Практика дао Toyota. Руководство по внедрению принципов менеджмента Toyota Лайкер Джеффри
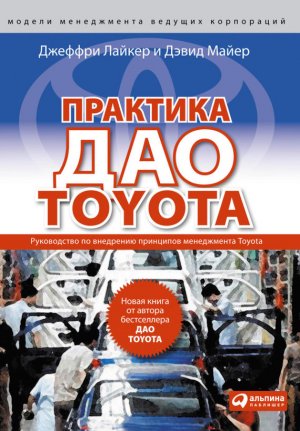
У каждого сэнсэя своя манера преподавания. Тайити Оно использовал весьма жесткие методы обучения, оказывая на ученика психологическое, а порой и физическое давление. Задача сэнсэя при таком подходе — выявить промах и дать ему жесткую критическую оценку, чтобы ученик осознал, что несовершенен и должен упорно трудиться, чтобы выйти на соответствующий уровень. Некоторые сэнсэи, работающие по найму, — опытные консультанты по бережливому производству — полагают, что должны быть мягче и деликатнее, и заходят в этом стремлении слишком далеко. Они знают, что, если их критика будет слишком жесткой, они могут лишиться работы. Поэтому они превращаются в членов группы и выполняют значительную часть работы самостоятельно.
В большинстве случаев сэнсэй не должен быть ни слишком суров, ни слишком мягок и не должен выполнять работу своими руками. Он должен вести в бой тех, кого обучает. Часто для этого нужно поставить перед учеником сложную задачу и отойти в сторону, давая ученику возможность испытать свои силы, а порой и потерпеть неудачу. Затем можно вмешаться и преподать урок. Так выглядит процесс обучения на опыте. Чтобы усвоить урок, ученик должен выполнить работу сам, воспринимая стоящую перед ним задачу как вызов. Вряд ли он научится многому, если будет лишь наблюдать за работой сэнсэя.
Частота визитов сэнсэя может быть разной — от полной занятости до проведения практических семинаров по кайдзен раз в две недели или два дня в месяц. Обычно полная занятость — это слишком много, а два дня в месяц — минимум.
Сэнсэй, занятый полный рабочий день, вместо того чтобы заниматься коучингом, как правило, выполняет работу сам. Необходимость в этом может возникнуть, если нет сильных учеников, выделенных на полный рабочий день, а также если работу нужно сделать быстро. Но такой подход приемлем лишь в качестве временного. Если сэнсэй, занятый полный рабочий день, может инициировать достаточный объем преобразований и показать возможности бережливого производства, можно надеяться, что это побудит менеджмент выделить способного и решительного человека, который будет постоянно работать рядом с сэнсэем. Тогда сэнсэй может сократить объем личного участия в работе.
Практические семинары по кайдзен, проводимые раз в две недели, могут помочь осуществить значительные преобразования в сжатые сроки (см. рассказ про компанию Теппесо в главе 19). Если сэнсэй появляется лишь для проведения таких семинаров, скорее всего, коучинг сводится к обучению на рабочих местах в процессе семинара. Чрезвычайно важно, чтобы работа с сэнсэем не ограничивалась только практическими семинарами.
Подход, при котором сэнсэй проводит в компании два дня в месяц, весьма эффективен при наличии сильной внутренней команды. Сэнсэй анализирует работу, выполненную после предыдущей встречи, дает ей критическую оценку и определяет, что надо сделать в течение следующего месяца. Сэнсэй может продемонстрировать, как использовать какой-либо инструмент, или оказать помощь в решении сложной технической задачи, после чего уходит. При такой модели сэнсэй не может делать работу сам, он должен заниматься обучением, иначе дело не сдвинется с места. Ученики понимают, что не должны во всем полагаться на сэнсэя.
Собрав элементы, необходимые для осуществления устойчивых преобразований, воедино, мы получим картину, подобную изображенной на рис. 20-2. Здесь показана структура процесса преобразований, которая учитывает распределение ролей и ответственности, потребность в широком участии и наличии хозяина (в особенности в рамках линейной структуры), а также необходимость в наставничестве и преданном делу, знающем руководстве.
Важность преданного делу, знающего руководителя трудно переоценить. «История двух поршней» говорит о том, как важны оба эти качества: знания и преданность делу. Казалось бы, в данном случае в наличии было все, что нужно, — поддержка высшего менеджмента, стимулирующая преобразования структура, наличие хозяина в рамках линейной структуры и даже один из лучших в мире экспертов по бережливому производству в области станочной обработки. Поскольку создавалась новая линия, было решено изначально построить ее на основе принципов бережливого производства.
Инженер, который вел один из проектов, учился у сэнсэя, и ему удалось создать весьма эффективную, бережливую линию. Другой руководитель проекта не понимал или не желал понимать своей задачи и пошел на поводу у директора завода, который не находил времени, чтобы разобраться в происходящем. Результат его работы был вполне предсказуем — он потерпел неудачу.
Конкретная ситуация: история двух поршней: принципы станочной обработки на Toyota и на американской фирме
«Мне кажется, что, передо мной стоит кружка с превосходным пивом, — сказал Исияки Ёсина, ветеран Toyota Motor Corporation с 30-летним стажем, который стал консультантом Engineering Integrators Company (EIC). — Но каждый раз, когда я протягиваю руку к чудесному ледяному напитку, она наталкивается на невидимую стену», — Ёсина-сан описывал происходящее метафорически, как принято на Toyota. Описанный им образ красноречиво говорил о том, как расстраивает его отсутствие прогресса в освоении бережливого производства в Acme Systems на протяжении полутора лет, которые он проработал в этой компании*.
Введение
Мы уже обращали внимание читателя на то, что преобразования представляют собой процесс, затрагивающий корпоративные принципы и требующий преданного делу, просвещенного руководства. Это прекрасно иллюстрирует история Дэвида Острайхера, стажера Acme Systems, — одного из крупнейших в мире поставщиков разнообразных комплектующих для автомобилей. Дэвид работал вместе с ведущим специалистом по TPS в области механообработки, бывшим главным инженером Toyota, который вышел на пенсию после 30 лет работы в сфере организации производства. Ёсина, который работал в Acme Systems экспертом на условиях весьма высокой повременной оплаты, прекрасно разбирался в механообработке. Работая в Toyota в странах Азии, он приобрел обширный опыт монтажа оборудования, однако это была его первая попытка применить методы Toyota в США. Возможность продолжить изучение TPS под началом Ёсина приводила Дэвида в восторг, так же, как и компания, в которую он попал. Все в
Эта история представляет собой адаптированное изложение случая, описанного Дэвидом Острайхером. Она основана на реальных событиях, хотя имена участников вымышлены, а некоторые обстоятельства изменены с целью прояснения сути обсуждаемых вопросов. При желании вы можете поделиться с Дэвидом Острайхером своими соображениями, отправив ему письмо по адресу [email protected]. Дэвид с удовольствием даст необходимые пояснения к описанному случаю и будет рад предложениям по использованию данной истории в качестве учебного материала.
Acme, начиная с генерального директора, были преданы идее бережливого предприятия и имели почти десятилетний опыт работы в этом направлении. Ёсина был приглашен для запуска нескольких новых поточных линий, которые позволяли продемонстрировать потенциал TPS применительно к механообработке.
На одном заводе монтировалось две линии, предназначенные для выпуска разных типов компрессоров, — А1 и Х10. Каждой линией занимался свой руководитель проекта. Как выяснилось, инженер, который руководил работами на линии А1, воспользовался рекомендациями Ёсина и, следуя им, добился прекрасных результатов, тогда как инженер, который работал с линией Х10, все время искал быстрые решения, чтобы добиться краткосрочного снижения издержек. Результаты его работы оказались неудовлетворительными. Любопытно, что оба преследовали одни и те же амбициозные цели и имели возможность работать с одним и тем же специалистом мирового класса.
Показатель качества с первого раза определялся как процент произведенных изделий, которые с первого раза соответствовали требованиям. На момент начала работ уровень качества с первого раза застыл примерно на 85% при целевом показателе более 98%. Под «операционной готовностью» понималась доля рабочего времени, в течение которого оборудование готово к обработке деталей. Традиционно операционная готовность процессов механообработке в Acme составляла 60-70%, и команду попросили поднять этот показатель до 85%. Требования по финансовым показателям (минимальная чистая прибыль, операционная прибыль и прибыль на чистые активы) были довольно высоки, но вполне достижимы. Было очевидно, что на бережливое производство возлагались большие надежды.
Руководитель проекта А1 отвечал за перевод прежнего семейства продуктов А1 с существующего завода на другой, где установлено совершенно новое оборудование. Руководитель проекта Х10 отвечал за оптимальную концепцию линии Х10, которую предстояло добавить к комплексу двух уже функционирующих модулей Х10 на новом заводе.
Хотя две линии производили поршни для разных продуктовых семейств, на бумаге процессы их изготовления выглядели очень похоже.
