Практика дао Toyota. Руководство по внедрению принципов менеджмента Toyota Лайкер Джеффри
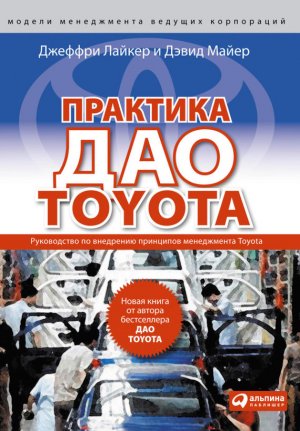
B.Определите текущие методы перераспределения ресурсов (людей, материалов, оборудования) при колебаниях спроса. В какой мере
вы способны удовлетворить предъявляемые требования (показатели эффективности и доставки продукции потребителю)?
2.Введение выровненного графика требует предварительной работы, а его соблюдение — упорного труда.
А. Оцените влияние вариации и установите, принесет ли пользу выравнивание потока продукции.
Б. Намерены ли вы работать над устранением проблем, которые препятствуют более равномерному выпуску продукции меньшими партиями?
3.Если вы производите продукцию про запас, создайте супермаркет для готовых изделий, чтобы сгладить вариацию требований потребителя.
A.Определите среднесуточный объем спроса на вашу продукцию. Б. Определите питч для каждого вида продукции. 10-20% (а возможно и более) видов изделий, пользующихся максимальным (с учетом объема) спросом, должны производиться ежедневно.
B.Определите повторяющийся питч для прочих видов продукции и воспроизводимую последовательность их изготовления с учетом необходимой структуры ассортимента и потребностей обеспечения сбалансированного потока.
4.Ваш выровненный график становится стандартом работы. Оцените степень соблюдения стандарта и устраните препятствия, которые мешают стабильному соблюдению графика. Примечание: Не меняйте план из-за недостатков процесса. Исправьте обнаруженные недостатки.
5.По мере повышения эффективности процесса постепенно поднимайте планку. Оцените поток создания ценности и задумайтесь над следующими вопросами:
A.Знаете ли вы «точку управления» своего потока создания ценности?
Б. Проводите ли вы измерения в этой точке и управляете ли ею?
B.Какие изменения в точке управления могут сказаться на потоке создания ценности в целом?
Г. Каким образом эти изменения отразятся на потоке создания ценности (на каком участке цепь порвется)?
Д. Можно ли принять корректирующие меры, которые позволят устранить слабое звено в потоке создания ценности до внесения изменений?
6.Выравнивание обеспечивает «базовый стандарт» для распределения ресурсов. Планирование факторов, перечисленных ниже, опирается на выровненный график:
A.Пополнение запаса материалов: все поставки материалов на предприятии осуществляются с учетом стабильных потребностей каждого процесса. Эти потребности определяют питч пополнения запаса материалов и являются основой стратегии пополнения запасов, включающей стабильное пополнение запасов поставщиками.
Б. Люди: выровненный график становится основой для определения времени такта, которое необходимо для стандартизированной работы. Введите стандартизированную работу на всех процессах и определите требуемую численность персонала.
B.Оборудование: стандартизированная работа — основа для определения требований к оборудованию. Определяйте потребности в оборудовании исходя из нужд персонала и работы по выровненному графику.
СДЕЛАЙ ОСТАНОВКУ С ЦЕЛЬЮ РЕШЕНИЯ ПРОБЛЕМ ЧАСТЬЮ ПРОИЗВОДСТВЕННОЙ КУЛЬТУРЫ
Нас часто спрашивают: «Каким образом Toyota добивается того, что качество ее продукции неизменно выше, чем у других автомобилестроительных компаний?» Хотя на этот вопрос нельзя ответить одним словом, можно сказать, что в значительной мере это происходит благодаря принципу встраивания качества и готовности остановить процесс и исправить проблему, как только она возникла, вместо того чтобы передавать ее дальше, рассчитывая исправить потом. Казалось бы, вполне разумный подход. Если у вас появилась проблема, лучше остановиться и решить ее, предупредив ее повторное возникновение. Однако в действительности, когда от людей требуют «выйти на заданные цифры», они изо дня в день стараются любой ценой добиться требуемых показателей производительности, уделяя основное внимание краткосрочным результатам. Массовое производство нацелено на количество. Бережливое производство нацелено на устранение потерь.
Это не значит, что в Toyota любят останавливать линию. Избыток простоев ведет к резкому снижению производительности и рентабельности, и если вы то и дело останавливаете линию, результаты будут весьма плачевными. Если вы сторонник принципа остановки линии, вам придется либо смириться с такими результатами, либо кропотливо трудиться над устранением проблем. Приверженность этому принципу требует решимости и видения. У Toyota ушли годы на то, чтобы создать систему, которая позволяет извлечь из остановки линии пользу в долгосрочной перспективе. Была создана поддерживающая инфраструктура, которая позволяет оперативно выявлять и устранять проблемы. Таким образом, негативные последствия остановки линии сводятся к минимуму.
На протяжении последних двадцати или более лет требования к качеству постоянно растут. Все понимают, что выживание на рынке зависит от способности обеспечивать неизменно высокие показатели. Интерес к методу шести сигм с его тремя дефектами на миллион помогает понять, что сегодня качество — это обязательное требование. Вопрос уже не в том, нужно ли поставлять высококачественную продукцию, теперь он ставится иначе: «Что делать, чтобы этого добиться?» Лучше всего начать с себя. Если вы хотите взять несколько уроков у Toyota, нужно четко представлять, как и почему она действует так, а не иначе.
Схема на рис. 8-1 подобна моделям, к которым мы обращались в предыдущих главах, но на сей раз речь идет об остановке линии. Традиционный подход, ориентированный на снижение издержек на единицу продукции, порождает образ мышления, не допускающий остановки линии, поскольку теория гласит: чем выше показатели производительности, тем ниже издержки на единицу продукции. В соответствии с таким подходом любые проблемы можно исправить позднее, а качество контролировать с помощью дополнительных проверок и локализации дефектной продукции. Эти ошибочные представления формируют у работников убеждение, что выявление проблем и поиск решений не самое важное занятие. У людей постоянно возникают идеи решения проблем, но они не утруждают себя лишними хлопотами, поскольку постоянно слышат: «Не волнуйтесь, эту проблему мы решим потом. У нас есть кому об этом позаботиться. Занимайтесь своим делом». В таких условиях нести ответственность за выявление проблем приходится ОТК. Этот же отдел занимается и поиском виноватых, что часто порождает взаимные обиды, поскольку инспекторов по качеству, докладывающих о проблеме, часто воспринимают как стукачей, которые доносят на своих сотрудников. В целом такая система не способствует созданию атмосферы сотрудничества и взаимного уважения — двум важным составляющим дао Toyota.
На рис. 8-2 представлены базовые принципы Toyota, касающиеся устранения потерь. Обратите внимание, что все примеры такого рода начинаются с определения базовых принципов. Если философия нацелена прежде всего на устранение потерь (в данном случае речь идет о потерях при устра-
нении дефектов), естественным продолжением такого образа мышления будет формирование системы, которая обеспечивает качество без доработки. Toyota создала развитую систему, которая предоставляет в распоряжение людей инструменты и ресурсы для выявления и решения проблем. Само собой, остановка производственной линии — событие чрезвычайное, с которым надо разобраться как можно быстрее. Если персонал не будет действовать слаженно и оперативно, линия станет то и дело останавливаться. Люди знают, что в случае возникновения проблемы они могут рассчи-
тывать на поддержку, и не боятся наказания. Так формируется стремление содействовать повышению эффективности.
Феноменальные финансовые показатели Toyota и легендарный уровень качества ее продукции не оставляют сомнений в том, что метод «останови и исправь» работает. И все же по какой-то причине во многих организациях по-прежнему считают, что нужно сделать все, чтобы не допустить остановки линии. Нередко в этом винят организационную культуру. Как изменить культуру? Как поменять привычки, которые складывались с момента возникновения компании?
