Практика дао Toyota. Руководство по внедрению принципов менеджмента Toyota Лайкер Джеффри
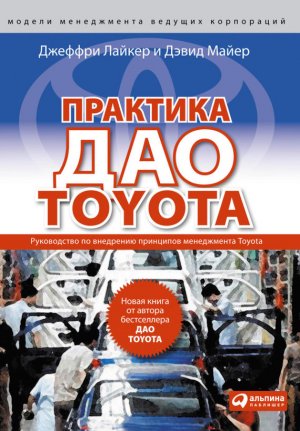
Ведомость производительности процесса
В ведомости производительности процесса (здесь не показана) фиксируется мощность оборудования, используемого в процессе. Время цикла оборудования, т. е. количество времени, необходимое на обработку одного изделия, следует учитывать, принимая во внимание запланированные простои при смене инструмента и переналадке. В первую очередь это относится к станочным операциям, где имеет место износ инструмента и не обойтись без его замены, однако ведомость применима и к таким операциям, как литье под давлением и штамповка, где необходимо учитывать время переналадки. Такая ведомость — полезный инструмент выявления операций, представляющих собой узкие места.
Использование этого документа очень похоже на планирование загрузки производственных мощностей, которым занимается большинство ин-Ясенеров-технологов при выборе оборудования. Основная цель — определить, соответствует ли мощность оборудования потребностям производства. Расчеты производятся с учетом времени полезной работы, времени цикла на единицу продукции и потерь времени при смене инструмента или иных видах переналадки.
Помимо попыток разработать процедуру стандартизированной работы, опираясь на перечисленные выше мифы, сложности возникают при попытках стандартизировать всю работу, а не ее составляющие, а также работу с большой вариацией. В большинстве случаев работа представляет собой набор задач, выполняемых одним человеком.
К примеру, задачей оператора может быть сборка какого-либо изделия. При этом он сам подбирает и доставляет необходимые материалы и подает готовые изделия на следующую операцию. Сборка изделия является относительно единообразной работой, которую несложно задокументировать, но как быть с остальными видами работ? Они осуществляются непоследовательно, иногда однократно в течение нескольких циклов. Как соединить эти два абсолютно разных вида работ в ведомости стандартизированной работы? Обычно это попросту невозможно. Элементы работы, необходимые для сборки продукта, добавляют ценность и подлежат стандартизации. Как правило, операторы в Toyota не занимаются ни подбором материала, ни транспортировкой готовой продукции, поскольку эти виды деятельности отвлекают от работы по добавлению ценности. Транспортировкой материалов и деталей занимается другой работник, например транспортный рабочий, и его работу стандархизуют отдельно.
В главах 4 и 5 мы рассказывали о необходимости изолировать вариацию, чтобы обеспечить возможность стандартизации. Следующий пример иллюстрирует сложности при стандартизации работы, которой присуща высокая вариация. Общее правило: сначала изолировать вариацию и лишь потом приступать к стандартизации.
Конкретная ситуация: три задачи на одном рабочем месте
В данном случае работа оператора представляет собой обслуживание двух автоматических резательных станков, которые нарезают и обрабатывают заготовки стального прутка.
Первая операция состоит в проверке качества и обслуживании станка (удаление металлической стружки и перемещение готовой продукции). Оператору приходится регулярно осматривать некоторое количество деталей. Такие проверки представляют собой повторяемую операцию, которая выполняется каждый час (стандартное время цикла).
Вторая операция представляет собой установку прутка. Эта работа тоже постоянно повторяется, однако время цикла варьируется в зависимости от вида изготавливаемых деталей в диапазоне от часа до двух.
Третья операция — это наладка станка и замена инструмента при его износе и при переходе с одного вида изделий на другой. Данный вид работы повторяется раз в несколько часов, а периодичность выполнения этой операции отличается высокой вариабельностью.
Таким образом, работа включает как регулярно повторяемые операции однотипного характера, так и операции, отличающиеся высокой вариабельностью времени выполнения. Когда все они производятся на одном рабочем месте, установить четкую последовательность операций, которая поддается стандартизации, невозможно. Дело осложняется тем, что каждый оператор отвечает за два станка. Если один из них нуждается в переналадке, а в другой требуется установить пруток, станок, требующий переналадки, простаивает, пока не освободится оператор. Если оба станка одновременно нуждаются в переналадке, один из них ждет своей очереди. Нередко потерянное таким образом время составляет несколько дней. Если оба станка работают и оператор занят только первой операцией, у него остается лишнее время, которое он проводит в ожидании. Получается, что при таком сценарии и станок, и оператор простаивают в ожидании.
Чтобы изолировать вариацию, было решено перераспределить выполнение операций, поручив их разным операторам. Первую задачу поручили работнику, который отвечал теперь за обслуживание и проверку качества на десяти станках. Вторую операцию — установку прутка — выполнял второй работник, который тоже отвечал за десять станков, наладкой всех десяти станков занимались еще два человека. В результате такого перераспределения обязанностей «высвободился» один оператор, что позволило создать Должность лидера команды для дополнительной поддержки линии.
Еще один позитивный результат состоял в том, что теперь наладкой оборудования занимались два человека и это позволило снизить общее время наладки. Вследствие этого размеры партии снизились, повысилась частота перехода с одного изделия на другое, а общий объем запасов сократился. Благодаря появлению должности лидера команды рабочие места отсутствующих больше не пустовали, что обеспечивало стабильный выход продукции изо дня в день. Станки были оснащены сигнальной системой андон, чтобы оператор мог своевременно установить новые заготовки и станок не простаивал. Кроме того, сигнал андон оповещал оператора о том, что в ближайшее время понадобится наладка станка или смена инструмента. Такие сигналы позволяли операторам заранее подготовить необходимый материал и инструменты. В результате преобразований общая производительность процесса возросла на 30%.
Как уже говорилось выше, распространен миф о том, что описание стандартизированной работы должно висеть на видном месте, чтобы оператор мог сверяться с ним, выполняя свою работу. На предприятиях Toyota такое описание обычно вывешивается в проходе, а не перед оператором, поскольку в первую очередь эти сведения интересуют лидера команды и лидера группы, которые проверяют соблюдение стандартов.
Но разве аудиты не означают, что менеджмент использует принудительные меры, а сама стандартизированная работа представляет собой проявление бюрократической косности? В обстановке враждебности любые проверки порождают конфликты и напряжение. Однако в условиях, где первоочередное внимание уделяется устранению потерь для лучшего обслуживания потребителя, аудиты стандартизированной работы служат средством поддержания стабильности процесса. Они объединяют менеджмент и рабочих. Операторы часто отклоняются от стандартной процедуры, когда видят проблемы и ищут «обходные пути». Аудит со стороньГ~иенеджмента обеспечивает выявление коренных проблем и их оперативное исправление, что позволяет возобновить работу в соответствии со стандартом.
Чтобы привыкнуть к новому методу, нужно время
Изменение метода работы (стандартизированная работа) требует времени на адаптацию. Расстаться с прошлым бывает непросто,
поскольку наше тело продолжает действовать по привычке. Так, если вы сменили автомобиль с механической коробкой передач на машину с АКПП, какое-то время ваша рука будет непроизвольно тянуться к рычагу переключения передач (не обнаруживая его на прежнем месте!). Пока оператор не адаптируется к новому методу, следует оказывать ему постоянную поддержку.
Аудит в Toyota могут инициировать два обстоятельства. Первое — проблема. Что стало причиной дефекта? Почему оператор систематически отстает? Часто наблюдение за оператором на протяжении нескольких циклов и сравнение его действий со стандартной процедурой работы позволяет выявить истоки проблемы. Второе — настало время аудита. Наряду с графиком профилактического обслуживания в Toyota существует график аудитов рабочих стандартов. Чтобы провести профилактический ремонт, в Toyota не ждут, пока станок сломается. Точно так же необязательно ждать, пока оператор допустит ошибку, чтобы проверить, соблюдается ли процедура стандартной работы.
Аудит позволяет выявить отклонение от стандартного метода. Мы часто ошибочно полагаем, что отклонения случаются по вине оператора. Разобравшись, в чем дело, мы можем обнаружить, что причиной отклонения была неисправность оборудования или проблема с продуктом. Смысл проверки в том, чтобы найти причину проблемы и устранить ее.
На многих предприятиях Toyota существует визуальная система для проверки соблюдения стандартов. Каждая рабочая группа использует доску визуального отображения информации с карточками, которая называется «доска камисибай» (книга историй). На заводе NUMMI лидеры групп каждый день проверяют соблюдение требований стандартизированной работы и точность документов по стандартизированной работе в одном из процессов. Это позволяет за месяц проверить каждое рабочее место. При этом на карточке, которая содержит перечень вопросов, помечается, какие отклонения были выявлены и какие меры приняты. На доске предусмотрено специальное гнездо для карточек по каждому процессу. После проверки карточка в порядке очередности аудитов помещается в свободную прорезь соответствующего гнезда. Если в ходе аудита обнаружена проблема, карточка вставляется в прорезь темной стороной наружу — это служит сигналом к принятию мер. Заместители менеджеров ежедневно проверяют доски, чтобы удостовериться, что аудит проведен должным образом. Они наугад вынимают одну из карточек и проверяют соответствие процесса стандартизированной работе совместно с лидером группы. В заводских цехах находится около 90 таких досок.
Сравните эту ситуацию с практикой множества компаний, которые «применяют» стандартизированную работу. Карта стандартизированной Работы заполнена по всем правилам и вывешена на видном месте, скорее всего, инженером по организации производства. Порой эти карты оформлены очень красиво и даже содержат фотографии отдельных операций. Они повешены так, чтобы их видел оператор. Этими картами никто не пользуется, зато их можно продемонстрировать посетителям, которые скажут-. «Это похоже на бережливое производство».
После первоначальной стандартизации операций начинается самое интересное. Пришло время спросить: «Каковы дальнейшие возможности?» Теперь ответ дать труднее. Мы должны заново переосмыслить нашу основную цель — выполнять больше работы, добавляющей ценность, с меньшими затратами, иными словами, изготавливать больше изделий, расходуя меньше ресурсов. Не спешите браться за дальнейшие совершенствование. Сначала давайте разберемся, что мы будем делать с нашими достижениями. Важно сориентировать совершенствование на потребности, а не просто заниматься им потому, что оно возможно. Совершенствование как таковое возможно всегда!