При выборе оборудования для линии Х10 решающую роль сыграли предпочтения директора завода, который с целью сохранения единообразия остановился на том же типе станков, что использовался для производства поршней Х10 раньше. При выборе станков для линии А1 перевесили рекомендации Ёсина, и в качестве поставщика была избрана компания Toyoda Machinery Works (TMW). Эта компания надеялась завязать с Acme прочные, долгосрочные отношения. Acme давно была хорошо известна как производитель шлифовальных станков, но на американском рынке станков для механообработки она присутствовала недавно.
Далее мы более подробно поговорим о некоторых технических решениях, принятых каждой из команд. Мы не собираемся читать лекции по механообработке, но хотим наглядно и подробно проиллюстрировать образ мышления, который необходим для разработки по-настоящему бережливой производственной линии.
Ёсина встречается с командой А1
Ёсина считал, что его дело — направлять ход работ, не навязывая своего мнения по части технических решений. Он давал рекомендации общего характера и высказывал свои соображения в отношении идей, которые предлагали команды. Команда А1 внимательно прислушивалась к своему наставнику, стремясь узнать как можно больше, и ее решения были воплощением концепций бережливого производства. Одной из задач стала организация материального потока: команда хотела организовать поток единичных изделий, понимая все ограничения, которые накладывали условия работы. Вместо того чтобы сразу создавать поток единичных изделий, команда решила обрабатывать четыре поршня одновременно. В пользу такого решения говорили следующие соображения. Во-первых, это позволит идеально сбалансировать работу, поскольку станок позволяет одновременно обрабатывать четыре поршня. Взяв четыре поршня (по два в каждую руку), оператор устанавливает их в станок, замыкая тем самым пружинный контакт, после чего переходит к соседнему станку, чтобы забрать четыре поршня, которые автоматически выталкиваются, готовые к очередной операции обработки. Во-вторых, время цикла станочной обработки таково, что для бесперебойного обеспечения деталями сборочного участка линии А1 за один цикл нужно обрабатывать четыре поршня, поскольку это позволяет уложиться во время такта.
Но при одновременной обработке четырех поршней образовывалось такое количество стружки, что было непонятно, как добиться, чтобы зажимные приспособления, которые TMW поставляла вместе с оборудованием, оставались чистыми. Если зажимные приспособления не будут чистыми при обработке каждой детали, это негативно отразится на показателе качества с первого раза. Представители TMW обратились к своей базе данных о процессах и предложили команде обрабатывать поршни горизонтально, поскольку тогда центробежная сила и сила тяжести будут отбрасывать стружку в сторону, не позволяя им скапливаться вокруг деталей и зажимных приспособлений. Высказав это предложение Ёсина, члены команды смотрели на него, ожидая реакции. Ёсина кивнул в знак согласия.
Следующий вопрос касался планировки линии. Места на участке, отведенном под линию А1, было немного, но команда хотела последовать совету Ёсина и расположить станки в линию. Члены команды хорошо помнили, что говорил Ёсина о достоинствах такого подхода на одной из их встреч:
«Для потребителя завод — все равно что витрина магазина. Размещение станков должно производить благоприятное впечатление на посетителей. Никаких изолированных островков. Поточные линии должны быть прямыми, а станки — стоять друг за другом, чтобы взгляду открывалась ровная, аккуратная линия. Поток от получения материала до отгрузки готовых изделий должен быть простым. Лишь если работа имеет достаточно продолжительное время цикла и оператору приходится выполнять несколько операций и много ходить, следует создавать ячейки U- или L-образной формы, которые позволяют сократить расстояние и устранить потери времени на ходьбу. Всегда представляйте себя на месте детали: куда бы вам хотелось отправиться дальше? Желали бы вы между поступлением и отгрузкой следовать сложным, извилистым маршрутом или вы предпочли бы прямой путь от поставщика к потребителю?»
Последней из поднятых тем было удобство обслуживания. Предшествующее поколение станков А1 пользовалось дурной славой среди обслуживающего персонала, поскольку поддерживать их в рабочем состоянии было очень нелегко. Датчики и точки смазки были разбросаны по всему станку, а график профилактического обслуживания отсутствовал. Стремясь преодолеть подобную практику, команда А1 решила сделать первый шаг в этом направлении и позаботиться о том, чтобы все визуальные индикаторы состояния станка были вынесены на единую плоскость в нерабочей зоне и были доступны при техобслуживании.
Ёсина внимательно просмотрел все представленные материалы и, судя по всему, остался доволен. Он не думал, что все пройдет, как запланировано, так как понимал, что по ходу дела наверняка возникнут проблемы, которые потребуют принятия контрмер. Тем не менее он одобрил базовые принципы, на которые опиралась команда при разработке решений.
Ёсина встречается с командой Х10
Команда Х10 относилась к Ёсина иначе. Казалось, все ее члены считают, что его присутствие лишь отвлекает их от более срочных дел. Они вежливо выслушивали его соображения, но принимали решения с учетом более привычных критериев, главным образом краткосрочных издержек.
Представив Ёсина свои идеи, они начали на все лады превозносить экономию, которой удалось добиться, заказав зажимные приспособления у одной из местных компаний, вместо того чтобы покупать их у производителя станков. Ответственный за снабжение по семейству продуктов Х10 подсчитал, что заказ оснастки у местного производителя сразу позволит снизить издержки на 8%. Кроме того, поскольку предприятие поставщика зажимных приспособлений расположено неподалеку, это даст возможность быстро пополнять запас выходящих из строя зажимных приспособлений или вносить изменения в их конструкцию.
Затем команда рассказала о своих достижениях в создании потока единичных изделий. Члены команды знали, что поток единичных изделий — это идеал бережливого производства (об этом говорили на одном из практических семинаров в Acme, в котором участвовали члены группы), и не сомневались, что Ёсина одобрит их подход. Команда особенно гордилась тем, что в ходе одной из конечных операций из заготовки получалось целых два поршня. Это непременно позволит повысить показатели производительности линии, ведь на начальных этапах процесса будет обрабатываться всего одна деталь, а в итоге из нее получится два готовых изделия.
Затем речь зашла о потоке работы в ячейке. Все знали, что станок от поставщика № 2 работает примерно на 66% быстрее, чем станок от поставщика №5. Вместо того чтобы дождаться, пока Ёсина задаст непростой вопрос о сбалансированности загрузки операторов, команда опередила его и изложила свою идею: на нескольких станках будут установлены лотки с запасом деталей (дюжина заготовок), ожидающих обработки (незавершенное производство). Поскольку станок от поставщика № 2 работает быстрее, установка и снятие деталей на этом станке будут осуществляться вручную. Станок от поставщика № 5 имеет более продолжительное время цикла, поэтому для данного станка было приобретено устройство автоматической загрузки/разгрузки. Таким путем, по расчетам команды, время, которое уйдет у оператора на то, чтобы загрузить и разгрузить станок от поставщика №2 вручную, компенсирует меньшую продолжительность времени цикла, и этот станок будет работать в едином ритме со станком от поставщика № 5. Запас в дюжину единиц незавершенного производства сослужит роль буфера на тот случай, если вдруг окажется, что автоматическое загрузочно-разгрузочное устройство и оператор работают несогласованно.
Что касается метода обработки деталей, команда Х10 решила, что инструмент следует перемещать по вертикали, фиксируя деталь с помощью зажимного приспособления. При этом не учитывалось, что при обработке детали используется охлаждающая жидкость и при первом же внедрении стандартизированной работы от операторов потребуют, чтобы они ежечасно удаляли с зажимных приспособлений и инструмента скопления металлической стружки.
Эти решения обусловили весьма причудливую планировку нового модуля Х10, который должен был соседствовать с двумя другими ячейками (рис. 20-3). Такое взаимное расположение модулей преследовало цель сократить трудозатраты транспортных рабочих, обслуживающих линию, более чем на 200 часов в год. Кроме того, команда Х10 одобрила решение предыдущих команд Х10 передать процесс нанесения металлического покрытия внешнему исполнителю, несмотря на то что качество его работы ухудшилось. Хотя это увеличит объем запасов незавершенного производства на 15%, зато не придется тратить $95 ООО на закупку оборудования и связанное с ней обучение персонала.
Презентация завершилась выступлением члена команды, который отвечал за качество. Поскольку решения, принятые в процессе работы над проектом, позволяли сэкономить значительные средства, команда планировала воспользоваться экономией и вложить средства в пакет программ для сбора данных, что позволит контролировать производительность каждого станка. Эти данные будут сводиться воедино при помощи программного модуля, который дает возможность генерировать отчеты, содержащие различные представляющие интерес показатели, в частности время простоя, количество единиц произведенной продукции и время цикла станка. Сбор информации такого рода был чрезвычайно важен, поскольку уровень качества двух действующих модулей Х10 не соответствовал требуемому уровню.
На этом презентация завершилась. Ёсина не высказал никаких конкретных замечаний по поводу представленных ему планов. Вместо этого он подошел к столу и вручил членам команды эскиз планировки линии XI0, который набросал во время презентации. Участники презентации с удивлением увидели, что Ёсина не пытался вписать линию в причудливые формы свободного пространства между двумя уже готовыми модулями, а просто выстроил станки в прямую линию. Они согласились обсудить его предложение с директором завода. Ёсина поблагодарил группу за потраченное время и сказал, что он будет с нетерпением ждать решения вопроса о планировке.