Изменение культуры — чрезвычайно сложная задача. Прежде чем вы приметесь за преобразование культуры, поймите, что она существует не в вакууме. Для формирования культуры нужно время. Она возникает в силу ряда обстоятельств и впоследствии поддерживается. Если механизмов, поддерживающих нужную культуру, не создано, складывается культура индивидуализма, основной принцип которой — «своя рубашка ближе к телу».
Это случилось, когда я работал инструктором по бережливому производству на сборочном заводе одной из автомобилестроительных компаний США. Любой практик дао Toyota понимал, что ситуация чрезвычайно сложна, и я ужасно волновался. Дао Toyota способствует выработке условных рефлексов, подобных рефлексам знаменитых собак Павлова. У меня выработался рефлекс выявлять потенциальные проблемы и откликаться, когда меня зовут на помощь. И хотя данный завод еще не впитал дао Toyota и я не отвечал за то, что происходит вокруг, я реагировал на происходящее в духе дао Toyota.
Конкретная ситуация: остановка линии не сводится к подаче световых и звуковых сигналов
Я обнаружил у себя этот рефлекс спустя некоторое время после того, как ушел из Toyota. Очутившись в производственной зоне ка-кого-либо предприятия, я машинально отмечаю потенциальные проблемы и потребность в корректирующих действиях еще до того, как проблема становится явной. Нередко я с ужасом замечаю, что руководство предприятия пребывает в «блаженном неведении» по части того, что творится вокруг. Мы проходим мимо явных и потенциальных проблем, точно их не существует. «Остановись, здесь проблема, — взывает мой разум. — Нужно устранить ее, она чревата неприятными последствиями». Потом «туман» сгущается, и проблема теряется из виду. Насущной потребности в немедленном исправлении ситуации нет. При этом я вижу, что проблем так много, что они попросту захлестывают меня, и понимаю, что руководство тонет в них, а поддерживающая структура отсутствует. Кругом полным-полно проблем, и люди из кожи вон лезут, чтобы продержаться еще один день. Именно тогда я по-настоящему оценил систему Toyota.
Как-то раз я наблюдал за работой линии окончательной сборки (иногда ее называли «денежной линией») на заводе одной из компаний «большой тройки» и заметил, что напольное покрытие в салоне автомобиля со стороны водительского места повреждено. Рядом со мной стоял мастер. У меня возникло рефлекторное стремление остановить линию. Разумеется, здесь не было андон, как в Toyota, и я показал повреждение мастеру, ожидая реакции с его стороны. Он согласился, что покрытие и в самом деле порвано, но и не подумал что-нибудь предпринять! Я пришел в смятение. Я поинтересовался, что нам делать, но он ответил, что проблему исправят на ремонтном участке. На мой вопрос, не следует ли нам найти источник проблемы, чтобы предупредить ее повторение, мастер лишь пожал плечами. «Они наверняка уже все выяснили», — ответил он.
Это был мой первый опыт знакомства с ситуациями такого рода. Я не знал, как себя вести, но внутренне был крайне обеспокоен. Мы столкнулись с проблемой, которая могла оказаться очень серьезной. Нам следовало как минимум остановить линию и позаботиться о том, чтобы данный автомобиль был снят со сборки, поскольку на ремонтном участке предстояло демонтировать все элементы салона, установленные после настила покрытия, в том числе сиденья и большую часть отделки. По сути это означало капитальный ремонт. Помимо того, что это дорого, обратный монтаж наверняка будет хуже первоначальной работы. Демонтаж отделочных элементов и переустановка сидений приведут к тому, что со временем машина начнет скрипеть и дребезжать, а подобные проблемы весьма раздражают потребителей.
В итоге мы полностью устранились от данной проблемы. Мы не отправились в конец линии, чтобы убедиться, что дефект обнаружен, а ремонт выполнен (т. е. что дефектное изделие не попало к потребителю), и не попытались выявить источник проблемы и позаботиться о том, чтобы она не возникла вновь. Мы просто ушли!
Позднее я обнаружил множество глубинных проблем. К примеру, если мастер (или кто-то другой) обнаруживает проблему и указывает на нее рабочему, тот может подать жалобу в профсоюз и заявить, что к нему придираются. Даже если такое заявление рабочего бездоказательно, разбираться с ним намного сложнее, чем исправить проблему на более позднем этапе. Десятки лет отношения между менеджментом и персоналом становились все более враждебными, а это препятствует сотрудничеству (хотя в порядке исключения мне попадались люди, которые искренне стремились работать иначе). Если мы хотим, чтобы стратегия «останови линию» работала, нужно прежде всего изменить культуру.
Нельзя просто объявить людям: «С сегодняшнего дня все будет иначе!», рассчитывая на то, что культура внезапно изменится. Как изменить мастера, который за 30 лет приспособился к старой системе? Как поменять подход к измерению результативности? Если люди знают, что об эффективности их работы судят по выработке, как они отреагируют? Нельзя вдруг взять и решить, что с этой минуты мы будем останавливать линию для устранения проблем.
Ниже мы перечислим, что и в каком порядке следует делать, чтобы успешно сформировать культуру и систему, опирающиеся на принцип «остановки линии». Говоря об «остановке линии», мы имеем в виду остановку оборудования или остановку процесса работы. Это значит одно: когда обнаружена проблема, все останавливается.
1.Задумайтесь, какова нынешняя культура, как она стала такой.
2.Составьте четкое представление о необходимых изменениях.
3.Не забывайте об уважении к людям и их чувстве собственного достоинства.
4.Обеспечьте приемлемый уровень стабильности процессов.
5.Продумайте метод остановки линии.
6.Данный процесс должен предусматривать звуковую и визуальную индикацию в точке выявления проблемы (забудьте о системах вызова ответственных).
7.Назначьте ответственных за принятие мер при остановке линии.
8.Определите их функции и процедуру реагирования на проблемы.
9.Измените метод оценки, переключившись с чисто количественных показателей на показатели встроенного качества.
10.Научите людей решать проблемы.
11.Сделайте решение проблем насущной и неотложной необходимостью.
В приблизительном переводе термин дзидока означает «умные машины» и применяется к оборудованию, способному самостоятельно останавливаться при появлении проблемы. Не так-то просто создать машину, которая работает, не требуя постоянного наблюдения оператора, и подает сигнал в случае проблемы. К счастью, сегодня многие производители оборудования встраивают в машины функции самопроверки. Однако, как и многие другие концепции Toyota, дзидока не сводится к автоматической остановке станка.
Ядро философии Toyota — уважение к людям, обеспечивающим создание ценности. Только люди могут думать и решать проблемы. Машины нужны для того, чтобы облегчить человеку жизнь, а не для того, чтобы господствовать над ним. Станок, который останавливается сам, избавляет человека от необходимости постоянно следить за его работой и позволяет человеку использовать свои способности более продуктивно (например, занимаясь добавлением ценности).
Хорошо известна история про корреспондента, который готовил материал о Toyota и о заводе в Джорджтауне. Понаблюдав за линией, на которой выполнялась сборка дверного блока, он удивился отсутствию роботов, которые стоят на заводах конкурентов. «Разве это не снижает эффективность работы предприятия?» — поинтересовался он. Президент ТММК терпеливо объяснил, что у роботов есть свои недостатки. Они не умеют думать и не могут чувствовать. При установке двери важно, чтобы рабочий понимал, что нужно потребителю, и выполнял свою работу с учетом его желаний. Он должен чувствовать, как закрывается дверь, и слышать, какой звук она при этом издает. Научить этому робота невозможно. Вероятно, труд рабочего обойдется дороже, но способность человека к чувственному восприятию в итоге окупится.
