Столярные, плотничные, стекольные и паркетные работы: Практическое пособие Костенко Евгений
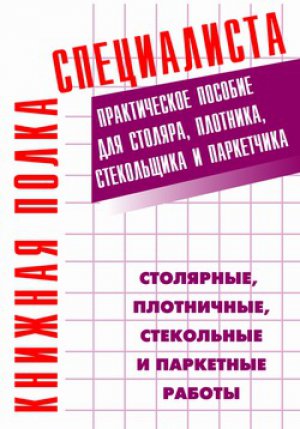
Опалубку колонн устанавливают следующим образом. Сначала на фундаменте (подколеннике) размечают оси колонн. В процессе бетонирования в фундаменты закладывают деревянные пробки. После разметки осей колонн на фундамент кладут рамку основания таким образом, чтобы ее оси совпал с осями колонны, прочерченными на фундаменте; после этого к фундаменту подносят щиты колонны и приступают к сборке короба, устанавливая его в рамку.
Рис. 157. Опалубка прямоугольных колонн: а – короб в собранном виде; б – стальной хомут; в – крепление короба колонны подкосами (расшивинами); 1 – дверка; 2 – короб; 3 – вырезы для ввода опалубки балок; 4 – хомуты; 5 – клинья; 6 – рамка основания; 7 – отверстия для клиньев; 8, 9 – щиты; 10 – упорные планки; 11 – рамка; 12 – пробка; 13 – подкос.
После установки короба проверяют точность внутренних размеров, совпадение осей арматуры колонны с осями опалубки, вертикальность установки опалубки. Хомуты на короб ставят после установки и выверки опалубки. Собранные короба, установленные в рамки, в проектном положении при высоте колонн до 6 м закрепляют расшивинами.
Опалубку балок и прогонов (рис. 158) обычно устанавливают одновременно и выполняют в виде коробов с днищем из ранее сколоченных щитов. Короб должен плотно прилегать к днищу, иначе через образующиеся щели из бетонной смеси будет вытекать цементное молоко. При сборке опалубки на высоте более 6 м пользуются лесами, а при сборке опалубки на высоте менее 6 м – подмостями.
На высоте менее 6 м опалубку устанавливают следующим образом. Сначала устанавливают днища коробов прогонов в вырезы коробов колонн и крепят после выверки горизонтальности монтажными гвоздями. После этого на землю кладут лаги и ставят на них на нужном расстоянии инвентарные стойки, которые подводят под днище прогонов. Вертикальность установки стоек проверяют отвесом с подбивкой клиньев. Стойки закрепляют монтажными гвоздями через днище в их оголовники. Боковые щиты короба прогонов крепят к боковым сторонам вырезов коробов колонн прижимными досками, прикрепляя их гвоздями к оголовнику стойки. По окончании этих работ днище опалубки вводят в вырезы коробов колонн и прогонов, подводя под него стойки, и ставят боковые щиты.
Стыки коробов балок с коробами прогонов заделывают скошенными репками, прикрепляя их монтажными гвоздями. Короб балки состоит из боковых щитов, днища, схваток, сбоку щитов расположена подкружальная доска. Для получения нужных размеров короб стягивают схватками.
Рис. 158. Установка опалубки балок и прогонов: а – общий вид установки; б – поперечное сечение короба при наличии плиты; в – поперечное сечение короба при отсутствии плиты; 1 – днище короба прогона; 2 – боковые щиты короба прогона; 3 – боковые щиты короба балки; 4 – днище короба балки; 5 – подставка; 6 – оголовник стойки; 7 – прижимные доски; 8 – доска опалубки плиты; 9 – доска подкружальная; 10 – схватки; 11 – стяжки
Рис. 159. Опалубка стен: а – доска направляющая, установленная на грунт; б – доска направляющая, установленная на бетонную подготовку; в – общий вид опалубки стены; г – ребро, собранное из двух досок; 1 – направляющая доска; 2 – колышек; 3 – пробка; 4 – щит стены; 5 – ребро; 6 – временная распорка; 7 – проволочная скрутка; 8 – схватка; 9 – брусок бетонный полый
Рис. 160. Опалубочный щит с термореактивным обогревом конструкции ЦНИИОМТП: 1 – вилочный разъем; 2 – электронагреватель; 3 – кляммеры; 4 – отражательный экран; 5 – утеплитель; 6 – защитная фанерная крышка с водостойким покрытием; 7 – каркас щита
Опалубка стен (рис. 159) состоит из двух строго параллельных панелей, собранных из щитов. Расстояние между панелями должно равняться проектной толщине стены. При сборке опалубки толщину стены фиксируют временными распорками.
Сначала планируют основание, на котором будет собираться опалубка, после чего устанавливают направляющие доски. В проектном положении направляющие доски крепят колышками, забиваемыми в грунт. Если направляющие доски кладут на бетонное основание, то их крепят гвоздями, забиваемыми в пробки, заранее уложенные в бетон. Кромки направляющих досок, обращенные к бетону, фрезеруют. Для стен толщиной до 500 мм опалубку собирают из щитов, поддерживаемых ребрами, а при стенах толщиной более 500 мм панели дополнительно скрепляют схватками. Боковое давление бетонной смеси воспринимается скруткой или стяжными болтами. Стяжные болты перед установкой смазывают минеральным маслом, чтобы их легче было вынимать. По мере заполнения бетонной смесью пространства между панелями временные распорки убирают. При установке опалубки стен надо проверить отвесом вертикальность установленных щитов, а шаблоном – расстояние между щитами.
Применяют также термореактивные опалубочные щиты на основе разборно-переставной опалубки «Монолит-72», при использовании которых наряду с формованием можно производить тепловую обработку свежеуложенной бетонной смеси (электрообогрев). Щит опалубки (рис. 160) устроен так: на внутренней поверхности стальной палубы приварены кляммеры из проволоки диаметром 3 мм, к которым крепятся электронагреватели.