К примеру, если вы намерены и дальше сокращать время наладки, что вы будете делать с освободившимся временем? Важно ли вам уменьшить размер партии, повысить гибкость, или вы заинтересованы в наращивании объема? Нередко мы видим компании, которые берутся за сокращение времени наладки, добиваются ощутимых результатов, но не знают, куда девать освободившееся время, и продолжительность наладки мало-помалу возвращается на исходный уровень. Тот же феномен отмечается и при прочих «усовершенствованиях». После усовершенствования вы должны перестроить процесс таким образом, чтобы поддержание достигнутого уровня стало условием дальнейшего успеха. Более высокий уровень должен стать новым стандартом, а от лишнего нужно избавиться. Если в поддержании нового уровня нет необходимости, любые достижения быстро сойдут на нет.
ПОДСКАЗКА
На освоение нового стандарта требуется время
Пока люди привыкают к новому методу, производительность нередко слегка снижается. Не спешите возвращаться к прежним методам. Продолжайте наблюдать за происходящим, следя за тем, чтобы работники придерживались нового метода, а любые необходимые поправки вносились немедленно.
Многие затрудняются определить, чем отличается время такта от времени цикла. Время такта — это не инструмент. Это понятие используется при планировании работы и описывает темп потребительского спроса. Чтобы рассчитать данный показатель, нужно разделить время, отведенное на производство изделий, на число изделий, которое запросят потребители в течение данного временного интервала. Полученный результат может, к примеру, говорить о том, что для удовлетворения потребительского спроса каждые три минуты нужно изготавливать одну деталь. Просто? Тем не менее время такта часто понимается неправильно. А определение времени такта для линий, производящих множество разных продуктов, темпы спроса на которые различны, превращается в весьма мудреную задачу.
Рассмотрим такой пример: если рабочее время в течение одной смены составляет 400 минут, а спрос составляет 400 изделий за смену, время, которое отводится на единицу продукции (время такта), составляет одну минуту (на каждое изделие). Чтобы удовлетворить спрос, время цикла каждой операции в среднем не должно превышать одну минуту. Если время цикла (фактическое время, которое требуется для выполнения всех действий по одной работе) превышает время такта, данная операция станет узким местом и, чтобы уложиться в график, придется работать сверхурочно. Если время цикла меньше, чем время такта, возникнет перепроизводство или ожидание.
Самая трудная задача — определить потребительский спрос. В большинстве случаев (если вы не поставщик Toyota) спрос имеет значительные колебания. Как определить время такта, если спрос — величина непостоянная? Следует понимать, что время такта служит «точкой отсчета» при планировании работы, и легко представлять, каковы могут быть последствия неправильного определения точки отсчета.
Первым делом следует признать, что время цикла отдельных операций — время, необходимое для выполнения работы, — колеблется не слишком сильно, если они стандартизированы. В примере, который приводился выше, цикл работы оборудования составляет 23 секунды, а время работы оператора и время на ходьбу — 56 секунд. Общее время цикла составляет 75 секунд и может незначительно колебаться в зависимости от скорости работы оператора, который подготавливает детали для автоматической сварки. Это значит, что производительность данного процесса будет Достаточно стабильной при отсутствии сбоев, вызванных отказами оборудования. Какое влияние оказывают на данную операцию значительная вариация спроса? Никакого! Время рабочего цикла может варьироваться лишь в пределах нескольких секунд. Как удовлетворить спрос, если он растет? Можно увеличить рабочее время (например, за счет сверхурочной работы, если спрос растет не слишком сильно). Использование понятия времени такта не изменит сложившуюся ситуацию.
Так как же определить спрос и время такта? Выберите показатель спроса, который будет достаточно высок, чтобы потребность была удовлетворена большую часть времени. Допустим, к примеру, что спрос колеблется в диапазоне от 10 ООО до 20 ООО единиц продукции в месяц, а средний показатель составляет 16 ООО единиц в месяц. Какое число следует выбрать? Отчасти это зависит от ситуации, но обычно мы рекомендуем ориентироваться на более высокий показатель. И вот почему. Предположим, что мы используем максимальный показатель — 20 ООО. Рассчитывая время такта, мы получим при этом более низкий показатель (на изготовление единицы продукции отводится меньше времени). Затем сравниваем время цикла и время такта для выявления расхождения. Смысл такого расчета в том, что чем значительнее расхождение, тем больше требуется усовершенствований, чтобы достичь времени такта, а потенциал совершенствования определяется объемом потерь в процессе.
Сталкиваясь с подобной задачей, сэнсэй Toyota скажет: «Нет проблем», имея в виду, что потерь всегда предостаточно и добиться необходимого усовершенствования, несомненно, можно. Единственная опасность завышения темпов спроса в том, что в этом случае придется потратить больше сил, чтобы выйти на заданное время такта. Вряд ли вам захочется тратить силы впустую, искусственно завышая показатель спроса (тем самым снижая время такта), но это не столь уж серьезная проблема. Если процесс усовершенствован сверх фактической потребности, можно сократить объем ресурсов или заняться расширением продаж.
Время такта определяет единый ритм выполнения всех операций в потоке создания ценности. График загрузки операторов представляет собой действенный визуальный инструмент, который позволяет увидеть соотношение между временем цикла и такта. В некоторых случаях она помогает ответить на вопрос «А что, если?» в отношении потенциальных возможностей процесса. На рис. 6-8 представлен график загрузки операторов, составленный для сравнения времени цикла отдельных операций в потоке создания ценности со временем такта. В данном случае компания хотела увеличить объем производства, чтобы удовлетворить возросший по приблизительным оценкам спрос. В компании хотели знать, насколько значительные изменения потребуются, чтобы выйти на гипотетическое время такта 90 секунд на изделие. Мы видим, что пока в заданное время такта не укладываются две операции.
Если две эти операции будут оптимизированы, какой объем усовершенствований необходим, прежде чем будет достигнуто следующее «плато» выравнивания? На рис. 6-9 обозначено следующее «плато». Несколько операций имеют время цикла около 60 секунд. Если сократить время цикла Двух самых продолжительных операций до 60 секунд, это позволит потоку создания ценности выдавать одно изделие каждые 60 секунд. Означает ли это, что нужно немедленно взяться за решение данной задачи? Если мы решим ее, несмотря на то что время такта, рассчитанное с учетом фактического спроса, превышает 60 секунд, мы придем к перепроизводству — основному виду потерь.
После сокращения времени цикла двух самых продолжительных операций стало понятно, что фактическое время такта, необходимое для удоа-летворения спроса, составляет 80 секунд. Это позволило произвести перегруппировку операций и сократить их число. В нашем случае после сокращения времени шлифовки и полировки общая продолжительность всех операций составила 645 секунд. Если разделить 645 секунд рабочего времени на время такта 80 секунд, мы получим восемь операций с соответствующим временем такта вместо исходных 12. Таким образом, за счет перегруппировки мы можем сократить количество операций на треть, обеспечив время такта 80 секунд. Если речь идет о процессах ручного труда, это означает высвобождение 4 операторов (примечание: эти «лишние» операторы могут быть использованы для создания системы лидеров команд, описанной в главе 10). Интересно отметить, что, если сбалансировать операции, ориентируясь на менее продолжительное время такта 60 секунд, понадобится 11 операторов (645/60 = 10,75). Таким образом, повышение скорости может обойтись дороже.
Учитывайте время такта при планировании работы и выборе необходимых усовершенствований. Если вы выбрали слишком большое время такта, вы не удовлетворите спрос, а это хуже, чем выбрать слишком маленькое время такта и превысить спрос (при условии, что для удовлетворения ошибочно определенного спроса вам не понадобилось привлекать дополнительные ресурсы). Всегда проще остановить производство при избыточной производительности, чем увеличить объем производства при недостаточной производительности. Если вы сомневаетесь, лучше ориентироваться на более высокие показатели спроса и меньшее время такта.
Применение средств визуального контроля — важнейший момент в процессе стандартизации. К сожалению, значение этой составляющей бережливого процесса очень часто недооценивается. Мы нередко слышим: «Они всего-навсего занимаются 5S». Возможно, виной тому примеры средств визуального контроля, которые приводятся чаще всего, скажем разметка пола, которая показывает, где должны стоять контейнеры с мусором и прочие объекты в рабочей зоне. Работники считают подобную разметку лишней — они ведь и так понимают, что где находится! Другой пример — значки, обозначающие место для различных предметов и видов материала. «Мы и так знаем, что и куда класть». Однако когда работника просят рассказать более подробно, например описать процесс поставки материала, назвать его стандартное количество или допустимый минимум и максимум запасов, обычно ответы становятся менее вразумительными.
На рис. 6-10 показано, что средства визуального контроля предназначены прежде всего для того, чтобы определить желаемое «нормальное» состояние (стандарт) и быстро заметить отклонение от стандарта. Как мы видели, на каждом рабочем месте требуется соблюдать массу технических условий и процедур. Добиться того, чтобы каждый работник знал их наизусть, практически невозможно, и даже если записать их в тетрадку, это не поможет немедленно вспомнить их при необходимости.
Нередко люди настолько убеждены, что знают стандарты, что любое визуальное напоминание кажется им излишним. Оценить подлинное зна-
ние стандартов несложно. Попросите нескольких работников описать конкретный метод выполнения работы. Есть ли возможность установить, что все делается, как положено? Ситуация на окрасочном участке, описанная ниже, говорит о том, что, если возможность быстро оценить соблюдение стандарта отсутствует, отклонения не замечаются и не прекращаются.
Вот что происходит, когда стандарт всем известен, но не визуализирован.
Речь идет об окрасочном участке с тремя отдельными камерами покраски. На этом участке основная линия разветвлялась на три, каждая из которых подавала изделия к одной из трех камер. При таком разветвлении основной линии для обеспечения потока продукта очень важно, чтобы подача изделий осуществлялась в определенной последовательности с учетом цвета и модели. Это единственный способ избежать чрезмерной нагрузки на какую-либо из камер и заторов на линии. Наблюдение за окрасочным участком (стояние в кругу) показало, что потоку продукта через одну или две камеры часто препятствует затор перед другой камерой. Из-за этого весь процесс подачи изделий останавливался, что сказывалось на показателях совокупного времени простоя линии. Проблема была чрезвычайно острой, поскольку заторы при окраске сдер-
живали работу всего предприятия (это единственный участок на заводе, через который проходят все изделия) и не позволяли реализовать потенциальные возможности системы в полной мере.