Четыре дня спустя Ёсина получил приглашение на встречу с инженером по организации производства. Во время встречи инженер сообщил, что после обсуждения с директором завода было решено оставить компоновку такой, как предложила команда. Директор завода не понял, зачем полностью перестраивать планировку всего участка. Ёсина знал, что, если бы директор завода нашел несколько минут, чтобы спуститься в цех, он мог бы своими глазами увидеть неровные ряды станков разной высоты, извилистые проходы и тесноту, которые отличали замысловатую планировку, получившую его поддержку (рис. 20-3).
Услышав это, Ёсина пришел в смятение. Он не мог понять, почему Acme заплатила его компании сотни тысяч долларов за консультационные услуги, а потом отвергла его рекомендации. Он вскочил и выбежал вон, еле слышно пробормотав «Яппари»*.
Эффективность двух линий станочной обработки
Какая линия работала лучше? К концу 2004 года прошло около двух лет с того момента, как линии А1 и Х10 начали свою работу. Хотя официальных данных по эффективности работы линий немного, беседы с операторами, инженерами и менеджерами позволили выяснить следующее:
' В приблизительном переводе означает «этого следовало ожидать» или «я так и знал».
Большая часть простоев на линии А1 вызвана перебоями в подаче материала с предшествующего процесса, который тоже осуществляется на данном заводе. Простои на линии Х10 возникали в результате проблем с качеством и поломок оборудования. Чтобы обеспечить надлежащее качество изделий на линии Х10, было решено перед отправкой поршней на сборку проверять размеры каждого готового изделия в зоне, которая отнесена от линии станочной обработки на 100 ярдов. Для сравнения — на линии А1 контроль размеров готовых изделий осуществляется выборочно (1 изделие на 1000).
Какие уроки можно извлечь из данной истории?
Знающее и преданное делу руководство — ключевой фактор успешного освоения бережливого производства. Мы часто спрашиваем: почему компании не занимаются усердным и настойчивым внедрением всего, чему можно научиться у Toyota, несмотря на колоссальный успех, который обеспечивает дао Toyota? Мешают ли этому особенности культуры или сопротивление преобразованиям? Этот пример показывает, где зарыта собака. Все упирается в руководство. На заводе, про который шла речь, были все составляющие, необходимые для успешных преобразований: поддержка высшего менеджмента, опыт успешной работы в области бережливого производства в прошлом, доступность любых инструментов бережливого производства и соответствующих учебных материалов, возможность начать с чистого листа и консультативная помощь одного из лучших в мире специалистов в области бережливого производства, который работал на предприятии полный рабочий день.
Руководитель проекта А1 был убежденным сторонником бережливого производства и стремился учиться. Директор завода предоставил ему полную свободу действий, позволив самому решать, какой быть будущей линии. Мы воздаем директору должное за невмешательство. Но когда инженер проекта Х10 отказался от возможности учиться и вернулся к традиционному образу мышления, директор завода немедленно принял его сторону, препятствуя реализации новаторских идей Ёсина. Примером тому служит одобрение директором чрезмерно сложной планировки линии, которую пытались вписать в свободное место, вместо того чтобы постараться обеспечить рекомендованную прямолинейную компоновку. Казалось бы, у директора завода были все основания последовать совету высокооплачиваемого и знающего консультанта и создать образцовую линию, которая позволит заводу стать более заметным в компании предприятием. Но когда настал критический момент, он решил пойти удобным, проторенным путем. Он считал, что директор завода не обязан ходить в цех и смотреть, что творится на самом деле.
2.Есть разница между поставщиком и сильным техническим партнером. Несомненно, линия А1 очень выиграла от работы с Toyoda Machinery Works. Команда Х10 якобы для обеспечения единообразия выбрала для своей линии станки, которые к тому времени уже эксплуатировались на заводе, производя некачественные детали, причем коренные причины низкого качества так и не были установлены. Оснастку они решили закупить у других производителей, погнавшись за дешевизной и удобством работы с поставщиком, расположенным неподалеку, однако при этом не учли, что особенности оснастки тесно связаны с конструкцией станка. Ёсина, опытный специалист и знаток дао Toyota, понимал, что, если вначале потратить чуть больше на хорошие инструменты и оснастку, это позволит снизить общие затраты в дальнейшем. В то время как на линии Х10 стояли станки разных марок, совмещение которых уже вызывало проблемы в работе созданных ранее модулей Х10, группа А1 опиралась на опыт Ёсина и TMW. Именно это помогло ей решить, как выстроить процесс изготовления поршней и какие станки использовать. Ёсина и TMW опирались на обширные знания о станках и процессах, что позволило обеспечить надежность и стабильность производственного процесса.
3.Есть разница между теоретическим усвоением концепций TPS и глубинным пониманием. В компании годами обучали персонал бережливому производству, и все были хорошо знакомы с терминологией TPS. Однако стоящие перед машинной обработкой проблемы было решить не так просто. Принятие верных технических решений давалось командам нелегко, несмотря на опыт инженерной работы и подготовку, связанную с TPS.
Основным различием между линиями Х10 и А1, которое, скорее всего, существенно влияло на показатели качества, была плоскость перемещения инструмента. На линии Х10 инструмент перемещался вертикально, а деталь фиксировалась в плоскости ху. Под действием силы тяжести стружка и охлаждающая жидкость попадали на инструмент, а затем — на детали. Постепенно отходы накапливались, что вело к росту числа дефектных поршней. На линии А1 инструмент перемещался горизонтально, а деталь зажималась в плоскости yz. Хотя при таком конструктивном решении стружка и охлаждающая жидкость все равно падали вниз, они не попадали на деталь, а улавливались сепаратором, после чего стружка отправлялась на переработку, а охлаждающая жидкость была готова к повторному использованию. Это тонкое техническое различие говорит о пристальном внимании к деталям, которое отличает дао Toyota.
Другим примером технических различий между двумя линиями было превратное истолкование командой Х10 концепции потока единичных изделий. Они поняли эту идею слишком буквально, и это имело ряд последствий для процесса механообработки. Во-первых, возможности оператора использовались недостаточно эффективно. Основные обязанности оператора в процессе обработки — это проверка качества, смена инструмента и выявление мелких неисправностей. Все это оператор делает, снимая обрабатываемые детали с одного станка, устанавливая их на другой и запуская очередной цикл обработки. Если оператор за один цикл переустанавливает всего одну деталь, его потенциал не используется в полной мере. Более того, команда Х10 совершила роковую ошибку, не учитывая порядок установки оборудования. Станок, который они приобрели, мог обрабатывать несколько поршней одновременно, и для изготовления конечного продукта требовалось четыре поршня, однако команда решила во что бы то ни стало создать поток единичных изделий. (См. модель сокращения потерь на рис. 5-1, глава 5.) Базовый принцип состоит в сокращении потерь. Поток — это метод выявления проблем, и поток единичных изделий — далеко не всегда лучший метод. В данном случае он лишь увеличил объем потерь.
4.Встраивание качества предпочтительнее сложных технических решений. Дзидока, или встраивание в процесс свойственной человеку способности отличать качественный продукт, представляет собой элемент производственной системы Toyota. К сожалению, команды Х10 и А1 поняли его по-разному. По-видимому, команда Х10 считала, что программное обеспечение для сбора данных, которое она намеревалась использовать, предупредит передачу некачественных деталей на следующий процесс, и казалось бы, такая цель весьма похвальна. Но данная система была нацелена на обнаружение дефектов, а не на их предотвращение. Речь шла об автоматизации сбора данных, а не о выявлении коренной причины проблемы и оперативном принятии контрмер. Для сравнения следует отметить, что линия А1 была разработана таким образом, чтобы предупредить появление дефектов за счет продуманного процесса, в том числе физических параметров обработки деталей. Показатели эффективности работы каждой из линий говорят о том, что создание процесса, который позволяет предупредить производство некачественных деталей, дает намного лучшие результаты, чем поиск ошибок, которые допускает менее продуманная система.
5.Самые дешевые в краткосрочном аспекте решения в долгосрочной перспективе могут обойтись очень дорого. Решение сэкономить $95 ООО на покупке оборудования для нанесения металлического покрытия позволило сократить капиталовложения на начальном этапе работы, однако привело к увеличению времени
выполнения заказа и росту объема запасов. К тому же оно мешало Acme быстро решать проблемы, поскольку компания не могла повлиять на дефекты, поступающие от поставщика, причем в последнее время количество таких дефектов возросло. Это еще один пример недальновидного мышления, ориентированного на краткосрочные результаты. Ему можно противопоставить мышление, ориентированное на минимизацию общих затрат в течение жизненного цикла изделия.
Вы получаете то, что измеряете! Сколько раз мы слышали эти слова? Если вы измеряете число продуктов, изготавливаемых в течение человеко-часа, вы получаете перепроизводство. Если вы измеряете отклонения от бюджета, вы заставляете людей стремиться увеличить бюджет или сократить затраты, даже если речь идет о выгодных капиталовложениях. Если вы измеряете квартальные прибыли, вы заставляете компанию урезать все расходы в конце квартала, чтобы добиться нужных показателей. Все эти высказывания истинны. Узкий подход, предполагающий оценку изолированных аспектов бизнеса и применение карательных мер к тем, кто не сумеет быстро выдать нужные показатели, ведет к тому, что менеджеры тратят все силы на то, чтобы показатели выглядели наилучшим образом, даже если это идет в ущерб совершенствованию в долгосрочной перспективе.
