Практика дао Toyota. Руководство по внедрению принципов менеджмента Toyota Лайкер Джеффри
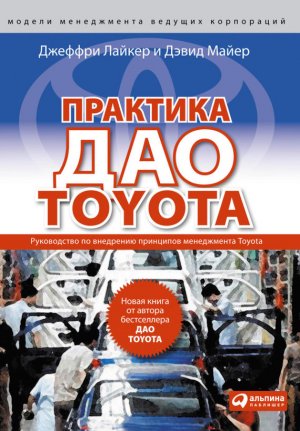
Одно из основных преимуществ потока и четкого соглашения заключается в том, что теперь последствия проблем делаются явными. Если в примере, приведенном выше, средства визуального контроля свидетельствуют о постоянном отклонении от условий договора, значит, возникла очередная проблема.
Отклонение явным образом свидетельствует о наличии скрытой проблемы, требующей решения. В такой ситуации менеджеры часто сетуют: «Они прекрасно знают, что делать, но мы не можем заставить их работать, как положено». Многие менеджеры совершают ошибку, обвиняя оператора в несоблюдении правил, хотя на самом деле своими действиями оператор компенсирует проблему, которая нуждается в решении. Остановитесь и постойте в кругу, чтобы определить, какой недостаток компенсирует оператор.
Обычно у подобной ситуации есть две причины. Во-первых, нужно убедиться, что условия договора представлены визуально в понятном для всех виде; во-вторых, проверить, нет ли дополнительных проблем, которые оператор вынужден обходить.
Основными причинами отклонений в работе оператора являются:
1.Дисбаланс времени рабочего цикла отдельных операций, причиной которого может быть нормальная вариация объема работ, квалификации оператора или продолжительности цикла работы станка. Обычно от правил отклоняется тот, у кого остается лишнее время.
2.Периодические простои из-за отсутствия деталей (или опасения, что детали закончатся). Операторы покидают рабочую зону, чтобы взять на себя выполнение дополнительных функций — например, принести детали или проверить их качество. Приостановка работы из-за отказов оборудования или исправления дефектов.
3.Периодические приостановки из-за трудностей в работе с оборудованием или зажимными приспособлениями, а также при выполнении слишком сложных операций.
4.Разнообразные причины, например стремление создать задел, чтобы выиграть время для переналадки, иногда оператор по какой-либо причине покидает линию, отправляется на обед или перерыв по скользящему графику, а также иные причины подобного рода.
В ряде ситуаций имеет смысл корректировать объем незавершенного производства в зависимости от операции. Поток единичных изделий требует безупречно сбалансировать продолжительность операций, что представляет собой чрезвычайно сложную задачу. Представьте себе операцию, например снятие заусенцев с детали, изготовленной литьем под давлением, для которой вариация времени рабочего — обычное дело.
Время цикла будет слегка варьироваться каждый раз, поскольку по большей части мы имеем дело с операциями, выполняемыми вручную, и никто не способен многократно пройти рабочий цикл за один и тот же отрезок времени (даже участники Олимпийских игр не могут дважды пробежать одну и ту же дистанцию с одинаковым результатом). Эта незначительная вариация может вызывать периодические сбои в потоке. Операторы не любят стоять без дела, и чтобы компенсировать проблему, они начинают нар а-щивать буферные запасы. Наращивание буферных запасов является вполне логичным выбором для компенсации незначительной вариации времени; однако объемы наращивания следует ограничить стандартом. При этом оговоренные размеры буфера, компенсирующие незначительную вариацию времени, должны составлять не более двух-трех единиц продукции.
ПОДСКАЗКА
Польза взгляда со стороны
Зачастую трудности общения вызваны тем, что нам сложно
— «j/ осознать, почему другие не понимают, казалось бы, очевидных вещей. Смысл договора о стандартных условиях — обеспечить единое понимание этих условий всеми и каждым. Чтобы проверить, насколько вам это удалось, найдите человека, незнакомого с рабочей зоной, покажите ему стандарт и попросите объяснить суть договора. Вы удивитесь, увидев, как сложно донести информацию об условиях договора при помощи визуальных средств!
Рассматривая более сложный пример, мы увидим, что и здесь за основу берутся те же самые концепции. В нашем случае производятся три разные модели продукции — 1, 2 и 3 — и нужно обеспечить гибкость, которая позволит в любой момент изготовить одну из этих моделей. Схема организации
Предположим, на операции С требуется изготовить модель 2. Оператор берет одно изделие с заданного места между операцией В и операцией С. По условиям договора это служит сигналом для операции В: пустое место — это сигнал, и когда потребитель вытягивает изделие, следует подать на это место следующее, т. е. изготовить деталь для модели 2. Теперь ситуация соответствует рис. 5-7.
После этого операция В забирает деталь 2, которая находится между операциями А и В, что побуждает операцию А приступить к изготовлению детали для модели 2. По завершении работы операция В восполняет запас между операцией В и операцией С. Теперь картина соответствует рис. 5-8.
Разумеется, это упрощенная модель, однако здесь выполняются все три необходимых условия и их соблюдение поддерживается с помощью визуальных средств. Эта базовая модель применима при производстве продукции в больших объемах или небольшого ассортимента, а также при работе с запасами. Ее основное преимущество — гибкость, которая позволяет изготовить любую модель в любой момент времени и быстро переключаться с одной модели на другую.
Рассматривая несложную модель (рис. 5-8), которая предполагает производство всего трех видов деталей, многие думают, что широкий ассортимент изделий при производстве на заказ не позволяет использовать систему вытягивания. Такое убеждение опирается на ошибочное предположение, что, когда на операции С изготавливается конкретная модель, предыдущая операция (В) получает сигнал вытягивания, с тем чтобы изготовить деталь для той же самой модели. Если на операции С работают с деталью типа «1», значит, В должна возместить деталь, использованную для «1».
Что происходит, если вы работаете с тысячами разных деталей и некоторые из них используются не чаще раза в месяц? При широком ассортименте или производстве на заказ сигнал о том, что изготавливать дальше (индивидуальный заказ), поступает не на операцию С, а на операцию А. По завершении операции А деталь передается на операцию В. После обработки детали на операции В она передается на операцию С. Таким образом, работа «протекает» через последующие операции. Не забывайте, что поток и вытягивание — это не одно и то же. Принято думать, ч.то, если предписание о производстве изделия поступает в начало линии (операция А), значит, работа должна выталкиваться на операцию В и операцию С.
Давайте вернемся к отличиям вытягивания от выталкивания. Первым отличием является четкий договор между двумя сторонами. Существует ли такой договор между операцией А и операцией В в случае производства изделий на заказ? Да, его условием по-прежнему является обработка изделий по одному. Второе отличие требует, чтобы условия договора закрепляли за изделиями определенное место. Это место закрепляется по тому же принципу, что и в предыдущем примере. Третье отличие требует обеспечить контроль соблюдения условий данного договора (стандарта) в процессе производства. Каким образом осуществляется контроль производства? Все так же, с помощью визуальных средств.
В чем разница с примером, рассмотренным ранее? Единственное различие в договорах — условие о том, чего хочет потребитель. Объемы производства остались прежними, но как быть с моделью? Процессы-потребители (В и С) не определяют, какую модель будет изготавливать процесс-поставщик. Условие договора заключается в следующем. Каждая операция обрабатывает изделия в последовательности, заданной предшествующей операцией. Это называется последовательным вытягиванием или последовательным потоком.
На рис. 5-9 показан последовательный поток в условиях высокого разнообразия типов продукции. График задается для операции А, на которой уже были изготовлены модель 2, модель 1 и еще одна модель 2; следующим изделием по графику является модель 3. Поскольку между операцией А и операцией В есть свободное место, А может приступать к изготовлению следующего по графику изделия. Правила вытягивания остаются в силе — если место между А и В занято, операция А не может приступить к изготовлению очередного изделия. По правилам, если место между операцией-по-ставщиком и операцией-потребителем занято, операция-поставщик может заниматься обработкой детали, но не может передать ее дальше. Деталь остается на рабочем месте. В результате операция В по-прежнему определяет, что делать (изготавливать ли очередное по графику изделие) и когда (когда освобождается место). Если обработка детали на операции В завершится раньше, чем поступит сигнал (освободится место) перед операцией С, оператор держит ее на рабочем месте до поступления сигнала с операции С.
В условиях широкого ассортимента уровень гибкости ограничен временем выполнения заказа на отрезке, который начинается точкой формирования графика и заканчивается конечной операцией по изготовлению продукта. Время выполнения заказа определяется количеством операций, которые проходит продукт. Внесение изменений в график не означает немедленных изменений на выходе процесса из-за задержки, соответствующей продолжительности прохождения потока.