К среднему поперечному ребру щита болтами прикрепляют кронштейн с вилочным разъемом, к которому подсоединяют концы электронагревателей. Над электронагревателями на расстоянии 10–15 мм кладут отражательный экран из тонкого алюминия, предназначенный для уменьшения теплопотерь. Внутренние промежутки щита заполняют утеплителем. Поверх утеплителя (шлаковойлочных плит) для его защиты от повреждений кладут фанеру толщиной 4–5 мм.
Питание опалубки электроэнергией осуществляется от понижающих трансформаторов через инвентарные распределительные устройства. Опалубку устанавливают на грунт, очищенный от мусора, снега, наледи и заранее отогретый. Примерно за полчаса до заполнения опалубки бетонной смесью включают электронагреватели. Размеры щитов: 500–6001200–1800 мм.
Устойчивость опалубки при монтаже обеспечивается стойками, которые опираются на прочное основание и раскрепляются расшивинами. Ни в коем случае нельзя допускать, чтобы при бетонировании опалубка проседала, выпучивалась, т. е. деформировалась. Площадка для установки опалубки должна быть ровной, без бугров и впадин. При установке щитов надо следить за плотностью их примыкания друг к другу. До начала укладки арматуры опалубку осматривают и проверяют поверхности опалубки и их положение относительно проектных осей конструкций, правильность установки, крепления опалубки и установки пробок, закладных деталей, плотность соединения щитов и стыков.
Правильность размеров опалубки проверяют стальным метром, горизонтальность – уровнем, вертикальность коробов, колонн – отвесом. Готовую опалубку принимает мастер или прораб.
Перед установкой опалубку очищают от мусора, грязи, арматуру – от ржавчины, имеющиеся щели в опалубке заделывают. Поверхности оборачиваемой опалубки покрывают смазкой.
Опалубку разбирают после достижения бетоном требуемой прочности по разрешению прораба те рабочие, которые будут повторно ее устанавливать. Разборку производят осторожно, не нарушая целостности бетона и опалубки. Стойки, поддерживающие днище опалубки, снимают лишь после разборки боковой опалубки и осмотра распадубленных элементов и поддерживающих конструкций. Демонтаж термореактивной опалубки производят после отключения всех щитов от источников питания и изъятия коммутирующей разводки из рабочей зоны. Разобранные элементы опалубки осторожно снимают, очищают металлическими щетками от остатков бетона и освобождают от торчащих гвоздей.
Опалубку большей частью приходится устанавливать на высоте, поэтому при выполнении этой работы нужно строго соблюдать правила техники безопасности. При работе на высоте более 1,5 м без ограждений плотники должны быть обеспечены предохранительными поясами с карабинами.
Допускаемые отклонения положений и размеров (мм) устанавливаемой опалубки, поддерживающих лесов от проекта. Расстояние между опорами изгибаемых элементов опалубки и расстояние между связями вертикальных поддерживающих конструкций от проектных размеров: на 1 м длины – 25 мм, на весь пролет – не более 75 мм. Расстояние от вертикали или проектного наклона плоскостей опалубки и линии их пересечения: на 1 м ысоты – 5 мм, на всю высоту: фундаментов – 20 мм; стен и колонн высотой до 5 м – 10 мм; стен и колонн высотой более 5 м – 15 мм; балок и арок – 5 мм. Смещение осей опалубки от проектного положения: фундаментов – 15 мм; стен и колонн – 8 мм; балок, прогонов, арок – 10 мм. Внутренние размеры опалубки балок, колонн и расстояние между внутренними поверхностями опалубки стен от проектных размеров – 3 мм. Местные неровности опалубки при проверке двухметровой рейкой – 3 мм.
Работа по возведению опалубки на одной вертикали на двух ярусах разрешается только при устройстве навесов, которые защищают работающих ниже. Открытые проемы в стенах, находящихся на одной отметке с перекрытием, на котором ведутся работы по установке опалубки, должны быть ограждены. Щиты, доски следует укладывать так, чтобы острия гвоздей были обращены вниз. Разбирать опалубку можно с разрешения мастера, производителя работ, а опалубку для конструкций длиной более 6 м – с разрешения главного инженера организации. При разборке опалубки необходимо принять меры против возможного падения элементов опалубки.
Глава 8
БИОЛОГИЧЕСКАЯ ЗАЩИТА
ДЕРЕВЯННЫХ КОНСТРУКЦИЙ
(АНТИСЕПТИРОВАНИЕ)
Древесина загнивает вследствие заражения и развития в ней дереворазрушающих грибов. Развитие грибов в элементах конструкций зданий происходит при определенных условиях. Особенно усиленно домовые грибы развиваются в древесине, имеющей повышенную влажность (30–60 %). В помещении зданий грибы развиваются при плохом проветривании внутри конструкций (подполья и т. п.).
Меры по борьбе с поражением деревянных деталей и изделий, а также конструкций из них проводятся при строительстве и эксплуатации зданий.
Защита древесины заключается в создании таких эксплуатационных условий работы конструкций, при которых обеспечиваются достаточная степень сухости и систематическое проветривание элементов из древесины.
Для ограждения воздушно-сухой древесины от увлажнения нельзя допускать непосредственного примыкания опор деревянных конструкций к каменной кладке, бетону и т. п. Все деревянные части, соприкасающиеся с кладкой, изолируют водонепроницаемым материалом (толем, рубероидом).
Слой утеплителя деревянных стен здания с внутренней стороны ограждают пароизолятором (пергамин, толь, рубероид, пленка и т. п.), благодаря чему стена не подвергается конденсационному увлажнению, возникающему вследствие разности температур и влажности наружного и внутреннего воздуха.
Антисептики, применяемые для обработки деревянных элементов зданий, должны иметь большую токсичность к грибам, насекомым и вместе с тем не должны влиять на здоровье рабочих. Антисептики бывают водорастворимые (фтористый натрий, кремнефтористый аммоний), маслянистые (сланцевые, каменноугольные масла) и растворимые в органических растворителях (пенолхлорфенол, нафтенат меди).
Древесину пропитывают антисептиками под внешним давлением – в автоклавах и без давления – в ваннах, пастами и т. д.