Есть много хороших книг, рассказывающих о системе показателей бережливого производства. Какие показатели стимулируют совершенствование? С точки зрения высказанных выше соображений о власти вопрос о показателях бережливого производства связан с применением принуждения и вознаграждения. Как заставить людей делать то, что нужно, с помощью показателей, которые обеспечат адекватное применение вознаграждения или карательных мер?
Мы занимаемся обучением и консультированием долгие годы, и вопрос о системе правильных показателей бережливого производства возникает постоянно. Мы неизменно предлагаем представителям компании взглянуть на собственные показатели и задать себе два вопроса: «Какие показатели поощряют нежелательное поведение, идущее вразрез с принципами бережливого производства, а какие ведут к наказанию за правильное поведение?» и «Как привести их в соответствие с показателями, стимулирующими надлежащее поведение?». Это чрезвычайно полезное упражнение. Тем не менее,
ПОДСКАЗКА
Используйте комплекс показателей, который позволяет увидеть проблемы и достижения
Ни для кого не секрет, что любая крупная компания управляется при помощи показателей. Существует ряд показателей, которые рассматриваются как индикаторы благополучия бизнеса, и именно на них ориентируется высшее руководство. Если речь идет о таких традиционных показателях, как отклонение фактического фонда оплаты труда от нормативного, отношение прямых и косвенных издержек и т.п., любое упоминание о бережливом производстве бесполезно. Мы говорим об одном, а измеряем совсем другое. Поэтому необходимо расширить комплекс показателей, которые анализирует высшее руководство. Руководствуйтесь несложным принципом измерять «большую пятерку» показателей: качество, затраты, дисциплину поставок, безопасность и моральный дух. Если / данные показатели измеряются, тенденции в отношении целевых показателей отслеживаются, а высший менеджмент реагирует на отклонение от плана, значит, вы продвигаетесь вперед, держа курс на бережливое производство, главное при этом — избегать перекосов. К примеру, если вы ориентируетесь только на затраты, менеджеры тут же сосредоточатся исключительно на затратах. Если отслеживаются только затраты на рабочую силу, перекос будет еще сильнее. Используйте разнообразные показатели состояния бизнеса и помните, что это всего лишь показатели. Если какой-то из них свидетельствует о наличии проблемы, отправляйтесь на место событий, понаблюдайте за происходящим и разберитесь, в чем подлинная проблема. После этого разработайте контрмеры, которые помогут ее устранить.
когда нас спрашивают, каковы «правильные показатели бережливого производства», мы начинаем беспокоиться, и вот почему.
1.Власть может проявляться не только через вознаграждения и принуждения. Что еще может стимулировать надлежащее поведение? Изменение системы показателей — несложный бюрократический метод управления людьми. Зачастую он просто оправдывает неспособность сформировать подлинное лидерство.
2.Невозможно точно измерить все виды желательного поведения. К сожалению, измеряя модели поведения А, В и С, вы, скорее всего, сконцентрируетесь именно на этих видах поведения и будете уделять меньше внимания моделям D, Е и F, которые могут оказаться не менее важными, но плохо поддаваться измерению.
3.Нас интересует создание мотивации непрерывного совершенствования и инноваций. Если вы держите людей в ежовых рукавицах, контро-
ПОДСКАЗКА
Стандартизированный процесс лучше поддается измерению и совершенствованию
Основной смысл измерения — убедиться в позитивной динамике совершенствования. Если процесс не стандартизирован, эффективное измерение невозможно. Вариация параметров слишком велика, а база сравнения для оценки результирующих измерений отсутствует. Стандартизированный процесс имеет определенные параметры, такие как время такта и поступающие от потребителя сигналы об уровне спроса, а стандартизированное использование ресурсов обеспечивает контроль затрат. Определить, выполняет ли процесс требования, предъявляемые потребителем, очень легко. Голос потребителя представлен визуально. Можно без труда измерить общие затраты, поскольку базовые издержки остаются неизменными, меняется только время. Время выполнения процесса, необходимое для удовлетворения потребителя, варьируется в зависимости от производительности. Что происходит, если вытягивание со стороны потребителя прекращается? Чтобы предотвратить перепроизводство, в соответствии с условиями договоренности процесс должен остановиться. Если мой процесс останавливается, мои затраты растут, а производительность труда падает. А это несправедливо по отношению ко мне, верно? Поэтому, оценивая любой процесс, необходимо учитывать разные показатели. Нужно принимать во внимание стабильность обслуживания потребителя при минимальных затратах. В Toyota, если процесс останавливается из-за того, что прекращается вытягивание со стороны потребителя, никто не винит процесс-поставщик. Все просто «ждут канбан». Операция ожидает поступления очередного сигнала от поставщика, и время ожидания вычитается из доступного для работы времени, поэтому подобный простой не отражается на показателях производительности процесса.
лируя каждый их шаг, скорее всего, вместо новаторского мышления вы получите механическую работу, ориентированную на измеряемые показатели.
4. Нам известно: когда вознаграждение прекращается или у субъекта возникает ощущение, что он не получает заслуженного, мотивация исчезает.
В Toyota мы не знаем никого, кто занимался бы совершенствованием только ради денег или в угоду начальству. Должно быть, такие люди существуют, но мы не можем привести ни одного примера. При этом мы знаем множество людей, которые работают до изнеможения, чтобы сделать что-то во благо компании. Марк Твен с оттенком горечи сказал: «Всегда поступай правильно. Это доставит удовольствие некоторым и удивит всех остальных». Разве не замечательно создать культуру, в условиях которой ваши сотрудники будут совершать удивительные поступки, не оглядываясь на показатели?
В главе 16 Дао Toyota рассказывается о разнообразных факторах мотивации, которые являются неотъемлемой частью работы в Toyota. Речь идет как о внутренней мотивации (упорная работа при решении трудной задачи с обратной связью, свидетельствующей о достижении цели), так и о внешней (похвала или небольшое денежное вознаграждение). Но мы не знаем никого, кто рассчитывает, что за каждую решенную проблему с ним расплатятся звонкой монетой.
Мы видели, какое удовлетворение и волнение испытывают те, кто завершает работу над проектом и получает ощутимые результаты. Желание порадовать потребителя, внести свой вклад в работу команды и сделать Toyota еще сильнее представляет собой мощный фактор мотивации.
Измерить свои достижения в создании обучающейся бережливой организации невозможно, и все же никакое совершенствование невозможно без системы показателей. Лучше всего воспринимать показатели как цели совершенствования. Применительно к бережливому производству уместно вспомнить про правило SMART (см. ниже). Движущей силой любого процесса совершенствования должны быть цели, отвечающие всем пяти параметрам. Следует периодически измерять показатели и наносить их значения на простые и наглядные графики, о которых рассказывалось в главе 14. Не нужно пытаться измерить все аспекты работы группы, завода или менеджера. Занимаясь конкретным проектом по усовершенствованию, рабочая или временная проектная группа и менеджеры ставят амбициозные, но реальные цели в отношении этого проекта, а затем измеряют прогресс в их достижении. Для постановки согласованных целей на всех уровнях, начиная с президента и заканчивая заводским цехом, в Toyota применяется метод хосин канри31, или развертывание политики.
Нас часто спрашивают: «Как удержаться на том уровне, которого мы достигли к настоящему моменту?» Решающую роль здесь играет обычный контрольный листок, используемый при аудите. Единственно возможный способ понять, как удержаться на уровне, достигнутом в результате усовершенствования, — это проверить состояние участка, увидев происходящее своими глазами. Форма на рис. 20-4 предназначена для аудита стан-
ПОДСКАЗКА
Цели и правило SMART
Цели должны быть:
Конкретными (Specific): Джон делает работу х (он — член команды, который отвечает за данную работу)
Измеримыми (Measurable): Джон отслеживает общую эффективность оборудования М7 и держит команду в курсе дела Ориентированными на действие (Action-oriented): Джон возглавляет программу 5S и докладывает о результатах работы
Реалистичными (Realistic): к завтрашнему дню Джон должен подготовить краткие резюме на всех сотрудников Ориентированными во времени (Time-based): Джон возглавляет программу 5S на участке 7 и доложит о результатах 12 июля
дартизированной работы. Она чрезвычайно проста и представляет собой перечень вопросов, на которые нужно ответить «да»/«нет». Аудиты проводятся лидером группы или работником, занимающим аналогичную должность, с заданной периодичностью, например раз в неделю или раз в две недели. Результаты суммируются, и итоговая оценка наносится на график, на котором следует отметить целевой показатель, что позволит судить о прогрессе в достижении цели. На рис. 20-5 представлена форма аудита системы хейдзунка (выравнивания).