ЛОВУШКА
Ряды лампочек — не всегда эффективные андон
Когда концепции андон и дзидока стали достоянием широких масс, мы стали замечать, как на оборудовании появляются ряды лампочек. Обычно подобный комплект включал три-четыре сигнальные лампочки разного цвета, установленные единым блоком. Решение создать такой андон порождает несколько проблем. Во-первых, мы видим, что, как правило, световые сигналы остаются без внимания. По всему производственному участку горит множество разноцветных лампочек, однако никакой реакции не следует. Обилие лампочек снижает ^восприимчивость, дезориентируя людей. Кроме того, понять, что значат сигналы, бывает непросто, поскольку какие-либо обозначения отсутствуют. Когда мы просили работников объяснить смысл того или иного сигнала, мы получали самые разные ответы. И наконец, световой сигнал имеет свои особенности. Его довольно легко игнорировать в отличие от гудка или сирены. (Например, на Toyota каждой ситуации соответствует свой звуковой сигнал. Например, при вызове мастера или остановке линии звучит фрагмент миниатюры Бетховена «К Элизе».)
Как ни печально, это классический случай применения инструментов бережливого производства без глубинного понимания их назначения и в отсутствие системы хансей, предполагающей размышление о слабых местах. Люди ошибочно полагают, что, установив сигнальные лампочки, они создали андон или дзидока. Чтобы понять, выполняют ли инструменты свою функцию, нужно проанализировать ситуацию.
Используя дзидока, следует уяснить, на каком участке процесса имеют место потери. Есть ли у вас оборудование, которое требует постоянного внимания? Вынуждает ли оно оператора терять время на ожидание? Чтобы представить подлинное положение вещей, следует внимательно понаблюдать за происходящим. Люди давным-давно поняли, что ситуация, при которой оператор бездельничает, пока работает станок, нежелательна, поэтому оператор нередко заполняет это время какой-нибудь работой. Ожидание не всегда заметно сразу, поэтому нужно присмотреться, чем занят оператор, пока машина работает. Ведет ли его работа к добавлению ценности?
Понаблюдайте, не работает ли оборудование вхолостую из-за того, что никто не замечает, что рабочий цикл завершен. Нередко приходится наблюдать, как в устройстве автоматической подачи застревает материал или же его запас заканчивается и машина простаивает в ожидании. Это тоже потери. Следует оснащать станки датчиками, которые звуковым и визуальным сигналом оповещают оператора о том, что станок нуждается в его внимании (желательно, чтобы такой сигнал подавался до того, как запас материала иссякнет).
Принимаясь за создание системы, важно представить цикл решения проблемы от начала и до конца — от обнаружения проблемы до предупреждения ее повторного возникновения. Этот цикл наглядно представлен на рис. 8-3. Такой цикл типичен для Toyota.
В течение дня этот цикл повторяется многократно. Выявление и устранение проблем происходит постоянно, почти не сказываясь на производственном процессе (в разделе «Свести время простоя линии к минимуму» рассказывается об остановке для решения проблемы, а рис. 8-4 иллюстрирует работу системы остановки для решения проблемы). Этапы этого цикла следует воспринимать как «цепь событий», где один эпизод неизбежно влечет за собой следующий. Данный процесс является таким же согласованным и управляемым, как игра хорошей баскетбольной команды.
1. Обнаружение. Первый этап процесса — выявление отклонений от нормальных условий. Установить наличие проблемы помогают визуальные стандарты (см. главу 6), которые делают отклонение очевидным для всех. Предположим, выполняя определенную задачу, оператор видит, что не укладывается в заданное время (время такта). Это становится очевидным, поскольку стандартизированная работа соотнесена с перемещением сборочной линии и
разметка на полу показывает границы участка, на котором должен находиться оператор, выполняя соответствующую операцию. Если он переходит границу, прежде чем операция выполнена, значит, он отстает и должен позвать на помощь.
Рассмотрим другой пример, на этот раз связанный с качеством. Чтобы определить, допущен ли дефект, работнику необходима база для сравнения. Да-да, bj»i догадались правильно, речь идет о стандарте. В главе 6 говорилось о значении эталонных образцов. Кроме того, оператору можно предоставить определенную свободу действий для самостоятельного устранения небольших проблем при условии, что он укладывается во время такта. Эти «правила» тоже часть стандарта. Они же — важная составляющая следующего этапа, на котором оператор решает, когда надо позвать на помощь. Все это стоит четко определить!
2. Извещение руководства. Если проблема выходит за пределы компетенции оператора, он должен известить о проблеме своего руководителя и обратиться за помощью. Для этого используется сигнальный шнур или иное средство привлечения внимания. Андон в Toyota устроены таким образом, чтобы персонал, отвечающий за оказание помощи (лидеры команд и лидеры групп), мог быстро
и точно определить рабочее место, на котором возникла проблема. Обычно система андон подает звуковой сигнал, а на участке, где возникла проблема, загорается лампочка.
Во многих компаниях, которые пытаются внедрить систему андон, работники не решаются признать, что им требуется помощь. Они боятся, что их будут винить в случившемся. Начальство судит о работнике и его квалификации с учетом того, как часто ему требуется помощь («хороший» работник не будет то и дело останавливать линию). Это ключевой момент формирования культуры. Руководство должно осознать, что его функция состоит в поддержке сотрудников и в поиске оптимальных методов работы, позволяющих каждому успешно выполнять свою работу. Если у руководителей или у подчиненных возникают недовольство и чувство обиды, система андон бесполезна.
Откликнувшись на просьбу о помощи, лидер тем самым снимает с оператора ответственность за проблему и берет ее на себя. Оператор описывает ситуацию, и как только лидер понимает, в чем дело, оператор возвращается к выполнению своих прямых обязанностей. Теперь «хозяином» проблемы становится лидер, который должен ее локализовать (не исключено, что для полного устранения причины ему придется подключить к работе членов команды).
3. Оценка. Взяв ответственность на себя, лидер должен первым делом оценить ситуацию. Носит ли проблема локальный или масштабный характер? Если речь идет о проблеме местного характера, справиться с ней несложно (например, оператор не укладывается во время такта) и лидер берет ответственность на себя, в первую очередь следует оценить возможность запустить линию вновь или решить проблему до ее остановки. Если проблема значительна или ее причина неясна (например, проблема с качеством, истоки которой где-то в другом месте), линию, скорее всего, придется остановить, и ее работа возобновится лишь после того, как ситуация будет исправлена.
Если лидер, который взял на себя решение проблемы, не может перезапустить линию сразу, следует известить еще более высокий уровень управления. Теперь вы видите, что порядок извещения вышестоящих руководителей («эскалирование» проблемы) тоже регулируется заранее заданными правилами. На установление и устранение проблемы лидеру команды дается определенное время (несколько минут), после чего он должен доложить о ситуации лидеру группы. Когда ответственность переходит к лидеру группы, в его распоряжении тоже есть определенный лимит времени, и если по его истечении проблема не будет устранена, он должен уведомить менеджера. Чем значительнее проблема, тем выше уровень, на который она передается. Таким образом, крупным проблемам уделяется надлежащее внимание, а высшему менеджменту не приходится заниматься мелкими проблемами, которые могут решить лидеры. Задача менеджмента — обеспечить необходимые ресурсы для быстрого устранения проблемы и позаботиться о том, чтобы были приняты корректирующие меры, которые предотвратят ее повторное появление.
4.Контроль. Прежде всего следует оценить, можно ли решить проблему на рабочем месте и не дойдет ли она до потребителя. Чтобы убедиться в этом, лидер, как правило, проверяет, не перешла ли проблема на следующую операцию. Остановка линии позволяет предупредить дальнейшее распространение проблемы. Это стержневой принцип данной системы — остановить линию, пока проблема не устранена или не взята под контроль. Остановка линии — важное решение, которое немедленно привлекает внимание к проблеме. Именно в этом и заключается ее смысл. В традиционных условиях остановка линии воспринимается негативно, и ее стараются по возможности избегать, а если ситуация все же вынуждает пойти на подобный шаг, делается все, чтобы не привлекать к нему внимания. С точки зрения дао Toyota факт обнаружения проблемы — в определенном смысле «повод для торжества», поскольку всех воодушевляет открывшаяся возможность исправить ситуацию. Нельзя сказать, что в Toyota радуются, когда люди совершают ошибки, но если коренная причина ошибки обнаружена и устранена, все понимают, что это повысит устойчивость процесса в долгосрочном аспекте.