Менеджер участка покраски и работники, которые занимались подачей изделий, единодушно согласились, что при подаче продукции необходимо соблюдать определенную последовательность номенклатуры позиций, и даже выработали единое мнение о том, какой должна быть эта последовательность. Однако при этом каждый замечал, что «они» не всегда соблюдают правила. (Кто такие эти таинственные «они», было не совсем понятно.) Более глубокий анализ показал, что желательный метод (пока еще не стандарт) не имеет четкого определения и описан довольно невразумительно. Это описание включало формулировки такого рода: «Не более двух изделий этого вида в час», «Данное изделие может следовать за одной из трех названных моделей», «Не более шести изделий этого цвета в час». Было понятно, что попытки запомнить предложенную последовательность обречены на неудачу (описание включало слишком много переменных). Эти правила мог выучить разве что тот, кто выполнял данную работу изо дня в день, и если постоянный работник отсутствовал, найти ему замену вне группы было практически невозможно.
Для определения порядка подачи изделий на окраску, который учитывал бы все требования к цвету и ассортименту, была создана команда из трех человек, хорошо знакомых с процессом. Команда потратила почти три дня, чтобы разработать последовательность, удовлетворяющую всем параметрам и условиям. Представьте, как сложно было запомнить такую последовательность наизусть! Неудивительно, что операторы не соблюдали правила, ведь даже сформулировать их оказалось весьма непросто.
Команда разработала доску для визуального отображения последовательности подачи. Завершив операцию, работник должен был передвинуть на доске магнит с цветной маркировкой, показав этим, что задание выполнено. Такие нововведения пришлись по душе операторам, поскольку требования были сформулированы четко и ясно и больше никто не кричал на них из-за того, что они не соблюдают правила. Остановки линии стали случаться значительно реже, а количество изделий (каждое изделие включает несколько субкомпонентов), которые проходили через окрасочный участок в течение дня, возросло с 80 до 110 и более. Освоив систему визуализации стандартов, операторы усовершенствовали доску отображения информации, продолжая уточнять требования и выравнивать номенклатуру изделий (подробнее об этом рассказывается в следующей главе).
Разработка стандартизированной работы — это первый шаг. Он не только позволяет определить стандартный способ выполнения операции, но и предполагает процесс анализа, в ходе которого выявляются потери. Устранение этих потерь — неотъемлемая часть стандартизации. После того как стандарт разработан, а операторы обучены, надо регулярно проверять, соблюдаются ли стандарты, и если нет, то почему. Следует поощрять стремление операторов к подаче предложений по оптимизации процесса. Такие предложения вносятся в стандарты по мере их пересмотра.
После того как стандарт разработан, его условия следует визуализировать, чтобы любое отклонение было заметно сразу. Пример окрасочного участка свидетельствует об эффективности стандарта, представленного визуально в доступной для всех форме. Визуальные индикаторы становятся действенным инструментом, лишь когда используются для визуального контроля, показывая различие между стандартными и фактическими условиями (рис. 6-11). Соблюдение стандарта позволяет «рассеять туман», оптимизировать поток и повысить общую эффективность. В Toyota визуальным средствам контроля соблюдения стандартов придается огромное значение. Необходимо еще раз подчеркнуть, как важно сделать процесс «зримым».
Вопросы для самопроверки
Начните это упражнение как обычно — взяв карту текущего состояния потока создания ценности, пройдите траекторию потока. Если вы уже внесли какие-то усовершенствования и установили связи между некоторыми операциями, значит, вы уже разработали ряд стандартов. Попробуйте представить будущее состояние потока создания ценности и обозначьте установленные связи на карте будущего состояния.
1.Определен ли потребительский спрос и рассчитано ли время такта?
A.Определите текущий щтод мониторинга времени такта на каждой операции.
Б. Можно ли увидеть и понять данный стандарт? Если нет, определите, какие корректирующие действия обеспечат визуальное оповещение о стандартном времени такта, и внесите их в план действий.
B.Измеряется ли соблюдение заданного времени такта в процессе выполнения работы? Записываются ли эти измерения? Если нет, внесите эти действия в план.
Г. Периодическое отставание от времени такта — показатель нестабильности. Установите причины нестабильности и разработайте корректирующие меры, которые позволят повысить стабильность и обеспечить соблюдение стандарта (время такта) на протяжении по меньшей мере 85% рабочего времени.
2.Заданная и контролируемая связь между процессами определяет
условия договора (стандарт) между процессом-поставщиком и
процессом-потребителем. Проанализируйте связь между процессами и ответьте на следующие вопросы:
А. Существует ли визуальное оповещение о стандартах?
—Что именно должно делаться?
—Когда это следует делать?
—Кто должен это делать?
—Как определить успешность сделанного?
Б. Какова текущая возможность обеспечить соблюдение стандарта (удовлетворить потребителя)? Если показатели соблюдения стандарта ниже 85%, определите, что следует предпринять для повышения результативности, и составьте план соответствующих мероприятий.
3.Выявите операцию, которая периодически отклоняется от стандарта. Постойте в кругу и понаблюдайте за следующими условиями:
А. Можно ли повторить последовательность действий? (Если
постоянные сбои мешают задокументировать этапы работы, метод не считается повторяемым.) Если нет, составьте список причин вариации и корректирующих мер, необходимых для стабилизации процесса.
Б. Составляют ли помехи, вызванные проблемами с оборудованием и качеством, более 10% рабочего времени процесса? (Не упустите из виду незначительные проблемы, например: неудобно устанавливать детали в зажимное приспособление и извлекать их.) Составьте план устранения проблем, которые создают помехи в процессе.
4.После того как основные проблемы решены и процесс стал надежным и стабильным, постойте в кругу и понаблюдайте за работой, выявляя потери.
A.Используйте ведомость стандартизированной работы, чтобы задокументировать основные этапы работы.
Б. Нарисуйте схему рабочей зоны и обозначьте на ней место выполнения каждой операции.
B.Отметьте потери и разработайте план оптимизации процесса, который позволит сократить их объем.
Г. Используйте ведомость стандартизированной работы для схематического изображения предполагаемых изменений, представив устранение потерь как сокращение общего времени цикла.
Д. Как сказалось сокращение потерь (и снижение времени цикла) на общей сбалансированности работы и потоке в целом?
5. Работая над заданием главы 5, вы измерили время цикла каждой операции. Выявите в потоке создания ценности процессы, препятствующие потоку (время цикла которых превышает время такта), и займитесь целенаправленным сокращением потерь в этих процессах, используя стандартизированную работу как инструмент анализа.
:
Глава 7
ВЫРАВНИВАНИЕ: БУДЬ ПОДОБЕН ЧЕРЕПАХЕ, А НЕ ЗАЙЦУ
Дао Toyota изобилует парадоксами, и один из наиболее поразительных — это парадокс выравнивания: тот, кто медлителен, но упорен, опережает того, кто спешит, но движется рывками, как в известной притче о зайце и черепахе, которую часто цитируют старые знатоки производственной системы Toyota (TPS). Черепаха продвигается вперед неторопливо, но уверенно, тогда как заяц сначала мчится сломя голову, а потом лежит, выбившись из сил. Подобный образ действий мы частенько наблюдаем и в жизни. Сначала мы напряженно трудимся, чтобы успеть в срок, а потом расслабляемся. В Toyota всегда предпочитали работать размеренно и неторопливо.
Помимо равномерного распределения объема работ выравнивание предполагает равномерное сочетание видов работ. Рационализировать этот аспект нелегко. Если вы производите два вида деталей, скажем А и В в равном количестве, кажется естественным чередовать как можно более крупные партии А и В. Это представляется особенно правильным, когда переключение с А на В требует времени. И все же Toyota предпочитает изготавливать эти изделия в ином порядке — А, В, А, В... Выравнивание номенклатуры продуктов ближе к идеальному потоку единичных изделий.
В наши дни модным увлечением стало «производство на заказ». Здесь задают тон такие компании, как Dell Computer, которые изготавливают лишь то, что потребитель заказывает через Интернет, благодаря чему практически избавляются от запаса готовых изделий. К сожалению, то, что хорошо для сборщика, не всегда хорошо для поставщика. Dell опирается на своих поставщиков, которые держат значительное количество запасов вблизи ее сборочного завода, оплачивая при этом складские расходы. С точки зрения Toyota, Dell не устранила коренной причины проблемы, а просто переложила ее на плечи других компаний. Пока поток создания ценности не станет бережливым, кто-то обязательно будет нести повышенные затраты — в данном случае это поставщики, у которых снижается прибыль и растут расходы.
Кто-то может спросить: «Но раз Toyota — бережливый производитель, разве она не изготавливает продукцию в точном соответствии с заказами потребителей, педантично придерживаясь порядка поступления этих заказов, как Dell?» Безусловно, нет! Порядок поступления заказов от потребителей нестабилен и непредсказуем, а основа TPS — стабильный, выровненный график работ. Еще один парадокс Toyota — для создания бережливого потока создания ценности иногда целесообразно держать некоторое количество запасов готовой продукции — самых дорогостоящих запасов. Это позволит вам обеспечить поставку заказанной продукции и при этом работать по выровненному графику. В этой главе мы поговорим, зачем выравнивать производство и как это делается.
Термин «хейдзунка», как мы уже говорили, означает «сглаживать, выравнивать, делать плавным». Но часто при переводе слова на другой язык его концептуальное значение теряется. В контексте бережливого производства данный термин означает «выравнивание ассортимента продукции в течение определенного отрезка времени», что позволяет производить каждую деталь ежедневно (или даже каждые несколько часов). Хотя потребитель редко заказывает продукцию партиями, тем не менее ее производство часто организовано именно так. Идея состоит в том, чтобы изготавливать продукцию в небольших количествах, приближая объемы производства к фактическому спросу.
Однако это лишь часть концепции. Создание идеально плавного процесса производства требует высочайшей гибкости и восприимчивости к изменению потребительского спроса.
Нам никогда не приходилось сталкиваться с ситуацией, когда потребители на радость производителю заказывали изо дня в день одно и то же количество одних и тех же деталей. В жизни все далеко не так просто! Постоянно меняющийся спрос порождает множество проблем в потоке создания ценности: возникает необходимость адаптации ресурсов к постоянно меняющимся потребностям. Если колебания спроса значительны, чтобы к ним приспособиться, нужно наращивать объем запасов. Когда спрос на пике, мощностей не хватает, но во время спада возникает избыток, В такой ситуации приходится поддерживать чрезмерный объем ресурсов, рассчитанный на пиковый спрос, и мириться с недоиспользованием ресурсов в моменты спада.
