позволяют быстро справиться с подобными неприятностями. Иногда в качестве метода, который позволяет оперативно решить проблемы такого рода, компании используют недельные практические семинары по кайдзен. На рис. 19-2 сведены воедино сильные и слабые стороны фокуса на критичные проекты.
Характерные особенности | | |
• Безотлагательность: срочно найти выход | • Некоторые компании используют практические |
из кризиса | семинары по кайдзен |
• Один показатель | |
• Четкие задачи по совершенствованию | |
• Улучшение изолированных процессов | |
Сильные стороны•Высокая заинтересованность/активная поддержка•Ресурсы, как правило, доступны•Ориентация на действие•Готовность к быстрым и радикальным преобразованиям•Впечатляющие результаты позволяют переубедить скептиков•Решает проблемы высшего менеджмента, что позволяет заручиться его поддержкой в дальнейшемЛовушки•Отсутствие целостного видения / единой стратегии•Отсутствие системы, обеспечивающей стабильность преобразований•Риск отката назад•Нет «хозяина», если инициатива идет от функционального подразделения•Впечатляющие краткосрочные результаты становятся базой для оценки дальнейших усилий по освоению бережливого производства•Бережливое производство превращается в инструмент тушения пожаров (краткосрочная перспектива) |
Нам приходилось консультировать компании, менеджмент которых относился к бережливому производству с долей скепсиса, требуя подтверждений его эффективности. Предполагая, что бережливое производство имеет определенный потенциал и стоит опробовать его на практике, руководители выжидали, желая посмотреть, применимо ли оно к их работе и совместимо ли с их культурой. В таких случаях мы иногда спрашиваем: «Что вам особенно досаждает? Какие проблемы не дают вам спать по ночам?» Обычно ответы позволяют выявить ряд великолепных возможностей для немедленных преобразований, результаты которых заставляют руководство попросту потерять дар речи. К тому же, если вы взялись за проект, который важен для руководства, по всей вероятности, вам помогут преодолеть любые помехи, предоставят доступ к ресурсам и при необходимости окажут всемерную поддержку. Когда положение чудесным образом улучшается, менеджмент начинает верить в новый подход.
Но тот, кто идет с мечом, может от меча и погибнуть. Когда менеджеры видят, как бережливые технологии решают критичные проблемы, они начинают хотеть большего. «Давайте перейдем на этот участок, здесь тоже серьезная проблема». Или: «Нет, лучше займитесь этим проклятым станком. С тех пор как он появился, от него одни неприятности». В конечном счете все может вылиться ^бесконечную череду локальных кайдзен, как при проведении практических семинаров. Это все равно что дать наркоману высококачественный наркотик. Он согласится, но каков будет результат?
Многие проекты шести сигм весьма «критичны». От «черных поясов» требуют, чтобы любой проект обязательно давал крупную экономию. Самый простой способ добиться этого — найти критичный проект. Это наглядно показывает приведенный ниже пример сокращения продолжительности переналадки по методу шесть сигм. Задача этого проекта состояла в том, чтобы устранить узкое место в процессе литья под давлением, сократив продолжительность переналадки. Проект оказался успешным и обеспечил экономию почти в 30 тыс. долл. в год за счет сокращения затрат на рабочую силу в процессе переналадки. К сожалению, с точки зрения бережливого производства этот проект привел к увеличению размеров партии и объема запасов отформованных деталей и к росту общих затрат. Метод шести сигм при всей своей изощренности позволил снизить время переналадки всего до 1,2 часа, что весьма далеко от мирового уровня.
Это не значит, что следует раз и навсегда отказаться от акцента на критичные проекты. Во-первых, такие проекты позволяют быстро добиться ощутимых результатов и получить право заняться более продуманным формированием системы бережливого производства, ориентированным на долгосрочную перспективу, — а значит, деньги вложены в банк. Во-вторых, работать над такими проектами случается и тем, кто занимается освоением бережливого производства достаточно длительное время. Когда основные системы бережливого производства сформированы, базовый уровень стабильности обеспечен, поток создан, производство выровнено, а люди работают в командах и имеют развитые навыки решения проблем, работать над важными проблемами приходится довольно часто. Именно на такие проблемы ориентируется кайдзен. Однако подобные проекты лишь часть более органичного процесса кайдзен, и их нельзя считать движущей силой перехода к бережливому производству.
Конкретная ситуация: сокращение продолжительности переналадки по методу шесть сигм для устранения узкого места25
На заводе, который производит автокомпоненты, в том числе фары, молодая женщина-инженер готовилась к получению звания «черного пояса». В качестве проекта она выбрала важную проблему, которая существовала на заводе долгие годы. Проблема заключалась в том, что чрезмерное количество времени и ресурсов тратилось на переналадку машин для литья пластмассы под давлением. Длительная переналадка делала литье под давлением узким местом.
Были собраны подробные данные. Время переналадки при переходе на другой вид изделий в среднем составляло 3,5 часа. Переналадка каждой из 34 машин производилась трижды в неделю. Итоговые потери производственного времени составляли 357 часов в неделю. Был определен целевой показатель продолжительности переналадки — 2,5 часа. Более длительная переналадка расценивалась как дефект. Базовая задача проекта состояла в том, чтобы в половине случаев переналадка составляла менее 2,5 часа, а значит, количество дефектов должно было снизиться вдвое. Была поставлена и сверхплановая задача — добиться того, чтобы 90% переналадок выполнялось за 2,5 часа и менее.
Чтобы определить распределение вероятности для переналадок, был проанализирован значительный объем данных. Анализ позволил выявить статистически значимые различия для разных смен, машин и пресс-форм. Система измерения продолжительности переналадки и стабильности процесса также проверялась при помощи статистических методов, после чего была разработана подробная карта процесса переналадки. В работе использовались различные статистические инструменты, в том числе критерий Стьюдента, распределение Вейбулла, блочные диаграммы («ящики с усами») и график распределения вероятности. Помимо этого применялись более традиционные инструменты бережливого производства, такие как составление перечня этапов процесса и разделение операций переналадки на внешнюю и внутреннюю. Операции по внешней переналадке можно выполнять, пока машина продолжает работать, внутренняя переналадка требует ее остановки. Все эти виды деятельности были проранжированы в зависимости от времени выполнения. Была составлена причинно-следственная диаграмма «рыбий скелет», в которой были отражены факторы, снижающие эффективность переналадки, связанные с материалами, обо-
рудованием, людьми, методами, измерениями и окружающей средой. Были выявлены две важнейшие причины — ожидание тележки для переналадки и процесс прогрева пресс-формы, который длился 38% всего времени переналадки, или 1,3 часа. Кроме того, было обнаружено, что 12 из 22 операций можно выполнить, пока машина продолжает работать (внешние операции).
Инженер, которая готовилась к получению «черного пояса», использовала метод мозгового штурма для генерации идей по усовершенствованию. К этому были привлечены и работники цеха. В итоге было решено реализовать следующие идеи:
•Составлять график смены пресс-форм таким образом, чтобы данная процедура приходилась на перерыв на ланч. Это позволит прогреть пресс-формы за время ланча (затраты на оборудование для предварительного нагрева пресс-форм были сочтены неоправданными).
•Добавить дополнительную тележку.
•Вместо того чтобы поручать переналадку операторам, выделить для^этой работы специальную команду, которая сможет осуществить значительную часть операций по внешней переналадке, пока машина продолжает работать.
Результаты превзошли целевые показатели. Были собраны подробные данные, которые нанесли на графики и проанализировали. Результаты свидетельствовали о значительном улучшении ситуации, которое составило 98% — 2828 дефектов на миллион (дефект определялся как переналадка продолжительностью более 2,5 часа). Теперь переналадка в среднем занимала 1,2 часа, что значительно меньше целевого показателя в 2,5 часа. Анализ экономии, который учитывал прежде всего сокращение трудозатрат на переналадку, показал, что она составила почти 300 тыс. долл. в год. На самом деле количество переналадок в неделю превышало заложенное в смету и параллельно велась работа по стабилизации графика и сокращению числа переналадок. Возникли споры, нужно ли оценивать экономию трудовых ресурсов за счет проекта исходя из числа переналадок в текущий момент или с учетом сокращения их коли чества в будущем.
Так, значит, проект оказался успешным? Или в этом можно усомниться? Давайте подумаем, что здесь не так:
1.На работу ушло несколько месяцев. Большая часть времени была потрачена на сложный статистический анализ и подготовку презентационных материалов. Если бы за подобную работу взялся опытный специалист по бережливому производству, все это можно было бы сделать в течение одного недельного семинара по кайдзен.
2.Инженер выполнила большую часть работы в одиночку. Она почти не привлекала к участию персонал производственного участка и не старалась его заинтересовать.
3.Инженер недооценила ряд важнейших идей. Например, она отвергла идею предварительного прогрева пресс-форм, которая могла бы сыграть решающую роль. Будь агент перемен опытным производственником, внимание было бы уделено именно этой идее.
4.Целевой показатель 2,5 часа не представляет собой сложной задачи, требующей напряжения сил, и даже 1,2 часа для переналадки оборудования для литья под давлением — слишком долго для «серьезной» цели. Приемлемый плановый показатель должен составлять 15-20 минут, а сверхплановый — 5 минут. Именно столько времени занимает переналадка на заводах, освоивших бережливое производство. Пятнадцатиминутная переналадка позволила бы увеличить число переналадок, снизить.размеры партии и при этом значительно сократить трудозатраты.
5.В целом поток создания ценности стал менее бережливым. Карта потока создания ценности не составлялась. Карта, составленная постфактум, показала, что до сокращения времени переналадки отлитые детали лежали пять дней. Сокращение продолжительности переналадок, приуроченных теперь к перерыву на ланч, в сочетании с последующим уменьшением числа переналадок привело к тому, что теперь запас деталей ожидал дальнейшей обработки на несколько дней дольше, а значит, возросла продолжительность производственного цикла. Составление карты потока создания ценности могло бы навести на мысль, что цель сокращения времени переналадки — увеличить их частоту, чтобы сократить объем запасов.