5.Локализация. Когда лидер выявляет источник проблемы, ее можно локализовать. В случае проблем с качеством лидер должен периодически проходить вдоль линии, стараясь определить источник проблемы. Этой процедуре помогает хорошее знание процесса. Так, если какая-то деталь устанавливается неправильно, чтобы выявить источник проблемы, лидеру достаточно подойти к оператору, который устанавливает данную деталь. Если проблема возникает от случая к случаю, лидер должен проверять все предшествующие операции,
пока источник не будет выявлен. Если дефект появляется нерегулярно, возможно, следует перезапустить линию и продолжить поиск источника. В зависимости от остроты проблемы такое решение принимает лидер группы или вышестоящий руководитель.
Другая цель локализации — определение границ проблемы. Когда и где она начинается и заканчивается? Важно не только определить ее источник, но и гарантировать, что все дефектные изделия исправлены. Если проблема серьезна, к ее решению привлекается несколько лидеров, каждый из которых берет на себя часть ответственности.
6. Предупреждение. После того как проблема взята под контроль и локализована и производство возобновилось, основные усилия переключаются на предупреждение. В некоторых случаях предупредительные меры носят краткосрочный характер, пока не удалось найти эффективных долгосрочных решений. Лидер команды принимает такие краткосрочные контрмеры немедленно, чтобы предотвратить повторное появление проблемы. Если нужно найти долгосрочное решение, возможно, ответственность за него будет возложена на команду в целом. Все члены команды отвечают за разработку эффективных предупредительных действий. Для поиска первопричины и выработки эффективных решений долгосрочного характера применяется процесс решения проблем.
ПОДСКАЗКА
Прежде чем применять принцип «останови линию», следует обеспечить стабильность и механизм поддержки
Линии Toyota не останавливаются сразу после того, как подан сигнал андон. Между подачей сигнала и остановкой существует непродолжительное временное окно (порядка 5-30 секунд), которое позволяет лидеру команды отреагировать на сигнал и отменить остановку линии под свою ответственность. Такая система весьма уязвима и требует поддерживающих механизмов, обеспечивающих быстрое реагирование. Само собой, такого уровня Toyota достигла не сразу. Сначала нужно было добиться высокой стабильности — иначе линию приходилось бы останавливать беспрестанно— и вложить средства в создание системы лидеров команд, которая позволяет почти мгновенно откликаться на сигналы андон. Внедряйте собственную систему андон, в которой оперативность реакции соответствует уровню проблем в процессах. Если приемлемый уровень стабильности процессов не обеспечен, система поддержки будет перегружена и наступит полный развал.
Toyota разработала систему, которая часто позволяет выявлять проблемы и извещать о них руководителя без остановки линии. Когда проблема выявлена, оператор дергает за шнур андон. Раздается сигнал тревоги, и загорается желтая лампочка. Линия продолжает двигаться, пока не достигнет границы рабочей зоны — точки остановки (рис. 8-4). Система остановки для решения проблем особенно полезна для снижения времени фактических простоев линии, когда рабочий отстает от заданного режима выполнения работы. На полу рабочей зоны сделана разметка в соответствии с очередностью выполнения этапов стандартизированной работы. Если лидер оперативно откликнется на вызов и вновь дернет шнур, прежде чем достигнута точка остановки, линия без помех продолжит свою работу. Если лидер не успел подойти вовремя или считает, что проблема требует остановки, когда граница рабочего места будет достигнута, линия автоматически остановится и загорится красная лампочка андон.
Такой подход позволяет исправить множество незначительных проблем, не создавая помех движению линии, без бесконечных остановок и перезапусков. Нужно иметь в виду, что любая остановка весьма неприятное событие, поскольку всем, кто работает на линии, при ее перезапуске приходится заново синхронизировать свои действия. Учитывая это обстоятельство, в Toyota при перезапуске линии подают звуковой сигнал для всех операторов.
Сборочные линии в Toyota, как правило, очень длинные и представляют собой отрезки прямой, соединенные U-образными изгибами. Фактически остановка линии представляет собой остановку ее линейного сегмента.
Каждый из таких сегментов можно ненадолго остановить, не затрагивая остальные (рис. 8-5). Как уже отмечалось, периодические кратковременные остановки линии оказывают разрушающее воздействие на поток. Представьте череду машин, которая останавливается по красному сигналу светофора. Что происходит, когда загорается зеленый свет? Могут ли все машины тронуться одновременно? Нет, они стартуют одна за другой, прежде чем вновь двинутся сплошным потоком. Тот же феномен имеет место при запуске потока. На изогнутых участках линии используется небольшой резервный запас, который позволяет амортизировать кратковременные, — не более 10 минут — перерывы в работе. Если оператор подает сигнал андон и лидер успевает принять’меры прежде, чем машина поступит в зону работы следующего оператора, останавливать линию не приходится. Если проблема значительна и ее не удается исправить в пределах одного рабочего места, останавливается линейный сегмент линии (например, участок А), при этом остальные участки (В и С) продолжают работу, используя буферный запас. Если время простоя превышает то, на которое рассчитан буфер, останавливается следующий участок. Разумеется, объем буферов слишком мал, чтобы запасы могли скрыть крупные проблемы.
Конкретная ситуация: остановка линии — награда за достижения в бережливом производстве
Из компаний, не входящих в группу Toyota, General Motors распола-гала, пожалуй, самыми широкими возможностями изучения производственной системы Toyota. GM и Toyota — совладельцы совместного предприятия NUMMI, где TPS стала впервые применяться за пределами Японии. General Motors имеет свободный доступ на завод NUMMI и отправляет многих своих сотрудников туда на год или на более длительный срок. Когда GM начала изучать TPS, она просто копировала увиденное в NUMMI, однако быстро поняла, что это не дает результата. К примеру, система андон не работала так, как в Toyota. Инвестировав средства в суперсовременную технологию остановки для решения проблем, General Motors не добилась ровным счетом ничего. Рабочие не пользовались этой системой для выявления и решения проблем.
В Хэмтрамаке, Мичиган, на заводе, где изготавливали Cadillac, GM повела себя умнее. Здесь также была создана система андон, чтобы
останавливать линию для решения проблем. Однако функцию автоматической остановки линии подключили не сразу. Вместо этого на заводе занимались стабилизацией процесса и обучением работников различным методам бережливого производства, в частности стандартизированной работе и дисциплине использования системы канбан. Здесь сформировали рабочие группы и ввели текущую оценку деятельности каждой рабочей группы. Оценивалась дисциплина рабочей группы при использовании канбан, стандартная работа и оперативность решения проблем на линии. Рабочая группа получала право на подключение автоматической системы остановки линии, лишь когда добивалась высоких результатов работы. Каждый раз, когда очередная рабочая группа успешно проходила испытание, это событие торжественно отмечалось и о нем узнавали все. Все команды упорно трудились, стремясь удостоиться этой чести. И тогда метод остановки линии заработал как положено.
Существует любопытный парадокс. Проверка качества не добавляет ценности, однако в Toyota придают особое значение включению самопроверки во все виды стандартизированной работы. Хотя на первый взгляд это противоречит другим принципам, такой подход представляет собой своеобразный компромисс. Проверка не добавляет ценности, но предотвращает более крупные потери. Важно понимать, что на Toyota очень серьезно относятся к любым дополнительным потерям и стараются свести к минимуму любую бесполезную деятельность. Есть несколько способов включить проверку в процесс работы так, чтобы потери были сведены к минимуму, а польза была максимальной.
На каждого оператора возлагаются следующие обязанности, связанные с проверкой качества:
1.Проверять поступающую работу на отсутствие дефектов.
2.Проверять собственную работу на отсутствие дефектов.
3.Никогда не передавать заведомо дефектный продукт на следующую операцию.