Чтобы такой поток работал без сбоев, каждый оператор должен быть готов в любой момент изготовить любую модель. Часто самая трудная задача при создании последовательного потока в условиях производства на заказ — сбалансировать продолжительность операций. В предыдущей главе приводился конкретный пример того, как снизить высокий уровень вариации, характерный для производства на заказ, и как сбалансировать работу, сгруппировав операции с учетом их продолжительности.
Что, если безупречно сбалансировать время цикла операций А, В и С невозможно? Первым делом спросим: «Может ли каждая из этих операций стабильно выполнять стоящую перед ней задачу быстрее, чем требует потребитель, т. е. быстрее времени такта?» Если, исходя из средних значений, на этот вопрос можно ответить да, но операция часто не укладывается во время такта из-за вариабельности, значит, необходим буферный запас. Буфер не должен быть неуправляемой системой выталкивания. Его можно обозначить визуально, при помощи маркировки, которая будет определять допустимое между операциями количество единиц продукции, например три изделия между смежными операциями. При этом следует соблюдать принцип ФИФО («первым вошел — первый вышел»), чтобы в поток не могли вклиниться детали со стороны.
Теперь мы видим, что поток и вытягивание действуют рука об руку. Для создания системы вытягивания необходимы три составляющих, которые обеспечивают связь между операциями. Эта связь важна для выявления проблем. Она ведет к созданию единого процесса, все операции которого взаимозависимы. Это заставляет безотлагательно устранять помехи потоку. Если на какой-то операции возникает проблема, это немедленно сказывается на остальных операциях. Попытки обойти проблему за счет перераспределения ресурсов и оборудования или изменения графика вызовут дополнительные проблемы в системе в целом, поскольку все операции взаимосвязаны.
Исходя из такого понимания основ вытягивания, можно создать систему, которая будет работоспособна в любой ситуации. Модель потока единичных изделий, описанная выше, применима на линиях или ячейках, где работники передают продукт по цепочке.
Как применить эти принципы к операциям, которые разделены физически, или к процессам обработки деталей партиями? Прежде всего важно понять особенности, заложенные в самой природе операции. Те, кто имеет опыт работы с TPS, понимают, что всегда есть операции, которые по той или иной причине нельзя организовать как поток единичных изделий. Дело может быть в размерах деталей (очень крупные или мелкие), общих ресурсах (несколько поставщиков и/или потребителей) или ограничениях процесса (например, время переналадки).
Так, процессы штамповки в Toyota на сегодняшний день не позволяют изготавливать сначала крыло, потом капот, а потом вновь крыло. Операция штамповки имеет множество ограничений, препятствующих потоку единичных изделий, и изделия на этом участке производятся партиями. Во-первых, габариты оборудования не позволяют поместить его рядом с операцией-потребителем (участком сварки кузовов). Во-вторых, штамповочный пресс («общий ресурс») производит разные виды деталей, которые необходимы разным потребителям (крыло и капот устанавливаются на разных участках), а значит, невозможно разместить оборудование вблизи от всех потребителей. К тому же, хотя время переналадки весьма мало, оно накладывает ограничения на переключение с одной детали на другую.
Как в такой ситуации реализовать базовые концепции определенности, закрепления и контроля? Для начала уясните условия договора между поставщиком и потребителями. Поставляйте нужный материал по требованию. Все операции должны придерживаться основного правила: «Всегда удовлетворяй потребителя», иными словами, «Не допускай, чтобы у потребителя были недостачи». Это правило номер один. Всегда соблюдайте правило номер один! (Здесь имеет место парадокс. Хотя задача состоит в постоянном удовлетворении потребителя, ранее мы отмечали, что в процессе, который никогда не останавливает операцию-потребитель, по всей вероятности имеет место избыток потерь.)
Четко ли сформулированы условия договора? Первым делом нужно определить количество незавершенного производства между поставщиком и потребителем, которое позволив компенсировать время переналадки оборудования поставщика и обеспечить продуктом очередного потребителя. Многие операции в настоящее время имеют договоренности с весьма размытыми условиями (не представленными наглядно и не контролируемыми), и будет очень полезно начать с определения объема буферного запаса.
Определено ли место для запаса незавершенного производства? Закреплено ли оно за данным запасом? Промаркировано ли надлежащим образом? Маркировка должна содержать информацию о допустимом максимуме и минимуме. Превышение максимума служит наглядным свидетельством перепроизводства, а приближение к минимуму служит «сигналом раннего предупреждения» о возможной проблеме с поставкой, которой следует заняться заранее (выяви потенциальную проблему до того, как она стала проблемой). Закреплены ли за материалом контейнеры для транспортировки? Б нашем примере со штамповкой для каждого вида деталей сконструированы специальные контейнеры. Крыло нельзя уложить в контейнер для капота.
Последняя составляющая — это визуальное оповещение о нуждах потребителя. Если процесс-потребитель находится за пределами видимости, следует создать механизм, который позволит визуализировать потребности потребителя и статус операции. Канбан — именно такой визуальный механизм передачи сигнала от потребителя к поставщику. Для связи с поставщиками, которые в течение дня регулярно присылают грузовики с комплектующими, в Toyota принято использовать карточки канбан. Карточки, которые возвращаются от потребителя, оповещают о расходах материала. Они наглядно воплощают условия соглашения, касающиеся объемов незавершенного производства. Количество карточек, накопившихся у поставщика, представляет собой величину, обратную объему незавершенного производства. Чем больше канбан вернулось к поставщику, тем меньше запасы незавершенного производства у потребителя.
Мы не собираемся подробно описывать, как работает механизм канбан, однако понять его основные принципы несложно. Канбан — это механизм контроля перепроизводства. Это может быть участок свободного места на полу, если два оператора работают рядом. Если потребитель и поставщик не видят друг друга, это может быть карточка, пустой стеллаж или электронный сигнал. Информация, которую содержит канбан, должна соответствовать условиям соглашения и включает сведения о местоположении поставщика и потребителя, используемом оборудовании, материале и, разумеется, количестве и виде изделий.
Вернитесь к приведенному выше примеру потока единичных изделий. Каким образом операция В узнает о том, что операция С нуждается в очередной модели 1? Операция С забирает соответствующую деталь, и пустое пространство служит для операции В сигналом о необходимости восполнения запаса. Функцию канбан выполняет пустое место, которое визуально оповещает о количестве и виде изделий. Любая система канбан представляет собой производную этой базовой концепции.
Конкретная ситуация: стыковка операций для выявления потерь при разработках
Поставщик сидений для автомобилей имел весьма замысловатую процедуру разработки новых изделий, включающую многочисленные межпроцессные проверки. Каждый этап разработки автомобиля был
расписан до мелочей. Критерии межпроцессных проверок при проектировании продукта были предельно четкими, и если в ходе проверки конструкторское решение не удовлетворяло заданным критериям, оно не передавалось на следующий этап процесса. Все были обучены данному процессу и знали, что и когда следует делать.
Один из наших сотрудников работал с этой компанией в качестве консультанта и, занимаясь составлением карты потока создания ценности для текущего состояния процесса, обнаружил, что реальная ситуация с межпроцессными проверками не соответствует процедуре, описанной на бумаге (подобные открытия случаются нередко). Постоянные проволочки и задержки порождали заторы в системе и препятствовали потоку. Была разработана концепция будущего состояния, после чего началась работа по стабилизации подпроцессов, а затем их предварительное связывание.
Одним из узких мест в существующем процессе был этап изготовления и испытаний опытных образцов. Разрабатывалась конструкция сидений, заказывались комплектующие, изготавливались и испытывались сотни опытных образцов.
Когда была составлена карта процесса, стало видно, что это классический случай обработки партиями и выталкивания по графику (см. рис. 5-10). Сначала полностью разрабатывалась конструкторская документация на все сиденья — сиденья с подогревом, сиденья без подогрева, многоместные сиденья, сиденья для водителя, электрический привод сиденья и т.д. На основании разработанной документации заказывались комплектующие. Комплектующие поступали от поставщиков в разное время. Группа, которая изготавливала опытный образец, ждала поступления комплектующих сколько могла, после чего приступала к изготовлению тех сидений, которые можно было сделать из имеющихся комплектующих. После этого сиденья огромными партиями отправлялись на испытания. Если сиденья не проходили испытания, их отправляли на доработку для устранения проблем.
Была разработана карта будущего состояния процесса. Теперь было ясно, что основная проблема состоит в обработке продукции партиями. На каждом этапе процесса формировались крупные партии, которые выталкивались на следующий этап. На схеме текущего состояния результат такого подхода — запасы показаны в виде
треугольников. На этапе конструирования сидений это были запасы информации — проекты, накопление которых предшествовало этапу заказа комплектующих. Решение: создать систему последовательного вытягивания. Но как добиться этого применительно к информационному процессу, который представляет собой проектирование?