Родным братом критичных проектов является метод, который можно назвать «критичные инструменты». Нередко в рамках кратких курсов по бережливому производству мы обнаруживаем, что основные цели участников сводятся к тому, чтобы изучить инструменты, которые можно применить в работе. Именно инструменты представляются людям средством, которое может принести реальную пользу. Теории хороши, но инструменты более действенны.
В таком отношении к инструментам бережливого производства нет ничего дурного. Плотники, музыканты, спортсмены, инженеры и профессионалы в любой другой области, безусловно, должны владеть орудиями своего ремесла. В этом нет никаких сомнений. Вопрос в другом: стоит ли с самого начала освоения бережливого производства ориентироваться главным образом на последовательное обучение отдельным инструментам и их поочередное внедрение в масштабах предприятия.
Такое поочередное внедрение инструментов в масштабах завода имеет массу притягательных моментов, отмеченных на рис. 19-3. Если в составе компании есть несколько предприятий, внедрение может охватывать их все. Так, можно внедрять любые инструменты бережливого производства, включая стандартизированную работу, всеобщий уход за оборудованием, 5S, быструю переналадку, ячейки, канбан, предупреждение ошибок, шесть сигм и даже рабочие группы. Этот подход представляется относительно быстрым, несложным и недорогим путем, который позволяет многому научиться, добиться общей осведомленности, разработать стандартные модели внедрения и заложить фундамент для дальнейшего формирования системы бережливого производства. В главе 4 подчеркивается важность обеспечения стабильности до создания потока. Почему бы не начать с внедрения в масштабах организации инструментов обеспечения стабильности, например всеобщего ухода за оборудованием и стандартизированной работы?^
В главе 3 мы подчеркивали, что связывание двух операций для создания потока между ними требует обеспечения базовой стабильности процесса. Мы говорили о том, что бережливое производство — это система и воспользоваться ее плодами в полной мере позволяет лишь создание потока. Это видно, когда система действует. Можно годами заниматься стабилизацией работы отдельных участков, откладывая связывание потоков и лишая себя возможности узнать, что же представляет собой подлинное бережливое производство. Если сравнить стабильность с фундаментом, получается, что вы закладываете один фундамент за другим, а до строительства дома дело так и не доходит.
Понятие дома важно еще и-потому, что его составные части взаимно упрочивают друг друга. Например, для создания потока необходимы стабильные процессы, однако поток снижает «уровень воды» и ужесточает требования к стабильности. Простои станка разрушают поток, но зачем выбиваться из сил, занимаясь изо дня в день профилактическим обслуживанием оборудования, остановка которого не влияет на следующий процесс, который может использовать запасы? Если же поломка станка перекрывает кислород следующему процессу и он останавливается, ремонт станка и профилактическое обслуживание становятся безотлагательными.
Инструменты бережливого производства, призванные способствовать устранению потерь, — не оторванное от других средство. Основной позитивный результат сокращения времени переналадки — возможность осуществлять переналадку чаще и снизить размер партии, а это, в свою очередь, способствует выравниванию пройзводства. Тем не менее мы видели много компаний, которые использовали снижение переналадки как автономный инструмент ради того, чтобы производить больше деталей и обрабатывать материал еще более крупными партиями. Это явное искажение идеи.
Теперь давайте поднимемся уровнем выше — речь пойдет об организации в целом. Представим, что вице-президент по производству решил всерьез заняться освоением бережливого производства. Узнав об этом подходе через книги или посещение других компаний в рамках бенчмаркинга, а может быть, благодаря успешным семинарам по кайдзен или выполнению критичных проектов, представитель высшего руководства заявляет: «Нам нужна настоящая система бережливого производства». Это прекрасно, именно такого отношения к бережливому производству мы добиваемся.
Мы помогали строить собственную производственную систему в нескольких компаниях. Одним из самых крупных проектов было создание производственной системы Ford в середине 1990-х годов, хотя здесь, наверное, уместнее говорить о воссоздании, поскольку изначально TPS опиралась на систему Ford. История каждого из таких проектов в общих чертах рассказана на рис. 19—4. Консультанты занимаются «созданием» системы, работая с представителями административного персонала компании, которые отвечают за внедрение бережливого производства, и привлекая к работе остальных сотрудников. Хотя в основе такой системы лежит TPS, возможны различия в терминологии, конкретном воплощении (Ford, к примеру, использует модель, включающую пять взаимосвязанных компонентов) и отдельных принципах, которые зависят от особенностей компании. Много времени уходит на выработку языка и создание имиджа. Чтобы получить согласие высшего руководства, приходится писать много документов и делать большое число презентаций.
Разнообразные параметры стандартных рабочих процедур сводятся воедино. Проводится аудит бережливого производства. Компания осознает, что существующая система показателей стимулирует модели поведения массового производства. Она инициирует систему показателей бережливо-
го производства: время выполнения заказа, качество с первого раза, общая эффективность оборудования. Моральный дух сотрудников определяется с помощью опросов. Например, в Ford был разработан комплекс важнейших показателей для каждого из пяти компонентов.
Развертывание новой производственной системы (иногда ее называют «операционной системой») представляет собой процесс образования и обучения: образование — это изучение базовых концепций бережливого производства, а обучение — освоение конкретных особенностей операционной системы. К примеру, компании Ford понадобился многодневный курс по применению новой системы показателей бережливого производства, поскольку каждый из заводов, расположенных по всему миру, должен был начать отчитываться по новым показателям. Основное внимание следует уделять единой производственной системе, стандартной для всех производственных предприятий. Так работает Toyota, и это действенный подход. Он позволяет легко обмениваться передовым опытом.
Разработка и внедрение единой операционной системы имеют массу позитивных результатов. У организации появляется индивидуальный облик, который отождествляется с ее операционной системой. Создается общий язык, который позволяет обмениваться информацией о движении вперед. Система показателей бережливого производства способствует стабилизации и формированию потока и не поощряет перепроизводство.
Каковы же недостатки подхода, обладающего столь очевидными преимуществами? Самое главное — не ставить телегу впереди лошади. Дао Toyota опирается на действия и обучение на собственном опыте. Такой подход предполагает, что подлинное понимание бережливого производства приходит лишь тогда, когда у людей появляется возможность опробовать бережливое производство как систему. Иначе оно остается просто абстрактной идеей, которую можно понять умозрительно, но не опробовать на ощупь. Усвоив ее теоретически, вы сможете лишь философствовать о ней. По существу, перед вами стоит три проблемы:
1.Как создать собственную производственную систему, не имея глубокого и полного представления о бережливом производстве?
2.Данный процесс часто связан с выработкой консенсуса, и даже если кто-то в компании хорошо знает, что такое бережливое производство, у других такие знания отсутствуют.
3.Формирование операционной системы привлекает бюрократов, которые обожают разрабатывать системы показателей, планировать обучение и представлять воображаемый облик организации в будущем, но боятся действовать.
Все это выливается в медленный и дорогостоящий процесс создания презентаций в PowerPoint с последующим обучением и обсуждениями. Но бережливое производство осваивают на практике, а не за разговорами. Как сказал наш друг, бывший вице-президент Toyota Расс Скэфейд: «PowerPoint не поможет проложить путь к бережливому производству».
Образцовый поток создания ценности
Теперь вы много знаете о том, чего не стоит делать. Но что следует делать? Как в сказке про Златовласку и трех медведей, одни подходы слишком узки и конкретны (совершенствование изолированных процессов, критичные проекты, отдельные инструменты бережливого производства), другие слишком грандиозны (создание собственной производственной системы). Мы убеждены, что создание образцового потока создания ценности — это именно то, что нужно большинству организаций. Что мы имеем в виду?х
В то время как критичные проекты и процессы представляют собой отдельные островки, разбросанные по всей организации, потоки создания ценности пронизывают структуру организации в целом, от сырья до потребителя. Бережливое производство — это философия потока создания ценности, суть которой — определить, что есть ценность для потребителя, и устранить потери в потоке создания ценности. Так почему бы не сосредоточиться на создании бережливых потоков создания ценности? Это позволит применить инструменты бережливого производства в комплексе для создания систем соответствующего уровня.
Составление карт потока создания ценности, описанное в главе 3, — основной инструмент, который позволяет представить, каким должен быть бережливый поток создания ценности. Работа начинается с составления карты текущего состояния. Потери становятся очевидны, однако при данном подходе использование кайдзен для решения проблем не допускается. Карга потока создания ценности не предназначена для планирования серии локальных кайдзен. Текущее состояние — это отправная точка для разработки концепции будущего состояния — целостной картины связанных потоков. В идеале составлением карты текущего состояния занимается межфункциональная команда руководителей, которую возглавляет менеджер потока создания ценности или иной менеджер высшего уровня. Эта же команда впоследствии вырабатывает консенсус в отношении будущего состояния бережливого потока. Концепция будущего состояния воплощается в жизнь в ходе реализации плана действий.
План действий представляет собой обычный график Гантта. При этом мы настоятельно рекомендуем сгруппировать действия в соответствии с областями материального и информационного потока26. Пример карты будущего состояния с разбивкой на петли представлен на рис. 19-5. В данном случае показаны три петли:
1.Петля, задающая ритм. Это петля, которая ближе всего к потребителю, она задает ритм всех предшествующих операций. Она же является единственной на заводе точкой составления графика. В данном случае выровненный график задается для процесса 3, а затем за счет обработки по принципу «первым вошел -— первым вышел» в неизменной последовательности передается дальше до супермаркета готовых изделий. Ритм процесса 3 определяет ритм вытягивания промежуточных изделий из супермаркета, который в свою очередь связан вытягиванием с процессом 1, который вытягивает материал у поставщика.