Выполнить проверку поступающей работы оператор может, пока деталь или он сам находится в движении. Например, завершив рабочий цикл и переходя к следующей машине, оператор может на ходу осмотреть поступающую деталь. Взяв ее в руки, рабочий не ограничивается одним взглядом, а сосредоточенно изучает ее, чтобы удостовериться, что взял нужную деталь без дефектов. Такая проверка — обязательное условие надлежащего выполнения работы. Это не просто тщательный внешний осмотр; проверка осуществляется быстро и целенаправленно. Тщательный 100%-й осмотр производится по окончании сборки узла или одной из основных технологических операций, например сварки кузова, его окраски или изготовления ходовой части.
Сознательная проверка отдельных зон, для которых характерно появление проблем, повышает эффективность процесса проверки (используйте данные!). Другие проверки можно выполнить в процессе установки или перемещения детали. Следует приучить персонал в процессе работы обращать особое внимание на определенные зоны. Более подробно про производственный инструктаж — метод обучения персонала, используемый в Toyota, — рассказывается в главе 11.
Проверить подобным образом собственную работу может каждый. Это можно сделать, снимая деталь со станка или передавая ее на следующую операцию, поскольку заранее известно, на что обращать особое внимание. Для важных операций или для операций, на которых часто возникают проблемы, используется прием, который называется ёси. (Так во время предполетной проверки пилот произносит слово «готово».) Стандарт требует, чтобы по завершении задачи оператор указал на деталь пальцем (да-да, в буквальном смысле слова!) и произнес «ёси», что означает: «Я проверил эту деталь». Для лидера это служит визуальным сигналом о том, что проверка выполнена (что помогает ему следить за выполнением стандартизированной работы). Если бы оператор просто осматривал деталь, понять, следует ли он инструкциям по проверке, было бы невозможно. К тому же, указывая на деталь, оператор совершает сознательное действие, тем самым подключая к работе интеллект. Ёси снижает вероятность того, что проверка будет пропущена. Подобным образом, если на деталь можно наносить цветовую маркировку, все важные участки при проверке помечаются цветным маркером. Процесс, предусматривающий физическое действие, помогает не пропустить важных вещей.
Разумеется, одна из главных задач остановки линии — предупредить передачу дефектного изделия на следующие операции. Даже при наличии развитой системы поддержки приучить людей придерживаться этого принципа очень и очень непросто. Люди неохотно признают свою несостоятельность и ошибки. Одно из важных преимуществ работы небольшими партиями заключается в том, что, если дефект остался незамеченным на одном рабочем месте, а операторы на следующих этапах проверяют поступающую работу, цикл обратной связи, т. е. отрезок времени от момента возникновения проблемы до ее обнаружения на одной из последующих операций, будет коротким. При традиционном производстве крупными партиями продолжительность цикла обратной связи может составлять неделю и более.
ПОДСКАЗКА
Не вводите правила, которые невозможно соблюдать
Этот совет полезен во многих ситуациях, но в данном случае речь идет о принципе никогда не передавать заведомо дефектную продукцию на следующий процесс. Мало просто сказать людям, что этого делать нельзя. Что делать, если дефект обнаружен? Кого нужно позвать? Куда положить дефектное изделие? Если эти вопросы не решены, неизбежна неразбериха и конфликты. Если люди хотят поступить правильно и выполнить инструкцию, но соблюсти правило и выполнить работу надлежащим образом невозможно, они предпочтут выполнить работу, нарушив правило. Понаблюдайте, что происходит. Выполните данную операцию самостоятельно, чтобы получить о ней исчерпывающее представление. Не следует думать, что люди нарушают правила, потому что им не важен результат. Не исключено, что система, которая помогает соблюдать эти правила, отсутствует.
Предупредить ошибки оператору помогает использование методов и устройств пока-ёкэ. Обычно этот термин переводится как «предупреждение ошибок» или «предупреждение отклонений». Предупреждение ошибок представляет собой не только и не столько инструмент бережливого производства, сколько образ мышления и отношение к проблемам. Такой подход основан на утверждении, что, хотя люди не совершают ошибки и не отклоняются от стандарта нарочно, они тем не менее могут возникать.
Люди на Toyota совершенно иначе смотрят на причины возникновения ошибок, чем в других компаниях. В компаниях, с которыми мы работали, все единодушно соглашались с утверждением «люди совершают ошибки», но при этом были столь же единодушно убеждены в том, что «если бы люди были внимательнее, они не совершали бы так много ошибок». Принято считать, что «человеку свойственно ошибаться». В Toyota исходят из того, что ошибка свидетельствует о несостоятельности систем и методов, применяемых для выполнения работы. Ошибки случаются потому, что существующий метод допускает их возникновение!
Такое различие подходов ведет к тому, что ответственность за ошибки возлагается не на людей, а на метод, а значит, в ошибках винят не человека, а систему. Когда люди знают, что их ни в чем не упрекают, они могут сосредоточить свои усилия на создании более эффективных систем и решении проблем, вместо того чтобы оправдываться. В Toyota нередко можно увидеть, как менеджер просит прощения у рабочего, который допустил ошибку, поскольку именно менеджмент отвечает за создание эффективных систем, предупреждающих появление ошибок. Когда вы в последний раз видели, как кто-то в вашей компании извинялся перед рабочим, допустившим ошибку?
Следующий пример иллюстрирует образ мышления, типичный для большинства организаций.
Конкретная ситуация: ошибки при передаче заказов по факсу
В ходе мероприятий по сокращению продолжительности обработки заказов в офисном подразделении выяснилось, что утверждение заказа часто задерживалось на несколько дней из-за ошибок при отправке факсов дилерам. Прежде чем оформить заказ на поставку продукции, его следовало отправить дилеру для проверки и утверждения. Дилер должен был дать ответ в течение двух дней. Если предложение по недосмотру отправляли не тому дилеру, проходило два-три дня, прежде чем кто-либо его хватится. В результате выяснялось, что нужный факс не приходил. Анализ регистра отправленных факсов показал, что в действительности факсы часто по невнимательности отправляли на другие номера.
Дальнейшее расследование показало, что некоторые служащие допускали больше ошибок, чем их коллеги, на основании чего был сделан вывод, что они «небрежнее» прочих. В качестве «решения» проблемы было предложено повесить рядом с аппаратом для отправки факсов инструкции. Их содержание сводилось к призывам «быть внимательными» и «удостовериться, что факс отправляется куда следует». Разумеется, это не исправило положения. Был сделан вывод, что с некоторыми растяпами ничего не поделаешь, а значит, нужно ужесточить проверки.
Когда ситуация была проанализирована с точки зрения дао Toyota, реакция была следующей: «Человеку свойственно ошибаться, такова жизнь. Полностью избавиться от ошибок, которые совершает человек, невозможно». Тем не менее проблема в другом. Тот, кто разрабатывает систему, как правило, ориентируется в ней без труда и полагает, что другие тоже должны в ней разбираться. Создатель системы (или тот, кто использует ее годами) убежден, что все просто и понятно. Он не учитывает, что другие люди имеют иной опыт работы с данной системой и к тому же у всех разные способности. Не справляющихся с работой считают бестолковыми. О самой системе при этом задумываются редко. Чтобы выявить причины ошибок, которые коренятся в самой системе, давайте рассмотрим метод, который применялся в нашем примере.
Количество входящих и исходящих факсов в офисе было очень большим, поэтому использовались четыре аппарата. Каждый аппарат имел память на 100 номеров и возможность ускоренного набора номеров. На стене висел список дилеров, в котором напротив каждого дилера был написан код быстрого набора номера (рис. 8-6). Список состоял из трех больших листов (20 на 20 дюймов) и висел на некотором отдалении за факсимильными аппаратами.
Когда мы проанализировали метод выполнения работы, пытаясь понять, почему совершаются ошибки, мы увидели, что хотя вся информация, необходимая для выполнения работы, имеется в наличии, форма ее подачи не учитывает особенностей выполняемой работы. Давайте рассмотрим этапы выполнения данной работы.
1.Заглянуть в заказ и найти название дилера.
2.Отыскать дилера в списке.
3.Найти в конце соответствующей строки номер факсимильного аппарата и код быстрого доступа.
4.Найти нужный факсимильный аппарат.
5.Правильно ввести код быстрого доступа и отправить факс.