Древесину, подлежащую антисептированию, очищают от грязи, снега, наледи, окоряют и очищают от луба, рассортировывают по породам, влажности, размерам. Для увеличения глубины проникания антисептика труднопропитываемую древесину (ядро сосны, ели, пихты) предварительно накалывают.
В горяче-холодных ваннах элементы деревянных конструкций пропитывают водными растворами антисептиков или маслянистыми антисептиками. При пропитывании водными антисептическими растворами древесину загружают в ванну, которую заполняют горячим водным раствором антисептика температурой 90–95 °C. Время выдержки в горячем растворе зависит от влажности древесины и ее сечения. Уровень раствора должен быть выше уровня древесины на 80–100 мм. По окончании выдержки древесины горячий раствор в той же ванне заменяют в течение 5–7 мин холодным температурой 20–30 °C либо переносят древесину в другую ванну с холодным раствором.
При пропитке древесины маслянистыми антисептиками температура в горячей ванне должна быть 95–110 °C, а в холодной – 40–50 °C. Качество пропитки характеризуется глубиной проникания антисептика в древесину. При пропитке в ваннах с предварительным подогревом древесина березы, бука, тополя, осины, ольхи, а также заболонь сосны и кедра должны быть пропитаны водными растворами антисептиков (или антипиренов) на глубину не менее 5 мм, а маслянистыми антисептиками – на глубину не менее 10 мм; древесина ядра сосны, кедра, ели, пихты – на глубину не менее 2 мм. Глубину проникания антисептиков, окрашивающих древесину, определяют по цвету древесины, а глубину проникания бесцветных (фтористых) антисептиков – индикаторами.
Поверхностную антисептическую обработку элементов деревянных конструкций пастами марки 100 производят краско– или гидропультами или погружением в ванну с пастой, а пасту марки 200 наносят специальными механизмами или кистью равномерным слоем без пропусков.
В зимнее время пасту перед нанесением подогревают до температуры 40–50 °C, а древесину обрабатывают при температуре не ниже 10 °C.
Ремонтируют элементы зданий, пораженных домовыми грибами, обычно летом, так как в это время года деревянные конструкции зданий просушиваются лучше всего. Для борьбы с домовыми грибами необходимо провести следующее: устранить возможность увлажнения древесины в конструкциях, просушить и проветрить помещения, удалить пораженные грибами участки древесины.
Для удаления пораженной части элементов зданий надо вскрыть конструкции и удалить не только явно пораженную древесину, но и прилегающую к ней на расстоянии до 0,5 м здоровую часть древесины.
Все удаленные и пораженные элементы древесины и мусор обезвреживают на месте вскрытия 5–10 %-ным раствором медного или железного купороса, после чего мусор и пораженную древесину сжигают, не допуская их для использования в качестве дров, так как они могут послужить источником повторного заражения элементов здания.
Верхний слой неорганической засыпки толщиной не менее 100 мм и мусор из подполья, зараженного грибами, удаляют и антисептируют 10 %-ным раствором железного купороса, после чего закапывают вдали от здания в землю на глубину не менее 0,5 м.
Новую засыпку до укладки антисептируют сухой хлорной известью в количестве 0,2 кг на 1 м2 подполья. Каменные или кирпичные элементы, стены фундаментов, столбики, примыкающие к зараженной древесине, аккуратно очищают от грибных образований и обжигают паяльной лампой.
Вместо удаленных деревянных элементов применяют новую древесину влажностью до 20 %, очищенную от коры и луба. До установки на место новые элементы антисептируют пастой 200.
Антисептики – ядовитые вещества, опасные для здоровья человека, поэтому при работе с ними нужно быть очень осторожными. Готовят антисептические растворы на специальных открытых площадках так, чтобы рабочие располагались с наветренной стороны. Посторонним лицам находиться на этой площадке запрещается. Рабочие, приготавливающие растворы, обеспечиваются противогазами или респираторами, очками и резиновыми перчатками. Ванны для антисептирования должны иметь крышки.
Глава 9
ЗАЩИТА ДРЕВЕСИНЫ ОТ ВОЗГОРАНИЯ
Для защиты древесины от возгорания применяют огнезащитные и пропиточные составы. Обрабатывают древесину двумя способами: методом глубокой и поверхностной пропитки. Для защиты деревянных конструкций от возгорания методом глубокой пропитки (в автоклавах, горяче-холодных ваннах) применяют антипирены: диамоний фосфат в смеси с сернокислым аммонием 12–20 %-ной концентрации; сульфат аммония в смеси с фосфорнокислым аммонием или фосфорнокислым натрием такой же концентрации; буру в смеси с борной кислотой 20 %-ной концентрации.
Поверхностную огнезащитную обработку клееных конструкций ведут пропиточным составом ПП, нагретым для лучшей адгезии с поверхностью до температуры 50–60 °C и состоящим из углекислого калия (25 частей по массе), керосинового контакта Петрова (3 части по массе) и воды (72 частей по массе). Элементы деревянных конструкций обрабатывают составом 20 %-ной концентрации 2 раза. Интервал между первой и второй обработкой должен быть не менее 2 ч, температура воздуха в помещении 18–20 °C.
На строительной площадке для защиты древесины от возгорания используют вспучивающееся огнезащитное покрытие ВПД. Им покрывают конструкции, эксплуатируемые внутри помещений с неагрессивной средой, положительной температурой до 35 °C и относительной влажностью воздуха до 60 %. Толщина высохшего покрытия после нанесения должна быть не менее 0,2 мм.
Состав покрытия (в частях по массе): меламино– и мочевиноформальдегидная смола ММФ-50 – 31,5; карбоксиметилцеллюлоза (КМЦ) – 15,9; мелем – 18,4; дициандиамид технический – 6,3; аммофос марки А – 27,5.