2.Промежуточная петля процесса. Здесь происходит обработка поставляемых материалов и пополнение супермаркета с запасом продукции для потребителя — петли, задающей ритм.
3.Петля поставщика. Включает поставщика сырьевых материалов и петлю пополнения, которая поддерживает запас поставляемых деталей в супермаркете.
Заметьте, что каждая из этих петель представляет собой целостный замкнутый контур материального и информационного потоков. Материальный поток движется к потребителю, а информационный поток — в обратном направлении, инициируя выполнение очередного заказа, поступающего непосредственно от потребителя. Можно заниматься оптимизацией каждой из этих петель автономно, и в случае незначительных помех в работе одной петли, буферный запас в супермаркете не нарушит работу соседней петли. Для стабилизации процесса необходима серия целенаправленных кайдзен-прорывов локального характера.
Работа с потоком создания ценности не заменяет проекты кайдзен, без которых не обойтись при стабилизации отдельных процессов и устранении вариации. Для решения особо сложных проблем, связанных с вариацией процесса, может оказаться полезным применение метода шести сигм. Не исключает такая работа и применения инструментов бережливого производ-
Рис. 19-5. Базовая карта будущего состояния с петлями и кайдзен-прорывами
ства, поскольку они необходимы для внедрения отдельных составляющих будущего состояния потока создания ценности — ячеек, канбан и т.д. К тому же ориентация на поток создания ценности позволяет применять эти инструменты и методы совершенствования процесса в более широком плане, рассматривая материальный и информационный поток как систему. Такой подход влияет и на последовательность внедрения. Нередко просматривается склонность внедрять инструменты по одному, например сокращать продолжительность переналадки в масштабах всего завода. Занимаясь потоком создания ценности, вы поочередно работаете над петлями, связанными с помощью системы вытягивания, и делаете все необходимое, чтобы обеспечить стабильность, поток, Стандартизацию и пошаговое выравнивание в каждой отдельной петле. Может оказаться, что у вас достаточно ресурсов, чтобы работать над несколькими петлями параллельно, в иных случаях вы можете заниматься ими последовательно.
В этом подходе есть место и критичным проектам. К примеру, может оказаться, что процесс 1 представляет собой узкое место и систематически приводит к остановке других операций, вызывая задержку поставок. Непременно начните с процесса 1 и промежуточной петли процесса. Нет закона, который гласит, что нужно начинать с петли, задающей ритм, но при прочих равных условиях логично избрать эту петлю отправной точкой. Таким образом, начинайте с ближайшего к потребителю участка и обеспечьте выровненное вытягивание в процессе, задающем ритм, что
позволит обеспечить понимание времени такта в данной точке потока создания ценности.
Если мы вернемся к истории с Теппесо и посмотрим, что произошло в компании три года спустя, то увидим, что в Смитвилле стали применять именно этот подход, занимаясь потоками создания ценности. Здесь начали с составления карт потока создания ценности и создания образцовой линии. На заводе обнаружили, что результаты первой попытки — внедрить бережливое производство с помощью практических семинаров по кайдзен — были очень далеки от идеала бережливого производства. Новая волна — совершенствование потоков создания ценности — принесла дополнительные результаты, не менее впечатляющие, чем первый этап радикальных преобразований с помощью семинаров по кайдзен.
Конкретная ситуация:
Теппесо, Смитвилл. Потоки создания ценности, 2-й этап
После года серьезных преобразований (кайкаку) путем проведения практических семинаров по кайдзен в 2000 году, завод мало занимался совершенствованием и фактически вернулся почти к тому же состоянию, в каком пребывал до трансформации. 5S и прочие принципы бережливого производства соблюдались далеко не всегда, порядка на заводе становилось все меньше. Всерьез за исправление ситуации здесь взялись в 2003-2004 годах, когда на заводе стали применять метод оптимизации потоков создания ценности, уделяя основное внимание созданию единого материального и информационного потока в ходе связывания отдельных операций. Новый подход был нацелен на создание «образцовых потоков создания ценности». В качестве пилотного проекта было избрано семейство продуктов, поставляемых на Toyota. Теппесо привлекла к этой работе компанию Рика Харриса, взяв на вооружение модель супермаркета для закупаемых деталей и систему «буксировочной лебедки», описанную в книге «Создание материального потока» (Making Material Flow)*.
Когда в Смитвилле составили карту текущего состояния, то обнаружили, что, несмотря на радикальные преобразования, на предприятии существуют отдельные островки бережливого производства, соединенные системами выталкивания. Карта текущего состояния потока создания ценности показана на рис. 19-7. Обратите внимание на стрелки, которыми обозначены зоны выталкивания. По сути, поступающие запасы материала постоянно выталкиваются: с одного процесса обработки на другой, потом на операцию сборки (сварка сборочных узлов) и, наконец, на окончательную сборку. Последняя
представляет собой сварку глушителя (поступает от внешнего поставщика), выхлопной трубы и прочих деталей в единую выхлопную систему. Общее время выполнения заказа, от поступления стали до отгрузки готовых выхлопных систем, составляло 17 дней.
Концепция будущего состояния, теперь уже реализованная, показана на рис. 19-8. Мы не будем комментировать данную карту подробно и обратим ваше внимание лишь на ряд ключевых моментов:
1.Два этапа сборки (основная и вспомогательная, рис. 19-7) теперь выполняются в единой сборочной ячейке (обеспечить поток, где это возможно).
2.Операции, связанные с изготовлением компонентов (гибка труб, штамповка) и закупкой деталей со стороны, связаны системой вытягивания с применением супермаркетов и канбан (обеспечить вытягивание, где это необходимо).
3.Один из компонентов, который раньше производился партиями (резонатор), теперь изготавливается на станке, предназначенном исключительно для деталей для Toyota, с небольшим буферным запасом деталей, которые поступают на сборку по принципу ФИФО. Объем запасов не превышает трех коробок, тогда как при прежней системе детали дожидались обработки 1,5 дня.
4.Ежедневные заказы вводятся в одной точке — на сборке, при этом ввод заказов осуществляется по выровненному графику, а все остальные операции связаны со сборкой системой вытягивания. Система MRP используется исключительно для закупаемых деталей с длительным временем выполнения заказа.
Супермаркет закупаемых деталей сделан по образцу системы Toyota. Предусмотрен один центральный супермаркет и «водяной паук», который, перемещаясь по стандартному маршруту, ежечасно доставляет детали из супермаркета на различные операции. Работница, на которую возложены эти обязанности, собирает карточки канбан и управляет системой канбан на всем заводе. Каждый час она повторяет свой маршрут. В процедуре стандартизированной работы четко прописано, где она будет находиться каждую минуту, подобно следующему по четкому графику автобусу или поезду. После внедрения такой системы число рабочих, доставляющих детали, сократилось, хотя подача материала теперь осуществляется не ежедневно, как раньше, а ежечасно.
Результаты, представленные на рис. 19-9, впечатляют. Процесс внедрения занял девять месяцев, при этом запасы закупаемых деталей сократились вдвое, освободилась четверть полезной площади производственных помещений, количество деталей на одного рабочего выросло почти вдвое, а продолжительность сверхурочной работы сократилась с 252 до 10 часов в неделю. Следует иметь в виду, что таких результатов за такие короткие сроки удалось достичь, поскольку завод уже имел большой потенциал в плане бережливого производства. Это позволило Теппесо работать над несколькими потоками создания цен-
ности одновременно. Работая над данным потоком создания ценности, Теппесо применила тот же подход к другим важнейшим потокам создания ценности и в основном завершила их преобразование спустя шесть месяцев после создания первой образцовой линии. Такие изменения системного уровня, как правило, более устойчивы, поскольку влекут за собой более глубокую трансформацию культуры.
Есть ли у данного подхода какие-то недостатки или он обещает нирвану? Разумеется, ни один подход не совершенен. Как видно на рис. 19-6, работа над образцовым потоком создания ценности требует больших затрат времени, формирования межфункциональной команды, которая возглавит процесс, и активного участия сотрудников всех уровней. Пока происходит создание образцовой линии, менеджеры и сотрудники наблюдают, как она совершенствуется. Нам приходилось видеть и неэффективное применение этого метода, когда команда была озабочена не тем, что делать, а тем, как создавать карты, красиво оформленные и точные. Жаль, что они годны разве что на обои. На некоторых заводах принимают решение составить карты для каждого семейства продуктов. Результат — бесконечные совещания, куча бумаги... и никаких действий. Мы твердо верим в принцип: «не браться за составление карты раньше времени». Приступать к составлению карты следует лишь тогда, когда вы знаете, что сразу приметесь за внедрение.
Перечисленные подходы не исключают друг друга. Самое важное — продумать и спланировать процесс развертывания инструментов бережливого производства так, чтобы он обеспечил создание бережливых систем, а в конечном итоге привел к созданию бережливых потоков создания ценности. В Теппесо разработали план построения будущего состояния потока создания ценности. Здесь выбрали семейство продуктов, составили карту процесса, а затем внедрили модель потока создания ценности. Однако вскоре после запуска образцового потока создания ценности на одной из линий началось совершенствование других процессов в масштабах всего завода. На проблемных участках могут применяться, к примеру, практические семинары по кайдзен, реализовываться критичные проекты, а в масштабах завода могут внедряться отдельные инструменты, такие как 5S или всеобщий уход за оборудованием (рис. 19-10).
Преимущество параллельного использования этих подходов в том, что оно позволяет воспользоваться их сильными сторонами и смягчить недостатки. Запустив пилотный проект, вы получите возможность пойти, увидеть происходящее своими глазами и опробовать TPS на практике во всем объеме. К тому же это позволит привлечь к работе с базовыми инструментами бережливого производства более широкий круг лиц. Решение актуальных
проблем поможет заручиться поддержкой менеджмента и получить доступ к необходимым ресурсам. Недостаток подобного образа действий — реальная опасность распыления ресурсов, из-за которого ни одно начинание не будет завершено своевременно и должным образом. Помня об этом, будьте готовы приостановить ряд проектов, как только увидите, что качество падает или возникают задержки. В данном случае следует приостановить внедрение в масштабах завода и сконцентрироваться на образцовой линии.