Анализируя данный метод, мы обнаружили, что на каждом этапе можно сделать ошибку. Можно найти дилера в заказе, но ошибиться, отыскивая его в списке. Определяя код быстрого набора номера в конце списка, легко случайно спутать строки и ошибиться при выборе кода (не забывайте, что список висит за факсимильными аппаратами, что не позволяет водить вдоль строки пальцем). Разобравшись со списком, служащий должен запомнить номер аппарата и код быстрого доступа. Он может найти нужный аппарат, но ошибиться, набирая код, или правильно набрать код, но ошибиться с выбором аппарата, или вообще забыть информацию, найденную в списке.
Менеджеры полагали, что служащим следует быть внимательными, изучая список, и что запомнить номер аппарата и код быстрого доступа несложно. Они считали существующую систему вполне приемлемой, поскольку сами использовали ее очень редко, когда показывали служащим, что с ее помощью вполне можно справиться с задачей и не ошибиться. Если бы им приходилось повторять данную операцию сотни и тысячи раз, да еще в спешке, они бы обнаружили, что тоже делают много ошибок. Менеджеры часто становятся жертвами такого заблуждения. Несложно выполнить операцию один раз и не совершить ошибку. Безошибочно повторить ее сотни раз совсем другое дело.
Чтобы упростить выполнение работы и свести число ошибок к минимуму, давайте проанализируем потенциальные причины ошибок.
Ошибка: Неправильно определен код или номер факсимильного аппарата дилера.
Каковы причины совершения этой ошибки?
1.Столбцы с важной информацией (название дилера и код) находятся по разные стороны широкого листа бумаги (их разделяют почти 20 дюймов).
2.Нет четкого разграничения отдельных строк списка, поэтому легко перескочить на соседнюю строку.
3.Списки висят за факсимильным аппаратом, и служащий не может водить вдоль строки пальцем.
Решение: Изменить формат списка, поместить наименование дилерской организации и код быстрого набора номера в соседних столбцах. Тем самым снизится вероятность перепутать строки. Тонировать строки через одну, как показано на рис. 8-7, чтобы снизить вероятность перепутать строки.
Рис. 8-7. Список дилеров, оформленный по-новому
Ошибка: Сотрудник использовал не тот факсимильный аппарат. Каковы причины совершения этой ошибки?
Списки расположены за факсимильными аппаратами, и сотруднику приходится запоминать номер аппарата, а потом отыскивать нужный аппарат. Эту ситуацию иллюстрирует рис. 8-8.
Решение: Составить отдельный список дилеров для каждого факсимильного аппарата и поместить его перед аппаратом, чтобы сотрудник имел возможность водить по строке пальцем. Новое расположение списков показано на рис. 8-9.
Введение этих изменений позволило значительно снизить количество ошибок. Кроме того, обнаружились ошибки в некоторых кодах быстрого набора, введенных в память. Факс мог не попасть к адресату, даже если сотрудник правильно определил код.
Вы спросите: «Рассматривали ли вы процесс проверки, в ходе которой определяется, попал ли факс к адресату?» Да, было сделано и это, но не забывайте, что данная операция сходна с проверкой готовой продукции. Этот дополнительный этап не выявляет коренных причин ошибок и к тому же повышает затраты. Его следует применять лишь к критическим процессам и лишь после того, как коренные причины выявлены и устранены.
Для разработки эффективного метода предупреждения ошибок нужно уяснить, как или почему совершается ошибка. Понятно ли, какие обстоятельства ведут к ее появлению? Носит ли ошибка случайный или систематический характер? Совершают ли ее все или трудности испытывает только один работник? Если ошибку совершает один человек, возможно, следует проанализировать стандартизированную работу и убедиться, что никакие этапы не пропускаются. Если ошибку совершают все, это свидетельствует о причине системного характера, например об отсутствии нужных сведений или нечетко определенном этапе работы. Не впадайте в заблуждение, полагая, что любая ошибка требует специального «устройства» для ее предупреждения12.
Следующий пример показывает, что любую проблему можно решить множеством способов. Поощряйте своих сотрудников к творческому поиску высокоэффективных решений, не требующих значительных затрат. У простоты есть огромные преимущества. Оглянитесь вокруг и подумайте, нельзя ли применить к вашей проблеме известные методы решения других проблем. Например, идея застежки-липучки родилась в ходе наблюдения за репейником, так одна «проблема» превратилась в решение другой.
Конкретная ситуация: всегда есть несколько способов предупреждения ошибок
На заводе Toyota в Джорджтауне детали окрашивались в соответствии с выровненной последовательностью ассортиментных позиций. Первая деталь могла окрашиваться, скажем, в белый цвет, вторая — в синий, третья — в черный, затем снова шла белая деталь. Система подвода краски требовала ее постоянной циркуляции, при этом на каждого маляра приходилось по одному окрасочному пистолету. Каждый раз при смене цвета детали маляр отсоединял наконечник шланга для краски от быстроразъемного соединения и подсоединял к нему окрасочный пистолет. Быстро пропустив через краскопровод струю краски, маляр приступал к окраске очередной детали. Поскольку цвет краски менялся от детали к детали, при окраске очередной детали маляру приходилось отсоединять один шланг и подсоединять другой. При предупреждении ошибок важно учитывать, что обычно люди ведут себя подобно электричеству — они ищут пути наименьшего сопротивления. В данном случае малярам хотелось избежать беспрерывного отсоединения и подсоединения шлангов.
Каждую покрасочную камеру обслуживали три маляра. После того как первый маляр окрашивал очередную деталь, его коллеги, которые продолжали окраску, видели цвет (и ассортимент) поступающих к ним деталей. Предположим, заданная последовательность предполагала, что за белой деталью следовала красная, потом снова белая и т. д. Когда маляр видел, что белый цвет вот-вот понадобится вновь, он не возвращал шланг с белой краской на место (т. е. не подсоединял его к быстроразъемному соединению на стене). Иногда маляр, не соблюдая правил, оставлял не подсоединенными сразу несколько шлангов, а потом ошибочно подсоединял один шланг к быстроразъемному соединению другого. В результате в системе подвода краски смешивались два цвета, что выливалось в серьезную проблему. Подобные ошибки совершались несколько раз в год, и общие потери времени и материалов при ликвидации последствий превышали $80 ООО в год, не считая издержек потребителя (сборочной линии).
Линия покраски простаивала, пока лидеры команд вручную смешивали краску в баках для каждого маляра, и лишь после того как краска была готова, работа линии возобновлялась. Остановка линии часто вела к нехватке деталей на сборке, что тоже было весьма острой проблемой. Предшествующие попытки предупредить совершение ошибок породили следующие «решения»:
1.Довести до сведения маляров, что стандартизированная работа предписывает отсоединять не более одного шланга за раз и они должны соблюдать стандартную процедуру. Как и следовало ожидать, эффективность такого подхода к предупреждению ошибок — напомнить работникам, что они должны следовать предписанному методу, — была невысока.
2.Повесить плакат с надписью: «Не отсоединять больше одного шланга». Такой прием при попытках предупредить ошибки — вывесить^напоминание о необходимости соблюдать правила или следовать заданному методу — широко распространен, но малоэффективен. Большинство людей считает, что вывешенный на видном месте плакат позволяет предупредить ошибки. Это кажется им логичным. Однако люди по большей части нарушают правила не по злому умыслу и при этом часто рассуждают следующим образом: «Думаю, мне удастся избежать ошибки, а значит, ничего страшного, если я нарушу правило».
3.Снабдить шланги маркировкой. Но нанесенные обозначения скоро скрылись под брызгами краски и стали нечитаемыми.