До покрытия поверхность древесины очищают от пыли, грязи, наплывов смолы, жировых пятен. Влажность древесины должна быть не более 20 %. Наносят состав пневмораспылителем в два слоя с сушкой не менее 5 ч после первого покрытия и 24 ч – после второго. При нанесении состава нужно пользоваться резиновыми перчатками, респираторами, защитными очками и комбинезонами. Конструкции и их элементы, обработанные огнезащитными составами на основе солей, должны быть защищены от увлажнения и вымывания солей.
Глава 10
РЕМОНТ ПЛОТНИЧНЫХ КОНСТРУКЦИЙ
Ремонт крыши. До начала ремонта нужно осмотреть конструкцию крыши и определить, какие элементы подлежат ремонту. Загнивший подстропильный брус заменяют брусом такой же длины и сечения, предварительно обработав его антисептиком. В брусе заранее делают нужные врубки, чтобы концы стропильных ног опирались точно, без подгонки.
Загнившие стропила либо заменяют новыми, либо усиливают досками-накладками, прикрепляя их болтами. При провисании крыши необходимо сначала выровнять ее, установив стойки с клиньями либо домкрат, после чего под провисшие стропила ставят подкосы, которые соединяют со стропильной ногой скобами. Поврежденные участки кровли заменяют новыми.
Ремонт перекрытий. В балочных перекрытиях наиболее подвержены загниванию балки и щиты. В балках большей частью загнивают концы, заделанные в стены. Состояние балок определяют визуально, а также путем простукивания обухом топора. Если при простукивании получается глухой звук, состояние балки неудовлетворительное. Загнившие балки усиливают деревянными антисептированными накладками из досок или бруса с обеих сторон, прикрепляя их болтами. Накладки должны быть того же сечения, что и балки, но длиннее загнившей части примерно в 2 раза. Негодные щиты перекрытия заменяют такими же новыми антисептированными щитами.
Ремонт дощатых полов. Дощатые полы спустя год после укладки усыхают, коробятся, поэтому их необходимо сплотить. До начала сплачивания полов аккуратно снимают плинтус и маркируют его, чтобы после ремонта можно было его поставить на прежнее место. Топором аккуратно приподнимают каждую доску отдельно, отдирая ее от лаги, а гвозди вытаскивают. После разборки части пола приступают к его настилке, пользуясь сжимами. После сплачивания каждую доску крепят к лагам гвоздями с утапливанием шляпок добойником. При выходе из строя отдельных досок (загнивание, поломка и т. п.) аналогичным путем убирают дефектную доску пола и заменяют ее здоровой, предварительно проантисептировав пласть и кромки, и крепят гвоздями с утапливанием шляпок.
Ремонт стен рубленых (бревенчатых) и брусчатых домов. Венцы бревенчатых домен загнивают вследствие некачественной изоляции их от каменных фундаментов, применения влажных бревен и влияния атмосферных осадков. Чаще всего загнивают нижние венцы, а также бревна, расположенные под оконными коробками и в углах. При замене нижнего венца дома взамен вышедшего из строя подготавливают новое бревно, выбирают в нем паз, окаривают и антисептируют его. После этого под столбчатые фундаменты с другой стороны от пролета, где расположено бревно, подлежащее замене, подводят козелки или домкраты и несколько приподнимают венец, вырубают загнившее бревно и заменяют его новым. Нижние брусья в брусчатых домах заменяют аналогично.
Ремонт каркасных и панельных домов. В процессе эксплуатации домов в отдельных зданиях наблюдается промерзание стен. Это вызвано тем, что в стенах проседает утеплитель – минераловатные плиты, минеральная вата. Промерзание стен устанавливают в зимнее время, причем обычно в верхней части стены появляется иней. Ремонт стен производят следующим образом: снимают аккуратно 1/3 внутренней стороны здания облицовку (ДВП, гипсокартонные листы и т. д.), затем снимают с панелей, каркаса обшивку, после чего вытаскивают осевший утеплитель и вставляют новый, следя за тем, чтобы между ним и каркасом не было зазоров. Минераловатные плиты лучше крепить на клею – они не проседают и не образуют мостиков холода. После установки утеплителя стены обшивают и облицовывают плитными материалами (ДВП, гипсокартонными листами и т. д.).
Раздел четвертый
СТЕКОЛЬНЫЕ РАБОТЫ
Глава 1
НАЗНАЧЕНИЕ И ВИДЫ СТЕКОЛЬНЫХ РАБОТ
В помещениях с постоянным пребыванием людей, в том числе в жилых, общественных и производственных зданиях, должно быть организовано хорошее естественное освещение. Естественное освещение бывает боковое, верхнее, комбинированное – верхнее и боковое. При естественном освещении помещения свет извне (т. е. дневной свет) проникает через световые проемы (окна), расположенные в наружных ограждающих конструкциях (стенах).
Боковое естественное освещение – это освещение помещения через световые проемы, устроенные в наружных стенах. Верхнее естественное освещение осуществляется через фонари, световые проемы, расположенные в покрытии, а также через проемы в стенах в местах перепада высот здания.
Комбинированное естественное освещение является сочетанием верхнего и бокового естественного освещения. Через остекленные световые проемы проникают солнечные лучи, которые благотворно влияют на состояние человека, повышают его работоспособность и отрицательно воздействуют на вредные микроорганизмы.
Освещенность помещений и рабочих мест регламентируется строительными нормами и правилами «Естественное и искусственное освещение». В соответствии с правилами помещения освещают через окна, световые фонари, стеклянные крыши. Причем освещенность помещения должна соответствовать нормам, так как нарушение норм может вызвать при излишнем освещении в летний период перегрев помещений, а в зимний период их переохлаждение.
В зависимости от размеров помещений, климатических условий, вида зданий и их назначения освещение и вентиляция помещений проводятся через световые проемы, размеры которых определяются в соответствии со СНиПом. Остекление световых проемов (окон, фонарей) бывает одинарное, двойное, тройное; из оконного стекла, стеклопакетов, стеклоблоков и т. п.
Остекление оконных переплетов должно быть выполнено качественно, так как при некачественном выполнении этих работ деревянные окна промерзают, загнивают, а металлические переплеты, помимо промерзания, коррозируют.