Заметьте, что на всех уровнях внедрения на рис. 19-10 показан цикл «планируй — делай — проверяй — воздействуй». Внедрение бережливого производства не сводится к окупаемости инвестиций. Нередко компании вкладывают значительные средства в обучение и консалтинг, а высший менеджмент требует составить ненавистный бизнес-кейс. Когда окупится внедрение? Если вам нужны цифры для пресловутого бизнес-кейса, вы можете рассчитывать на признание, лишь отчитавшись о реальном сокращении издержек. ак правило, это означает сокращение штатов. Может быть, вам также удастся заработать 10 центов на доллар, добившись экономии за счет сокращения объема запасов. Команда непрерывного совершенствования отныне все время находится под прицелом, о чем и сообщает консультантам: «Мы должны добиться окупаемости в течение года».
Хороший консультант по бережливому производству может обеспечить такую окупаемость. Он может сократить численность персонала, уменьшить объем запасов, и показатели пойдут вверх. Но чем это закончится? С точ-
ки зрения цикла PDCA такой образ действий представляет многократное повторение этапов «планируй — делай», «планируй — делай», причем работа ведется такими темпами, что времени перевести дыхание и проверить хоть что-то, кроме сокращения издержек, просто не остается.
Мы говорили о множестве стратегий совершенствования в рамках бережливого производства на разных уровнях. В модели на рис. 19-11 комплекс этих стратегий структурирован с учетом двух факторов: ориентирована ли стратегия на уровень потока создания ценности или на уровень изолированных процессов? Нацелена ли стратегия на применение технических инструментов, позволяющих получить краткосрочные результаты, или наряду с этим предполагает'развитие сотрудников компании с учетом долгосрочной перспективы?
Мы перечислили сильные и слабые стороны совершенствования отдельных процессов и описали работу с потоком создания ценности, в основе которой лежит составление карт потока создания ценности и создание образцового потока на одной из линий. Оба подхода часто используются компаниями главным образом для достижения краткосрочных финансовых результатов. При этом упускается куда более важная возможность обучать и развивать людей и организацию, что позволит им продолжать совершенствование в дальнейшем, т. е. умножать позитивные результаты. Многие компании, располагая программами вовлечения персонала, занимаются исключительно совершенствованием отдельных процессов и развитием и обучением персонала. Люди учатся работать в команде и применять инструменты решения задач, но при этом не понимают более широких концепций совершенствования потока создания ценности. Как мы видели, Toyota занимается совершенствованием по каждому из четырех названных направлений, при этом по сравнению с большинством прочих компаний она уделяет значительно больше внимания созданию обучающейся бережливой организации, а это предполагает сочетание оптимизации потока создания ценности с развитием людей. А как определяется позиция вашей компании?
Компания Denso — крупнейший поставщик комплектующих для Toyota — росла и строила бережливое производство вместе с самой Toyota. Однако ее завод в городе Бэттл-Крик, штат Мичиган, значительно отставал от Toyota в освоении TPS. В прошлом здесь внедрялись отдельные инструменты, однако бережливое производство не работало как система. Ниже мы расскажем о том, как разрабатывалась собственная производственная система «Эффективное предприятие» и как в непрерывное совершенствование вовлекались все сотрудники. Для внедрения этой системы использовались реальные проекты и образцовые потоки создания ценности. В каждой из основных ассортиментных групп было выбрано семейство продуктов, где началось формирование бережливых потоков создания ценности — от потребителя до сырья. Остальные продуктовые семейства были подключены только после того, как внедрение было завершено на первой, «образцовой» линии. Даже заводу, который считается эталоном бережливого производства, следует время от времени критически переоценивать свое состояние и поднимать бережливое производство на новый уровень. При этом рекомендуется использовать подход образцовых потоков создания ценности.
Конкретная ситуация: компания Denso — работа над потоками создания ценности
В 2004 году объем продаж Denso составил почти 24,2 млрд долл., а в ее штате работало 95 ООО сотрудников. Когда-то Nippon Denso (Japan Electronics) была подразделением Toyota, позднее она обрела независимость. Но Toyota до сих пор владеет значительной частью Denso (в настоящее время ей принадлежит 23%). Параллельно развитию производственной системы Toyota развивалась и Denso, и когда Toyota начала производить автомобили на территории США, Denso в 1984 году построила завод (DMMI) в городе Бэттл-Крик, штат Мичиган, чтобы производить кондиционеры и теплообменные устройства (радиаторы/конденсаторы) для автомобилей. В условиях острой конкуренции среди производителей автокомпонентов объем продаж DMMI рос из года в год, во многом благодаря Toyota, а также DaimlerChrysler и General Motors. Годовой объем продаж в период с 2002 по 2004 год увеличился с 1 млрд долл. до 1,25 млрд долл., при этом Denso славилась исключительным уровнем технологии, высоким качеством и почти безупречной дисциплиной поставок, благодаря чему она возглавляла список самых эффективных компаний. Получать прибыль на рынке автокомпонентов непросто, однако DMMI из года в год поддерживала хорошую рентабельность. Казалось бы, будучи прекрасным примером бережливого производства, компания Denso знает о нем почти все. Если бы на Denso не представляли потенциал непрерывного совершенствования, они могли бы сказать: «Мы добились успеха», но, к счастью, там думают иначе.
В 2003 году, в DMMI, Бэттл-Крик, была начата программа «Эффективное предприятие». DMMI — компания с давними традициями TPS. От новой программы можно было ждать усиления автоматизации, повышения роли информационных технологий и развития новых концепций бережливого производства. Тем не менее «Эффективное предприятие» — это всего лишь модифицированная на DMMI версия TPS. Символ «Эффективного предприятия», изображенный на рис. 19-12, внешне напоминает начертание египетского иероглифа, который мог бы быть обнаружен на стенах одной из великих пирамид. Однако, несмотря на столь интригующую символику, концепция «Эффективное предприятие» не имеет ничего общего с передовой производственной технологией. «Эффективное предприятие» — это прежде всего люди и философия. Другое название этого симола — «Треугольник Такахаси», которое дано в честь председателя совета директоров Denso, который ушел на пенсию. Данную концепцию энергично проводит в жизнь президент DMMI Акио (Алекс) Сикамура, подлинный приверженец TPS. Понятно, что, когда предприятие возглавляет убежденный сторонник данного подхода, это становится важнейшим стимулом коренных преобразований.
Концепция «Эффективное предприятие» была названа «деятельностью», а не «программой». О какой работе шла речь? В прошлом компания реализовала немало прекрасных технических программ, нацеленных на повышение эффективности, включая кайдзен под руководством инженерно-технического персонала в 1996 году, всеобщую организацию производства в 1996-1997 годах и концепции TPS в 1998 году (малые партии, канбан). В период с 2000 по 2003 год в DMMI осознали необходимость более активного участия в процессе членов команд, и в результате была разработана программа, названная WOW (wipe out waste) — «Избавимся от потерь». Каждая из названных программ заметно повлияла на эффективность производства. И все же в компании понимали, что DMMI ощутимо отстает от заводов Toyota. Поэтому в 2002 году была развернута инициатива «Эффективное предприятие». Ее цели были определены следующим образом:
1.Усилить ориентацию на кайдзен в мышлении всех сотрудников.
2.Определить общую цель (видение).
3.Снизить затраты за счет устранения потерь на протяжении всего
потока создания ценности.
Концепция эффективного предприятия была нацелена прежде всего на вовлечение сотрудников в работу по сокращению потерь на протяжении всего потока создания продукта, от поставщика до потребителя. В компании понимали, что, для того чтобы вывести TPS на новый уровень, понадобится привлечь экспертов по TPS. Возглавить отдел организации производства было поручено Андрису Сталтмани-су, которому предстояло вывести это подразделение на новый уровень TPS. За плечами Андриса было 18 лет работы в области организации и технологий производства, он был одним из тех, кто работал в Бэттл-Крике со дня основания завода. Его сэнсэем стал Яманоти Ютака,
вице-президент по планированию и управлению производством из Denso в Японии. Вместе с тем было понятно, что ключевой фактор успеха — это наличие хозяина на производстве. От Джо Стича (директора производства), который также был знатоком TPS, требовалось поддерживать работу изнутри.
В ходе развертывания проекта на предприятии было выделено три целевых участка: ОВКВ (обогрев, вентиляция и кондиционирование воздуха), конденсаторы и радиаторы. На каждом участке было выбрано семейство продуктов для создания образцовой линии — сюда можно было прийти, увидеть все своими глазами и заняться совершенствованием. Сначала работу на образцовых участках координировал отдел организации производства, затем ответственность постепенно передавалась производственникам. При помощи кайдзен осуществлялось базовое совершенствование процессов, выполнялась оптимизация управления на цеховом уровне и совершенствование потока создания ценности. В числе прочих использовались такие инструменты, как визуальный контроль, стандартизированная работа, работа малыми партиями, частая доставка и доска хейдзунка (выравнивание объема работ с учетом ассортимента продукции).
По мнению Брайена Денброка, главы одного из подразделений отдела организации производства, который отвечал за внедрение модели на заводе, обеспечение хейдзунка в масштабах всего завода было чрезвычайно сложной задачей из-за широкого ассортимента продукции и разнообразия потребителей. Ориентируясь на поставленную цель — стать компанией мирового уровня, завод ОВКВ создал образцовую линию по производству готовой продукции. Эта линия стала наглядным примером для всех остальных.