4.Над быстроразъемным соединением для шланга с белой краской установили откидной козырек, и чтобы присоединить шланг, маляр должен был приподнять этот козырек. Эта мера была связана с тем, что большая часть аварийных ситуаций в прошлом была связана со смешиванием белой краски с какой-либо другой. Сорок процентов всех автомобилей были белого цвета, и вероятность того, что поток деталей будет включать значительное количество белых деталей, была достаточно высока. Козырек над быстроразъемным соединением предназначался для того, чтобы оператор «задумался», прежде чем вернуть шланг с белой краской на место (что-то вроде метода ёси). Это «решение» тоже не возымело действия, поскольку оно не препятствовало ошибочному подсоединению шлангов. Оно лишь усложняло работу (в 40% случаев требовалось поднять козырек).
Эти четыре попытки предупреждения ошибок представлены в иерархическом порядке — указание на ошибки, вывешивание плакатов, маркировка и попытка обеспечить самопроверку. Меры такого рода могут сократить число ошибок, но не позволяют избавиться от них полностью.
После того как все эти попытки потерпели неудачу, было предложено использовать устройство, позволяющее переключать окрасочный пистолет с одного цвета на другой и избавляющее от необходимости отсоединять шланги. Такое устройство обеспечивало эффективное предотвращение ошибок, однако имело свои недостатки. Примерно на фунт увеличивался вес окрасочного пистолета, а значит, ухудшались его эргономические качества. К тому же такое решение обошлось бы недешево — чтобы оснастить подобными устройствами окрасочный участок, требовалось более $10 ООО.
Наблюдения показали, что операторы отклоняются от предписанного метода не по злому умыслу. Они нарушали правила, руководствуясь естественным стремлением сделать работу менее трудоемкой, пребывая в уверенности, что никогда не совершат ошибку. В данном случае требовался метод предупреждения ошибок, который не допускал бы возможности сознательного выбора (при соблюдении правил). Нужно было попросту исключить альтернативный образ действий.
Наблюдателю, который смотрел, как маляры подсоединяют и отсоединяют шланги, пришло в голову, что это напоминает процесс открывания замка дверным ключом. Так родилась идея. Что, если сделать для каждого шланга отдельный тип соединения? Как будто быстроразъемное соединение — это замок, а шланг — ключ. Слесарь изготовил опытный образец такого приспособления. Оно представляло собой кусок стального листа толщиной в четверть дюйма, закрепленный перед быстроразъемными соединениями. В листе были выполнены отверстия для шлангов. Для разъема каждого цвета была сделана особая комбинация прорезей (рис. 8-10), а наконечник каждого шланга был снабжен соответствующей комбинацией штырей, которые входили в прорези, как ключ в замок. Опытный образец приспособления был установлен на одном из окрасочных участков для тестирования. После внесения в конструкцию ряда поправок подобными приспособлениями были оснащены все окрасочные участки (на всех участках конфигурация соединений типа ключ-замок была идентичной).
Разумеется, данный метод не позволяет исключить ошибки полностью. В сущности, можно найти уязвимые места в любом методе (вспомните компьютерных хакеров, которые взламывают системы безопасности). В данном случае, если штыри сломаются, приспособление станет неэффективным. Чтобы не допустить такой возможности, лидер команды включил осмотр штырей в перечень ежедневных проверочных мероприятий перед началом смены.
Внедрение этого несложного решения обошлось всего в $200, включая материал и работу, при этом вес шлангов для краски возрос всего на несколько унций, т. е. решение практически не отразилось на эргономических характеристиках. Созданное приспособление позволило свести повторное возникновение проблемы к нулю.
Существует ряд ключевых моментов, которые способствуют успешному предупреждению ошибок. Определяющий фактор успеха — ваш образ мышления. Приемы и инструменты предупреждения ошибок просты, их несложно внедрить. Самое трудное — найти первопричину и творчески подойти к ее устранению.
Существует определенная иерархия мер по предупреждению ошибок. Высший уровень — полное предотвращение повторения ошибки. Однако это не всегда осуществимо и целесообразно. При желании можно обойти любую систему или устройство. Если использование устройства предупреждения ошибок сопряжено с трудностями и неудобствами, люди будут стараться «идти в обход». Если предложенное вами лекарство хуже самой болезни, люди будут уклоняться от лечения.
Если исключить ошибки полностью невозможно (а в большинстве случаев это именно так), постарайтесь, чтобы дефекты выявлялись по мере их
появления. Устройства и методы обнаружения дефектов (к этой категории относятся и устройства дзидока) распространены шире, чем средства их предупреждения. Такое устройство может выявлять поломку инструмента или давать сигнал оператору в случае отсутствия детали. Хотя они не предотвращают поломку или повреждение деталей, проблема быстро выявляется и оперативно устраняется.
Не переборщите с пока-ёкэ
К сожалению, даже в благих делах нужно знать меру. Мы замечаем склонность применять все больше устройств предупреждения ошибок. Зачастую такие устройства создаются инженерами без участия рабочих, выполняющих операцию. Устройства становятся все более замысловатыми и повышают сложность работы. Нам приходилось видеть операции, на выполнение которых требовалось 15 секунд, и при этом еще 25 секунд или более тратилось на работу с устройством предупреждения ошибок! Примером может служить ситуация, когда на литую деталь устанавливали несколько скоб и направляющих, а затем закрепляли ее в устройстве для предупреждения ошибок. Для этого изделие помещали в зажимное приспособление и поворачивали, чтобы убедиться, что были использованы именно те детали, какие нужно. После того как цикл завершался, изделие освобождали из зажима и извлекали из устройства. На такую проверку уходило чуть ли не в два раза больше времени, чем на саму работу! Как ни прискорбно, после столь сложного процесса испытаний изделие могло упасть на пол, а значит, потребитель мог, несмотря на все принятые меры, получить дефектную продукцию! Сложность подобных устройств создает множество неудобств. Старайтесь, чтобы методы предупреждения ошибок были простыми и эффективными.
В любом случае главное, чтобы дефекты (или ошибки) не отразились на потребителе. Это актуально даже при использовании эффективного устройства предупреждения ошибок. Следует обязательно предусматривать межпроцессные проверки, которые помогут оградить потребителя от какого бы то ни было риска. Ранее уже говорилось о том, что такие проверки осуществляет каждый работник, контролируя собственную работу и ключевые параметры работы других. Чем больше таких промежуточных проверок (шлагбаумов), тем меньше вероятность того, что дефект попадет к потребителю.
Ниже мы приводим список причин ошибок и упущений. Хотя он не исчерпывает всех причин, самые основные присутствуют.
1.Отклонение от заданного метода работы (работа должна быть стандартизирована до применения пока-ёкэ):
а)пропущенные этапы;
б)нарушение последовательности этапов.
2.Отсутствующие детали (или составляющие работы).
3.Неподходящая деталь (будьте особенно внимательны с взаимозаменяемыми деталями).
4.Неправильная настройка (ошибки при выборе инструмента или настроек).
5.Ошибки в информации или документации.
6.Ошибки, связанные с изменением последовательности (будьте внимательны с длинными строками цифр).
7.Ошибки, связанные с неверной интерпретацией (ищите сходные описания, цифры, внешние признаки).
8.Ошибка идентифицирована, однако исправить или устранить ее не удается.
Заметьте, что предупреждение ошибок не ограничивается предотвращением дефектов. Оно применимо к любому виду деятельности и к любой ошибке, которая вызывает отклонение от стандарта. Рабочий, к примеру, может забыть забрать изделие, а проектировщик — не ввести в документацию важную информацию. Обратимся к знакомому всем нам примеру.
Намереваясь заказать ланч, вы подъезжаете к своей любимой закусочной, где клиентов обслуживают в автомобиле, и видите, что ваш заказ, принятый кассиром, высветился на дисплее. Надпись на дисплее гласит: «Этот экран обеспечивает правильность приема заказа». Значит, ошибка может случиться во время приема заказа. Каким образом? Кассир может не расслышать сказанное. Клиент может ошибиться, называя блюдо или количество (едва ли подобное не случается в вашем бизнесе!). Кассир может нажать не ту клавишу (обратите внимание, что кассовые аппараты запрограммированы таким образом, что каждому блюду соответствует отдельная клавиша, что экономит время) или ошибиться, вводя данные о количестве.