Аудит стандартизированной работы в NUMMI несколько сложнее. В цехах стоят большие доски для аудита стандартизированной работы — ка-мисибай (книга историй), напоминающие перфокарты. На доске в вертикальной колонке размещаются карточки — по одной для каждого рабочего места — с перечнем вопросов, требующих ответа «да»/«нет». Лидер группы ежедневно проверяет по одному процессу, наблюдая, выполняет ли член команды то, что написано в карте стандартизированной работы. При необходимости он отмечает выявленные расхождения и записывает контрмеры. После аудита соответствующая карточка вставляется в прорезь справа от основной колонки — это говорит о том, что аудит выполнен. Если в ходе аудита обнаружились проблемы, карточка поворачивается темной стороной наружу, что служит сигналом к принятию мер. Заместитель менеджера ежедневно проверяет состояние досок. Всего на сборочном заводе NUMMI таких досок более 90. Подобные доски используются и для всеобщего ухода за оборудованием. Менеджеры Toyota часто обходят производственные предприятия, проверяя правильность методов работы, применяемых на каждом участке.
Очень часто люди относятся к системам показателей пассивно. Кто-нибудь из представителей высшего руководства просматривает собранные данные, чтобы выявить проблемы и наказать виновного. Хосин канри и доски аудита представляют собой пример активного подхода к показателям. Люди, выполняющие работу, ставят цели, отслеживают прогресс в их достижении и принимают оперативные меры, если целевых показателей достичь не удается. Менеджеры посещают производственные участки для аудитов и общения с теми, кто занимается выполнением работы. Культура многих компаний не предполагает подобного образа действий.
Итак, вопрос в следующем: как создать культуру непрерывного совершенствования, при которой не нужно подстегивать совершенствование с помощью бесконечных измерений, а сознательные работники ставят амбициозные цели и сами отслеживают их выполнение? у
Исследования в области социальной психологии, касающиеся взаимосвязи установок и поведения, имеют давнюю историю. Хотя перечень трудов на эту тему весьма обширен, а терминология сложна, выводы достаточно определенны. Когда людей спрашивают, каковы их убеждения, ответы не всегда позволяют прогнозировать их поведение. К примеру, человек может твердо заявить, что у него нет предубеждений в отношении меньшинств, однако своим поведением может демонстрировать, что такие предубеждения имеются. Обмен информацией и просвещение могут повлиять на форму и содержание высказываний таких людей, но не меняют их поведения.
В то же время, если нам удается изменить поведение, мы можем повлиять и на установки. К примеру, кто-то предпочитает не работать вместе с представителями ряда меньшинств, но если ему все-таки придется работать с ними бок о бок, весьма вероятно, что со временем его установки изменятся. Данный феномен объясняет теория когнитивного диссонанса, которая гласит, что человек стремится привести свои противоречивые представления в состояние гармонии. Работая с представителем меньшинства, мы видим его разумный и плодотворный подход к делу, и эти представления идут вразрез с нашей неприязнью к данному меньшинству. Простейший способ преодолеть несоответствие между данными фактами — изменить негативные установки по отношению к меньшинствам: «Может быть, они не так уж и плохи».
На самом деле все несколько сложнее, однако главное состоит в том, что куда проще изменить мысли людей, повлияв на их поведение, чем изменить их поведение, влияя на их мысли. Если мы хотим, чтобы люди поняли постулаты бережливого производства и заинтересовались им, следует дать им возможность испытать его на себе. Опыт, коучинг и оперативная обратная связь со временем изменят их поведение. В то же время едва ли можно рассчитывать на успешность попыток повлиять на установки людей с помощью зажигательных речей, интерактивных учебных видео-курсов или аудиторного обучения. Возможно, люди начнут говорить правильные вещи, однако это не скажется на их глубинных установках и поведении (см. «Историю двух поршней»).
Таким образом, не стоит рассчитывать, что процесс аудиторного обучения может изменить культуру. Можно научить людей быть политкорректными в высказываниях и выражать свои мысли в самой изысканной форме, однако это не отразится на ценностных ориентациях и убеждениях. Такова горькая правда, хотя, казалось бы, куда проще изменить культуру при помощи образовательной программы, чем перестраивать структуру и процессы организации, чтобы изменить мышление людей. Однако бережливое производство не означает легкого пути. Бережливое производстве требует делать то, что работает. Оно требует признать реальное положение вещей и верить, что реальность можно изменить и тем самым достичь своих целей.
Так стоит вообще беспокоиться о культуре? Как это ни парадоксально вам не удастся напрямую изменить культуру посредством общения и просвещения. При этом именно культура — решающий фактор создания стабильного, конкурентоспособного предприятия. Ее нельзя игнорировать.
В Toyota это поняли давным-давно. Говорят, когда Фудзио Тё разработав схему «дом TPS», иллюстрирующую теорию производственной системы Toyota Тайити Оно разорвал его рисунок. Оно был убежден, что познать TPS можнс лишь на собственном опыте, применяя ее в заводском цеху. Он не верил, чтс люди поймут сущность TPS, разглядывая изображение дома. В Дао Toyoti президент Тё излагает данную философию следующим образом:
Вокруг слишком много непонятного, поэтому мы говорим своим сотрудникам: смелее, действуйте, пробуйте! Взявшись за дело, вы увидите, как мало вы знаете, и наделаете ошибок, но вы исправите эти ошибки и переделаете уже готовое заново. Предприняв вторую попытку, вы совершите новые ошибки и набьете новые шишки и переделаете сделанное еще раз.
С самого начала производственная система Toyota предполагала обучение на практике. Любой, кто участвовал в практическом семинаре по кайдзет или руководил им, представляет глубину полученного опыта и интенсив ность подобного обучения. В течение недели в команде формируется свое го рода микрокультура. Зачастую такая микрокультура ощутимо отлича ется от устоявшейся культуры организации. В рамках этой микрокультуры ценится обмен идеями, дух экспериментаторства и даже совершение ошибок. Группа учится распознавать потери на более глубоком, чем обычно, уровне и обнаруживает, что можно избавиться от потерь, с которыми она так долго мирилась. Опыт такой работы заставляет изменить взгляд на вещи. Нам приходилось слышать следующие высказывания: «Мне просто не верится, что я мирился с этой проблемой в течение 20 лет и ни разу не попытался предпринять хоть что-нибудь». Потери начинают бросаться людям в глаза, и они сознают, насколько лучше могли бы работать. В пятницу устраивается торжество в честь достижений группы, и атмосфера микрокультуры, сформировавшейся в течение этой недели, ощущается еще более остро. А потом часто происходит печальное событие. Наступает понедельник, и все возвращается на круги своя.
Один из недостатков практических семинаров по кайдзен в том, что изменить культуру за неделю невозможно. А когда эта неделя проходит, координатор обычно отправляется на другой участок и проводит другой семинар с другой группой. Подобное краткосрочное наступление на существующую культуру с последующим отступлением не позволяет переменам зайти далеко. Подлинная ценность такого семинара определяется не деньгами, которые позволила сэкономить эта неделя, но потенциалом в сфере приобретения новых навыков и изменения культуры... что часто остается неосознанным.
Проект по совершенствованию потока создания ценности имеет значительно больше шансов изменить культуру в зоне реализации проекта. При этом инструментом работы с потоком создания ценности может быть все тот же практический семинар по кайдзен, однако в этом случае работа уже не заканчивается с наступлением пятницы. Семинар становится частью серии подобных мероприятий, которые продолжаются на протяжении четырех-шести месяцев. После завершения интенсивной работы проект по-прежнему требует серьезного внимания менеджмента, что является условием дальнейшего преобразования культуры. Для формирования культуры бережливого производства, — когда люди понимают, что такое поток, видят потери, без колебаний берутся за их устранение и привыкают к дисциплине, которая обеспечивает стабильность преобразований, — требуется не менее трех лет.
Если вам удается сформировать новую культуру на одном из важнейших участков организации, что следует делать для ее распространения? Надо ли на каждом следующем участке приниматься за дело заново? Ответ — нет. Есть несколько путей передачи знаний и опыта:
1. Если в пилотном проекте участвует менеджмент, это позволяет ему многому научиться. Руководители становятся убежденными сторонниками бережливого производства, а их видение обретает ясность и силу. Все это распространяется и на следующий проект по оптимизации потока создания ценности.
2.Внутренние тренеры по бережливому производству учатся на собственном опыте, что ускоряет работу с каждым следующим проектом.
3.Узнав про пилотный проект, люди, работающие на других участках, приходят посмотреть на происходящее, и увиденное отражается на их мышлении и поведении.
4.Существуют возможности перевода персонала, который участвовал в реализации проекта, на другие участки, в качестве непосредственных носителей новой культуры, а может быть, и в качестве потенциальных тренеров по бережливому производству.
Одним словом, новую культуру могут нести с собой только люди, имеющие непосредственный опыт культурных преобразований и представляющие собой часть этих преобразований. Весьма действенный метод — перевод на новое место рабочих или мастеров. Нередко реализация пилотного проекта позволяет сократить количество рабочих мест, и высвободившихся работников можно перевести на другие участки или направить в отдел кайдзен. Занимаясь преобразованиями, многие менеджеры упускают из виду, что люди, чья должность упразднена, — это не потери, от которых следует избавляться. Такой человек — активный носитель новой культуры, и дело менеджера — всячески способствовать ее развитию. Если использовать такого человека должным образом, он может принести огромную пользу.