Готовая продукция отгружается потребителю со склада. На большом стеллаже хранится трехчасовой запас заказов. Когда на стеллаж кладут детали, это регистрируется посредством канбан и карточка возвращается на табло хейдзунка. Канбан укладываются таким образом, чтобы обеспечить выравнивание производства, питч составляет 10 минут. Таким образом каждые 10 минут рабочий подает производству сигнал (канбан) о выполнении заказа на определенную продукцию для пополнения запаса изделий, фактически приобретенных потребителем и изъятых со склада. Канбан хранения обмениваются на канбан производства, которые определяют ход работы линии в течение очередных 10 минут. Так задается темп потока единичных изделий на сборочной линии’27'.
Когда такой процесс хейдзунка применяется в масштабах всего завода (с помощью досок визуального менеджмента, известных как табло хейд-зунка), это позволяет из одной точки увидеть состояние всего процесса. Согласно философии Toyota для этой цели целесообразно использовать рабочего, которого иногда называют «водяным пауком», поскольку, перемещаясь по заданному маршруту, он видит материальный и информационный поток в целом. Выравнивание объема работ в масштабах завода дает возможность стандартизировать все виды работ с учетом 10-минутного интервала. Это упрощает все операции и позволяет с первого взгляда определить, соблюдается ли стандарт. Когда такие условия созданы, наблюдательный и вдумчивый человек может оценить состояние всего завода.
С помощью табло хейдзунка осуществляется выравнивание производства широкого ассортимента деталей. Для этого необходимо, чтобы продолжительность переналадки (смена зажимных приспособлений на сборочной линии) не превышала времени такта (время такта равно доступному рабочему времени, деленному на потребительский спрос). Переналадка сборочной линии, которая работает две смены, выполняется от 90 до 125 раз в день. Время такта соблюдается за счет заданных интервалов подачи деталей конвейерной линией и перераспределения элементов работы между членами команды на сборочной линии. При этом имеет место двустороннее движение канбан: к промежуточному складу изделий (канбан отбора), а затем к производственному процессу (канбан производства) для вытягивания деталей в зону окончательной сборки. Канбан поступают на промежуточный склад 88 раз в день. Столь высокая частота отбора и поставки требует тонкой настройки процесса, который отличает высокая стабильность. Даже небольшие проблемы нарушают ход производства и выявляются незамедлительно. Чтобы подобные помехи не мешали эффективной работе компании, она должна быть готова к оперативному устранению проблем и последующему принятию долгосрочных контрмер. Вспомнив рис. 3-4 (глава 3), где представлена спираль непрерывного совершенствования, можно сказать, что завод прошел уже несколько витков этой спирали, занимаясь стабилизацией, созданием потока, стандартизацией и выравниванием производства.
Результаты работы образцовых линий впечатляли. Затраты на производство значительно снизились, а качество и дисциплина поставок поднялись на весьма достойный уровень. Но самое главное — у DMMI появилась возможность использовать свои достижения на остальных сборочных линиях. В этой работе непосредственно участвуют члены команд DMMI, и ориентация их мышления на кайдзен растет. Это благоприятствует формированию новой культуры, которая позволяет реализовать потенциал сотрудников в области совершенствования.
Внедрение бережливого производства — это всегда приобретение знаний, даже если пройден уже значительный путь. Любой опыт — это возможность учиться и расти. Но нужно обязательно найти время, чтобы проанализировать то, что уже сделано, и подумать, как добиться новых улучшений. Призывая к непрерывному обучению, мы не раз слышали в ответ что-нибудь вроде: «Но мы занимаемся бизнесом, а значит, должны делать деньги. Такова жизнь».
Toyota делает огромные деньги. Но она трудилась десятки лет, чтобы начать получать прибыль от инвестиций в обучение. Когда мы говорим о необходимости таких инвестиций, для нас совершенно очевидно, что вокруг полным-полно потерь и что компания получит выгоду, если повысит качество продукции, сократит время выполнения заказов, станет более гибкой и восприимчивой к изменениям и повысит производительность. Заблаговременные инвестиции в обучение помогут умножить экономию в долгосрочной перспективе. Вспомните четырехкомпонентную модель, в основе которой лежит принцип: «учитывай долгосрочную перспективу, даже если это наносит ущерб краткосрочным финансовым целям». Организации, которые видят в бережливом производстве программу краткосрочного снижения затрат, никогда не добьются того, чего могли бы. Они никогда не станут высокоэффективными организациями.
Многим компаниям не терпится побыстрее внедрить бережливое производство в собственной организации и на уровне расширенного предприятия. Несложный анализ показывает, что большая часть затрат, как правило, приходится на закупаемые детали. Также известно, что начальные этапы процесса, например разработка продукции, оказывают на производство эффект мультипликатора, который в значительной мере превосходит инвестиции в разработку. Так почему же не начать именно с этих областей? Наш опыт говорит о том, что, если преждевременно внедрять бережливое производство на уровне предприятия или расширенного предприятия, вреда будет больше, чем пользы, по ряду причин:
1. Бережливое производство проще понять на процессах материального характера. Не забывайте, что ранние этапы освоения бережливого производства в значительной мере представляют собой обучение. К тому же, как это ни прискорбно, многое решает политика, — чтобы убедить тех, кто принимает решения и распоряжается финансовыми ресурсами, нужны заметные, измеримые результаты. Проще всего добиться этого при помощи производственных процессов, которые осуществляются изо дня в день. В организации, которая занимается исключительно оказанием услуг, для этой цели больше всего подходят самые часто повторяющиеся операции, например ввод заказов или выполнение анализов (в больнице).
2.Опасность превысить возможности имеющихся ресурсов. По всей вероятности, менеджмент выделит на освоение бережливого производства ограниченное количество людей. Обратите особое внимание на самых способных и обучаемых. Даже если решено создать особое подразделение в офисе, которое будет заниматься бережливым производством, лучше, чтобы его сотрудники для начала провели некоторое время «на передовой», занимаясь выполнением работы, добавляющей ценность. Так они лучше усвоят, что такое бережливое производство, и перенесут значительную часть этого опыта в офис.
3.При оказании услуг бережливые процессы должны поддерживать важнейшие операции по добавлению ценности. Можно повысить эффективность подразделения, выполняющего вспомогательные функции, сделав его более бережливым, и все же любой проект по бережливому производству должен начинаться с определения цели бизнеса: кто ваш потребитель? Каковы его нужды? Если потребителем процесса оказания услуг является процесс физического видоизменения материала, сначала нужно пойти и посмотреть, каков будет этот процесс после трансформации, чтобы понять, как обеспечить его поддержку. Когда Гленну Умингеру поручили разработать систему оперативного учета для завода Toyota в Джорджтауне, он провел целый год на производстве, выполняя проекты по TPS, что радикально изменило его взгляды. В результате он разработал систему управленческого учета, ориентированную на TPS. По сравнению с системой, которую он использовал на прежнем месте работы, новая была менее громоздкой и более бережливой.
4.Опасность превратить бережливое производство в модное увлечение. Нередко лучшим консультантам и опытным специалистам по бережливому производству поручают работать на производстве или с важнейшими процессами добавления ценности в организации сферы услуг. При этом подразделения, которые выполняют вспомогательные функции, остаются брошенными на произвол судьбы, и их подготовка сводится к краткому учебному курсу. Работа группы, которая занимается непрерывным совершенствованием, носит поверхностный характер, и бережливое производство превращается в «программу месяца». Помните, сделать правильно важнее, чем сделать быстро.
5.Попытки заставить поставщиков освоить бережливое производство, прежде чем это сделали вы сами, лицемерны и опасны. Какое вы имеете право учить бережливому производству своих поставщиков, если не освоили его сами? Это право нужно заслужить. Кроме того, бережливая цепочка поставок предполагает наличие комплекса
иерархически взаимосвязанных компонентов, и если вы возьметесь за развитие и обучение поставщиков, не создав доверия и взаимопонимания, поставщики будут рассматривать такое обучение как компенсацию за давление на них по поводу цены.
Прежде всего мы призываем вас к терпению. Представьте себе буддийского монаха, который наставляет юного ученика, или тренера по карате, или, если уж на то пошло, любого хорошего преподавателя, который помогает своему подопечному осваивать сложные навыки, будь то спорт или игра на музыкальном инструменте. Едва ли ученик сразу начнет с исполнения сложных партий или отправится прямиком на игровое поле. Сначала нужно подготовиться, многократно выполняя не слишком увлекательные упражнения. Нужно научиться владеть своим телом и концентрироваться. Один из лучших тренеров по гольфу, которого обучал один из самых блестящих гольфистов в мире, сказал, что первые три месяца он учился гольфу, ни разу не ударив по мячу. Вспомните про круг Тайити Оно. Постойте в кругу и понаблюдайте. Потребность в терпении и дисциплине распространяется и на процесс решения задач. Не бросайтесь сломя голову внедрять найденные решения. Не спеша определите подлинную сущность причины, а потом с помощью метода «пяти почему» найдите коренную причину. Не торопясь, шаг за шагом проводите для каждого работника производственный инструктаж, прежде чем поручить ему выполнение текущей работы. Не жалейте времени на проверки, аудиты и разработку контрмер, ведь это позволит учиться и совершенствоваться. Занимаясь крупными, заметными усовершенствованиями, не отказывайтесь от массы небольших, менее значительных улучшений. Такое терпение предполагает проницательность и дальновидность и требует понимания цели на философском уровне. И это самая трудная часть бережливого производства. Но в долгосрочной перспективе она окупится сторицей.
Вопросы для размышлений
Большинство читателей этой книги наверняка работают в организациях, которые уже успели приобрести некоторый опыт в области бережливого производства. В то же время многим еще предстоит большая работа, на которую уйдут годы. Тем, кто уже знаком с бережливым производством, мы предлагаем осмыслить свой предшествующий опыт и составить план дальнейшей работы над уровнем «процесс» четырехкомпонентной модели. Новичкам предоставляется возможность разработать план. Вам придется поразмыслить над ним вместе с командой представителей вашей организации, которые
уполномочены принимать решения и могут на законном основании определить направленность инициативы по освоению бережливого производства.