Было решено разработать скользящий график выдачи результатов работы на каждом этапе. Вместо того чтобы ждать, пока будет выпущена конструкторская документация на все сиденья, по завершении разработки одного изделия оно передавалось на следующий этап, чтобы можно было приступить к заказу комплектующих. Как только поступали все комплектующие для этого сиденья, начиналось изготовление прототипа, который отправлялся в отдел испытаний, чтобы как можно быстрее сообщить их результаты инженерам-разработчикам.
Важнейшим инструментом, который помог изменить ситуацию, стала так называемая «доска вытягивания». Это был несложный инструмент визуального менеджмента: белая доска с основной информацией по каждому из сидений. Такая доска появилась в каждом отделе. Это позволяло сотрудникам отдела комплектации видеть, когда заказаны комплектующие, когда они должны поступить, прибыли ли они вовремя и когда предполагается завершить разработку очередного сиденья. Если в отделе комплектации не успевали заказать и получить комплектующие на скопившиеся разработки, об этом сообщали проектировщикам. Если отдел комплектации был готов взять новую работу, об этом тоже уведомляли проектировщиков.
Результатом такой работы было значительное сокращение продолжительности процесса. Узкие места и заторы были устранены, обратная связь стала более оперативной, а качество разработок повысилось. Неожиданно процесс обрел некую степень контроля.
Конкретная ситуация: создание потока при обработке заказов
Создание потока — эффективный метод, который приносит пользу любому процессу, производящему любой продукт. (Слово «продукт» обычно ассоциируется у нас с товарами промышленного производства, однако данные концепции применимы к любому объекту, который в процессе обработки передается из рук в руки. Это может быть заказ на поставку, страховой полис или сэндвич, приготовленный в Subway.) В данном случае продукт представлял собой заказ потребителя, который требовал ввода данных в компьютерную систему, внесения изменений в соответствии с требованиями заказчика, заказа материалов для изготовления изделий по индивидуальным заказам, вычерчивания индивидуально заказанных деталей с помощью САПР и проведения анализа.
Так же, как при обычном производственном процессе, все перечисленные виды деятельности были распределены между разными отделами, каждый из которых выполнял конкретную задачу. Заказ перемещался из отдела в отдел, каждый раз попадая в лоток для входящих документов, полный разных бумаг. Была разработана сложная система отслеживания дат, с тем чтобы заказы обрабатывались по принципу ФИФО, однако на деле все происходило совсем иначе. Некоторые заказы были более сложными и требовали больше времени, другие были попроще или требовали ускоренной обработки, поскольку речь шла об уже отгруженных изделиях. Поскольку время обработки таких заказов было весьма продолжительным, меньше времени оставалось на производство, а сложность процесса только усугубляла ситуацию.
Как всегда при создании потока, сложнее всего было сбалансировать время и объем выполняемой работы. В одних случаях на ввод заказа уходило больше времени, чем на работы с помощью САПР, в других все было наоборот. Узкие места то и дело возникали то тут, то там, и вариация времени выполнения заказа была очень высока. Ситуация обострялась, когда кто-либо из сотрудников отсутствовал на рабочем месте (особенно если текущие заказы требовали активного участия именно того отдела, где работал отсутствующий).
Сначала составили карту процесса и разбили продукты на семейства (потоки создания ценности). Решение выделить отдельные семейства продуктов было продиктовано необходимостью изолировать вариацию, как описано в главе 4. С учетом сложности заказа и времени его обработки были выделены три потока создания ценности. Самые сложные заказы с максимальным уровнем вариации были выделены в один поток, а более простые заказы на конечную доработку — в другой. Третий поток создания ценности (подавляющая часть заказов) включал заказы, сложность и время обработки которых приближались к стандарту.
Группа решила объединить сотрудников в команды, создав рабочие ячейки, каждая из которых будет заниматься отдельным потоком создания ценности. Планировку офиса изменили, и теперь члены одной команды сидели рядом. Это способствовало поточной обработке заказов. Группировка заказов с учетом сложности и времени, требуемого на обработку, позволила определить стандартное число сотрудников, работающих с каждым потоком создания ценности. Обычно при этом обнаруживается, что в процессе заняты «лишние» работники. На самом деле их нельзя считать «лишними», поскольку их время уходит на то, чтобы компенсировать различные виды вариации, включая отсутствие коллег. Для стандартизации работы и создания потока желательно верно определить необходимую численность персонала (с учетом времени такта и содержания работы). Если должностные обязанности стандартизированы, чрезвычайно важно, чтобы никакое рабочее место не пустовало! Поэтому «лишние» сотрудники становятся лидерами команд и выполняют множество важных функций, описанных в главе 10, включая подмену отсутствующих.
Как уже говорилось в этой главе, чтобы создать поток, необходимо уяснить условия договора между операциями, распределить ресурсы и пространство и определить метод работы и механизм контроля. Лишь в этом случае каждый поток создания ценности должен стать связанным. Важным аспектом является визуальное оповещение о состоянии каждой ячейки. При поступлении заказа первым делом определяется его категория, после чего заказ помещают в цветную папку соответствующего потока создания ценности. Папки с заказами, ожидающими своей очереди, лежат на стеллаже. Лидер может проверить объем работ и при необходимости откорректировать его распределение: если объем заказов превышает условленный лимит (стандарт), лидер передает часть работы другому потоку создания ценности. Условия договора (стандарт) были определены с учетом возможности перераспределения объема работ (например, простые заказы можно передать на поток, где обрабатываются заказы средней сложности, но сложные заказы нельзя обрабатывать на потоке, обрабатывающем простые заказы). Кроме того, было четко определено, кому разрешается заниматься подобным перераспределением. Если все команды не укладываются в график, приходится работать сверхурочно.
Между всеми операциями в каждой ячейке предусмотрены составляющие потока. Поскольку обработке заказов свойственна вариация времени, необходим связующий механизм, позволяющий компенсировать вариацию времени рабочего цикла и при этом поддерживать поток и выявлять проблемы. Поток единичных изделий в данном случае невозможен. Вместо него была создана очередь с заданной последовательностью (она же очередь ФИФО). Стеллаж с заказами, ожидающими своей очереди, имеет определенное количество ячеек, что позволяет визуально определить состояние потока и сбалансированность отдельных операций. Лидер команды следит за состоянием очереди и корректирует распределение объема работ в пределах ячейки (например, обработка заказа выполняется «вне потока», после чего заказ возвращается в поток для дальнейшей работы с ним), обеспечивая сбалансированную работу. Подобная корректировка осуществляется только тогда, когда условия работы отклоняются от соглашения, и лишь после всесторонней оценки ситуации.
Например, если по условиям договора команда в единицу времени должна обрабатывать не более пяти заказов и этот максимальный уровень достигнут, член команды уведомляет лидера о необходимости оценить ситуацию. Если лидер команды видит, что следующие заказы будут проще и «отставший» оператор обработает их быстрее, чем предыдущие, он может воздержаться от принятия каких-либо мер. Такой дисбаланс носит временный характер и исчезнет сам собой при обработке очередных заказов. Если же дальше предстоит обработка не менее сложных заказов и положение вряд ли улучшится само собой, лидер группы вносит в процесс коррективы.
Команда обнаружила, что группировка заказов с учетом их сложности помимо оптимизации потока дает возможность обучать новых сотрудников на простых видах работы, прежде чем поручать им более
сложные задания. Сотрудники из разных отделов стали единой командой, при этом члены команд занимаются взаимным обучением, что повышает гибкость такой команды. Поскольку теперь операторы работают бок о бок, это позволяет более оперативно реагировать на появление проблем, и объем доработок значительно снизился.
Группа сумела добиться значительного сокращения времени обработки заказов, в первую очередь самых важных заказов на финальную доработку. По мере расширения предприятия эта группа обрабатывала все больше заказов, не привлекая новых сотрудников и не прибегая к сверхурочной работе.
Чаще всего бережливое производство ассоциируется с системой «точно вовремя», — нужная деталь в нужном количестве в нужное время и в нужном месте. Как видите, бережливое производство не ограничивается только этим. Ключ к устранению потерь — это создание потока, а принципы вытягивания требуют производства, организованного по системе «точно вовремя».
Проще всего понять поток, взглянув на ось, показанную на рис. 5-11. Обеспечить определенный уровень потока может помочь даже пугающий всех график. Высшим достижением служит поток единичных изделий при отсутствии запасов между операциями. Между операциями может размещаться супермаркет, пополняемый по мере расходования запасов, другие
возможные варианты — это последовательное вытягивание деталей с одного процесса на другой или управление запасами по принципу ФИФО. Заметьте, что система канбан, предполагающая пополнение супермаркета, далеко не лучший вариант, она — следующая позиция после самой плохой — графика. Канбан — это признание того, что без запасов не обойтись и ими нужно управлять. Потери встроены в систему. Последовательное вытягивание и очередь ФИФО обычно требуют меньшего объема запасов, чем супермаркет, и обеспечивают более плавный поток.