В Toyota осознают важность и сложность преобразования культуры Создавая предприятия в других странах, компания придает огромное значение формированию дао Toyota на каждом из них. Эта задача решается с помощью системы координаторов. Тысячи координаторов Toyota работают по всему миру, и их основная обязанность — распространение дао Toyota Для этого мало приехать на неделю-две и провести краткий курс обучения эта работа занимает два-три года и требует ежедневной наставническог помощи. Координаторы ставят перед своими учениками трудные задачи и наблюдая за тем, как они идут к цели, изыскивают возможности для коу чинга.
Нам часто задают один и тот же вопрос: «Может ли дао Toyota работап за пределами Японии, будучи порождением уникальной японской культу ры?» Несомненно, принципы дао Toyota гармонично сочетаются с культу рой Японии, которая весьма своеобразна. Как-никак культура Toyota сфор мировалась в японской среде. Дисциплина, собранность, внимание i деталям, ориентация на работу в команде, преданность компании, систем;
пожизненного найма, медленное и постепенное продвижение по служебной лестнице, склонность к размышлениям (хансей), стремление к совершенству и многие другие особенности национальной культуры поддерживают и укрепляют дао Toyota. Тем не менее Toyota добилась значительного успеха в создании подобной системы на территории других стран. Со временем в компании поняли, что сформировать культуру Toyota за рубежом в том же виде, в каком она существует в Японии, не удастся, поэтому придется адаптировать ее к особенностям местной культуры. Итог такой работы — новая, гибридная культура, которая представляет собой сочетание исходной культуры Toyota и местных особенностей. Однако система ценностей Toyota остается неизменной.
В какой степени такая адаптация изменила оригинальную культуру Toyota — вопрос спорный. Некоторые утверждают, что речь идет о создании совершенно новой культуры. Американцы, к примеру, не желают ставить работу превыше семьи и личной жизни, как часто делают японцы, они не так дисциплинированны в соблюдении стандартных методик, всег-
Свой путь к новой культуре
В главе 19 мы рассказывали о подходе, предполагающем создание собственной производственной системы компании. Обычно при этом имеется в виду создание единой операционной системы в масштабах всего предприятия. Идея сама по себе превосходная, и мы ее горячо одобряем. Проблемы начинаются, если в таком подходе видят метод директивного преобразования культуры сверху вниз при помощи административного ресурса. Чтобы проложить путь к новой культуре, мало презентаций PowerPoint. Все на свете красочные слайды и учебные программы не в состоянии изменить культуру. От голых теорий толку мало. Усвоить новые слова и понятия людям куда лучше поможет непосредственный опыт, глубокие культурные преобразования, затрагивающие руководство, и персонал, который несет с собой новую культуру и обучает ей других. Но одно только обучение и общение не могут изменить установки, чувства и поведение людей. В течение полутора лет мы работали с одним из наших клиентов, занимаясь пилотным проектом образцовой линии, обучая сотрудников пониманию процессов и формируя внутреннюю базу знаний и навыков. Но когда в центральном офисе компании было решено взяться за развертывание бережливого производства, вместо того чтобы привлечь к этой работе участников проекта, в компании отобрали людей без опыта, рассчитывая, что, пройдя теоретический курс обучения, они смогут возглавить преобразования. Это была грандиозная потеря!
да стремятся понять, почему следует выполнять работу так, а не иначе, они индивидуалисты, жаждут личного признания и индивидуальных вознаграждений, нетерпеливы и не любят загадывать далеко вперед. И хотя отчасти приведенные высказывания справедливы, Toyota проделала грандиозную работу по переносу значительной части важнейших атрибутов культуры компании за рубеж, в том числе в Америку. Toyota научила американцев:
•выявлять и устранять потери;
•решать проблемы методами Toyota;
•понимать значение стандартизации как основы кайдзен;
•стремиться к высокому качеству и удовлетворению потребителя;
•сознавать важность работы в команде;
•ценить людей.
Если партнеры являются подлинным продолжением бережливого предприятия, его культура должна распространяться и на них. Вспомним пример компании Denso, который приводится в главе 19. Казалось бы, поскольку Toyota владеет значительной частью компании Denso, которая входит в состав кейрецу, в Denso должны были основательно поднатореть в TPS. Однако здесь пришли к выводу, что уровень TPS в Denso несравним с заводами Toyota. Несмотря на использование ряда технических методов TPS, в компании отсутствует характерный для Toyota образ мышления, ориентированный на кайдзен. В качестве контрмеры был развернут проект «Эффективное предприятие».
Неудивительно, что символ проекта был назван треугольником Такаха-си в честь председателя Denso, который вышел на пенсию как представитель высшего менеджмента Toyota. В Denso одной из его обязанностей было формирование культуры, сравнимой с культурой Toyota. Но под силу ли было Denso угнаться за Toyota, где культуру непрерывного совершенствования поддерживали все сотрудники компании?
Почему Denso, которая успешно выполняла требования Toyota к уровню цен, так старалась не отстать от Toyota? Как мы уже говорили в главе 12, Toyota стремится управлять не ценами, а затратами своих поставщиков. Toyota снижает собственные затраты за счет бесчисленных усовершенствований, которые изо дня в день осуществляют рядовые сотрудники, решая незначительные проблемы. Если поставщики не будут трудиться над снижением затрат столь же интенсивно, все старания будут напрасны. Затраты поставщика окажутся узким местом в процессе. А именно эти затраты составляют значительную часть себестоимости автомобилей Toyota. Если поставщики пойдут на снижение цен, не снижая фактические затраты, они становятся «больными» поставщиками. У них нет наличных средств для реинвестиций в бизнес и перспективные технологии. Если поставщики снижают затраты за счет жесткого обращения с персоналом и собственными поставщиками и тому подобных краткосрочных мер, основная инфраструктура базы снабжения рушится.
В главе 3 мы рассказывали о стабилизации, создании потока, стандартизации и пошаговом выравнивании. Мы говорили, что для связи двух производственных операций необходимо добиться определенного уровня исходной стабильности. После этого можно связать данные операции, обеспечив определенный уровень потока. Это состояние становится новым стандартом, и дает возможность заняться выравниванием. Мы описали спираль непре-рывногоЧовершенствования, которая представляет собой циклическое повторение процесса на все более глубоком уровне. Теперь вместо двух производственных операций представьте себе сборочный завод и завод поставщика, к которым применимы те же принципы. Стабилизировав процесс на каждом из заводов, можно связать их между собой, стандартизировать новый процесс и приступить к пошаговому выравниванию. Этот процесс совершенствования непрерывно повторяется по спирали.
Теперь представим компанию вроде Denso, которая производит запчасти и отправляет их на склад Toyota. Далее представим структурное подразделение Denso, которое занимается разработкой продукции и проектирует системы обогрева, вентиляции и кондиционирования воздуха вместе с инженерами Toyota, работающими над созданием новой машины. А как насчет службы сбыта Toyota, которая продает машины дилерам? Во всех случаях действует единый принцип. Каждый партнер должен выйти на новый уровень стабильности, идя в ногу с Toyota, создать связанный поток, провести стандартизацию, а затем перейти к пошаговому выравниванию. Таков процесс непрерывного совершенствования. Если по уровню стабилизации Toyota значительно превзойдет своих партнеров, процесс остановится.
Toyota хочет, чтобы ее партнеры были независимы, поскольку, если они постоянно оглядываются на Toyota и ждут ее указаний, они никогда не обретут достаточный потенциал, чтобы совершенствоваться самостоятельно. Toyota не может стимулировать совершенствование поставщика, которое позволит ему достичь нужного ей уровня, поэтому представители компании говорят, что очень хорошо, если у поставщика есть собственная система, отличная от TPS. В сущности, такой подход даже поощряется...
до тех пор, пока он работает. Если же возникает серьезная проблема с качеством, или проблема при запуске продукции в производство, или проблема, из-за которой работа в Toyota может остановиться, персонал Toyota без промедления берется за дело и начинает обучать поставщика дао Toyota. Возможно, терминология будет иной, но поставщика будут учить всем тем принципам, которые изложены в этой книге. Наш опыт говорит о том, что поставщики Toyota полны желания учиться, поскольку знают, что это оптимальный путь.
Таким образом, чтобы изменить не только внутренние процессы, но и своих партнеров и сделать ваши культуры совместимыми и взаимодополняющими, необходимы следующие условия:
1)вы должны осуществить серьезные внутренние преобразования;
2)вы должны взрастить лидеров, за которыми охотно пойдут ваши поставщики и у которых они будут учиться;
3)вы должны проявлять терпение, обучая поставщиков;
4)поставщики должны стремиться учиться у вас;
5)поставщики должны видеть ценность, которую добавляет им обучение;
6)со временем независимость поставщиков должна расти, в перспективе они должны сформировать собственную культуру бережливого производства.