1.Составьте список проведенных мероприятий по совершенствованию процесса, которые были нацелены на освоение бережливого производства.
2.Распределите основные мероприятия в соответствии с категориями, представленными в четырех ячейках матрицы на рис. 19-11. В какую категорию попала большая часть работ?
3.Теперь подумайте, что делать дальше. Какое направление следует избрать в соответствии с моделями на рис. 19-10 и 19-11? К примеру, если до сих пор вы занимались в основном отдельными инструментами или критичными проектами, может быть, настало время взяться за образцовую линию потока создания ценности. Если модель на рис. 19-11 говорит о том, что у вас накопился значительный опыт в освоении инструментов (левая часть таблицы), возможно, пришла пора взяться за развитие людей. Опыт компании Denso учит, что, занимаясь работой с людьми, нужно привлекать их к участию в конкретных проектах по оптимизации отдельных процессов или всего потока создания ценности.
4.Разработайте высокоуровневый план работы. Можете воспользоваться простой концептуальной схемой на рис. 19-10, наметив приблизительные даты.
РУКОВОДСТВО ПЕРЕМЕНАМИ
Построение бережливого производства — это процесс, затрагивающий корпоративные принципы («политику»). Всем известно, что политика — это плохо. Политика царствует в организациях, в которых отсутствует рациональное и справедливое управление. В нормальной, благополучной компании правит разум и здравый смысл, и все стремятся к достижению единой цели.
Мы говорили о Toyota как об утопии, где все работают на общие цели, которые определяет потребитель. Выходит, если вы хотите учиться у Toyota, сначала нужно добиться, чтобы все работали на одни и те же цели? Нет, нет и нет! Или как резко выразился один японский сэнсэй: «Чушь! Чушь! Чушь!» (Именно так, к ужасу американцев, перевела его слова юная, миниатюрная женщина.)
Что мы понимаем под процессом формирования корпоративных принципов? В любой реальной организации, даже в Toyota, работают разные люди, и у них свои интересы и планы. Активные сторонники перемен вырабатывают собственное видение. Если это видение согласуется с интересами людей, они его поддерживают, если нет — отвергают. Степень поддержки и противодействия варьируется в зависимости от множества факторов: в какой мере концепция идет на пользу или в ущерб чьим-то интересам, насколько сильна заинтересованность, до какой степени культура организации способствует ориентации на единые цели. Процесс формирования корпоративных принципов связан с тем, как проявит себя данная совокупность разных интересов с течением времени. Тем, кто руководит преобразованиями, хотелось бы расставить все по местам, как фигуры на шахматной доске. Но в жизни постоянно приходится идти на компромиссы и вести корабль через мутные воды интересов других людей. Стоит переусердствовать и нарушить интересы большой группы людей, и вы получаете организованное сопротивление, которое может в два счета остановить процесс преобразований.
Политика — это власть, а власть — это способность добиваться своего, даже если приходится идти вразрез с чьими-то желаниями. Представьте, что люди хранят власть в горшочках: если твой горшочек опустел, тебе конец. Конечно, такая аналогия довольно примитивна, но властью действительно следует пользоваться очень экономно. Мудрый лидер знает, когда уступить, когда уговорить, когда попросить об одолжении, а когда вспомнить об официальной иерархии полномочий и отдать приказ. Некоторые лидеры интуитивно чувствуют, как пользоваться властью, другие беспрестанно совершают ошибки.
Лидерство связано со властью. Лидер становится лидером лишь тогда, когда он способен повести за собой других. Для того чтобы побудить людей идти туда, куда они двигались бы и без вас, не нужно быть лидером. Задача лидера в том, чтобы повести людей туда, куда они, скорее всего, не пошли бы сами. Лидер должен чувствовать направление. Иногда мы называем это чувство видением. Лидер должен уметь донести свое видение до других людей, сделать их своими сторонниками и побудить активно содействовать достижению цели. Если это удается, в особенности в тех случаях, когда люди не стали бы заниматься этим самостоятельно, можно говорить о власти.
Отец социологии Макс Вебер28 описал несколько типов власти:
1.Рационально-законная власть. Иначе — официальная власть. Поскольку в иерархии организации вы — босс, вы можете отдавать приказы, другие же должны повиноваться. Занимаемая должность дает вам законное право приказывать. Часто именно так понимается бюрократическая власть.
2.Власть, основанная на принуждении. Чтобы добиться подчинения, лидер может угрожать.
3.Власть, основанная на вознаграждении. У вас есть определенное вознаграждение, которое вы предоставляете в обмен на желаемое поведение. Вознаграждение может быть материальным, например денежным, или носить нематериальный характер, и представлять собой, скажем, похвалу. Оно не включено в исходную типологию Вебера, но является оборотной стороной власти, основанной на принуждении: вместо угроз используется обещание, что желательное поведение или результаты будут определенным образом вознаграждены.
4.Харизматическая власть. Если вы обладаете харизмой, люди сами захотят следовать за вами. Это своего рода животный магнетизм, сила, которая заставляет людей подчиняться лидеру.
5.Традиционная власть. Принятый образ действий. Если в день Сэди Хокинс29 девушка пригласит парня на танец, ему придется согласиться, поскольку этот праздник — часть культурного наследия, традиций и социальных норм.
Талантливый лидер знает, как использовать все перечисленные типы власти. Как правило, лидером, а не просто администратором считают того, кто хоть немного наделен харизмой. Любой менеджер-бюрократ полагается на первые три типа власти. Дайте ему соответствующие полномочия и возможность использовать вознаграждения и наказания, и он добьется многого. Но в распоряжении подлинного лидера есть масса инструментов, и он знает, как и когда их использовать. Когда следует напомнить, какую должность я занимаю? Когда использовать иерархию, чтобы пригрозить наказанием? Когда воспользоваться личным магнетизмом, чтобы повлиять на людей, общаясь с ними один на один? Когда произнести перед членами своей команды речь, которая заставит их плакать? Когда принять участие в официальной церемонии и использовать силу традиции? Одаренный лидер со временем научится эффективно использовать все типы власти. Бездарный лидер подобен ребенку с заряженным ружьем, который палит куда попало.
У нас было достаточно возможностей увидеть, как крупные международные компании внедряют бережливое производство в своих корпорациях, В их числе Ford, General Motors, Delphi, PPG, Boeing, Northhup Grumman, ВВС и BMC CUT A, United Technologies и многие другие. Во всех случаях ясно просматривается тенденция: некоторые производственные предприятия в деле бережливого производства значительно опережают другие (часто большинство), которые занимаются внедрением поверхностно, зачастую ограничиваясь ритуалом. Посетите такие заводы и посмотрите, что там происходит. В чем разница? Ответ всегда один — руководство. По меньшей мере в 90% случаев успешного внедрения бережливого производства директор завода уверен в успехе, имеет видение и знает, что нужно делать. В остальных 10% эта работа поручается представителю высшего менеджмента, например руководителю производства или заместителю директора завода, а сам директор остается в стороне.
Лидеры умеют руководить, а руководство означает эффективное применение власти. Как этому научить? Ведутся горячие споры о том, чему можно и чему нельзя научить в школе бизнеса. Мы убеждены, что в школе бизнеса нельзя научить лидерству. Вопрос в том, можно ли научить этому вообще, или эта способность дается нам от рождения. Как бы то ни было, компании могут сделать очень многое, чтобы взрастить лидеров, в том числе:
•тщательно отбирать лидеров;
•обеспечить потенциальным лидерам наставническую помощь со стороны успешных лидеров;
•создавать условия, которые требуют от людей напряжения сил и позволяют потенциальным лидерам проявить себя;
•обеспечить лидеров необходимой поддержкой и инструментами, чтобы их работа была более результативной.
В Toyota перечисленные методы весьма успешно используют на всех уровнях — от лидера команды и лидера группы до директора предприятия, главного инженера и руководителей высшего ранга. Лидеров тщательно отбирают и заботливо взращивают. Каждый лидер знает, что одна из важнейших задач, которые стоят перед ним, — заниматься воспитанием и развитием людей, в том числе будущих лидеров. Все в дао Toyota ориентировано на то, чтобы стимулировать рост и развитие людей, и такие условия позволяют лидеру проявить себя и добиться успеха. Инструменты производственной системы Toyota, культура Toyota и единая структура управления представляют собой плодородную почву для одаренных от природы лидеров.
Перемены невозможны без умелых лидеров30. Но каково их место в организации? Ответ: лидеры необходимы на высшем, среднем и низовом уровне. Давайте рассмотрим каждый из этих уровней, а потом поговорим, что значит стать учителем или тренером по бережливому производству.
Поведение «людей с передовой» отражает образ действий высшего руководства. В главе 11 мы говорили о том, что лидеры Toyota — практики. Их можно увидеть в цеху, конструкторском бюро и любом другом месте, где кипит работа. Они в полной мере овладели искусством генти генбуцу и умеют наблюдать и видеть, что происходит на самом деле. Везде, куда бы они ни отправились, они занимаются обучением и коучингом.
Но подобно прочим лидерам, им тоже приходится действовать с помощью других людей. В сущности, именно так можно определить лидера — это тот, кто имеет последователей. Мы н'е рассчитываем, что лидер будет заниматься деталями разработки или внедрения. Так в чем же состоит его роль?
На рис. 20-1 показана типовая структура руководства преобразованиями при освоении бережливого производства. Каждая из ролей, обозначенных на схеме, необходима, при этом спонсор проекта со стороны высшего руководства задействован в процессе в двух аспектах. С одной стороны, он
Рис. 20-1. Структура распределения ролей в процессе преобразований
предоставляет необходимые ресурсы — в том числе деньги, но не только. С другой стороны, в его распоряжении все источники власти, которые позволяют добиться желаемого результата.