Колебания потребительского спроса порождают так называемый «эффект кнута». Легкий взмах умелой руки, держащей кнут, — и вот уже его кончик со свистом рассекает воздух, грозя нанести удар сокрушительной силы. Подобным образом небольшая вариация потребительского спроса на конечной операции передается по всему потоку создания ценности с растущим на каждой последующей операции размахом. Эффект кнута особенно ощутим для удаленных поставщиков или процессов. В результате этого эффекта для удовлетворения значительных колебаний спроса требуется все больший объем ресурсов (и затрат).
В такой ситуации внедрение стандартизированной работы становится проблематичным, а то и вовсе невозможным. Не забывайте, что при стандартизации мы пытаемся равномерно распределить работу между операциями с учетом времени такта, которое определяется ритмом потребительского спроса. Если время такта падает и опускается с каждым взмахом кнута, выравнивание и стандартизированная работа тоже будут подвержены неконтролируемым колебаниям. О какой стандартизации может идти речь, если время такта постоянно меняется? Это основа второй формы хейдзунка — выравнивание во имя внутренней стабилизации потока создания ценности (это выравнивание распространяется и вовне, на поставщиков). Такое выравнивание спроса обеспечивает основу стандартизации, вокруг которой выстраиваются все потребности в ресурсах, как показано на рис. 7-1.
Принимаясь за выравнивание производства, вы избираете нелегкий путь. Такой выбор должен делаться сознательно, так как он имеет ряд последствий. Выравнивание требует безупречного согласования во времени и гибкости, обеспечивающих циклический выпуск небольших партий продукции. Создать гибкий процесс непросто. Любые проблемы, кото-
рые вызывают задержки, выявляются немедленно, но приводят к сбоям в графике.
Например, выравнивание номенклатуры продукции означает, что в течение дня производятся небольшие объемы каждого вида изделий, что требует переключения с одного изделия на другое. Нередко это связано со сменой материала, оснастки и т. д. Переналадка требует времени. Если процесс переналадки не стандартизирован и не продуман до мелочей, частые переналадки приведут к потерям и график будет нарушен. С точки зрения традиционного массового производства любые потери производственного времени есть зло. С точки зрения системы бережливого производства уменьшение размера партии есть благо. Тому, кто взялся за выравнивание, не остается ничего другого, как снижать время переналадки.
Некоторым не по душе постоянное повышение требований, так как работа становится напряженной. К тому же возникает риск не выйти на заданные показатели производительности. Наш разум инстинктивно стремится защитить нас от какого бы то ни было риска, ведь сознательный риск противен природе человека. В этом-то и сложность дао Toyota. Нам приходится сознательно подвергать себя риску. Чтобы свести риск к минимуму, нужно тщательно все продумать, усердно работать и грамотно управлять процессом. Следует понимать, что, взявшись за создание береж-
ливого процесса, вы беретесь за дело, которым предстоит заниматься всю жизнь. Бесперебойная работа процесса требует неусыпного внимания.
Так зачем вам это нужно? Обратившись к практике работы любого традиционного предприятия, мы услышим такие слова, как «авралы» и «всплески». Речь идет об изменениях спроса и объема работы в потоке создания ценности. Время многих менеджеров уходит на борьбу с этими колебаниями — они пытаются приспособиться к ситуации, перераспределяя ресурсы и беспрерывно занимаясь «тушением пожаров», вызванных очередным сокрушительным пиком спроса. Эти менеджеры спят и видят тот день, когда им удастся справиться с очередной волной и вернуть ход вещей в «нормальное» русло. К сожалению, за одной волной спроса обычно следует другая — как это и бывает в океане. Бесконечные попытки поймать волну не позволяют заниматься процессом совершенствования. Вместо стабилизации менеджмент большую часть времени занимается сдерживанием.
Что, если спрос на ваш продукт стабилен? Как это скажется на вашем процессе? Если поступающие в поток создания ценности сигналы о «потребительском» спросе носят устойчивый характер (кавычки показывают, что хейдзунка показывает не «фактический» потребительский спрос), это оказывает сглаживающее влияние на все процессы. Такое сглаживание делает возможной стандартизацию объема ресурсов, что значительно упрощает планирование и контроль.
Давайте еще раз обратимся к модели потока создания ценности, данной в главе 3. Она изображена на рис. 7-2. Мы видим, что будущее состояние потока создание ценности включает «доску» или «ящик» хейдзунка. Это распространенный способ визуального представления выровненного графика. Каждая ячейка ящика соответствует определенному отрезку времени (например, с 8:00 до 8:15), в течение которого рабочий берет канбан производства, подает его на операцию, задающую ритм, в качестве очередного заказа и забирает готовые изделия в соответствии с предыдущим заказом. Есть множество способов сделать то же самое; так, иногда заказы ежечасно вывешиваются на доске. Здесь возможны разные решения, но все они имеют одну цель: сделать очевидным временной интервал (питч) — с момента поступления заказа до его выполнения и количество продукции, которое нужно изготовить в течение питча (определение питча см. в книге Учитесь
Рис. 7-2. Будущее состояние потока создания ценности с подробной проработкой составляющих
видеть бизнес-процессы). Таков механизм, поддерживающий процесс выравнивания. Оператор, задающий ритм потоку, всегда знает, работает он быстрее или медленнее, чем нужно.
Что происходит, если процесс, задающий ритм потока создания ценности, соблюдает такой график? Он будет обрабатывать детали, постепенно изымая их из супермаркета предыдущей операции. Поскольку процесс, задающий ритм, работает по выровненному графику, изъятия тоже выровнены. Предположим, что сборочный процесс — это задающий ритм процесс и ему требуются три вида деталей — А, В, С, которые используются для производства трех разных видов конечного продукта. Если сборка конечного продукта выровнена, должно быть выровнено и потребление А, В и С. Это позволяет свести объем запасов А, В и С в супермаркете к минимуму. Если же сборщики вдруг станут целый день использовать только деталь А, а поставщик поместит в супермаркет количество деталей А, рассчитанное лишь на часть рабочего дня, запас деталей А на сборке быстро закончится, и она остановится. Поэтому если система рассчитана на выровненный график, очень важно следить за его соблюдением, иначе запас деталей иссякнет. Забирая из супермаркета исходные материалы, операция побуждает производство пополнить запас деталей в супермаркете, т. е. изъятие деталей служит для поставщика сигналом к пополнению запаса. Опять-таки, если операция, задающая ритм, выровнена, сигналы поступают к поставщику равномерно, что смягчает негативный «эффект кнута», который заставляет поставщиков работать в режиме авралов и простоев, из-за того что завод-потребитель вносит изменения в графики так, как удобно ему. При выровненном графике поставщики знают предъявляемые к ним требования и могут уверенно планировать свою работу. Они могут сбалансировать ресурсы с учетом известного времени такта и внедрять бережливое производство, повышая качество и снижая затраты.
Мы часто слышим, как компании жалуются, что не могут выровнять свою работу из-за потребителей. Отдел управления производством разрабатывает выровненный «график» для первой петли потока, даже если потребительский спрос не сглажен. Обратите внимание, что у отдела управления производством есть два источника информации для создания выровненного графика. Один из них — стрелка, идущая непосредственно от потребителя, — сигнал о сборке на заказ, а другой — стрелка от супермаркета с готовыми изделиями — сигнал о сборке про запас. Это общепринятый в бережливых системах способ работы с широким ассортиментом продукции. Изделия, спрос на которые, как вам известно, стабильно высок, изготавливаются про запас. Этот запас хранится в супермаркете и пополняется по мере поставки потребителю при помощи системы, подобной канбан. Изделия, спрос на которые менее предсказуем, изготавливаются по заказу. Отдел управления производством отслеживает фактический поток потребительских заказов и карточки канбан, поступающие из супермаркета. Обычно имеется еще третий поток — создание страхового буферного запаса, который пополняется, если фактических заказов и заказов канбан недостаточно, чтобы обеспечить дневную загрузку работой. За счет такой структуры потока заказов отдел управления производством располагает инструментами для выравнивания графика.
Никакого дополнительного внешнего планирования не требуется. Если речь идет об изготовлении про запас, нужды потребителя (представленные супермаркетом) очевидны для всех. Для определения состояния запасов применяется система канбан, позволяющая контролировать объем запасов. Для визуального отображения динамики уровня запасов свободные карточки канбан можно помещать на доску, при этом каждая карточка свидетельствует о снижении уровня запасов. Сведения об изделиях, производимых на заказ, тоже могут помещаться на доску, что позволит видеть, что изготавливается по фактическому заказу потребителя в текущий момент времени, и пополнять супермаркет и страховой запас. Установленная очередность становится простой и наглядной. Когда в Toyota говорят: «Оператор планирует свою работу сам», речь идет именно об этом. Оператор не занимается планированием и составлением графиков в традиционном смысле слова, т. е. не решает, что и когда следует изготовить, он просто использует информацию, которая поступает к нему с помощью визуальной системы, и принимает решения, руководствуясь заданной процедурой.
ПОДСКАЗКА
Чтобы извлечь максимальную выгоду, определите самые значимые позиции
Выравнивание применительно ко всем производимым продуктам может оказаться нецелесообразным из-за очень низкого или спорадического спроса на некоторые изделия. Прежде чем анализировать перечень продуктов, к которым следует применить выравнивание, вам, возможно, придется изолировать вариацию (см. главу 3) или использовать методику изоляции, названную нами «нарезка на кусочки», о которой пойдет речь далее. Выявите важнейшие продукты на основных участках и начните с тех, которые дадут вам максимальную прибыль.
Выравнивание графика с устойчивым многократным повторением питча в течение дня расценивается как передовая практика бережливого производства. Определенный уровень выравнивания необходим уже на этапе стабилизации (см. главу 4), чтобы иметь базис для расчетов времени такта и сформировать основной поток. На начальных стадиях питч, как правило, имеет большую продолжительность: нередко он равен рабочему дню. Такая величина питча обеспечивает фундамент для стабилизации, ее достижение не столь непосильная задача. Попытки преждевременно установить более краткий питч могут выявить слишком много проблем — с которыми существующая система не сможет справиться.