Повторяем, Toyota хочет, чтобы поставщики имели собственную культуру. Но ей нужно, чтобы эта культура была совместима с ее культурой, а это
Не опережайте события при обучении поставщиков бережливому производству
Трудно переоценить, насколько важно осуществить серьезные преобразования внутри, прежде чем браться за обучение бережливому производству поставщиков. Нам случалось видеть смехотворные ситуации, когда крупные компании, поигрывая мускулами, принимают решение просветить «маленький народец» — своих более мелких, «отсталых» поставщиков, даровав им бережливое производство. Проблема в том, что крупный и могущественный потребитель не идет дальше разговоров о бережливом производстве, бесконечных презентаций PowerPoint и ограниченного применения нескольких моделей. При этом поставщики будут упорно осваивать бережливое производство и значительно опередят своих потребителей. Когда потребители сначала пытаются учить поставщиков бережливому производству, а потом просят снизить цены, это равносильно охоте и собирательству.
значит, что поставщики должны применять базовые принципы дао Toyota. Так, если культура поставщика предполагает традиционную обработку крупными партиями и командные методы управления, ее затраты будут высоки, а работа с ней — чревата потенциальными сбоями. Toyota едва ли станет мириться с такой ситуацией. Однако если поставщик создал собственную, эффективную версию культуры бережливого производства, в Toyota это точно оценят.
Компания Delphi, о которой рассказывалось в главе 12, только приступает к созданию расширенного бережливого предприятия по образцу Toyota вместе со своими поставщиками. Представители высшего руководства Delphi, которые отвечают за снабжение, понимают, что решающий фактор успеха — это доверие поставщика. Стремясь решить эту задачу, они включили в перечень важнейших показателей результативности данные опросов поставщиков. Delphi заключила контракт с компанией Planning Perspectives, которая опрашивает поставщиков всех ведущих автомобилестроительных компаний, и попросила провести опрос поставщиков второго уровня. Результаты опроса за 2004 год были не слишком обнадеживающими. Поставщики считали, что Delphi не принадлежит к разумным и справедливым потребителям, которые заслуживают доверия. Это не было для Delphi неожиданностью, поскольку она долгие годы терпела произвол потребителей и в свою очередь была вынуждена весьма жестко обходиться с поставщиками. Теперь нужно было изменить антагонизм на взаимовыгодное сотрудничество. Delphi решает эту задачу с каждым из поставщиков в отдельности. Компания начала с того, что направила к поставщикам лучших экспертов по бережливому производству — как приглашенных консультантов, так и своих сотрудников,— чтобы помочь поставщикам сделать свои процессы бережливыми. Это начинание имело большой успех и стало первым шагом в завоевании расположения поставщиков. Разумеется, должно пройти некоторое время, прежде чем большинство ведущих поставщиков Delphi начнут всецело доверять своему потребителю, но в Delphi готовы вкладывать средства в развитие этих отношений и ждать, поскольку на становление расширенного бережливого предприятия нужны годы. Здесь делают все, чтобы со временем обеспечить совместимость культур и сформировать доверительные отношения как в самой компании, так и со своими партнерами — поставщиками.
Когда Дэвид Майер работал на заводе Toyota в Джорджтауне, его часто просили «сделать все, что в его силах». Это было скорее просьбой, чем приказом. В Toyota считают, что каждый должен делать все возможное, не щадя своих сил. Не нужно обсуждать, что «хорошо», «плохо», «истинно» или «ложно». Работники просто стараются сделать все, что они могут. И это все, что от них требуется. Мы думаем, что подобная просьба уместна в любой компании, которая решает непростую задачу внедрения одной из версий дао Toyota. Каждый должен делать все, что в его силах.
Нередко Дэвида просили: «попробуй, пожалуйста», а если он по каким-либо причинам не выполнял эту просьбу, ему говорили: «просто сделай». Нередко люди боятся экспериментировать из страха совершить ошибку или из боязни, что их поймут превратно. Одно можно сказать наверняка: не ошибается тот, кто ничего йе делает. Когда речь шла о сложной задаче, превышающей возможности Дэвида, ему советовали «попробовать». Это один из лучших советов в мире. Прежде чем вы сможете по-настоящему оценить значение или пользу рекомендаций, которые даны в этой книге, нужно просто попробовать.
Если вам нелегко заставить себя и других экспериментировать, тогда «просто делайте». Лишь после нескольких подобных случаев Дэвид открыл для себя смысл философии TPS. Другого пути постичь ее нет. Прийти к ее пониманию можно только через опыт. Мы любим предлагать компаниям, которые только что познакомились с какой-либо концепцией, опробовать ее на деле и поразмыслить о результатах, чтобы узнать больше, а потом поэкспериментировать с ней еще и еще раз. В Toyota неизменно поощряют людей к эксперименту, к совершенствованию, к непрерывному росту и развитию.
Иногда простейшее наставление открывает нам глубочайшие истины. За годы работы нам посчастливилось иметь дело с множеством блестящих учителей дао Toyota. Нередко их уроки давались нелегко. Как-то раз наставник Дэвида, мистер Такеути, настойчиво потребовал, чтобы Дэвид выполнил задание немедленно. Дэвид был очень занят, и его внимание было поглощено другими делами. Он сказал, что сделает то, что требует Такеути, через несколько недель («Ammo дэй», — сказал он по-японски, что в переводе означает «позже»). Однако Такеути мягко повторил, что Дэвид должен выполнить его просьбу немедленно — има по-японски. Этот поединок продолжался довольно долго, Дэвид твердил, что сделает работу позднее, Такеути настаивал на своем. Нужно сказать, что, упорствуя в своих требованиях, мистер Такеути был весьма терпелив. Однако в конечном счете настойчивость взяла верх над терпением. Он жестом пригласил Дэвида зайти в ближайший зал заседаний, где стояла белая доска, нарисовал лестницу (рис. 20-6) и сказал: «Дэйв-сан, мы должны каждый день подниматься чуть выше».
Потом он нарисовал стрелку параллельно ступеням и сказал: «Тогда со временем мы будем наверху!» (рис. 20-7).
Ценность такого урока часто осознается не сразу. В ту минут Дэвид хотел одного — чтобы Такеути оставил его в покое, — поэтому он уступил. Лишь некоторое время спустя Дэвид понял, какой глубокий смысл стоял за этими простыми словами. Toyota стремится изо дня в день одерживать небольшие победы. Если это удается, со временем компания становится сильнее. Обязанность лидера — позаботиться о том, чтобы каждый ежедневно вносил в общее дело свою лепту, как бы она ни была мала. Со временем эти совокупные усилия непременно позволят компании подняться на более высокую ступень. Дэвид понял, как тесно связан этот принцип с философией Toyota, предполагающей мышление и планирование с учетом долгосрочной перспективы. В Toyota настроены на долгий путь. Они знают, что черепаха, которая методично движется вперед, не только придет к финишу, но и непременно обгонит стремительного, но легкомысленного зайца.
Прежде чем будет видна очередная ступенька или потенциальная выгода от движения вперед, надо сделать первый шаг. Мы уже говорили об этом раньше, но повторим еще раз. Представьте, что вы стоите на лестнице. Если вы посмотрите перед собой, вы увидите лишь ее часть. По мере продвижения вперед перед вами откроются новые возможности (рис. 20-8).
Все это относится и к процессу изменений. Не сделав первых шагов, вы не увидите потенциальных возможностей совершенствования. По мере движения вперед вы будете неожиданно открывать возможности, которые не видели ранее. Таков парадокс: стоя на месте, вы не увидите, куда идти. Это естественный процесс обучения на собственном опыте. Отправившись в путь, вы будете ориентироваться по ходу дела.
К сожалению, людям нелегко решиться на эксперимент, поскольку они боятся потерпеть неудачу. Профессор Мичиганского университета Фиона Ли и ее коллеги занимаются изучением феномена экпериментирования32. Они проводили психологические эксперименты, чтобы проверить, хочется ли испытуемому преодолеть лабиринт, после того как, опробовав ряд альтернативных вариантов, он приобрел определенный опыт успехов и неудач. Лабиринт представлял собой ковер, расчерченный на квадраты, под каждым из которых находился электронный датчик. Если испытуемый наступал не на тот квадрат, раздавался резкий звуковой сигнал. Методом проб и ошибок, периодически делая неверные шаги, о которых оповещали звуковые сигналы, испытуемый мог постепенно нащупать правильный путь и выбраться из лабиринта. Однако исследователи обнаружили, что нередко люди застывали на месте и не желали двигаться вперед, боясь услышать очередной сигнал. В какой-то мере здесь сказывается влияние культуры. Американцы, воспитанные в духе индивидуализма, не любят делать ошибки. Неудача — позорное клеймо несостоятельности, поэтому американская культура препятствует экспериментам и попыткам сделать что-то новое и не стимулирует размышлять о совершенных ошибках и обращаться за помощью — даже если человек остро нуждается в помощи и тот, кто может помочь, находится рядом. Ли подтвердила это на примере действий квалифицированных американских специалистов, причем представители обоих полов вели себя примерно одинаково.