Освещение жилых, общественных зданий осуществляется в основном через оконные проемы, а производственных зданий, кроме того, и через остекленные фонари.
Оконные блоки могут быть деревянные, деревометаллические, металлические и пластмассовые.
Остекляют оконные блоки оконным стеклом и стеклопакетами. Для остекления окон применяют стекло толщиной 2–6 мм, а для остекления дверей – прозрачное или узорчатое стекло толщиной до 7 мм. Двери с качающимися полотнами остекляют только прозрачными стеклами.
Витрины в общественных зданиях остекляют большеразмерным полированным или неполированным стеклом толщиной 6,5–12 мм. Остекленные крыши для получения хорошего солнечного освещения применяют в теплицах, оранжереях и т. д.
Процесс производства стекольных работ состоит из следующих последовательно выполняемых работ: приготовления замазки, раскроя стекла, подготовки окон, дверей, переплетов, фонарей и т. д. к остеклению – очистки и олифовки фальцев, вставки стекол.
Стекольные работы состоят из следующих основных операций: кладки переплетов на стол, очистки фальцев (отверткой, стамеской), олифовки фальцев, нанесения на фальцы замазки с созданием основания (постели) под стекло промазчиком, раскроя стекла стеклорезом, вставки стекол, крепления стекол в фальцах шпильками, скобками и т. д. (пистолет, молоток), промазки стекол вдоль фальцев с выравниванием замазки (промазчик, нож, стамеска) и снятии ее излишков, очистки стекол от излишков замазки, протирки стекол.
Оконное стекло предназначено для заполнения световых проемов зданий и сооружений различного назначения. Стекло оконное неполированное марки М6 изготовляют в виде плоских листов, имеющих наименьшие размеры 400500 мм и наибольшие размеры при толщине 2–2,5 мм – 10001600 мм, при толщине 3–3,5 мм – 13002000 мм и при толщине 4–6 мм – 16002500 мм.
Стекло должно иметь прямоугольную форму, ровные кромки, целые углы и должно отламываться по линии надреза не растрескиваясь. Листы стекла должны быть равномерной толщины. Стекло должно быть бесцветным, в нем не должно быть дефектов: пузырей, инородных включений, волнистости и др.
Стекло витринное бывает двух марок: марки М7 – полированное и марки М8 – неполированное. Стекло выпускается толщиной 6,5–12 мм и имеет максимальные размеры 30006000 мм.
Витринное стекло применяется для устройства витрин в магазинах, витражей и в ограждающих конструкциях выставочных залов, аэропортах, вокзалах, кинотеатрах, клубах, павильонах и т. д.
Витринное стекло должно иметь прямоугольную форму, ровные кромки, целые углы.
Стекло листовое узорчатое предназначено для заполнения световых проемов и устройства внутренних ограждений в зданиях разного назначения, в том числе для декоративного остекления перегородок, дверей, окон с целью снижения солнечной радиации. Стекло листовое узорчатое прокатное бывает бесцветным или цветным и имеет на одной или обеих сторонах рельефный узор, полученный от гравировальных валков.
Стекло выпускается толщиной 3,5–7 мм, и при толщине 3,5–5 мм имеет длину 600–1600 мм, ширину 400–1200 мм, а при толщине 6–7 мм имеет длину 1000–2500 мм, ширину 800–1600 мм.
Узорчатое стекло перевозится в контейнерах или деревянных ящиках; при перевозке ящики или контейнеры должны быть установлены торцами по направлению движения с прочным креплением во избежание их передвижения или качания.
Храниться листы стекла должны на пирамидах или стеллажах на резиновых, войлочных или деревянных прокладках в наклонном положении с углом наклона к вертикали 10–15°. Ящики со стеклом также должны храниться в наклонном положении.
Морозовидное стекло можно получить из гладкого стекла путем обработки его пескоструйным аппаратом с созданием матовой поверхности и нанесения на него кистью в виде отдельных мазков в разных направлениях раствора столярного клея. До нанесения раствора клея стекло должно быть просушено и хорошо очищено от следов жира. После нанесения клея стекло нужно уложить в горизонтальном положении в сушильную камеру и при температуре порядка 50–60 °C высушить поверхность нанесенного клея. При нагревании стекло расширяется, а клей сжимается. После высыхания клей отстает от стекла в виде чешуек, срывая одновременно поверхностный слой стекла, образуя при этом на поверхности стекла узоры, напоминающие собой «мороз».
Армированное металлической сеткой листовое стекло бывает бесцветное или цветное, имеет поверхности гладкие или с узором. Стеклом этого типа заполняют световые проемы (фонари) и применяют для ограждения (балконов, лифтов) в жилых и общественных зданиях.
Длина стекла 800–1200 мм, а ширина 400–1600 мм. Толщина листов для бесцветного стекла 5,5 мм, для цветного стекла 6 мм.
Поверхности листов могут быть гладкими (коваными) или одна поверхность гладкой (кованой), а другая рифленой или узорчатой. На одной поверхности листа стекла допускаются неровности от заглубления сетки в виде незначительных складок в пределах допускаемых отклонений по толщине стекла. Бесцветное стекло может иметь зеленоватый или голубоватый оттенок.
Стекло армируется сварной сеткой из стальной проволоки с защитным алюминиевым покрытием с ячейками 12,5 и 25 мм, причем сетка должна располагаться по всему листу на расстоянии не менее 1,5 мм от поверхности стекла.
Увиолевое стекло применяется для остекления закрытых помещений типа оранжерей, лечебных учреждений и т. п. Оно пропускает не менее 25 % ультрафиолетовых лучей. Применение этого вида стекла создает более здоровые условия проживания, особенно в закрытых помещениях. Стекло имеет размеры 250250–20002000 мм и толщину 2–6 мм.
По истечении определенного времени стекло желтеет, т. е. стареет, в результате чего снижается способность для пропускания ультрафиолетовых лучей.