Стараясь как можно точнее определить уровень выравнивания, легко впасть в состояние «аналитического паралича». В работе имеет место несколько факторов, которые делают точное определение практически невозможным. Во-первых, как часто говорят о взаимных фондах: «Показатели в прошлом не гарантируют таких же показателей в будущем». Мы строим планы на будущее, опираясь на прошлые результаты, но это не значит, что они будут именно такими. Во-вторых, закон больших чисел означает, что чем больше объектов мы включаем в исследование, тем меньшее влияние оказывает каждый из них. Если мы рассматриваем совокупность значений объемов производства за год, случайные всплески сказываются на общем среднем значении не столь ощутимо. На языке неспециалиста это значит, что, если мы имеем дело с достаточно большой выборкой, «шум» отфильтровывается. В-третьих, информация, которую вы анализируете, может оказаться некорректной. Она может отражать не фактический спрос, а заказы, которые генерирует внутренняя система планирования потребностей в материалах (MRP) для удовлетворения «спроса». На количестве таких заказов сказывается множество факторов, и этот показатель далеко не всегда отражает фактический спрос. Наконец, как вы увидите далее, занимаясь выравниванием ассортимента продукции в целом с целью обеспечить необходимый баланс, неизбежно приходится вносить некоторые незначительные поправки. Мы рекомендуем выбрать ориентировочно приемлемый объем каждого вида продукции и приниматься за выравнивание процесса. Каким бы тщательным ни был ваш анализ, впоследствии вам непременно придется вносить коррективы.
Определите кратное для структуры выравнивания
ПОДСКАЗКА
Оптимальна структура выравнивания, кратная двум, т. е. структура повторяется ежедневно, через день, каждый четвертый день или максимум каждый шестой день. Если суточный спрос, умноженный на шесть, дает такой низкий объем производства изделия, что работать с ним по-прежнему нецелесообразно, вам придется снизить время наладки или перевести данное изделие в «другую» категорию, пока время наладки не снизится до необходимого уровня. В нашем примере изделия, спрос на которые был примерно в два раза меньше, чем на те, что изготавливались ежедневно, производились через день. Изделия, спрос на которые составлял примерно четверть от спроса на изделия, изготавливаемые ежедневно, производились каждый четвертый день.
Помимо питча выравнивания требуют еще три составляющих:
1.Объем выпуска, т.е. количество определенного вида продукта, которое следует произвести в течение заданного отрезка времени (питча).
2.Ассортимент, т.е. соотношение количества разных моделей, изготавливаемых в течение питча, например изделий А, В, С и т.д.
3.Последовательность изготовления продукции, которая представляет собой порядок изготовления заданного объема при заданном ассортименте. Этот порядок может предполагать последовательное изготовление нескольких изделий одной-модели, например А, А, А, В, В, В, С, С, С, или носить иной характер, скажем А, С, А, В, А, С.
Названные составляющие перечислены в порядке от простого к сложному. Учитывая исходное состояние процесса, вам, возможно, придется начать с простейшего выравнивания объема и структуры ассортимента на основе достаточно длительного питча, равного продолжительности смены или рабочего дня. Мы то и дело слышим, как кругом на все лады превозносят поток единичных изделий и последовательное выравнивание производства, однако текущая ситуация может сделать достижение этой цели для вашего предприятия делом далекого будущего. Не забывайте, что Toyota понадобилось 50 лет, чтобы достичь таких результатов, как сегодня, при этом компания считает, что во многих отношениях она до сих пор не совершенна. Главное — сделать усилие, чтобы добиться ощутимого улучшения, и оценить, на что вы способны, но не надрываться, иначе дело кончится провалом.
Начните с анализа фактического производства или объема продаж для каждого продукта в течение последних 12 месяцев. Так вы определите, что значит высокий, низкий и средний объем спроса. Нанесите фактические показатели на график, который в отличие от обычной таблицы цифр даст возможность наглядно увидеть «средневзвешенный показатель». Минимумы и максимумы позволят вам увидеть лишь амплитуду, а несколько пиковых значений могут исказить представление о среднем. Нанесение фактических показателей на график позволит вам визуально определить оптимальные позиции для выравнивания.
Окончательное решение о выравнивании объема в определенной мере носит субъективный характер. В большинстве случаев в Toyota выбирают показатель, составляющий примерно 80% максимального спроса (если данный всплеск спроса не представляет собой единичный случай), поскольку разницу между 80 и 100% можно компенсировать за счет сверхурочной работы (восемь часов в неделю). Для расчета времени такта используется показатель выровненного спроса. В предыдущей главе мы говорили о времени такта как о расчетном параметре. Если при определении выровненного объема спроса показатель в 80% кажется вам недостаточно достоверным, лучше ошибиться в сторону небольшого завышения спроса. На практике, когда вы определяете количество, которое удовлетворит предполагаемый выровненный суточный спрос, оно оказывается либо слишком большим, либо слишком маленьким, либо в точности соответствующим спросу (что менее вероятно). Проблема в том, что определить это заранее довольно сложно из-за вариации в производстве («туман»). Как только процесс стабилизируется, «туман» слегка рассеивается и правильный уровень делается более очевидным, что позволяет легко внести нужные поправки.
Уже первый цикл выравнивания позволит частично избавиться от потерь, вызванных попытками угнаться за колебаниями спроса, и позволит высвободить дополнительные мощности, не доступные раньше. Многие компании обнаруживают, что даже первичное выравнивание позволяет им «идти в ногу» с заказами, и убеждаются, что предыдущие предположения о спросе вели к перепроизводству. В такой ситуации можно либо сократить объем ресурсов, либо, если возможно, увеличить объем продаж.
Рассмотрим конкретный пример. Данные таблицы 7-1 представляют собой упрощенный вариант реальной ситуации, однако сами понятия применимы и к более сложным условиям. В приведенном примере мы занимаемся выравниванием производства 10 деталей, обозначенных буквами от А до J, спрос на каждую из которых колеблется. Спрос на изделия, попавшие в категорию «прочие», меньше, чем у перечисленных выше, и составляет в среднем 125 единиц, выравнивание применительно к отдельным
ЧАСТЬ III. СОЗДАНИЕ БЕРЕЖЛИВЫХ ПРОЦЕССОВ НА ВАШЕМ ПРЕДПРИЯТИИ Таблица 7-1. Требуемые объемы по видам деталей
Деталь | Среднесуточный спрос |
А | 250 |
В | 220 |
С | 210 |
D | 128 |
Е | 125 |
F | 75 |
G | 60 |
Н | 45 |
I | 45 |
J | 35 |
Прочие | 125 |
Всего | 1318 |
Таблица 7-2. Вариант структуры выравнивания производства |
День 1 | День 2 | День 3 | День 4 | День 5 | День 6 | День 7 | День 8 | |
А (КД) | 250 | 250 | 250 | 250 | 250 | 250 | 250 | 250 |
В(КД) | 220 | 220 | 220 | 220 | 220 | 220 | 220 | 220 |
С(КД) | 210 | 210 | 210 | 210 | 210 | 210 | 210 | 210 |
D(4fl) | 256 | 0 | 256 | 0 | 256 | 0 | 256 | 0 |
Е (ЧД) | 0 | 250 | 0 | 250 | 0 | 250 | 0 | 250 |
F (ЧД) | 150 | 0 | 150 | 0 | 150 | 0 | 150 | 0 |
G (К4Д) | 0 | 240 | 0 | 0 | 0 | 240 | 0 | 0 |
Н (К4Д) | 0 | 0 | 0 | 180 | 0 | 0 | 0 | 180 |
I (К4Д) | 180 | 0 | 0 | 0 | 180 | 0 | 0 | 0 |
J (К4Д) | 0 | 0 | 140 | 0 | 0 | 0 | 140 | 0 |
Прочие | 59 | 155 | 99 | 215 | 59 | 155 | 99 | 215 |
Итого | 1325 | 1325 | 1325 | 1325 | 1325 | 1325 | 1325 | 1325 |
Целевойпоказатель | 1325 | 1325 | 1325 | 1325 | 1325 | 1325 | 1325 | 1325 |
КД — каждый день; ЧД — через день; К4Д — каждые четыре дня |
видам этих деталей не производится. Общий суточный объем для всех видов продукции, включая «прочие», выровнен. На самом деле объем про-изводства «прочих» изделий варьируется, что позволяет увеличить или
Таблица 7-3. Альтернативная структура выравнивания производства | ||||||||
---|---|---|---|---|---|---|---|---|
День 1 | День 2 | День 3 | День 4 | День 5 | День 6 | День 7 | День 8 | |
А (КД) | 250 | 250 | 250 | 250 | 250 | 250 | 250 | 250 |
В(КД) | 220 | 220 | 220 | 220 | 220 | 220 | 220 | 220 |
С(КД) | 210 | 210 | 210 | 210 | 210 | 210 | 210 | 210 |
D(4TO | 256 | 0 | 256 | 0 | 256 | 0 | 256 | 0 |
Е (ЧД) | 250 | 0 | 250 | 0 | 250 | 0 | 250 | 0 |
F(4fl) | 150 | 0 | 150 | 0 | 150 | 0 | 150 | 0 |
G (К4Д) | 0 | 240 | 0 | 0 | 0 | 240 | 0 | 0 |
Н (К4Д) | 0 | 0 | 0 | . 180 | 0 | 0 | 0 | 180 |
I (К4Д) | 0 | 180 | 0 | 0 | 0 | 180 | 0 | 0 |
J (К4Д) | 0 | 0 | 0 | 140 | 0 | 0 | 0 | 140 |
Прочие | 0 | 225 | 0 | 325 | 0 | 225 | 0 | 325 |
Итого | 1336 | 1325 | 1336 | 1325 | 1336 | 1325 | 1336 | 1325 |
Целевойпоказатель | 1325 | 1325 | 1325 | 1325 | 1325 | 1325 | 1325 | 1325 |
КД — каждый день; ЧД — через день; К4Д — каждые четыре дня |
сократить общее времени работы, если фактический спрос больше или меньше запланированного. Этй коррективы не отражаются на результатах выравнивания для изделий A-J.
Структура производства разработана с учетом требуемых объемов производства деталей, применительно к которым производилось выравнивание. Данная структура призвана свести к минимуму негативные последствия переналадки (процесс был оптимизирован, но продолжительность переналадки пока превышает желаемую). Детали A-С производятся каждый день (КД), а детали D-F производятся через день (ЧД). Детали G-J производятся каждые четыре дня (К4Д — да-да, мы знаем, что наша задача производить каждую деталь каждый день, но до этого мы еще не дошли!).