Постепенные изменения, которым учился Дэвид, могут вызывать страх. Каждый день нужно делать что-то новое. Каждый день нужно рисковать. Рисковать сделать ошибку. Это может объяснить и другой феномен, с которым нам пришлось столкнуться. Когда мы начали заниматься консультированием других компаний, нас часто спрашивали: «Есть ли компании, похожие на нашу, которые уже освоили бережливое производство, и если да, не могли бы мы посетить их?» Доходило до того, что клиенты интересовались, нет ли у нас на примете компании, которая тоже занимается мелкосерийным производством декоративных сидений-крышек для унитазов, или мастерской по изготовлению зубных протезов, или лаборатории, которая выполняет особые анализы крови, или автоматизированного стекольного завода, или еще бог знает каких специализированных предприятий. К сожалению, не все виды компаний в мире имеют собственную модель бережливого производства — помимо Toyota и ее поставщиков таких моделей совсем немного. На самом деле наши клиенты хотят сказать: «Прежде чем мы возьмемся за дело, опишите мне во всех подробностях, каким станет мой бизнес». Нам задают и такой вопрос: «Во что нам обойдется освоение бережливого производства и какую экономию оно нам даст?» То есть дайте нам точные цифры, чтобы мы знали, чего ожидать, и не рисковали напрасно. Именно страх пройти этот путь шаг за шагом, продвигаясь все дальше в неизведанное, — причина того, что примеров успешного освоения бережливого производства так немного. Чтобы преодолеть этот страх, нужна вера.
В ходе своих экспериментов Фиона Ли и ее коллеги сделали еще одно любопытное открытие. Непоследовательность в отношении риска убивает стремление к инновации. Люди готовы рисковать, если будут выполнены два условия: (1) их не накажут за ошибку и (2) ошибка считается допустимой или даже приветствуется. Интересно, что, если на словах риск поощряется, но людей все-таки наказывают, или если людей не наказывают, но предупреждают, что ошибаться недопустимо, они экспериментируют менее охотно и чаще ведут себя пассивно. Самое любопытное: когда людям говорят, что идти на риск нельзя и, если они предпримут такую попытку, их ждет наказание, они идут на риск значительно чаще, чем когда соответствующие заявления отличаются непоследовательностью. Вот что удивительно. Оказывается, нет ничего хуже непоследовательности.
Многие организации, с которыми мы работали, отличаются крайней непоследовательностью. Эксперименты поощряются во время семинаров по кайдзен, но не в повседневной работе. Высший менеджмент превозносит преобразования, а менеджеры среднего звена, как и раньше, твердят о производительности и наказывают подчиненных за любое нарушение нормального хода производства. Менеджмент рассуждает об остановке производства для устранения проблем и повышения качества, а рабочим говорят, что они должны разбиться в лепешку, чтобы обеспечить выработку. Руководители говорят о том, что инновация и эксперимент — это прекрасно, но при этом наказывают людей за ошибки. Все это ставит под угрозу ощущение личной компетентности и самоценности, которыми так дорожат в западном обществе.
Все, о чем мы говорили, — непросто и весьма рискованно. Мы догадываемся, что Дао Toyota и Практика дао Toyota могут привести читателя в
Последовательность влияет на поведение
В главе 11, рассказывая о непрерывном совершенствовании в Toyota, мы говорили о том, что последовательность играет решающую роль в определении мышления и образа действий. Мы видели, как многие компании, пытаясь заниматься непрерывным совершенствованием, устанавливают множество критериев, которые определяют, «приемлемо» усовершенствование или нет. Многие усовершенствования игнорируются, поскольку непонятно, достойны ли они того, чтобы ими заниматься. Так благое начинание заходит в тупик, а инновация гибнет. Если вы заявляете, что стремитесь к непрерывному совершенствованию, оно должно быть непрерывным в буквальном смысле слова, в любое время, при любых условиях, безотносительно к величине выгоды, сложности или значимости. Не бывает слишком мелких усовершенствований, и оптимальный момент для их внедрения — прямо сейчас.
некоторое замешательство. Перед ним открываются потрясающие возможности, но ведущий к ним путь долог и тернист. Нужно добиться изменения культуры и учесть все аспекты каждого процесса. Однако размышляя таким образом, вы не сдвинетесь с места. Вам останется лишь разглядывать ступени, которые ведут вверх, или, что и того хуже, глядеть себе под ноги, изучая ступень, на которой вы стоите. Лучший совет, который мы можем вам дать: «Беритесь за дело»... и «сделайте все, что в ваших силах». Помните, что каждый день нужно подниматься чуть выше!
На этот раз вам придется поразмыслить над самым важным вопросом. Задумайтесь, насколько серьезны ваши намерения взяться за освоение бережливого производства. В этой книге мы постарались дать вам полную и подробную картину такой работы. За ней стоит нечто большее, чем техническое трюкачество многих программ по бережливому производству. Чтобы сформировать культуру непрерывного совершенствования, нужна подлинная приверженность делу, которое требует целой жизни. Готовы ли вы к этому? Этот вопрос можно задать как новичку в бережливом производстве, так и тому, кто занимается им уже десяток лет, но еще не постиг глубин дао Toyota. Задайте себе следующие вопросы и отправляйтесь тем путем, который изберете. Мы говорим «вы», имея в виду не только читателя этой книги, но и критическую массу руководителей.
1.Есть среди высшего руководства вашей организации подлинные приверженцы создания обучающегося бережливого предприятия? Если нет, можно ли рассчитывать на их обучаемость?
2.Готовы ли вы посвятить себя этому процессу надолго (навсегда)?
3.Что вы должны предпринять, чтобы подготовить себя к этому процессу?
4.Готовы ли вы взять на себя обязательства по обучению, внимательному наблюдению (генти генбуцу) и участию в непрерывном совершенствовании?
5.Как вы будете обучать других? Располагаете ли вы инструментами, предназначенными для этой цели?
6.Каким образом ваша организация может заручиться поддержкой сэнсэя, необходимой для преобразований?
7.Характерны ли для вашей организации непоследовательные, противоречивые установки? Если да, разработайте план, который позволит приступить к распространению последовательных установок.
8.Какие изменения культуры необходимы, чтобы выработать единые, последовательные установки?
ДОКТОР ДЖЕФФРИ ЛАЙКЕР — профессор кафедры организации и инженерного обеспечения производства Мичиганского университета, директор Japan Technology Management Program Мичиганского университета, автор бестселлера «Дао Toyota: 14 принципов менеджмента ведущей компании мира», который в 2005 году получил премию Сигео Синго и звание «Книги года» на ежегодном книжном конкурсе, проводимом Институтом организации производства. Джеффри Лайкер — лауреат трех премий Синго (1995, 1996 и 1997 годов). Доктор Лайкер был редактором книги «Стать бережливым: Опыт американских производителей» {Becoming Lean: Experiences of U.S. Manufacturer), которая в 1998 году получила премию Сигео Синго за выдающиеся достижения в исследованиях производства, и автором книг «Спроектировано в Японии» (Engineered in Japan), «Параллельное проектирование: интеграция разработки в различных организациях» (Concurrent Engineering Effectiveness: Integrating product development across organizations) и «Переделано в Америке: Распространение и трансформация японских методов производства» (Remade in America: Transplanting and Transforming Japanese Manufacturing Methods). Его последняя книга — «Результативная разработка: Как Toyota объединяет людей, процессы и технологии для создания бережливой системы разработки продукции» (High Performance Product Development: How Toyota integrate people, process and technology to create a revolutionary lean product development system) написана в соавторстве с Джеймсом Морганом. Доктор Лайкер активно пропагандирует свои идеи, читая лекции, в том числе на выездных заседаниях высших руководителей, и консультирует в области бережливого производства — самостоятельно или как соучредитель Optiprise, Inc. Среди его клиентов DaimlerChrysler, Metalsa, Danfoss, Rio Tinto Mining, Caterpillar Asia Pacific, Benteler Automotive, Amcor, Federal Mogul, PPG Industries, Johnson Controls, Tenneco Automotive, Framatome Technologies, Northrop Grumman Ship Systems, авиабаза в Джексонвилле, ВВС США и судостроительный завод ВМФ в Портсмуте.
ДЭВИД МАЙЕР одним из первых смог изучить TPS на заводе Toyota в Джорджтауне, штат Кентукки, где он был лидером группы. В Toyota Дэвид работал в подразделении по литью пластмасс. Более десяти лет — ив США, и в Японии — он учился у экспертов по TPS, в числе которых были японские координаторы, работающие на постоянной основе. Оставив Toyota, Дэвид основал Lean Associates, Inc., консультационную фирму, которая оказывает помощь во внедрении TPS.
Дэвид написал две главы книги «Бережливое производство: руководство для мастеров» (Lean Manufacturing: A Plant Floor Guide). Более восьми лет он работает лектором и тренером. Дэвид проводил презентацию практических семинаров по стандартизированной работе, составлению карт потока создания ценности и введению в основы бережливого производства для Общества инженеров-технологов США и на конференции по случаю вручения премии Сигео Синго. Дэвид консультировал компании из многих отраслей, в том числе автомобилестроительной, аэрокосмической, производства изделий из дерева и пластмасс, химической и металлообрабатывающей, а также сварочные и сборочные производства. Среди его клиентов были как производственные, так и сервисные компании. На деле показывая результаты TPS, он помогает компаниям сформировать базу знаний и навыков, необходимых для освоения бережливого производства.