Стекло закаленное – стемалит – применяется для внутренней и наружной отделки стен и перегородок зданий и сооружений и представляет собой плоские листы стекла, покрытые с одной стороны эмалевой краской с последующей термообработкой, благодаря чему стекло упрочняется и краска закрепляется на его поверхности. Стемалит изготовляется размерами по длине 400–1500 мм с интервалом в 100 мм, по ширине 900–1100 мм с интервалом в 50 мм, толщиной 5–7,5 мм. Стемалит изготовляется из оконного или витринного полированного и неполированного стекла.
Теплопоглощающее стекло применяют для остекления холодильных установок и т. п. Оно служит для поглощения инфракрасных (тепловых) лучей, поэтому широко применяется в тех помещениях, где пониженная температура вызывается технологией производства. Стекло имеет размеры 300500–22003500 мм, толщину 6 мм.
Блоки стеклянные пустотелые предназначены для кладки светопрозрачных не несущих ограждающих конструкций зданий и сооружений. Ограждения из стеклоблоков применяют также при устройстве световых проемов в наружных стенах, на лестничных клетках, в санузлах, в спортзалах, бассейнах и т. п. Блоки бывают неокрашенные и цветные. Размеры блоков по длине 194–294 мм, ширине 194–244 мм, толщине 98, 75 мм. Масса блоков 2,8–4,3 кг. Блоки бывают квадратные (БК), квадратные цветные (БКЦ), прямоугольные (БП). Неокрашенные блоки могут иметь желтоватый, голубоватый или зеленоватый оттенки. Наружные поверхности лицевых стенок блока должны быть плоскими. Внутренние поверхности лицевых стенок блока должны быть гладкими или иметь рельефный узор, а торцовых – гладкими. Толщина лицевых стенок блока должна быть не менее 8 мм.
Стеклопакеты клееные (рис. 161) предназначены для остекления окон, балконных дверей, витрин, зенитных фонарей жилых, общественных, промышленных зданий и сооружений.
Клееные стеклопакеты состоят из двух или трех плоских листов стекла, соединенных по контуру так, что между ними образуется герметически замкнутая камера с прослойкой осушенного воздуха.
В зависимости от конструкции стеклопакеты подразделяются на следующие типы: СПО – однокамерные без обрамляющей рамки; СПОР – однокамерные с обрамляющей рамкой; СПД – двухкамерные без обрамляющей рамки.
Для изготовления стеклопакетов применяются оконное, витринное, теплопоглощающее и другие виды стекол.
В однокамерных стеклопакетах расстояние между стеклами составляет 6–16 мм, в двухкамерных – 6–12 мм.
Стеклопакеты должны иметь прямоугольную форму. Внутренние поверхности стекол в стеклопакетах должны быть чистыми. Герметические слои в стеклопакетах делают сплошными, без разрывов и нарушений герметизирующего слоя. Ширина герметизирующего слоя стеклопакетов допускается не более 14 мм для однокамерных и 16 мм для двухкамерных. Стеклопакеты должны быть герметичными. Для изготовления распорных и обрамляющих рамок, соединительных уголков распорных рамок должна применяться лента из алюминиевых сплавов. Для заполнения внутренней полости распорной рамки стеклопакета в качестве влагопоглотителей должен применяться технический силикогель.
Максимальные размеры однокамерных стеклопакетов: 10001500, 20001600, 2000 2500, 29502950 мм; двухкамерных – 10001400, 1500 1700 мм.
Применение стеклопакетов дает следующие преимущества; снижаются теплопотери и звукопроводность, исключается запотеваемость стекол.
Рис. 161. Клеене стеклопакеты: а – однокамерный СПО; б – однокамерный СПОР; в – двухкамерный СПД; 1 – стекло; 2 – распорная рамка; 3 – влагопоглотитель; 4 – нетвердеющая мастика; 5 – вулканизирующийся герметик; 6 – воздушная прослойка; 7 – дегидратационная щель; 8 – обрамляющая рамка; – толщина стекла; h – толщина стеклопакета; hр – толщина стеклопакета с обрамляющей рамкой; hс – расстояние между стеклами; С – ширина герметизирующегося слоя; Ср – ширина полки обрамляющей рамки
Рис. 162. Типы профильного стекла: а – швеллерное; б – коробчатое; в – ребристое
Стекло профильное строительное (рис. 162) предназначено для устройства наружных светопрозрачных конструкций в зданиях и сооружениях различного назначения. Этот вид стекла светопрозрачен и создает в помещении рассеянное мягкое освещение. Стекло по сечению бывает в виде швеллера, коробчатым и ребристым. Профильное стекло выпускается бесцветным и цветным, армированным и неармированным, с гладкой (кованой), рифленой или узорчатой поверхностью. Стекло должно быть отожжено.
При транспортировке швеллерное и коробчатое стекло должно быть уложено на боковые поверхности, а ребристое – плашмя, торцами по направлению движения с расшивкой деревянными планками и заполнением свободного пространства древесной стружкой. Стекло на стройках должно храниться в закрытых помещениях или под навесом в стопах.
Глава 2
МАТЕРИАЛЫ ДЛЯ СТЕКОЛЬНЫХ РАБОТ И ПРИГОТОВЛЕНИЕ ЗАМАЗОК
1. Элементы для крепления стекла в переплетах
Для крепления стекла применяют мелкие гвозди длиной до 20 мм или шпильки, нарезанные из проволоки, имеющие насечку (для облегчения их нарезки). Толщина проволоки должна быть не более 1,5 мм. При креплении стекла в фальцах переплетов используют деревянные раскладки, которые крепятся шурупами либо гвоздями с приплюснутой или с откусанной шляпкой.
Эластичные прокладки (резиновые) взамен замазки используют при вставке стекол, в основном витринных. Эластичные прокладки (рис. 163, а) бывают прямоугольные, П-образные, трубчатые и должны быть мягкими и морозостойкими. Кроме резиновых, применяют прокладки поливинилхлоридные.