Таким образом, уже на этом этапе можно допустить ряд ошибок, а ведь пока у нас только приняли заказ! Вспомните «былые времена», когда официант передавал заказ клиента работнику кухни. При этом тоже был риск совершить ошибку. Официант мог повторить заказ неправильно, на кухне его могли не расслышать или забыть часть сказанного. В наши дни во многих ресторанах на кухне установлены мониторы, на которых отображается заказ, введенный с клавиатуры. Ошибиться или забыть стало невозможно. В процессе приготовления пищи также имеется масса возможностей для ошибок. Чаще всего эти ошибки связаны с заказами, которые «отклоняются» от стандарта (даже когда вам обещают, что все будет сделано, «в точности как вы просили»). Вы просили не класть майонез или положить побольше маринованных овощей? Ошибка может быть допущена при приготовлении нестандартного блюда, а может оказаться, что ваш заказ выполнят как надо, но вместо него запакуют не то блюдо. Отделены ли блюда, приготовленные с учетом особых требований, от стандартных? Помечаются ли они какими-либо опознавательными знаками для предупреждения ошибок? Несмотря на уйму возможностей совершить ошибку, кажется настоящим чудом, что обычно мы получаем именно то, что заказали.
В условиях традиционного производства в течение дня возникают самые разные проблемы, о которых редко уведомляют лидеров (прежде всего из-за того, что рабочие предпочитают этого не делать). Нам приходилось видеть бездействующие станки, груды дефектных деталей и даже операторов, которые по той или иной причине покидают рабочее место, и все это в отсутствие какой бы то ни было реакции. Часто немногочисленные лидеры просто не в состоянии справиться с потоком проблем.
Одно из основных отличий Toyota от остальных компаний — в ее поддерживающей структуре и том, как она используется для эффективного контроля проблем и сохранения работоспособности системы. Функции и обязанности лидера группы и лидера команды, а также рекомендации по отбору подходящих кандидатов на эти должности будут изложены в главе 10. Пока достаточно сказать, что самое важное — определить норму управляемости для тех, кто выполняет эти обязанности. Лидер не может помогать нескольким десяткам работников, если линия или рабочее место останавливается каждый раз, когда возникает проблема. При этом не следует забывать, что число лидеров — вопрос компромисса, поскольку лидеры не занимаются непосредственным добавлением ценности. Однако такое увеличение косвенных издержек помогает избежать куда больших потерь. Дао Toyota предполагает множество краткосрочных капиталовложений, которые в долгосрочном аспекте окупаются сторицей.
Вопросы для самопроверки
1.Задумайтесь, предполагает ли культура вашей организации встраивание качества и правильное выполнение с первого раза.
A.Какое отношение к людям и ошибкам бытует в вашей культуре? Считается ли, что люди делают ошибки нарочно, по недосмотру или потому что они — плохие работники? Послушайте, что говорят об этом ваши сотрудники, и возьмите их мнение на заметку.
Б. Считаете ли вы, что ряд проблем возникает из-за небрежности?
B.Как изменить свое мышление и образ действий, чтобы это дало результаты?
Г. Должны ли работники участвовать в анализе и устранении проблем, которые они обнаруживают?
2.Совершая обходы с целью выявления потерь, обратите особое внимание, что происходит в случае возникновения проблемы.
A.Как решается, что есть проблема? Можно ли определить отклонение от стандарта визуально?
Б. Как работник, заметивший проблему, определяет ее наличие? Есть ли у него стандарт для сравнения, или он определяет ее интуитивно, на основании личного опыта?
B.Что происходит дальше? Мог ли работник известить о проблеме своего начальника, или был вынужден искать помощи самостоятельно?
Г. Последовала ли реакция от руководства после его извещения о проблеме?
Д. Предполагала ли эта реакция проверку воздействия проблемы на потребителе? Если да, была ли проблема изолирована, чтобы не допустить ее попадания к потребителю?
Е. Включала ли реакция установление причины проблемы и корректирующие действия, которые предупредят ее повторное возникновение?
Ж. Каково было общее время реакции в цикле решения проблемы? Каковы были общие потери из-за неэффективности системы?
3. Какие мероприятия по оптимизации системы нужно добавить в план внедрения?
3.Основа встраивания качества в процесс — это стандартизированная работа. Проанализируйте процесс стандартизированной работы и ответьте на следующие вопросы:
А. Четко ли определена процедура стандартизированной работы? Б. Входит ли в обязанности каждого оператора проверка качества поступающей работы? Определены ли конкретные зоны про-
верки с учетом статистических данных (проверка зон возможных неисправностей)?
В. Определены ли ключевые точки качества для каждой операции, и проверяются ли они перед выполнением данной операции?
Г. Допускает ли система остановку процесса при выявлении проблемы?
Д. Обеспечивает ли система автоматическую передачу проблемы на более высокий уровень для принятия корректирующих мер?
4. При очередном возникновении проблемы, вызванной тем, что кто-
то совершил ошибку, проанализируйте процесс принятия мер.
A.Ограничиваются ли контрмеры напоминаниями работникам, развешиванием табличек и переобучением? Если да, это свидетельствует о неспособности выявить подлинные причины и найти эффективные решения.
Б. Есть ли у работников стимул предлагать собственное решение проблемы?
B.Выявите глубинную причину совершения данной ошибки (см. раздел, посвященный решению проблем). Что можно сделать, чтобы предупредить совершение этой или подобной ошибки?
Г. Каков ваш подход к предупреждению ошибок? Развешиваете ли вы плакаты, выявляя уже совершенные ошибки, или стараетесь предупредить возникновение проблемы?
Д. Дополните свой план внедрения конкретной программой обучения руководства методам анализа основных причин и предупреждения ошибок.
ТЕХНОЛОГИЯ ДОЛЖНА ОТВЕЧАТЬ ПОТРЕБНОСТЯМ ЛЮДЕЙ И БЕРЕЖЛИВЫХ ПРОЦЕССОВ
Г" ережливое производство — это антитехнология», «Фанатики береж-
^/ливого производства вечно поливают грязью информационные технологии», «Дай поборникам бережливого производства волю, они выбросят на помойку все компьютеры. Впрочем, для них даже обычная ручка чересчур сложна, им подавай бумагу и карандаш». Подобное приходится нередко слышать от расстроенных специалистов по ИТ, когда сторонники бережливого производства препятствуют внедрению предлагаемых ими технологий. У таких специалистов складывается впечатление, что в Toyota вообще не верят в передовые технологии, и все как один разгуливают со счётами под мышкой.
Мы хотим развеять этот миф. Toyota — высокотехнологическая компания. Она применяет самые передовые технологии в мире. Мы не сравнивали уровень технологии Toyota и ее конкурентов, однако можем заверить вас, что Toyota использует все современные технологии в полной мере — роботов, суперкомпьютеры, настольные компьютеры, радиочастотную идентификацию, системы SAP, полностью автоматизированное производство и т.д. Не забывайте, что Toyota была первой компанией, которая начала массовое производство гибридного автомобиля, изобилующего микропроцессорами, а автомобили Toyota в Японии оснащены системами GPS.
Истоки заблуждения понятны. Дело не в нежелании Toyota применять передовые технологии, но в ее особом отношении к технологиям. Когда эксперты по бережливому производству рекомендуют какой-либо компании прекратить пользоваться системой планирования потребностей в материалах (MRP) в существующем виде, или отказаться от автоматизированной транспортно-складской системы, или не тратить деньги на суперсовременную покрасочную камеру, они просят не вообще отказаться от передовой технологии, а лишь прекратить использовать ее образом, который порождает потери. Не следует подменять технологией необходимость думать.
Вспомним историю Toyota и Сакити Тоёда, «короля изобретателей» Японии. Тоёда хотел автоматизировать ткацкий станок. Однако он не стал создавать лабораторию, занимающуюся НИОКР, для разработки невиданного, самого передового и дорогостоящего станка. Он хотел создать простой, дешевый станок, который облегчил бы труд женщин в сельской общине. Первые станки Тоёда изготавливал вручную из дерева. Чтобы приводить станок в действие, ему пришлось спроектировать паровой двигатель.