Не забывайте, мы имеем дело с корпоративными принципами. Перемены всегда вызывают сопротивление. Всегда есть люди, которые считают, что перемены идут вразрез с их личными интересами или интересами подразделения. Рассмотрим следующий пример.
У одного из наших клиентов — военной базы, которая выполняла ремонт самолетов, — все ремонтные рабочие должны были списывать часы работы на тот или иной заказ. Чтобы привлечь рабочих к участию в проектах по внедрению бережливого производства, их сняли с привычной работы и объединили в команды для проведения практических семинаров по кайдзен. Внедрение шло весьма интенсивно, несколько проектов велось параллельно, и в их реализации участвовали десятки рабочих. Прилагались все сиды, чтобы ускорить ремонт самолетов, удовлетворяя нуждам потребителя. Результаты преобразований были весьма впечатляющими, и теперь по срокам выполнения работы завод опережал многие другие. Выгода должна была исчисляться десятками миллионов долларов. Однако часть времени рабочих теперь списывалась в бюджет внедрения бережливого производства, который испытывал все большие и большие финансовые трудности. Руководство военной базы настаивало, чтобы директор завода прекратил внедрение бережливого производства. То же самое предполагалось сделать и на предприятии по ремонту двигателей. Его руководитель мог бы уступить, если бы не командующий базой, который разрешил ему привлекать рабочих к проведению семинаров. Командующий был сторонником бережливого производства и знал, что поступает правильно.
Интересно, что повышенные затраты на проект возникали в результате «искажений», которые давала система учета. Все рабочие, которые участвовали в освоении бережливого производства, были на повременной оплате, но во время кайдзен или при ремонте самолета они получали твердый оклад. Фактически внедрение бережливого производства вело к повышению производительности и высвобождению значительного количества ремонтных рабочих. Переменные издержки на ремонт снижались, но поскольку система учета требовала рабочих списывать часы, они списывали их на бюджет внедрения бережливого производства, превышая тем самым его расходную часть. Руководство базы, находясь во власти этих цифр, было готов выступить на борьбу с программой освоения бережливого производства, которая, по его мнению, обходилась слишком дорого. Оно видел затраты, но не замечало выгод. На самом деле выгоды были весьма значительны, а ни о каких предельных издержках, связанных с рабочим временем, не было и речи. При этом рабочие набирались опыта и активно поддерживали внедрение бережливого производства.
Освоение бережливого производства всегда сопряжено с определенными трудностями, в числе которых финансовые проблемы, попытки воспрепятствовать прогрессу, отсутствие необходимой поддержки со стороны функциональных подразделений, например конструкторского бюро и отдела технического обслуживания, разговоры о нарушении установленных правил и т.д. Спонсор проекта должен уметь видеть ситуацию шире: бережливое производство может- коренным образом изменить компанию, превратив ее в высокоэффективную организацию. Действенное и последовательное вмешательство спонсора обеспечивает движение вперед и препятствует стагнации.
Наш опыт говорит о том, что побудить представителей высшего менеджмента увидеть преимущества бережливого производства и увлечь их новой идеей несложно. Однако разница между успехом и неудачей — это разница между одобрительными кивками и поддержкой на словах и реальными действиями на высшем уровне. Один из словарей определяет английское слово commitment (приверженность, обязательство) как преданность или верность делу. Дело — это бережливое производство. Лидеру необходимо видение обучающегося бережливого предприятия. Он должен неотступно стремиться к реализации видения. Даже встречая сопротивление, он должен продвигаться вперед и непоколебимо придерживаться избранного курса. Если лидер проявляет нерешительность, его подчиненные тоже начинают колебаться. Если лидер перед каждым этапом внедрения анализирует затраты и результаты и только потом берется за дело, это будет воспринято как колебания.
Преданный делу лидер должен предоставить ресурсы, необходимые для бесперебойной работы. Ресурсы — это люди и финансы, а также ответственность за результаты. Следует понимать, что эта работа чрезвычайно важна для компании и участие в ней является обязательным. Поскольку хозяин процесса (рис. 20-1) отвечает за успех, с него будут спрашивать в случае неудачи. При этом речь идет о двустороннем взаимодействии. Как показано на схеме, хозяин процесса отчитывается перед спонсором, а спонсор должен поощрять хозяина процесса за упорный труд и достигнутые результаты. Это означает, что спонсор должен быть в курсе дел, причем не в бюрократическом смысле, а в понимании дао Toyota, основанном на принципе генти генбуцу. Чтобы представлять, как идет совершенствование, спонсор должен видеть происходящее своими глазами.
Регулярно проводите анализ хода работ на производстве
К сожалению, представители высшего руководства, которые привыкли к совещаниям, деловым поездкам и электронной переписке, считают, что посещение цеха, где можно своими глазами увидеть, как идет освоение бережливого производства, не входит в число самых важных дел. Фудзио Тё (цитируется в Дао Toyota) рассказывает, как, будучи президентом Toyota Motor Manufacturing в Кентукки, он ежедневно приходил в цех, чтобы посмотреть, как американцы используют систему андон. Визиты президента воодушевляли подчиненных и стимулировали серьезно относиться делу. Выполнение этой важной обязанности требует, чтобы руководитель обладал соответствующими знаниями, которые позволят ему понимать то, что он видит. Следует осуществлять регулярные, запланированные обходы предприятия или нескольких предприятий. Ход выполнения проектов по бережливому производству можно оценить по визуальным индикаторам и общим показателям. Неплохим подспорьем для руководителей, особенно на первых порах, может быть контрольный листок, где отмечено, на что обращать внимание во время обхода. Следует хорошо продумать расписание таких визитов и относиться к ним серьезно.
На тех, кто находится в середине, давят со всех сторон: и снизу, и сверху. Такова участь менеджера среднего звена. В понятие «менеджер среднего звена» мы включаем всех, от мастера на линии до руководителей подразделений. Их работа состоит в том, чтобы воплощать великие идеи высшего руководства в конкретные дела и результаты. А значит, их действия сказываются на судьбе рядовых сотрудников, при помощи которых выполняется работа. Эти менеджеры должны обеспечивать дневную выработку, отвечать за качество и обслуживание и иметь дело со всевозможными экспертами, которых направляет к ним менеджмент, чтобы помочь им лучше выполнять свою работу.
Для менеджеров среднего звена бережливое производство — одна из множества идей высшего руководства, которые доносит до них вспомогательный персонал. У менеджеров среднего звена есть еще одна примечательная особенность. Несмотря на то что формально власть принадлежит высшему руководству, именно от менеджеров среднего звена зависит, будет ли работа выполнена, или ей станут чинить препятствия. Именно они определяют успех или провал бережливого производства. Работа с ними может оказаться не самым приятным делом для агента перемен. Дело не в том, что все менеджеры среднего звена упрямы и несговорчивы от природы. Дело в их должности. Дальше их, как говорится, «фишка не идет».
Агенту перемен, который занимается бережливым производством, возможно, придется решать чрезвычайно сложные задачи. С одной стороны, уровень среднего менеджмента представляет собой основной рычаг преобразований. Прекрасно, когда тебя поддерживает спонсор проекта, но реальную работу организует не он, а менеджер среднего звена. В Toyota мы видели, что большую часть преобразований на оперативном уровне направляли и стимулировали лидеры групп. С другой стороны, едва ли можно надеяться, что большинство- менеджеров среднего звена возглавят процесс преобразований на своих участках. В Toyota существенную часть этой работы выполняют лидеры команд, но это результат долгих лет подготовки, обучения и формирования особой культуры. В основе такого подхода лежит система лидеров команд и лидеров групп, о которой рассказывалось в главе 10.
Конечно, бывают и исключения. Среди менеджмента среднего звена, работающего в самых разных подразделениях — производственных, проектно-конструкторских, занимающихся контролем качества — всегда есть люди, которым близки идеи бережливого производства и которые с энтузиазмом берутся за дело. Если им удается достичь успеха, они могут постепенно добиться поддержки сверху, даже если изначально высший менеджмент был не на их стороне. К сожалению, такие случаи редки. Как правило, все начинается сверху.
Поэтому в большинстве случаев успех преобразований во многом зависит от тренера в области бережливого производства, который опирается на существующую иерархию и полномочия спонсора проекта и действует через менеджмент среднего звена. Возможно, со временем, если компании удастся сформировать подлинную культуру бережливого производства, произойдет крутой поворот и тренер по бережливому производству переключится на поддержку менеджеров среднего звена, которые будут стимулировать и направлять преобразования.
С точки зрения социологии любая организация — это сеть. Люди устанавливают между собой эмоциональные, социальные и коммуникативные связи. Если изобразить эти связи графически, например, с учетом частоты коммуникации, изображение будет напоминать паутину или сеть. Вглядевшись в нее повнимательнее, вы заметите, что отдельные участки этой сети плотнее, чем другие. Такие уплотнения образуются вокруг людей, которых называют «социометрическими звездами». Под этим термином понимают людей, которые пользуются популярностью или являются прирожденными лидерами. С их мнением считаются больше, чем с мнением других. Если вам удастся склонить на свою сторону этих неформальных лидеров, с их помощью вы сможете изменить культуру компании.
Выявить таких лидеров нетрудно. Поскольку круг их связей чрезвычайно широк, найти их можно разными путями. В компании обычно знают, о ком идет речь, к тому же такие люди, как правило, известны и непосредственным руководителям — менеджерам среднего звена. Именно их в Toyota стараются сделать лидерами команд.