Один из вариантов структуры выравнивания представлен в таблице 7-2. Суточная потребность, составляющая 1318 единиц продукции, была округлена на незначительную величину — до 1325. Как мы уже говорили, это не столь важно, поскольку имеет место вариация количества деталей в категории «прочие». Такая структура является более ровной и позволяет ежедневно производить некоторое количество «прочих» деталей. Если среднее количество заказов на «прочие» систематически превышает указанное количество, можно рассмотреть иную структуру.
В таблице 7-3 представлена альтернативная структура, где все детали, производимые в режиме ЧД, изготавливаются в один и тот же день наряду с производством деталей в режиме КД. Производство деталей в режиме КД осуществляется по-прежнему — они изготавливаются изо дня в день. Детали, производимые в режиме ЧД и К4Д, обеспечивают возможность маневра в зависимости от потребностей процесса. К примеру, в данном случае вся совокупность деталей, производимых в режиме ЧД, изготавливается в один и тот же день. Возможны и иные варианты структуры. Цель — обеспечить оптимальный выровненный объем структуры по горизонтали, т. е. по каждой детали в пределах заданного временного интервала — выровненный общий объем деталей по вертикали и выровненную структуру на протяжении питча. Эта структура определяет последовательность изготовления деталей А-J. Выравнивание в хронологическом аспекте осуществляется в пределах заданного воспроизводимого интервала. В нашем случае структура повторяется каждые четыре дня и производство каждого изделия выровнено в пределах четырех дней. Обычно временное окно при выравнивании в Toyota составляет месяц, в его основе лежит воспроизводимая структура одного дня. Примечание: линия основной сборки автомобилей применяет структуру выравнивания, ориентированную на высокую периодичность питча с учетом ассортимента изготавливаемых автомобилей, а вспомогательные операции, которые производят детали, пополняя супермаркет или «резерв для отбора», работают в соответствии с иной структурой выравнивания, производной от основной.
Заметьте, что в соответствии с альтернативной структурой общий объем в первый, третий, пятый и седьмой день превышает целевой суточный показатель. Это не слишком серьезная проблема, поскольку количество остается в разумных пределах (обычно максимальное отклонение не превышает 10%). При работе с фактическим спросом в большинстве случаев не удается добиться таких равномерных показателей, как в этом примере. Для начала попытайтесь выровнять показатели насколько возможно. Создав условия для производства по выровненному графику, вы сможете получить более основательное представление о фактической потребности и соответствующим образом откорректировать структуру выравнивания.
Составить выровненный график куда проще, чем производить продукцию в соответствии с планом! Скорее всего, поначалу вы обнаружите множество препятствий, мешающих придерживаться графика. Следует систематически выявлять и устранять эти препятствия, чтобы обеспечить стабильность (отследить причины, создающие помехи для хейдзунка, и применить метод решения проблем для их устранения). Теперь выровненный график следует считать «голосом потребителя». Правда, потребителя не совсем реального — речь идет о соглашении, которое представляет нужды потребителя, выровненные на благо вашего процесса.
Поскольку речь идет о потребителе, вы должны измерять и отслеживать свою способность его удовлетворить. Если в какой-то момент времени вы не можете обеспечить заданный объем, ассортимент или последовательность, это эквивалентно «невыполненному заказу» (т. е. неудовлетворенному потребителю, хотя, возможно, речь и не идет о невыполнении фактического заказа). Вам следует приучить людей относиться к хейдзунка как к голосу потребителя и как к важнейшей задаче, стоящей перед потоком создания ценности.
Поздравляем! Добравшись до этого этапа построения бережливого производства, вы должны быть готовы к тому, что самое интересное только начинается. После того как усовершенствования стандартизованы, процессы стабилизированы и связаны в поток создания ценности, вы приступаете к циклу непрерывного совершенствования. Да-да, вам придется проходить через все это вновь и вновь, до бесконечности. Хорошая новость в том, что с каждым успешным проходом очередного витка спирали непрерывного совершенствования путь дальше становится все проще, поскольку вы набираетесь опыта, а сопротивление переменам слабеет. Теперь любые изменения будут приносить прямую пользу процессу в целом. Иными словами, на смену «карманным» преобразованиям, которые не отражались на общем результате, придут усовершенствования, которые будут позитивно сказываться на эффективности всего потока создания ценности.
Но не все так хорошо. С этого момента совершенствование будет достигаться постоянным ужесточением требований ко всем операциям с целью сокращения времени выполнения заказа, повышения гибкости и стабильности, снижения уровня запасов и укрепления позиций вашей компании в долгосрочной перспективе. Эффект от таких действий будет постепенно возрастать, и каждый этап совершенствования будет давать прирост, границы которого будут находиться в заданных пределах. Созданная система позволяет определить желаемый результат и гарантировать его достижение.
Этот метод повышает нагрузку на поток создания ценности и вызывает разрыв его слабого звена, что порождает нестабильность. Обнаружение слабого звена позволяет мобилизовать ресурсы для решения выявленных проблем. Этот цикл повторяется вновь и вновь, как показывает модель спирали непрерывного совершенствования в главе 3 (рис. 3-4). В ходе каждого последующего цикла совершенствования выявляются все менее значительные проблемы. Таковы хорошие и плохие новости. Плохая новость состоит в том, что устранять проблемы будет все труднее. Хорошая новость в том, что вы добьетесь значительной оптимизации процесса, а уровень вашей квалификации будет расти по мере повышения сложности проблем.
После завершения связывания потока создания ценности к отдельным его участкам начинают предъявлять повышенные требования. Помните, что происходит с потоком создания ценности, если скорость процесса, задающего ритм, меняется? Этот процесс задает новый ритм всех остальных процессов в потоке создания ценности. Если выровненный график, который задает определенную ассортиментную структуру продукции, меняется, необходимо откорректировать все процессы таким образом, чтобы обеспечить поддержку новой структуры ассортимента.
Такое пошаговое выравнивание или уплотнение потока создания ценности стимулирует совершенствование. Речь идет о планируемом, управляемом процессе, при котором совершенствование идет вполне определенным образом. Так, если объем запасов в супермаркете сократился, это окажет определенное влияние на процесс-поставщик. Это может потребовать, к примеру, более частых переналадок, а как следствие — сокращения ее продолжительности. Любое изменение стандартного элемента потока создания ценности порождает потребность в совершенствовании.
В связанном потоке создания ценности существуют особые точки управления, которые воздействуют на другие процессы в потоке. Поскольку отдельные операции в потоке создания ценности связаны, изменения в одном месте (точке управления) требуют изменения всех процессов, снабжающих эту точку. Так как точка управления служит важнейшей операцией в потоке создания ценности, надо строго следить за ней для обеспечения стабильной работы потока создания ценности, а управление этой точкой поможет вам понять, как извлечь из всего потока создания ценности максимум возможного.
Одна из основных точек управления — выровненный график. Он представляет собой основу для времени такта. Работа задающего ритм процесса основана на времени такта, поэтому заданный ритм передается на все остальные операции. Зная точку управления, менеджеры могут эффективно выявлять неполадки в работе и заниматься непрерывным совершенствованием.
Если процесс, задающий ритм, стабильно производит заданный объем продукции и обеспечивает производство заданной ассортиментной структуры в нужной последовательности в соответствии с выровненным графиком, поток создания ценности удовлетворяет требования потребителя (следующий этап — это сокращение затрат). Однако если процесс, задающий ритм, не отвечает требованиям выровненного графика, этот процесс будет первым участком, где следует постоять в кругу. Этот удобный наблюдательный пункт даст возможность оценить, обеспечено ли надлежащее снабжение процесса, задающего ритм. Если нет, продвигайтесь к началу потока, чтобы выявить слабое звено. Если да, проверьте, не препятствует ли работе процесса, задающего ритм, одна из следующих за ним операций. (Правила запрещают перепроизводство, а значит, если процесс, задающий ритм, блокируется идущим за ним процессом, это будет заметно сразу.) Визуализация связи между процессами позволяет быстро выявить помехи в потоке, облегчая управление потоком создания ценности.
Такой точкой управления является канбан. Сокращение числа карточек11 канбан ведет к сокращению общего объема запасов в системе. Такое сокращение следует проводить систематически, как по мере совершенствования процесса, так и для того, чтобы стимулировать потребность в совершенствовании. Количество запасов, необходимое для поддержания процесса, может использоваться как мерило совершенствования. Устойчивое снижение уровня запасов — показатель отлаженного процесса.
Канбан может влиять и на оборачиваемость запасов. Если количество изделий на одну карточку канбан снижается (например, уменьшается объем контейнера), канбан будет проходить свой «цикл» чаще, ускоряя перемещение запасов в процессе. Кроме того, снижение количества запасов на единицу канбан ведет к повышению уровня гибкости при пополнении
Сокращение запасов — это мерило успеха, но не самоцель
При освоении бережливого производства многие считают сокращение запасов первоочередной задачей. Есть множество способов достижения этой цели, включая разного рода хитрости. Однако лучше поставить задачу создать связанный поток и использовать объем запасов как критерий успеха. Для управления запасами используется канбан, регулируя число карточек канбан, несложно оценить эффективность процесса. Управление запасами с помощью канбан стандартизировано, и возможность недобросовестной манипуляции запасами снижается.
запасов и снижает размеры рабочей зоны и объем потерь. Как ни странно, предпочтительно иметь «в системе» больше единиц канбан. Например, если общий уровень запасов составляет 2000 штук, лучше иметь 20 канбан — по одному на 100 изделий, чем 2 канбан — по одному на 1000 изделий. Очень трудно чувствовать спрос, если в системе только две карточки канбан, и каждый раз, когда карточка возвращается, приходится немедленно поставлять следующую партию изделий.
Хейдзунка не только выравнивает все процессы, но и определяет продолжительность питча. Поскольку в течение заданного питча материалы расходуются со стандартной скоростью, можно определить характеристики процесса пополнения запаса материалов. Пополнение запаса материалов подчиняется основной работе, добавляющей ценность, а значит, не следует заниматься определением «траектории» или методов подачи материалов до базовой стандартизации основного процесса.
Приведенный далее пример показывает, как выровненный график определяет процедуру пополнения материальных запасов. Это позволяет стандартизировать работу рабочих, в том числе траекторию их перемещения в течение питча или серии питчей. Общее количество материала стандартизируется, а количество материала в контейнере может регулироваться в зависимости от длительности питча. Для иллюстративных целей мы предполагаем, что в рассматриваемом процессе обеспечен высокий уровень хейдзунка, все изделия изготавливаются в строго определенной последовательности, а общая продолжительность рабочего времени составляет восемь часов. Спрос составляет 400 изделий, а весовые показатели количества каждого вида изделий показаны в таблице 7-4.