Шпильки, штыри (рис. 163, б), кляммеры (рис. 163, в) и пружинки (рис. 163, г) используют для крепления стекол в металлических или железобетонных переплетах. Штыри бывают квадратные или круглые, их изготовляют из стали. Они бывают длиной 20–25 мм, толщиной 4–6 мм. Кляммеры, пружинки делают преимущественно из оцинкованной кровельной стали. Если кляммеры, пружинки сделаны из обычной кровельной стали, их во избежание коррозии до установки следует покрыть масляной краской или масляным лаком.
Рис. 163. Элементы для крепления стекол: а – эластичные прокладки; б – штыри; в – кляммеры; г – пружинки.
2. Материалы для приготовления замазок
Для приготовления замазок применяют мел, олифу, белила, битум, портландцемент и т. п.
Мел является основным заполнителем при приготовлении замазок. Он представляет собой белый порошок. Для приготовления замазки применяется порошковый мел, получаемый после размола комообразного мела. Влажность мела должна быть не более 5 %, а тонкость помола такой, чтобы он через сито с мелкими отверстиями (625 в 1 см2) хорошо просеивался. При поступлении комового мела его размалывают в мелотерках. В случае поступления на стройку мела с повышенной влажностью его сушат до требуемой влажности в печах или на электроплитах. Следует учесть, что для приготовления замазки требуется мел только тонкого помола, при этих условиях замазка получается более качественной.
Олифа является связующим веществом при приготовлении замазок и бывает натуральной, вырабатываемой из льняного или конопляного масла с добавлением сиккативов (ускорителей высыхания). Помимо натуральной, бывает олифа типа «Оксоль», которая представляет собой раствор оксидированного растительного масла и сиккативов в уайтспирите.
При работе с олифой надо учесть, что она является пожароопасным веществом (температура вспышки в закрытом тигле 220–280 °C). Одежда, тряпки, пакля, вата, пропитанные олифой, могут самовозгораться. Все работы с применением олифы (приготовление замазок) должны производиться в помещениях, оборудованных приточно-вытяжной вентиляцией и противопожарными средствами.
Белила, сурик придают замазке большую прочность и окраску (цвет). Для замазки применяют в основном тертые белила. Замазка с применением белил ввиду большой прочности применяется для остекления витрин и уникальных зданий. Замазка на битуме применяется для остекления фонарей и переплетов в производственных зданиях. Для замазок применяют битумы марок БН50/50, БН70/30 и БН90/10.
Портландцемент представляет собой порошок тонкого помола и имеет серовато-зеленый цвет. Для приготовления замазок используется цемент марок 400–600. Замазка, приготовленная с компонентом из цемента, применяется для остекления металлических и железобетонных переплетов. Кроме того, для укладки стеклоблоков применяют растворы с применением цемента.
Замазки, уплотнительные прокладки предназначены для герметизации стыков при остеклении. Замазка может применяться отдельно или совместно с уплотнительной прокладкой. Уплотнительные материалы, замазка, прокладки должны быть воздухо– и водонепроницаемыми, морозостойкими, сохранять эластичность и отвечать санитарно-гигиеническим требованиям.
3. Приготовление замазок
Замазка представляет собой тестообразную массу. Она должна обладать удобонаносимостью, быть мягкой, пластичной, хорошо наноситься и обеспечивать плотное заполнение промежутков между стеклом и фальцами переплетов. Она должна хорошо прилипать к стеклу, древесине, бетону и металлу, не прилипать к рукам. Замазка должна без особых усилий наноситься ножом или стамеской, не прилипать к ним, не тянуться за ними и не соскальзывать с них. При нанесении ее на фалец она должна хорошо заглаживаться ножом или стамеской и оставлять после прохода ножа гладкую и блестящую поверхность. После высыхания (затвердения) на замазке не должно быть трещин, и она не должна отслаиваться (отваливаться) от фальца.
Кроме того, замазка должна быть водо-, морозо– и теплостойкой с тем, чтобы под воздействием переменной влажности и температуры она не деформировалась и не изменяла свои свойства, и длительное время должна быть вязкой.
В процессе и после высыхания замазка должна сохранять небольшую эластичность, чтобы при набухании переплетов в процессе эксплуатации стекло не лопалось вследствие некоторой подвижности (эластичности) замазки. Обычно замазка затвердевает по истечении 15 суток.
Замазка, приготовленная для нанесения промазчиком – шприцем, должна быть такой консистенции, чтобы она легко, без особых усилий выходила из него.
Наиболее качественной является замазка, приготовленная на натуральной олифе, несколько хуже по качеству замазка, приготовленная на искусственной олифе типа «Оксоль». Для остекления металлических, железобетонных переплетов используют замазку, приготовленную на натуральной олифе с применением в качестве добавок масляных – густотертых красок (белил), железного сурика. Замазка, приготовленная с этими добавками, более прочна и водостойка.
Приготавливают замазку двумя способами: вручную и механическим путем с помощью машин. Вручную замазки в небольших объемах обычно готовят на стройках, а в больших объемах – в специализированных централизованных мастерских.
Вручную замазку приготавливают следующим образом: берут металлический лист из кровельной стали, фанеры или противень и в него насыпают горкой сухой, тонкомолотый и просеянный мел. В середине листа в горке мела образуют лунку-воронку, в которую наливают олифу, после чего всю массу посредством шпателя аккуратно перемешивают. Мел и олифу берут в количестве, соответсвующем рецептуре. При перемешивании следят за тем, чтобы замазка была не слишком густой. В случае получения негустой замазки в нее добавляют мел в необходимом количестве или при большой густоте добавляют олифу. Для обмазки стекла в переплетах требуется пластичная замазка. В том случае, когда замазка получилась не очень густой, берут поддон без бортов или лист фанеры и насыпают сухой молотый мел равномерно толщиной 1–2 мм, затем руками берут ком замазки и прокатывают его по мелу до тех пор, пока он не наберет требуемое количество мела и перестанет прилипать к рукам.
Замазка должна быть однородной, без содержания включений – крупинок и прослоек мела и олифы.