Не следует считать, что освоить бережливое производство можно, лишь создав поток единичных изделий, главное в бережливом производстве — это устранение потерь. Если вы создали между операциями пополняемый супермаркет, избавьтесь от канбан и ужесточите условия работы системы. Если вы используете очередь ФИФО, сократите объем запасов на одно изделие, что позволит создать стимул для дальнейшего совершенствования.
Вопросы для самопроверки
1.Используя в качестве ориентира карту текущего состояния процесса, еще раз пройдите траекторию движения материального потока. По дороге выявляйте негибкие процессы, которые препятствуют созданию потока на данном этапе. Не пытайтесь выполнить это задание, не покидая офис. Чтобы понять помехи, нужно увидеть происходящее своими глазами.
А. Найдите процессы, не обладающие гибкостью, на карте.
Б. Составьте список причин их негибкости, например длительная переналадка или общие ресурсы, которые поставляют разнооб разные детали или снабжают разные процессы.
2.Оцените каждую связь поставщик-потребитель в существующем потоке создания ценности.
A.Определите, используется ли в каждом отдельном случае связывание по принципу ФИФО (если возможна поточная обработка) или через супермаркет.
Б. Разработайте план и определите все связи. Он должен учитывать вид материала, его количество (оговорить единицы измерения) и место расположения.
B.Выясните, закреплено ли за материалом определенное место, контейнеры или тележки, все ли связи обеспечены ресурсами.
Г. Определите механизм контроля каждой связи, подумайте, как обеспечить визуальный контроль, который упрощает проверку соблюдения правил.
3.Отлаженный поток требует, чтобы время цикла отдельных операций было сбалансировано.
А. Измерьте время цикла каждой операции в потоке создания ценности и составьте график соотношения циклов, чтобы определить текущее соотношение продолжительности операций.
Б. Двигаясь вдоль потока, выявляйте признаки дисбаланса в работе (такие как ожидание или накопление запасов) и отмечайте их на карте текущего состояния.
4.Вопросы, перечисленные в этом пункте, применимы к любому процессу мелкосерийного производства при широком ассортименте (изготовление индивидуальной, модульной или создаваемой на заказ продукции). Перед вами стоит та же задача, что и в любой другой компании, — создать оптимальный в данных условиях поток. В относительном выражении ваш поток, возможно, не будет безупречно сбалансированным и плавным, тем не менее его тоже можно совершенствовать.
A.Оцените возможность сгруппировать вашу продукцию в семейства с учетом трудоемкости отдельных операций (непродолжительное время, средняя продолжительность, длительное время).
Б. Можно ли улучшить поток, контролируя структуру ассортимента на входе потока создания ценности (с целью выравнивания объема работ)?
B.Составьте график годичных объемов заказа изделий (от максимальных объемов к минимальным) и оцените по нему отдельные семейства продуктов. При наличии изделий, которые заказываются в больших и средних объемах, следует подумать о создании ячеек для их изготовления. Возможно, их можно будет использовать для выравнивания графика (см. главу 7).
Г. При производстве на заказ в договоре фигурируют условные единицы. Что служит такой единицей? (Ею может быть изделие, заказ, временной интервал или любой другой элемент, единый для всех.)
5.Вопросы, перечисленные ниже, относятся к непроизводственным процессам. Даже если плоды ваших трудов нематериальны, как на производстве, ваша работа тоже имеет конечный результат. Этот результат и есть ваш продукт.
А. Определите свой продукт. Выявите траекторию перемещения продукта с одной операции на другую и составьте карту потока.
Б. В непроизводственных процессах увидеть перемещение продукта с операции на операцию бывает непросто. Продукт может
представлять собой документацию или информацию в компьютере. Здесь задача визуализации процесса особенно трудна.
—Существует ли визуальное оповещение о потоке продукта (если продукт находится в информационной системе или в лотке для входящих документов)?
—Как обеспечить визуальное оповещение о движении продукта, если последний невидим?
СТАНДАРТИЗАЦИЯ ПРОЦЕССОВ И ПРОЦЕДУР
Упоминание стандартизированной работы вызывает в памяти образы специалистов по организации производства с секундомерами в руках. Они одержимы повышением производительности и наводят ужас на рабочих, сражаясь за каждую секунду и выжимая из людей последние силы. Расписанная по минутам жизнь, где суровый босс следит, чтобы никто ни на йоту не отступал от правил. Разгул бюрократии, которая подавляет человеческую волю и творческое начало и превращает людей в автоматы.
Однако существует и иной взгляд на стандартизацию. Масааки Имаи в своей новаторской работе пишет, что без стандартизации нет кайдзен6. Стандартизация — это отправная точка для непрерывного совершенствования. Как рассказывается в Дао Toyota, Пол Адлер проанализировал производственную систему Toyota (TPS) с точки зрения теории организации7. Он обнаружил, что Toyota удается избежать большей части незапланированных негативных последствий бюрократии, поскольку она сумела создать так называемую «поощряющую бюрократию», где наряду со стандартизацией имеет место расширение полномочий сотрудников. Мы представляем себе бюрократию как «принуждающую» систему, которая мешает людям быть гибкими и совершенствоваться. Однако поощряющая бюрократия Toyota дает прямо противоположный результат — она предусматривает гибкость и инновацию, имеющие долгосрочные последствия.
Введение стандартизированных процессов и процедур — важнейшее условие устойчивой эффективности. Лишь при наличии стабильного процесса можно приступить к непрерывному творческому совершенствованию. Как мы уже показывали в предыдущих главах, разработка стандартов начинается на ранней стадии внедрения бережливого производства и продолжается в ходе развития и совершенствования бережливых операций. Создание стандартизированных процессов опирается на определение, наглядность (визуальные показатели) и последовательное применение методов, дающих наилучший результат. Стандартизация — не оторванный от других метод, который применяется через заданные промежутки времени, органическая часть непрерывного процесса выявления проблем, создания эффективных методов и поиска путей применения этих методов. Стандартизация не навязывается людям извне, но осуществляется по их инициативе. Самый значительный вклад в стандартизацию вносят те, кто выполняет работу и знает ее во всех подробностях.
Мы уже не раз говорили, что наша цель — помочь вам усвоить основные принципы и концепции Дао Toyota. Повторяем, в наши намерения не входит создание очередного учебника по применению инструментов бережливого производства. Процесс, который в Toyota называют «стандартизированной работой», так важен для производственной системы в целом, что ему посвящена треть внутреннего документа Toyota TPS Handbook8. И это понятно, стандартизированная работа и прочие стандарты работы — основа непрерывного совершенствования.
Здесь мы сталкиваемся с еще одним заблуждением в отношении TPS. Пока не выработаны стандарты для какой-либо операции, заниматься ее совершенствованием невозможно. Подумайте сами: если в нестандартизированный (непродуманный и хаотический) процесс были внесены усовершенствования, что именно вы усовершенствовали? Его хаотичность? Или вы просто добавили еще один возможный вариант выполнения работы, что только увеличило хаос? Если работник творчески совершенствует свою работу, но это не закрепляется стандартом, процесс пойдет лучше, лишь пока его выполняет именно этот человек. Результатами его усовершенствований не сможет воспользоваться никто другой. Если за усовершенствованием следует стандартизация, возникает основа, позволяющая персоналу непрерывно совершенствовать процесс. Так закладывается фундамент обучающейся организации.
К сожалению, нередко, работая с компаниями, которые внедряют бережливые процессы, мы слышим просьбу «заняться стандартизированной работой», словно речь идет о независимом инструменте, который можно запросто освоить в соответствии с графиком внедрения («По плану теперь мы должны заняться стандартизированной работой»). Одно из подобных заявлений прозвучало примерно так: «К октябрю мы должны разобраться со стандартизированной работой». На это последовал ответ: «Разумеется, мы можем это сделать, но стандартизированная работа — это инструмент, и подобно любому инструменту она имеет конкретное назначение и применяется для достижения конкретных целей».
В одной компании внедрение стандартизированной работы отставало от плана внедрения бережливого производства. Решение: нанять на лето школьного учителя, который распишет процедуру стандартизированной работы для всех операций. Результат: повсюду развешаны красиво оформленные карты стандартизированной работы, но стандарты никто не соблюдает. Разумеется, если вам хочется развесить повсюду листы бумаги, заполненные информацией, — дело ваше, однако реальной ценности вы этим не создадите. В ваших силах использовать стандартизированную работу для сокращения потерь, улучшения процесса работы и непрерывного совершенствования. Выбор за вами.