Таблица 7-4. Количество деталей как относительный показатель | ||
---|---|---|
Наименование детали | Количество в течение 8 часов | Веса (по количеству) |
А | 200 | 4 |
В | 100 | 2 |
С | 50 | 1 |
D | 50 | 1 |
Всего | 400 |
ПОДСКАЗКА
Установите питч исходя из имеющихся условий
Если у вас уже есть определенный опыт освоения бережливого ~производства, скорее всего, вы не станете устанавливать питч
продолжительностью в один час. Мы рекомендуем продвигаться вперед, сокращая питч каждый раз наполовину. Если сейчас вы перемещаете материал ежедневно (или питч не определен), начните с питча продолжительностью в одну смену. Когда воспроизводимость процесса улучшится, сократите питч вдвое.
С учетом требуемого количества и весовых показателей количества повторяющаяся структура хейдзунка (которая позволяет свести к минимуму размер партии) такова: ABACABAD — ABACABAD — ABACABAD.
Чтобы определить питч для регулярной работы согласно данной модели, разделим 8 часов на объем спроса (400 изделий) и умножим на количество изделий в модели выравнивания (питч):
28 800 секунд (8 часов) в день / 400 изделий =
= 72 секунды на одно изделие
Тогда:
72 секунды на одно изделие X 8 изделий в течение питча =
= 576 секунд на питч (9 минут 36 секунд), или 6,25 питч-циклов в час.
Предположим, мы хотим, чтобы рабочий занимался подачей материала ежечасно (питч пополнения запаса материала). В таблице 7-5 показаны расчеты количества контейнеров, которое понадобится перемещать, если цикл пополнения запасов будет составлять один час.
Таблица 7-5. Расчеты количества контейнеров, перемещаемых в течение питча | |||||
---|---|---|---|---|---|
Наименование детали | Веса (по количеству) | Повторений модели выравнивания в час | Потребность в час | Количество в контейнере | Контейнеров на питч |
А | 4 | 6,25 | 4 X 6,25 = 25 | 10 | 2,5 |
В | 2 | 6,25 | 2 X 6,25 = 12,5 | 5 | 2,5 |
С | 1 | 6,25 | 1 X 6,25 = 6,25 | 5 | 1,25 |
D | 1 | 6,25 | 1 X 6,25 = 6,25 | 5 | 1,25 |
На основании требований к перемещению материалов в течение часового цикла можно осуществить стандартизацию работы с учетом маршрута перемещения рабочего и других операций, которые он обслуживает.
Имея дело с 5-10 видами продуктов, применить хейдзунка не так уж сложно. Но что делать, если ассортимент готовой продукции чрезвычайно широк? Одна компания заявила, что изготавливает 25 ООО наименований изделий. Ее представители были убеждены, что в их случае хейдзунка исключается. Как осуществить выравнивание при таком многообразии? Здесь может пригодиться процесс, названный нами «нерезка на кусочки». Он представляет собой метод разбивки общей совокупности на группы продуктов со сходными характеристиками (если угодно, что-то вроде принципа «разделяй и властвуй»),
В ходе «нарезки» мы группируем всю продукцию по потокам создания ценности по принципам схожести самих продуктов и этапов их обработки. Такая группировка позволяет объединить сходные изделия и ограничить их количество — одна «нарезка» содержит, скажем, 5000 изделий вместо 25 ООО. Представьте, что вся совокупность ваших продуктов и процессов представляет собой прямоугольник. Рассортировав продукцию по «семействам» в соответствии с потоками создания ценности с близкими параметрами и этапами обработки, мы нарезаем прямоугольник по горизонтали на несколько частей (рис. 7-3). Наибольшего эффекта удается достичь, если в первую очередь «нарезать» самый значимый поток создания ценности.
Если разбить полученный срез (рис. 7-4) так, чтобы выделить из 5000 самые важные изделия, можно сфокусировать усилия еще больше. Кроме того, дальнейшее разбиение потока создания ценности включает выбор участка (операции), которому следует уделить первоочередное внимание при внедрении бережливого производства. Обычно чтобы решить, как классифицировать поток, нужно учесть объемы производства всех видов продукции. Когда ассортимент группируется с учетом этого фактора, неизменно обнаруживается, что всю продукцию можно разбить на три группы: ведущая группа, пользующаяся самым значительным спросом; вторая группа, объем которой составляет примерно половину объема первой; и третья группа, которая вдвое меньше второй (объемы в примере выравнивания, приведенном выше, типичны). Как правило, первая группа содержит меньшее по сравнению с двумя другими количество наименований, но составляет значительную долю общего объема изделий. (Если вы вспомнили при этом принцип Парето, вы абсолютно правы, здесь действует именно он. Данный метод позволяет изолировать «значимое меньшинство» от «незначительного большинства».)
Мы начали с 25 ООО наименований. Оказалось, что 35% общего объема продаж компании приходится всего на 100 продуктов! Это позволяет значительно сузить сферу приложения усилий. Дополнительная «нарезка» показала, что объемы производства изделия № 1 в десять раз выше, чем изделия № 50. В итоге было решено заняться выравниванием производства только 50 наименований продукции (из 25 000). Двигаясь по спирали непрерывного совершенствования, мы последовательно занимаемся отдельными срезами, добавляя новые с каждым следующим циклом. Когда производство первых 50 изделий будет успешно выровнено, а поток создания ценности — отлажен и стабилизирован, можно заняться следующими 50 изделиями.
Сфокусировавшись изначально на 50 изделиях, можно добиться максимальных результатов при минимуме усилий. Многие ошибочно полагают, что, если выровнять все разом невозможно, значит, метод хейдзунка неприменим. На самом деле математическая сторона вопроса проста. Что лучше— 0% времени иметь 100% нестабильно производимых продуктов или 100% времени иметь 25% полностью стабильных продуктов? Принцип «все или ничего» здесь неуместен.
По мере того как возможности процессов растут, можно переходить к выравниванию все меньших и меньших объемов. Может оказаться, что в выравнивании всех без исключения изделий нет смысла. Подумайте сами: если производство 75% изделий выровнено — а следовательно, на 75% выровнены общие потребности в ресурсах, — можно выделить оставшиеся 25% времени использования ресурсов (людей и оборудования) на производство изделий по мере необходимости. При этом сырьевые материалы распределяется между выровненными и невыровненными изделиями, а в расчет порядка пополнения запасов без труда вносятся соответствующие поправки.
Конкретная ситуация: выравнивание объема работ при изготовлении корпусной мебели на заказ
В этой компании объем работ на разных операциях ощутимо колебался в зависимости от изготавливаемой продукции, что порождало множество проблем, включая низкое качество (рабочим часто приходилось работать в спешке), простои линии и непредсказуемый график производства. Поскольку продукция изготавливалась по индивидуальным заказам, в компании были убеждены, что стандартизация процессов невозможна.
В ситуациях такого рода трудности могут показаться непреодолимыми. Множество взаимосвязанных проблем порождается волновым эффектом распределения объема работ (представьте горб, который перемещается вдоль тела змеи, проглотившей крысу). Как случается
нередко, компания пыталась бороться с симптомами, далекими от первопричины (там, где проблема давала о себе знать), выстраивая замысловатые схемы переброски рабочей силы туда, где образовался горб, хотя истоки проблемы были совсем в другом месте. В компании интуитивно догадывались об этом, но были убеждены, что изменить ситуацию невозможно, поскольку каждое изделие было единственным в своем роде и объем заказов ощутимо разнился, как и набор комплектующих (шкафы, двери, выдвижные ящики). В компании считали, что, поскольку темп заказов определяется потребителем, значит, выровнять объем работ невозможно.
Первым делом нужно было перестать относиться к каждому изделию, как к уникальному, оценить его с точки зрения содержания работы и уяснить, как это содержание сказывается на процессах в потоке создания ценности. Если взглянуть на ситуацию немного со стороны, становится очевидна схожесть как самой продукции, так и операций по ее обработке. В данном случае мы сразу заметили, что значительная часть объема работ приходится на одни и те же комплектующие. В основном это были шкафы, выдвижные ящики, полки, двери, детали общего назначения и элементы декора. Кроме того, мы обнаружили ряд общих для всех изделий характеристик, которые сказывались на объеме работ. В первую очередь это относилось к отделочному покрытию. Оно было двух типов: пропиточная краска и основная краска. В ходе дальнейшего изучения вопроса выяснилось, что каждый тип включал две разновидности. Поверхность, обработанная пропиткой, могла быть полированной или неполированной, а поверхность, покрытая основной краской, — светлой или темной.
Анализ потока создания ценности показал, что участок, на котором изделия покрывались краской или пропиткой, представлял собой процесс, задающий ритм. На этот участок стекались все изделия, которые после нанесения отделочного покрытия двигались дальше в порядке завершения работы. Выравнивание объема работ на операции, задающей ритм, должно было выровнять нагрузку на последующие операции (включая окончательную обработку) и обеспечить равномерную подачу сигналов на операции-поставщики.
При этом вновь встал вопрос: как выровнять объем работ, если все изделия разные? Ответить на него помогло стояние в кругу. Объем работ определялся типом отделки и площадью обрабатываемой поверхности. Рабочие подтвердили, что обработка пропиткой с последующей полировкой более трудоемка, чем обработка без полировки, а нанесение темной краски — более трудоемкий процесс, чем нанесение светлой, поскольку окончательная отделка с помощью темных эмалей требует шлифовки и полировки. Кроме того, мы отметили, что обработка изделий, имеющих большую площадь поверхности, а также обработка большого количества мелких деталей отличались высокой трудоемкостью. Становилось ясно, что решить проблему можно, определив заданную последовательность обработки выровненного
ассортимента. Но как это сделать, когда ни одно изделие не похоже на другое?
Нам было нелегко переубедить рабочих и их мастеров, которые боролись с этой проблемой долгие годы. Нам был нужен переменный стандарт, т. е. стандарт, допускающий вариацию. Речь шла об устойчивой (стандартизированной) вариации, поскольку подход к вариации был определен.