Есть масса способов привлечь таких людей к участию в работе. Разыскав такого человека, тренер по бережливому производству может побеседовать с ним в неформальной обстановке. Еще лучше — официально привлечь прирожденного лидера к участию в процессе преобразований. Прекрасная возможность для этого — практический семинар по кайдзен. Если во время такого семинара разбить группу участников на небольшие подгруппы, можно поставить неформальных лидеров во главе команд. Разумеется, менеджменту придется оплатить их участие в семинаре, однако речь идет о незначительных инвестициях, которые в долгосрочной перспективе окупятся сторицей. Некоторые компании отбирают несколько таких лидеров и вводят их в штат подразделения по развитию кайдзен. Одно дело, если в цех придет менеджер среднего звена и попытается заручиться поддержкой своих подчиненных, и совсем другое, если о такой поддержке попросит уважаемый товарищами рабочий. Итак, ищите неформальных лидеров и привлекайте их к работе.
Тренер по бережливому производству — это официальная должность. Это человек или группа людей из штата, которые выполняют роль эксперта. Их роль при переходе к бережливому производству чрезвычайно важна. К сожалению, все обычно слишком заняты, и бережливое производство оказывается еще одним видом дополнительной работы. Для штатного тренера бережливое производство — основная работа, которая обычно превращается в страстное увлечение.
Освоение бережливого производства должно осуществляться благодаря работе линейного, а не штабного персонала. Линейная структура предполагает отчетность и ответственность за получение результатов. Те, кто выполняет работу по добавлению ценности, представляют собой часть линейной структуры. Именно им предстоит применять бережливые системы, а значит, они и должны быть хозяевами этих систем.
Возьмем, к примеру, стандартизированную работу и вспомним отца научного менеджмента Фредерика Тейлора, который занимался изучением движений и затрат времени. Он считал, что стандартизация работы — дело вспомогательного персонала, т. е. инженеров по организации производства, — знатоков научного менеджмента. При помощи особых методик, которые не дано понять рабочим в цеху, инженеры определяют оптимальный метод выполнения работы. Мастер же должен следить за тем, чтобы рабочие придерживались этого метода. Непредвиденным результатом такого подхода стал конфликт между менеджментом и профсоюзами и враждебное отношение к «экспертам по эффективности». Это привело к росту потерь и конфликту целей менеджмента и рабочих.
Мы видели, что в Toyota стандартизированная работа — это инструмент непрерывного совершенствования, который используется рабочими, занимающимися добавлением ценности, а также лидерами команд и лидерами групп. Если мы наберем группу «экспертов по бережливому производству», которые будут «выталкивать» процедуру стандартизированной работы, навязывая рабочим собственные идеи, мы вернемся прямиком к научному менеджменту Тейлора.
При построении бережливого производства тренер — вторая по значимости фигура после высшего менеджмента. Горькая правда состоит в том, что рабочие, как правило, знают о бережливом производстве недостаточно или не имеют необходимой мотивации заниматься преобразованиями, смысл которых им не вполне понятен. Представители высшего менеджмента, даже будучи сторонниками бережливого производства, зачастую имеют столько срочных дел, что у них нет возможности изо дня в день уделять преобразованиям должное внимание. Таким образом, большая часть ответственности ложится на плечи тренера или команды по внедрению бережливого производства.
Можно ли с учетом этого поручать кому-либо заниматься бережливым производством на условиях неполной занятости дополнительно к выполнению основных обязанностей? Вероятно, что пять человек, каждый из которых тратит 20% рабочего времени на бережливое производство, справятся с этим не хуже, а может и лучше, чем один человек, который уделяет этому 100% времени. Однако пять человек, занятых выполнением прямых обязанностей, на которые обычно уходит 120% времени, вряд ли сумеют найти 20%, чтобы посвятить его бережливому производству. Мы крайне редко видим примеры успешного освоения бережливого производства там, где нет хотя бы одного тренера по бережливому производству, работающего на условиях полной занятости. В предыдущей главе мы рассказывали о компании Denso и ее подходе к бережливому производству. В рамках программы «Эффективное предприятие» были выделены внутренние эксперты по бережливому производству из отдела организации производства. На предприятиях Toyota в Северной Америке, включая NUMMI, все чаще наблюдается стремление самостоятельно подготовить экспертов по TPS — не менее двух специалистов, работающих на условиях полной занятости, для каждого из основных процессов (например, окраска, отделка, штамповка, окончательная сборка). Это означает, что те предприятия за пределами Японии, где TPS стала неотъемлемой частью культуры, все глубже осознают потребность в специалистах по TPS, которые позволяют им повысить результаты.
Перечислим обязанности тренера по бережливому производству. Тренер:
1)руководит программами по созданию образцовых линий;
2)руководит составлением карт потока создания ценности;
3)руководит практическими семинарами по кайдзен;
4)обучает философии бережливого производства и применению его инструментов (краткие учебные курсы и практическое освоение бережливого производства);
5)осуществляет коучинг лидеров на всех уровнях;
6)разрабатывает бережливую систему процессов (принципы, показатели, оценка, методы, стандартные рабочие процедуры);
7)стимулирует внутренние преобразования;
8)обучается в других организациях и приносит с собой новые идеи.
Идеальная организационная структура программы освоения бережливого производства, приведенная на рис. 20-1, предполагает, что спонсор, хозяин процесса и команда, которая работает с потоком создания ценности, возглавляют преобразования. К сожалению, в большинстве случаев это не соответствует действительности, особенно на ранних этапах преобразований. Чтобы обучение шло, а дело двигалось, необходим внешний импульс, который обеспечивает энергичный сэнсэй (консультант) со стороны. В то же время, когда результаты для линейных руководителей становятся очевидными, растет желание воспользоваться услугами внутреннего тренера по бережливому производству: «Пожалуйста, займитесь потом моим участком». Это явный признак прогресса, а значит, работа тренера становится куда более приятной.
Поскольку тренер играет в этом процессе решающую роль, их отбор следует проводить как можно более тщательно. Тренер по бережливому производству должен обладать следующими качествами:
1)быть толковым и расторопным;
2)обладать хорошей памятью;
3)иметь тягу к знаниям;
4)иметь опыт практической работы;
5)быть страстным приверженцем совершенствования процессов;
6)обладать управленческими навыками;
7)уметь ладить с людьми;
8)обладать развитыми коммуникативными навыками (устными и письменными);
Тренер быстрого приготовления
Поскольку инструменты и концепции бережливого производства по сути весьма логичны, может показаться, что подготовить тренера по бережливому производству несложно. Множество университетов и профессиональных ассоциаций готовы выдать соответствующий диплом. Однако хотя во время обучения можно узнать массу полезных вещей, освоить учебную программу — еще не значит стать квалифицированным тренером.
Есть два вида знания: процедурное знание и неявное знание. Процедурное знание, например о том, как создавать ячейки, можно приобрести в аудитории. Неявное знание приобретается на опыте под руководством умелого наставника. Для того чтобы понять, когда уместно создание ячейки, когда уровень стабильности позволяет создать ячейку для потока единичных изделий, как сделать сторонниками данной концепции представителей менеджмента, в какой точке связанного потока создания ценности должна находиться ячейка, как определить оптимальные параметры ячейки и многое другое, требуется скорее неявное, нежели процедурное знание. «История двух поршней», приведенная ниже, — наглядный пример того, как исполненные благих намерений менеджеры и инженеры, которые прошли весьма основательную формальную подготовку в области бережливого производства, не прислушались к эксперту по TPS и приняли массу неправильных решений, создавая ячейку для станочной обработки. Перспектива получить тренера быстрого приготовления с помощью интенсивной и непродолжительной программы обучения представляется некоторым менеджерам чрезвычайно соблазнительной. Не поддавайтесь искушению! Чтобы сформировать базовые навыки, которые впоследствии позволят стать хорошим тренером, нужно в течение нескольких лет приобретать опыт, неоднократно принимая участие в создании бережливого потока создания ценности в качестве члена команды, а затем ее лидера (см. программу по созданию образцовой линии в главе 19). Приобретать такой опыт следует под руководством умелого наставника, за плечами которого не менее 5-10 лет серьезной работы в области бережливого производства.
9) иметь базовые технические навыки (уметь работать с таблицами, графиками, данными и т.д.);
10)владеть системным мышлением (понимание потока процесса и т.д.);
11)уметь решать проблемы;
12)любить много читать;
13)быть открытым для новых идей;
14)быть собранным и организованным.
Это примерный перечень навыков и качеств, на который следует ориентироваться при поиске тренера. Однако обладать перечисленными качествами еще не значит стать тренером по бережливому производству. Тренеру нужна подготовка. Отчасти речь идет о технических навыках работы с инструментами бережливого производства. В этом отношении прекрасным подспорьем может стать чтение соответствующей литературы, а возможно, и курс по бережливому производству в университете. Однако более основательную подготовку, которая имеет решающее значение, тренер получает в процессе работы. В этом может помочь лишь тот, кто уже стал умелым наставником по бережливому производству. Речь идет о сэнсэе.
В Японии сэнсэем называют любого учителя. Однако за этим словом стоит нечто большее, а именно — тесные взаимоотношения. Сэнсэй пользуется глубоким уважением за знание и мудрость. Ученик стремится научиться у сэнсэя. Сэнсэй уже прошел путь, который предстоит пройти ученику.
Некоторым компаниям удается обзавестись собственным сэнсэем, который обучает и тренирует персонал. Таким сэнсэем может стать тот, кто ранее работал под руководством наставника или был менеджером в другой компании. Так, некоторые директора заводов и вице-президенты, в прошлом— менеджеры Toyota, естественным образом становятся сэнсэями. Однако чаще роль сэнсэя выполняют внешние консультанты, которые приобрели свои знания на опыте, возможно, работая в Toyota.
Самое важное для сэнсэя — быть учителем. Не рассчитывайте, что сэнсэй сделает все за вас. Учитель хорош настолько, насколько хороши его ученики. Поэтому именно тщательный отбор будущих тренеров, которым предстоит учиться у сэнсэя, определит, сможете ли вы реализовать потенциал сэнсэя в полной мере.