Мы говорим о стандартизации как об одном из «этапов», однако на самом деле стандартизация должна применяется непрерывно, о ней следует помнить при разработке любого метода работы. Подобно прочим составляющим TPS данная концепция чрезвычайно важна, но чтобы применять стандартизацию надлежащим абразом, ее следует тщательно осмыслить. Стандартизация — не комплект документации, который требует подготовки и тщательного контроля. Это средство обеспечения максимально эффективной и стабильной работы и основа устойчивости процесса. Без стандартизации такие инструменты, как шесть сигм и иные современные методы снижения вариации, бесполезны.
Пожалуй, из всех концепций бережливого производства наибольшее количество заблуждений и ошибок связано именно со стандартизацией. Корни этой проблемы восходят к стремлению получить максимальную прибыль за счет разбивки всего задания на составляющие и распределения этих составляющих между работниками, в чем весьма преуспел Фредедик Тейлор. История нормирования труда во многих отраслях (в первую очередь в автомобильной промышленности) — это история борьбы. Стандарты тех лет предназначались прежде всего для того, чтобы карать работников за низкую производительность.
Такой подход породил ряд легкоузнаваемых «игр» и попыток обмануть систему. Основным итогом стало противостояние между рабочими и менеджментом. Вместо стремления работать на общую цель, создавая возможно лучший продукт для потребителя, мы видим противоборство двух групп, которые ведут себя как антагонисты: менеджмент стремится как можно точнее регламентировать работу, чтобы установить нормы затрат труда и заставить каждого работника им следовать, а работники намеренно иначе работают, когда за ними наблюдают, чтобы к ним предъявляли более низкие требования, которые несложно выполнить. При этом менеджмент использует «стандарты», принимая решения, касающиеся производства, с учетом «нормативно допустимых затрат времени» и тому подобных показателей, в основе которых лежат нормы производительности. Цель — обеспечить, чтобы производственные рабочие «отработали» положенное количество часов. Если это выполняется и нормы затрат соответствуют запланированным (либо план перевыполняется), накладные расходы на контроль считаются оправданными, что теоретически обеспечивает получение целевой прибыли.
С точки зрения рабочих, трудовые нормы — это показатель «напряженности» их труда, который учитывает, сколько сил нужно потратить на выполнение работы. Кроме того, рабочие интуитивно понимают, что все люди обладают разным потенциалом и система ориентируется на самый низкий уровень возможностей. При таком подходе работающие медленно успешно справляются с работой, а более проворные могут добиться более высокой производительности или при желании «освободить» часть своего времени, работая быстрее других.
При такой модели стандарты работы устанавливаются исходя из неверно поставленной цели. Стандарт ориентирован прежде всего на нормы затрат, а не на обеспечение оптимального метода работы при минимальных потерях, который позволил бы получить продукт отличного качества при минимальных затратах. Такие нормы используются либо как кнут, чтобы наказывать рабочих за низкую производительность, либо как пряник, чтобы соблазнить их перевыполнить норму (повышение ставок зарплаты с учетом производительности — производная от описанного метода). Эти представления настолько въелись в сознание менеджмента и наемных работников, что введение стандартизированной работы по методу Toyota может оказаться одной из самых трудных задач при освоении бережливого производства. Всем чрезвычайно тяжело расстаться с привычным положением вещей, поскольку каждый научился работать и преуспевать в условиях этой системы. Менеджеры боятся, что усвоение дао Toyota приведет к тому, что подчиненные станут неуправляемыми, выбирая метод работы на свой вкус, а значит, будут работать спустя рукава. Кроме того, они боятся лишиться системы измерений, которая помогала им управлять подчиненными и контролировать их, чтобы добиться успеха. Всем знакомы разговоры такого рода:
Менеджер по производству — мастеру. «Ваш отдел опять превысил нормативы по времени работы. Что вы намерены предпринять, чтобы исправить дело?»
Мастер: «Нашему цеху пришлось выполнить несколько сложных заданий, и мы не уложились в отведенное время. Мы выйдем на работу в субботу и займемся работой попроще. Это поможет исправить положение».
Менеджер по производству. «Ладно. Я доложу об этом директору завода и скажу, что причина была в неудачном сочетании ассортиментных позиций. Я постараюсь, чтобы впредь вам было полегче».
Очевидно, что в данном случае первоочередное внимание ошибочно уделяется измерениям, а не созданию по-настоящему эффективного процесса, который обеспечит устойчивую результативность. Заметьте, что для улучшения показателей мастер собирается заняться «работой попроще». Однако деталь есть деталь, независимо от сложности или простоты ее обработки. Означает ли это, что при выполнении «работы попроще» будут изготавливаться именно те детали, которые нужны потребителю? Похоже, в данном случае это не Равное. Обидно, что столько времени и сил тратится впустую только ради того, чтобы выйти на нужные показатели, вместо того чтобы заняться оптимизацией процесса. Менеджеры попадают в порочный круг, из которого нет выхода, поскольку эффективность работы их самих определяется их способностью добиться целевых показателей.
При традиционной модели производства первоочередной задачей было свести к минимуму затраты на единицу продукции и создать стандартный метод работы, который обеспечивает запланированный уровень затрат
(рис. 6-1). Такая модель учитывает «затраты на единицу продукции», в то время как дао Toyota предполагает наращивание возможностей системы в целом и уделяет основное внимание «общим затратам», считая основным показателем успеха сокращение потерь. Традиционный подход изучает движения и время для определения наиболее «эффективной» рабочей процедуры, и на выполнение определенной задачи выделяется «стандартное» время. Обычно за оператором наблюдают и учитывают, сколько времени затрачивается на отдельные движения. Далеко не всегда метод, избранный оператором, оптимален: это всего лишь метод, который применяет оператор, когда за ним наблюдают. Такой процесс порождает «ложный стандарт», который впоследствии используется для определения «эффективности».
Дао Toyota преследует ту же цель, т. е. снижение затрат; однако основное внимание уделяется сокращению потерь в системе (рис. 6-2). Базой непрерывного совершенствования в Toyota считают стандартизацию, т.е. предполагается, что в перспективе результаты будут лучше предусмотренных стандартом. Традиционный подход рассматривает стандарт как самоцель, точно в нем закреплен предельный уровень эффективности, и это препятствует совершенствованию. Это коренное отличие образа мышления — основа множества парадоксальных составляющих бережливой системы. Цели остаются прежними: изготовить высококачественный продукт при минимальных затратах в кратчайшие сроки, однако образ мышления, определяющий достижение этих результатов, диаметрально противоположен тому, что доминировал в массовом производстве последние сто лет. К тому же подход массового производства ограничивает возможности достижения названных целей.
В основе модели сокращения потерь в рамках бережливого производства лежит особый образ мышления. Во всех организациях есть потери, которые порождаются неупорядоченными действиями и непоследовательными методами. Чтобы устранить потери, необходимо снизить или устранить вариацию внутри процессов. Вариация — это антитезис стандартизации. По определению вариация предполагает невозможность стандартизации. Как рассказывалось в главах 4 и 5, для введения стандартизированной работы нужно изолировать вариацию. Помимо прочего, стандартизация создает базу для сравнения и позволяет отличать стандартный (нормальный) метод от нестандартных (отклоняющихся от нормы) методов. Для оперативного определения эффективности и внесения поправок в режиме реального времени используются методы визуального контроля и прочие инструменты бережливого производства, что обеспечивает стабильное достижение целевых показателей результативности.
Основные средства внедрения стандартизированных процессов и процедур — документация по стандартизированной работе и ряд инструментов бережливого производства, которые использовались на предыдущих этапах (таблица 6-1).
Традиционная политика и процедуры часто препятствуют стандартизации. Возьмем ситуацию с приходом на работу. Стандартизированный процесс предполагает, что рабочий должен обязательно присутствовать на месте. Это значит, что, если кто-то не вышел на работу, отсутствующему следует найти замену, чтобы обеспечить надлежащий ход процесса. Процесс не может функционировать должным образом, если не предусмотрен резерв на случай непредвиденных обстоятельств, например на случай невыхода на работу кого-то из сотрудников. Тем не менее при традиционной системе высший менеджмент редко задумывается о таких проблемах, и мастера изо дня в день лезут из кожи вон, чтобы найти замену отсутствующим рабочим, не располагая стандартизированным методом решения проблемы.
Создайте структуру для поддержания стандартизированной работы
Toyota создала систему лидеров групп и лидеров команд. Лидер команды — сотрудник с почасовой оплатой, который отвечает за команду из пяти-семи человек. Лидеры команд следят за соблюдением стандартной процедуры, выявляя отклонения от стандарта (см. главу 11), и при необходимости заменяют отсутствующих. Они нередко участвуют в разработке стандартизированной работы для производства новых моделей. Благодаря лидерам команд описание стандартизированной работы не просто украшает стены, но становится подлинным инструментом непрерывного совершенствования. Любопытно, что в большинстве компаний позиция лидера команды отсутствует.