Анализ данных о выпуске продукции показал, что доля изделий, обработанных пропиткой, составляет 75%, а окрашенных — 25%. Полированные изделия (обработка которых была более трудоемкой) составляли около 25% изделий, покрытых пропиткой. Количество изделий, окрашенных темной и светлой краской, было примерно одинаково, с небольшим перевесом в сторону светлых (менее трудоемких). Это позволило нам определить первичную модель выравнивания, которая задавала структуру ассортимента с учетом отделочного покрытия и вида конечной обработки. Поскольку фактический суточный ассортимент не всегда соответствовал усредненному, модель учитывала условия вторичного характера. Заданная модель могла иметь, к примеру, следующий вид:
Поскольку трудоемкость окраски в светлый тон и обработки пропиткой без полировки была одинаковой, модель допускала замену одного вида работ другим. Цель состояла в том, чтобы обеспечить как можно более равномерное распределение объема работ и при этом соблюсти верное соотношение между отдельными видами работ.
Вторым срезом модели стали отдельные виды изделий. Команда решила, что начинать любую работу следует с элементов декора, поскольку они требуют особой обработки. Мелкие детали обрабатывались в конце, поскольку эти операции, как правило, были менее трудоемки и представляли собой своеобразный «разделитель» между заказами, позволяя сменить краску и т.д. Кроме того, между отдельными заказами предусматривались два пустых стеллажа, чтобы предупредить попадание чужеродного отделочного материала на окрашиваемые изделия. Была разработана модель выравнивания, которая предусматривала надлежащую последовательность размеров и площади поверхности для каждого заказа. Так же, как и при окраске, некоторые типы деталей оказались схожи и были взаимозаменяемыми (стандартизированная вариация).
Последовательность изготовления изделий имела следующий вид: элементы декора — шкаф — двери — шкаф — выдвижные ящики — полки — двери — шкафы — ящики/двери — при необходимости описанная последовательность повторяется — детали общего применения — пустой стеллаж — пустой стеллаж (следующий заказ) элементы декора...
Вторичные правила учитывали тип отделки (ее трудоемкость). Так, на стеллаже можно было разместить два маленьких шкафа или один большой (в случае полировки или покрытия темной краской только один независимо от размера). При обработке дверей на стеллаж укладывалось шесть дверей при окраске в светлые тона или обработке пропиткой без полировки и четыре двери при полировке или окраске в темные тона. Тот же принцип применялся к выдвижным ящикам и полкам.
В данной ситуации было трудно определить объем производства. Количество деталей, стеллажей и заказов было подвержено вариации. Компания поставила задачу выполнять 25 заказов в день, исходя из этого, мы определили целевой показатель объема, несмотря на то что общий объем работы варьировался. Однако эта вариация не отражалась на равномерности распределения объема работ в течение дня, поскольку с ней можно было справиться, незначительно меняя продолжительность рабочего дня. Структура ассортимента изделий включала два среза — первичная последовательность изделий с учетом типа отделки и вторичная последовательность отдельных видов изделий. Первичная последовательность учитывала тип отделки и соответствовала потребительскому спросу и объему работ, а вторичная последовательность обеспечивала надлежащее распределение объема работ. Таким образом, последовательность выполнения заказов, учитывающая тип отделки и виды изделий, позволила выровнять объем работ.
Эти преобразования стали базисом для стандартизации работы и потока. Выравнивание объема работ сократило количество простоев и сгладило поток на остальных операциях. Дальнейшие мероприятия по связыванию операций позволили уменьшить скопления запасов, которые раньше были обычным делом.
При изготовлении изделий по индивидуальным заказам точно измерить результативность непросто. Всегда присутствует вариация, которая искажает любой показатель. В таком случае следует проанализировать более длительный период (месяц), поскольку более продолжительный временной интервал сглаживает влияние вариации. Иными словами, из месяца в месяц мы начнем замечать повышение результативности, которая измеряется сравнением общей продолжительности рабочего времени с общим объемом продаж в долларах. Если рассматривать результативность за период в шесть месяцев, влияние вариации будет еще менее ощутимым и сдвиг среднего значения будет виден сразу.
Начиная обучать людей выравниванию объема работ, мы то и дело слышим: «У отдела продаж своя система вознаграждения, а продажи в нашей компании всегда на первом месте. Они продают все, что только могут, а мы на производстве должны изготавливать то, что они скажут. У них же каждую неделю все меняется на 100%, а то и больше». Более тщательный анализ данных обычно показывает, что уровень фактического спроса куда более единообразен, чем кажется производственникам.
В одной производственной компании, которая занималась офисной мебелью и изготавливала множество разных шкафов для документов, поток заказов, поступавших на завод, отличался нестабильностью. Тем не менее компания придерживалась принципа 100%-й сборки на заказ, и производственникам приходилось постоянно заниматься «тушением пожаров», чтобы выполнить все поступившие от потребителей заказы. В результате на всех стадиях производственного процесса скапливалось огромное количество запасов, а о времени такта не было и речи. Когда заказчики шкафов для документов интересовались временем выполнения заказа, им говорили, что срок составляет от шести до восьми недель. Работники завода трудились до седьмого пота, чтобы выполнить все поступившие заказы, которых было полным-полно, но время выполнения заказа растягивалось на шесть-восемь недель из-за работы, не добавляющей ценности. Почему бы не использовать этот временной буфер для выравнивания графика? Если бы завод имел запас готовых шкафов хотя бы тех видов, которые пользуются максимальным спросом, можно было бы сократить время выполнения заказа, составляющее шесть-восемь недель, и выровнять график, разработав более эффективный процесс. В итоге завод сгруппировал всю продукцию в три семейства в соответствии с потоками создания ценности, создал резерв готовых изделий, чтобы выровнять график, освободил четверть полезной площади завода для новых направлений и значительно сократил общий уровень запасов, время выполнения заказа и общие затраты.
Однако реализовать разумный план действий бывает не так-то просто. Компании, производящей мебель, пришлось изменить подход к размещению заказов, которым занимался отдел продаж. Пришлось изменить также процесс сбыта и подход к составлению графиков, которыми занимался отдел управления производством. Всеми этими процессами ведали разные функциональные подразделения, методы работы которых не менялись десятки лет. Никто не верил, что новая система будет работать, и все предрекали ей провал. Чтобы преодолеть сопротивление, потребовались четко проработанная концепция будущего состояния и мощная поддержка со стороны высшего руководства.
Нередко вознаграждение сотрудников отдела продаж зависит от объемов реализации за месяц или квартал. Такая система материального стимулирования порождает неравномерную структуру сбыта, поскольку для повышения продаж в конце периода менеджеры по продажам дают крупные скидки. Отдел продаж в Toyota сознает важность выровненного графика производства. При этом даже в Toyota производственники нередко ворчат на отдел продаж, и все же здесь эти подразделения действуют куда более согласованно, чем в других компаниях. Такое сотрудничество поощряется высшим руководством, которое понимает, что политика продаж влияет на «гладкость» графика, лежащем в основе TPS.
Применять системный подход и мыслить в масштабах предприятия непросто. Выравнивание графика, которое является основой бережливой системы, требует оценивать ситуацию через призму потока создания ценности.
Конкретная ситуация:
выравнивание графика в проектной организации
Интеллектуальному труду свойственна неравномерность. Невозможно разбить его на составляющие и составить график, как делается на производстве. Тем не менее Toyota нашла способ выравнивать объем работ при разработке новой продукции гораздо лучше своих конкурентов.
Во-первых, следует обеспечить базовую стабилизацию процесса. В Toyota сформирован стабильный процесс разработки, разбитый на отдельные этапы, при этом каждый этап имеет стандартную продолжительность, а на проектно-конструкторскую работу выделяется стандартное время.
Во-вторых, это позволяет Toyota составить предварительный график в начале работ над проектом и придерживаться его в дальнейшем. Toyota занимается модернизацией выпускаемых моделей приблизительно раз в два года, а примерно каждые четыре года конструкция автомобиля пересматривается полностью. Такое обновление моделей происходит не одновременно. Оно распределяется во времени таким образом, что в течение года в производство запускается примерно четвертая часть всех новых моделей.
В-третьих, в Toyota существует четкое представление о динамике объема работ при разработке автомобиля, и привлечение рабочей силы учитывает эту динамику. Обычно на начальном этапе над проектом работает небольшая группа ведущих инженеров, затем объем работ возрастает и вновь снижается при запуске в производство. Эти устойчивые закономерности соблюдаются за счет стабильности процесса в целом. Многие конкуренты Toyota при запуске автомобиля в производство отправляют на завод целую армию персонала. Однако в Toyota процесс тщательно распланирован, а на этапе разработки кон-
цепции над проектом работает достаточное количество высококвалифицированных инженеров, поэтому запуск в производство проходит гладко, и большая часть сотрудников на этом этапе переводится на другие проекты.
В-четвертых, справляться с возрастающим объемом работ Toyota помогают аффилированные компании. В их число входят тесно связанные с компанией фирмы-подрядчики, которые в периоды максимальных нагрузок предоставляют в распоряжение Toyota своих инженеров и специалистов по автоматизированному проектированию. Другие поставщики, а также Toyota Auto Body при необходимости предоставляют дополнительный инженерно-технический персонал. Это дает возможность Toyota держать штат высококвалифицированных инженеров и привлекать дополнительный персонал в случае необходимости. Стандартизированные процессы проектирования и разработки позволяют Toyota безболезненно подключать к работе над проектом штатных инженеров и персонал аффилированных компаний.
В-пятых, значительная часть технической документации в Toyota выпускается по графику. К примеру, конкуренты Toyota выпускают всю техническую документацию, например по кузову, одной большой партией, и инженерам, разрабатывающим штампы, приходится обрабатывать все полученные данные одновременно. Toyota выпускает документацию по кузову по мере готовности, эта документация сразу передается разработчикам, а по мере разработки штампов происходит их изготовление. Существует четкое представление о том, какие части кузова разрабатываются сначала, а какие — позднее. Это позволяет создать подобие потока единичных изделий, а значит, распределение объема работ является куда более равномерным, чем при одновременном выпуске комплекта конструкторской документации на все части кузова.
_I_
Вопросы для самопроверки
Для обеспечения стабильности процесса и непрерывного потока необходимо базовое выравнивание объема и ассортимента продукции. С помощью карты текущего состояния потока создания ценности выявите операции, которые по-прежнему не вполне удовлетворяют данным требованиям.
1. Сказывается ли на этих операциях вариация требований внешнего
потребителя?
A.Меняются ли требования изо дня в день?
Б. Определите диапазон колебаний (представьте изменения суточного спроса в виде линейного графика). Вариацию, превышающую 10%, следует снизить.