Введение процесса, который в Toyota обозначают широким понятием «стандартизированная работа», нередко оказывается очень непростым делом. Попытки других компаний применить этот, казалось бы, простой метод оказываются обескураживающе сложными. Разработка стандартизированной работы столь ощутимо отличается от расчета трудовых норм, что едва ли уместно проводить между ними какие-либо параллели. Методы, которые называются «стандартными» в других компаниях, не имеют ничего общего с понятием «стандартизированной работы» в Toyota, которое обозначает метод выполнения работы с минимальными потерями. На самом деле есть множество типов стандартов, и все они объединены в целостный метод, регламентирующий оптимальную рабочую процедуру. В Toyota стандартизованная работа — основной инструмент, регламентирующий методы работы. В ней описывается, кто, когда, где и какую работу выполняет.
Структура взаимосвязей между разными типами стандартов представлена на рис. 6-3 в виде дома. Все стандарты работают на единые цели — обеспечить выполнение работы заданным методом с минимумом затрат и дать работникам исчерпывающую информацию, способствующую повышению навыков и знаний.
Заметьте, что каждый тип стандарта имеет свое назначение, однако работа По стандартизированным методам должна удовлетворять всем названным стандартам. Это не значит, что все они содержатся в документации на стандартизированную работу. Эта документация оговаривает лишь этапы работы,
которые ведут к достижению желаемого результата (выполнению прочих стандартов). Позиции прочих стандартов учитываются при инструктаже оператора и представляют собой часть его подготовки, как показано на рис. 6-4.
В основе стандартов качества лежат ожидания потребителя, которые определяют требования к внешнему виду продукта и связаны с такими понятиями, как чистовая обработка/отделка. B^jom числе это: общий внешний вид; цветовое решение;
дефекты, несоответствия (закругленные края, вмятины и т.д.); допуски и посадки; обработка поверхности;
ограничения размера и количества дефектов.
Стандарты качества обычно включаются в ведомости по производственному инструктажу, где подробно описано, какие условия нужно отслеживать, на что именно следует обращать внимание и каковы критерии оценки хорошо/ плохо. Для определения основных параметров, которые необходимо отслеживать на производстве, и мест, где такие отклонения наиболее часты, используется информация, полученная при аудитах качества. Это позволяет выработать метод инспектирования в процессе выполнения работы и повышает исходный
ПОДСКАЗКА
Храните ценности в надежном месте
Эталонные образцы представляют большую ценность и требуют соответствующего обращения. Их следует хранить в надежном месте, возможно, под замком, и доступ к ним имеет лишь мастер. Когда у оператора сформирован навык оценки, их применяют достаточно редко. На эталонных образцах должна стоять дата и подпись лица, ответственного за качество. Ответственность за сохранность образцов возлагается на производственников. Относитесь к ним как к инвестированному капиталу!
уровень качества. Подробное описание данного метода инспектирования не включено в документацию на стандартизированную работу, но сам метод упоминается в ней отдельной позицией (осмотрите деталь).
Стандарты качества, требующие визуального контроля продукта, допускают возможность субъективной интерпретации. Так, «приемлемый внешний вид поверхности» можно истолковать по-разному в зависимости от личного истолкования понятия «приемлемый». В таких ситуациях необходимо, чтобы отдел качества обеспечил производство эталонными образцами требуемого уровня качества. Эти образцы позволяют четко договориться о том, что приемлемо, а что нет.
Обычно нормативы по безопасности труда и охране окружающей среды компании подчиняются нормам федерального права и нормам штата. Эти нормативы, как правило, разрабатываются специальными техническими отделами, и изменение таких стандартов менеджерами или сотрудниками допускается лишь с одобрения такого отдела. Однако сотрудникам, которые разрабатывают методы стандартизированной работы, дается возможность ознакомиться с этими требованиями, назначение которых — обеспечить должный уровень безопасности труда и охраны окружающей среды. Рабочая группа или менеджмент отдельного участка могут разрабатывать нормы техники безопасности при выполнении конкретного вида работ. Речь идет, например, о риске получения травмы — пореза или защемления оборудованием. Такие потенциально опасные моменты помечаются в документации на стандартизированную работу специальным значком.
Стандартные технические требования (спецификации) содержат техническую информацию по надлежащему функционированию оборудования и определенные требования к технологическому процессу, обеспечивающему производство продукта. Примеры таких требований:
•размеры и допуски;
•методы обработки (метод сварки, метод конечной обработки и т.д.);
•параметры работы оборудования (время, температура, давление и т.д.);
•последовательность операций, выполняемых на данном оборудовании;
•информацию о корректирующих мерах.
Стандартные технические требования не входят в документацию на стандартизированную работу. Документы по инструктажу оператора описывают их лишь в том случае, если они не отражены в прочих документах, например чертежах (нет необходимости документировать уже оговоренные стандарты повторно).
Параметры работы оборудования используются для разработки методов его проверки. Такая проверка вменяется в обязанность одному из работников и представляет собой процесс, выполняемый регулярно. В Toyota такой проверкой чаще всего занимается лидер команды. Проверка состояния оборудования производится несколько раз в день через неравные промежутки времени, тем самым обеспечиваются должные условия работы оборудования. Нередко такая проверка проводится перед началом смены, а затем в течение смены в зависимости от критичности оборудования. Задача проверки перед началом смены — обеспечить, чтобы все параметры процесса находились в заданном диапазоне, а оборудование было в рабочем состоянии и готово к эксплуатации.
Информация о корректирующих мерах так же, как и требования спецификации, используется для проверки оборудования. Она содержит подробные пошаговые инструкции о мерах, которые следует предпринять в случае отказа оборудования или проблем в процессе, и включает план действий в случае непредвиденных обстоятельств, в частности определяет возможности использования альтернативного оборудования или эксплуатации оборудования в режиме ручного управления.
Спецификации обычно разрабатываются отделом организации производства или технологическим отделом. На производстве эта информация используется по мере необходимости для разработки ведомостей по производственному инструктажу. Некоторые компании путают эти технические требования со стандартной работой оператора, однако стандартные технические требования не содержат информации об отдельных операциях, временном режиме и оптимальных методах выполнения работы.
СТАНДАРТНЫЕ ПРОЦЕДУРЫ
Стандартные процедуры разрабатываются производственной группой и определяют правила выполнения работы. Необходимость данных процедур может быть обусловлена прочими видами стандартов или определяется исключительно потребностями производства. Примеры включают:
•нормы незавершенного производства;
•правила и нормы канбан (уровень запасов, количество карточек и т.д.);
•траекторию перемещения потока материала по предприятию;
•требования 5S;
•доски оперативной информации о процессе производства;
•правила цветовой маркировки.
Содержание стандартных процедур должно быть видно всем в рабочей зоне с помощью визуальных средств, а следовательно, они не требуют разъяснений и не нуждаются во внесении в документацию на стандартизированную работу. Например, карточка канбан включает всю информацию, необходимую для ее использования, т. е. стандарт определяется самим ее содержанием. Подобным образом договоренности относительно выполнения операций обозначены при помощи визуальных средств непосредственно в рабочей зоне. Помните, что стандарты такого рода могут меняться достаточно часто по мере совершенствования процесса. Попытки отразить все эти изменения в документации и постоянно следить за ее обновлением по мере изменения условий в рабочей зоне превратились бы в настоящий кошмар. Разработайте систему визуальных средств, оповещающих о стандарте, и по мере надобности вносите в нее соответствующие поправки.
МИФЫ О СТАНДАРТИЗИРОВАННОЙ РАБОТЕ
За пределами Toyota существует множество мифов о стандартизированной работе. Печально видеть, сколько времени и сил тратят впустую компании, ставшие жертвой одного или нескольких подобных мифов, пытаясь создать систему, которая опирается на их заблуждения. Мы попытаемся развенчать как можно больше подобных мифов в надежде, что это поможет вам направить свои усилия на подлинное совершенствование процесса.
Миф 1: если мы применяем стандартизированную работу, каждый может почерпнуть все необходимые для работы сведения в документации
Трудно сказать, что породило данный миф, но возможно, его появление связано с описанием стандартизированной работы, применяемым в Toyota. Во время экскурсии по заводу Toyota речь то и дело заходит о применяемом операторами методе стандартизированной работы. Возможно, посетители ошибочно полагают, что вывешенная на видных местах информация представляет собой полное описание процесса работы, включающее сведения о соответствующих стандартах. Однако каждый, кто прочтет написанное повнимательнее, увидит, что операции описаны в самых общих чертах — данных сведений недостаточно даже для того, чтобы получить представление о выполняемой работе.
Чтобы член команды мог получить полное представление о работе, в Toyota применяется производственный инструктаж (описанный в главе 11). Это длительная процедура, ведь чтобы стать высококвалифицированным специалистом, нужно знать очень много. Любой, кто считает, что выполняемая работа так проста, что для ее описания хватит нескольких страниц, недооценивает уровень квалификации, необходимый работникам компании. Мы никогда не видели предприятия, где работа настолько проста, что «все, что нужно знать», можно уместить на нескольких страницах.
Миф 2: если мы применяем стандартизированную работу, можно в два счета обучить выполнению работы человека с улицы
См. миф 1. Это так, если речь идет об отдельном задании или конкретной задаче, но для того чтобы стать полноценным работником, досконально знающим свое дело, придется потратить немало сил. Отзвук этого мифа слышится в едких замечаниях, что «выполнить это может научиться любой дурак». Такие разговоры свидетельствуют не только о полном отсутствии уважения к наемным работниками и их способностям, но и о заблуждениях в отношении простоты выполняемой работы. Для формирования надлежащей культуры, без которой невозможно освоить бережливое производство, с подобным образом мышления придется расстаться.
Миф 3: в карту стандартизированной работы можно включить исчерпывающее описание работы и соответствующие стандарты
Мы имеем дело с типичной попыткой превратить инструмент, имеющий конкретное назначение, в средство на все случаи жизни. Стандартизированная работа — не перочинный ножик с множеством лезвий, а инструмент выявления и устранения потерь. После внедрения оптимального метода работы обеспечиваются визуальные ориентиры, которые позволяют придерживаться стандартного процесса, описанного в документации.
Миф 4: мы вывесим описание работы на стену, чтобы оператор постоянно на него смотрел и запоминал, как выполнять свою работу
В данном случае имеет место искаженное представление о цели визуализации. После того как оператор прошел обучение (тщательно контролируемый процесс, который гарантирует надлежащий уровень квалификации) и проделал соответствующую операцию первые несколько сотен раз, в напоминаниях о стандартном методе работы нет необходимости. Визуальные ориентиры используются менеджментом, который следит за соблюдением стандарта. Об этом мы поговорим далее, когда речь пойдет об «аудите стандартизированной работы».
Миф 5: работники сами разрабатывают свою стандартизированную работу
В этом мифе есть доля правды. В Toyota считают нежелательным, чтобы какая-либо работа «узурпировалась» отдельными работниками, и периодически переводят их с одной работы на другую, поэтому ни один сотрудник не является «хозяином» какого-либо вида работ. Разработка первоначальных стандартов работы осуществляется инженерами совместно с лучшими операторами, которые участвуют в работе «пилотной команды», и эта команда помогает при запуске в производство очередной новой модели. За обучение сотрудников стандартизованной работе отвечают лидеры групп и лидеры команд, они же поощряют рабочих вносить свой вклад в дальнейшее развитие метода. Как только обеспечен определенный уровень стабильности процесса, перед рабочими ставится задача поиска лучших методов, к которому подключаются другие сотрудники, включая менеджмент. Таким образом, коллективным «собственником» выполняемой работы становится команда вместе с лидером команды и лидером группы.
Этот миф часто сочетается с ложно понимаемыми попытками «обогащения труда», при которых сотрудникам предлагается разрабатывать собственные методы работы. Подобные представления нагоняют страх на менеджеров, в их воображении возникают пугающие картины, как, пользуясь случаем, их Подчиненные нарочно занижают эффективность своей работы.
Однако такие представления очень далеки от истины. Цель стандартизированной работы — создать метод работы, отвечающий нуждам потребителя при возможно меньшем объеме потерь. Но это не значит, что работники вольны выполнять работу любым удобным для них способом. Они по-прежнему должны соблюдать определенные правила и нормы. Подобная ситуация складывается в спортивной команде. Члены команды, играющие на определенных позициях, прекрасно знают свое дело, однако тренер не говорит им: «Предоставляю вам полную свободу действий, пусть каждый делает свое дело». У тренера есть свои представления о стратегии игры и о том, как каждый участник должен выполнять свои задачи. Тем не менее, если тренер жестко диктует своим подопечным, как следует играть, и при этом не использует уникальные дарования и опыт игроков, рано или поздно они взбунтуются. Методы работы Toyota тоже применяются не в пустоте. Все работники едины в намерении выполнить свою работу. При этом существует множество альтернатив. Задача в том, чтобы найти метод, который лучше нынешнего. (Имейте в виду, что понятие «лучше» не должно быть субъективным. Оно должно иметь количественное выражение и быть измеримым.) Ответственность за постановку целей перед подчиненными несет менеджмент, он же должен обеспечить работников инструментами и ресурсами, необходимыми для достижения целей.
Миф 6: если мы применяем стандартизированную работу, операторы будут выполнять задания должным образом и не будут отклоняться от стандарта
/
Это, пожалуй, самый нелепый миф. Определение порядка работы и его закрепление в документации очень и очень далеки от надлежащего выполнения работы. Ничто не мешает оператору отклоняться от заданной процедуры стандартизированной работы, однако о таком отклонении визуально оповещаются остальные. Чтобы обеспечить соблюдение стандарта, необходимо исключить возможность выполнения работы иным методом и рассеять «туман». Если любое отклонение от стандарта становится заметным сразу и вызывает негативные последствия, стандарт будет соблюдаться.
Процесс работы в Toyota определен так четко, а требования к соблюдению предписаний так строги, что отклонение от стандарта выявляется немедленно. Предположим, оператор решил выполнить какую-то операцию, нарушив заданную последовательность работы, и в результате время выполнения работы возросло. Скорее всего, такой оператор не уложится во время такта и будет вынужден остановить линию при помощи сигнала андон. Если подобное повторится несколько раз, это привлечет внимание лидера команды или мастера, которые, разбираясь в сложившейся ситуации, обязательно проверят соблюдение стандарта.
СТАНДАРТИЗИРОВАННАЯ РАБОТА
В Toyota говорят, что стандартизированная работа — это основа кайдзен. Если работа не стандартизирована и каждый раз выполняется по-разному, отсутствует точка отсчета, т. е. ориентир для сравнения. Многие компании приходят в смятение, обнаружив, что спустя некоторое время после «усовершенствования» работа начинает делаться по старинке и сохранить достигнутые результаты не удается. Заниматься кайдзен до стандартизации все равно что строить дом на зыбучем песке. Возможно, его и удастся построить, но он в два счета уйдет под землю.
«Но если стандартизированная работа — основа непрерывного совершенствования, почему не начать прямо с нее?» — спросите вы. Это хороший вопрос. В Toyota подчеркивают, что, для того чтобы приступить к стандартизации, необходим ряд предпосылок. Обычно они создаются на этапе стабилизации, но если вы из тех, кто норовит отставить в сторону закуску и немедленно приступить к основному блюду, и возьметесь за стандартизацию работы, не обеспечив стабильности, вы уподобитесь собаке, которая пытается поймать собственный хвост, — вы будете крутиться на одном месте и никогда не добьетесь желаемого результата.
Предпосылки стандартизированной работы
Прежде чем приступать к стандартизации, необходимо обеспечить определенный уровень стабильности. К сожалению, не существует однозначных критериев, которые позволяют сказать: «Теперь вы готовы к стандартизации работы». Можем лишь заметить, что, если вы ощущаете себя собакой, которая пытается поймать собственный хвост, уровень стабилизации процесса недостаточен, для того чтобы браться за стандартизацию. Итак, что нужно для обеспечения базовой стабильности?
1. Рабочая операция должна повторяться. Если при описании работы используются выражения «если... то», стандартизация невозможна. Например, если формулировка рабочего задания содержит оговорки вроде: «Если случится А, делай В, а если произойдет С, делай D», стандартизации не получится, пока такое описание не сменят несколько простых, четких правил.
2.Линия и оборудование должны быть надежными, а время простоев — минимальным. Если процесс постоянно прерывается, а работник вынужден отвлекаться, стандартизация невозможна.
3.Не должно быть значительных проблем с качеством. Продукт должен иметь минимум дефектов, а его основные характеристики должны быть единообразными. Если работник постоянно занят исправлением дефектов или то и дело сталкивается с проблемами, вызванными недостаточным единообразием продукта, например вариацией размера, которая заставляет заниматься подгонкой детали, а следовательно, порождает вариацию времени выполнения операции, увидеть подлинную картину работы невозможно.
ЛОВУШКА
Распространенная ошибка при внедрении «усовершенствованного» метода работы состоит в том, что оператора слишком рано оставляют наедине с новым процессом без какой-либо поддержки или и того хуже — не следят, удается ли оператору самостоятельно повторить все действия! Оператор чувствует себя униженным и растерянным, поскольку не знает, как приняться за новую процедуру, и начинает считать усовершенствование процесса в высшей степени неприятным, стрессовым занятием.
В процессе стандартизации работы используются три основных и вспомогательных документа. В задачи этой книги 'не входит подробный рассказ об использовании каждого из этих документов, однако мы считаем нужным остановиться на трех основных:
1.Карта стандартизированной работы.
2.Таблица совмещения стандартизированных работ9.
3.Ведомость производительности процесса.
Изначально этот документ представлял собой схему рабочей зоны и перемещений работника. Вербальное описание метода работы и время выпол-
нения отдельных операций отсутствовали. Время выполнения отдельных операций фиксировалось в отдельном документе — таблице совмещения стандартизированных работ. По ходу дела на многих операциях карта стандартизированной работы и таблица совмещения стандартизированных работ объединялись в один упрощенный документ, который часто называют
Рис. б-б. Таблица совмещения стандартизированных работ при наличии одного автомата
(по крайней мере, за пределами Toyota) «ведомостью стандартизированной работы» или «картой стандартизированной работы».
Первоначально ведомость стандартизированной работы использовалась как инструмент выявления и устранения потерь. После внесения изменений базой для дальнейшего совершенствования становится новый метод. Ведомость стандартизированной работы вывешивается на рабочем месте и служит средством визуального контроля, обращаясь к которому менеджмент проверяет соблюдение стандарта.
Использование любого инструмента зависит от обстоятельств. Какова квалификация пользователя? Какую ситуацию следует исправить? Не беспокойтесь о достижении безупречных результатов или «правильном» использовании карты. Применяя данный инструмент (стандартизированную работу) впервые, помните: прежде всего вы должны создать базис для совершенствования. Данный процесс включает следующие этапы:
1.Описать последовательность выполнения работы (отдельные операции).
2.Составить схему перемещений в процессе выполнения работы.
3.Выявить потери.
4.Определить, какие усовершенствования необходимы для достижения желаемых результатов (одна из задач — уложиться во время такта, о чем пойдет речь ниже).
5.Учесть использование материала и его поток (стандартный запас незавершенного производства).
6.Задокументировать усовершенствованный метод.
На рис. 6-5 показан пример ведомости стандартизированной работы. Ее основные элементы — последовательность выполнения работы и схема перемещения в процессе выполнения работы. Когда зафиксирована последовательность операций и составлена схема перемещения, мы спрашиваем: «Что вы видите?» Самое большое впечатление производят потери. Если мы задаем вопрос о ходе выполнения работы на схеме, мы слышим: «Это полная неразбериха!», «Вы только посмотрите, какое расстояние требуется проходить между отдельными операциями!» или «Оператор без конца ходит взад-вперед». Все эти замечания касаются потерь. Когда потери становятся очевидными, мы спрашиваем: «Есть ли метод получше?»
По мере того как вы идете вперед, занимаясь усовершенствованием, ваш подход к применению карты стандартизированной работы будет меняться. От стандартизации и устранения потерь в отдельных операциях вы перейдете к объединению и синхронизации операций в масштабах потока. Такое согласование достигается разработкой операций, которые выполняются в едином темпе, иначе называемом временем такта (речь о нем пойдет далее).
Если вы составите описание потока работы и покажете его оператору, это избавит его от чувства вины за неудачный метод. Если вы указываете операторам на наличие потерь, скорее всего, они начнут объяснять, почему без этого не обойтись (отстаивая свой метод работы). Если же вы представите работу в виде схемы и покажете эту схему операторам, по всей вероятности, они ответят: «До чего же бестолковый подход к делу! Его нужно изменить!»
Сегодня многие компании стремятся получить сертификат ISO. Если мы начнем применять стандартизированную работу в организации, которая старается разобраться в требованиях ISO, неизбежно встанет вопрос: «Регламентирует ли стандарт ISO документацию по стандартизированной работе?» Не будучи специалистами по ISO, мы неоднократно видели, как компании, взявшиеся за стандартизацию, тонули в грудах бумаг, превращая работу в настоящий кошмар. Многие компании предпочитали воздержаться от вывешивания каких-либо документов из страха получить «наблюдения» во время аудита ISO или из-за того, что любое изменение процесса потребует титанических усилий по исправлению и обновлению документации. Мы видели, как в одной компании перед аудитом ISO убрали все документы по стандартизированной работе, а затем развесили их вновь (чтобы порадовать аудиторов по бережливому производству). Входит ли стандартизированная работа в перечень контролируемых в рамках ISO документов, зависит от интерпретации.
Не забывайте, что стандартизированная работа — это инструмент анализа, обеспечивающий базис для непрерывного совершенствования. Это не инструкция для оператора и не инструмент его обучения (см. вышеперечисленные мифы). Менеджмент использует стандартизированную работу для проверки надлежащего выполнения основных этапов работы, поэтому нужно следить за своевременным обновлением соответствующих материалов. Если вы действительно хотите вписать стандартизированную работу в требования стандартов, позаботьтесь о создании простой системы, которая сделает этот документ «живым» и легко поддающимся изменению (например, чтобы он утверждался только на одном уровне).
Таблица совмещения стандартизированных работ
Как понятно из названия, данная таблица (которая также называется ведомостью совмещения стандартизированных работ) используется для анализа сложных видов работ. Ее назначение — показать соотношение продолжительности двух или более видов деятельности, которые осуществляются одновременно, главным образом таблица используется применительно к тем видам работ, которые требуют сочетания ручных и механизированных операций, однако может использоваться и для анализа операций, в ходе которых два или более оператора одновременно занимаются изготовлением одного изделия. Применение этого инструмента уместно, к примеру, в следующей ситуации: оператор загружает сварочный автомат и нажимает на пуск, и пока этот станок работает, оператор разгружает и загружает другой станок. Мы видели массу попыток использовать сводную таблицу стандартизированной работы для всевозможных видов работ, однако применять ее для анализа работы отдельного оператора, который не использует автоматическое оборудование, — пустая трата времени и сил. Занимаясь подобным анализом, вы научитесь разве что заполнять таблицу.
На рис. 6-5 представлена операция, которая включает использование автомата с автоматическим циклом работы. Анализ с помощью простой ведомости стандартизированной работы в данном случае имеет существенный недостаток — ведомость не показывает, что происходит после запуска станка. Вполне вероятно, что оператор ожидает завершения цикла, а значит, это время представляет собой потери. Чтобы не стоять без дела, оператор может найти для себя самые разные занятия, например готовить следующий комплект деталей, «приводить в порядОЕ» рабочее место (как-то нам пришлось наблюдать, как оператор перекладывал детали в контейнере, укладывая их ровными рядами, что выглядело очень мило, но не имело никакой практической ценности). Кроме того, в ведомости не учитывается время рабочего цикла станка. В такой ситуации может пригодиться таблица совмещения стандартизированных работ (рис. 6-6).
На рис. 6-6 показана таблица совмещения стандартизированных работ для того же самого процесса. Если вы прочитаете ее, последовательно отслеживая выполнение рабочих операций слева направо, вы увидите, в какой момент рабочий переходит с места на место для выполнения очередной операции. В данном примере оператор тратит одну секунду, чтобы взять крепежную скобу А, затем две секунды, чтобы подойти к зажимному приспособлению, шесть секунд, чтобы установить скобу А в зажимное приспособление, затем две секунды, чтобы сходить за следующей деталью, и т.д. На момент 11-й операции все детали загружены в сварочный робот, а по пунктирной линии видно, что время цикла робота составляет 23 секунды.
С точки зрения взаимодействия оператора и оборудования данный процесс достаточно прост. Он может быть сложнее, если оператор обслуживает ячейку и работает с тремя-четырьмя единицами оборудования. Подобно карте стандартизированной работы операций таблица совмещения стандартизированных работ наглядно показывает соотношение времени ручной работы, ходьбы, ожидания (время ожидания в данном случае должно стать первоочередным целевым показателем совершенствования!). Время ожидания начинается, после того как оператор запускает робот. Это время следует использовать для дополнительной работы по созданию ценности.
На рисунке 6-7 изображена та же работа, дополненная еще одной задачей — загрузкой и второй разгрузкой автоматического оборудования. Заметьте, что при этом время выполнения операций «перекрывается», т.е. время рабочего цикла автомата от момента начала операции превышает время такта. Здесь важно отметить, что цикл работы второго автомата завершается до того, как оператор готов заново загрузить его (станок оснащен устройством автоматической разгрузки, что весьма распространено в Toyota). В Toyota считают, что машина может подождать оператора, однако оператор никогда не должен ждать машину. Не забывайте: оператор важнее машины.