Качество замазки проверяют следующим образом: берут ком замазки и из него образуют валик, после чего валик за оба конца берут обеими руками и растягивают его. Если при растягивании валика он разрывается не сразу, а постепенно, и в середине образуется утончающаяся шейка в месте разрыва, то качество замазки удовлетворительное, если же валик разорвется сразу, без утончения, то качество замазки неудовлетворительное и она непригодна к употреблению.
Хранят замазку в плотно закрытой таре, чтобы она не засыхала. В случае отсутствия тары ее можно хранить в полиэтиленовом мешочке.
В централизованных мастерских для изготовления замазки применяют мешалки, в которые в соответствии с рецептурой вливают соответствующее количество олифы, а затем добавляют сухой, просеянный мел небольшими дозами, после чего включают электродвигатель мешалки, в бункере лопасти перемешивают смесь до получения пластичной замазки. Замазка наносится на фальцы при температуре в помещении не ниже 15 °C. При более низкой температуре замазку подогревают до 30–40 °C в сосуде, установленном в горячую воду.
Для повышения прочности и улучшения сцепления замазки со стеклом и древесиной переплетов компоненты замазки до ее приготовления подогревают до температуры 60–70 °C. Для герметизации фальцев применяют следующие замазки.
Меловую замазку применяют для остекления деревянных переплетов. Она состоит из 2,1 части олифы и 8 частей мела.
Белильная замазка отличается высокой прочностью, ее используют для остекления окон больших размеров, например, витрин. Готовят замазку так (частей по массе): 6 мела смешивают с 2,4 сухих цинковых белил, затем вводят 1,7 олифы и перемешивают до получения замазки нужной густоты.
Железно-суриковой замазкой пользуются для остекления металлических переплетов (фонарей). Эта замазка атмосферостойка и антикоррозийна. Замазку приготавливают так (частей по массе): сначала смешивают 7 мела с 1,7 сурика, а затем в смесь вводят 1,4 олифы.
Битумную мастику используют при остеклении окон производственных зданий. Готовят замазку следующим образом. Битум марки 70/30 в количестве 3,2 части наливают в сосуд и подогревают до температуры 200 °C, после чего охлаждают до 70–80 °C. Затем смешивают 1,2 части растворителя с наполнителем – 3,6 части талька или 2,4 части портландцемента. В эту смесь постепенно вливают битум и состав перемешивают до получения однородной массы. Замазку следует хранить в герметичной таре.
При работе с замазками и при их приготовлении следует строго соблюдать правила по технике безопасности. Все материалы для замазок должны храниться в закрытой таре, в том числе мел, цемент, асбест, а жидкие материалы (олифа, растворители и др.) в герметичной таре – канистрах. Замазки следует готовить в отдельном помещении, оборудованном приточно-вытяжной вентиляцией. При работе с материалами, имеющими в своем составе пыль (мел, цемент), следует принимать меры против их распыления. Работающих надо обеспечить спецодеждой из брезента, рукавицами, респираторами и защитными очками.
При работе с огнеопасными материалами (керосином, растворителями и др.) надо с ними обращаться осторожно, стараясь их не разливать и избегать попадания на одежду работающих.
Заполнять сосуды – котлы, баки с битумом – нужно лишь на 3/4 объема. Подогревать битум необходимо в сосудах паром (с паровой рубашкой). На открытом огне подогрев горючих материалов запрещается.
Подогревать замазку можно в бачках с паровой рубашкой или в электрических бачках. Подогрев замазки на электроплитах с открытыми нагревателями, в том числе трубчатыми, запрещается. В целях пожарной безопасности курение в помещении, где готовится замазка, недопустимо.
Глава 3
ИНСТРУМЕНТЫ И ОБОРУДОВАНИЕ ДЛЯ РЕЗКИ И ХРАНЕНИЯ СТЕКЛА
1. Оборудование и инструменты для резки стекла
Для выполнения стекольных работ, в том числе для раскроя, бригады должны быть обеспечены следующими оборудованием и инструментами (рис. 164): столами для раскроя стекла, стеклорезами, линейками, угольниками, метрами, рулетками и др.
Стеклорез из твердого сплава предназначен для резки оконного стекла толщиной до 4 мм. Он состоит из барабанчика с тремя режущими роликами, насаженными на шпильки и вмонтированными в барабанчик, державки и ручки. Диаметр ролика 6,6 ± 0,6 мм, угол заточки ролика 100 ± 10°. Ролик изготовляют из металла твердого сплава марки ВКЗ, ручку – из древесины твердых пород либо из пластмассы, барабанчик у стеклореза латунный. Размер стеклореза 1382921 мм, масса 72 г. Каждым роликом можно резать до 350 погонных м стекла, без переточки. По мере затупления ролик используют для резки более толстого стекла. В случае затупления ролика его заменяют новым путем ослабления винта и поворота барабанчика на 120°, после чего ставят новый ролик в рабочее положение и закрепляют винтом.
Рис. 164. Инструменты для стекольных работ: а – кусачки торцевые; б – плоскогубцы комбинированные; в – угольник; г – стеклорез; д – стеклорез алмазный; е – стеклорез универсальный; ж – промазчик; 1 – рычаг правый; 2 – рычаг левый; 3 – ось; 4 – основание; 5 – линейка; 6 – державка; 7 – ручка; 8 – барабанчик; 9 – режущий ролик; 10 – алмаз; 11 – паз; 12 – корпус; 13 – крышка корпуса; 14 – винт с поршнем; 15 – ручка; 16 – переходной корпус; 17– мундштук
Стеклорезы алмазные предназначены для резки листового стекла при остеклении оконным и витринным стеклом. Стеклорезы оснащены природными либо синтетическими алмазами и выпускаются двух типов: тип 1 – с рабочей частью в виде четырехгранной пирамиды, тип 2 – с криволинейной режущей кромкой рабочей части. Масса природного алмаза для стеклорезов должна быть и пределах 0,02–0,16 карата.
Стеклорезы, оснащенные резцами с рабочей частью в виде четырехгранной пирамиды (тип 1), обеспечивают резку листового стекла толщиной до 7 мм с природным алмазом и до 5 мм с синтетическим алмазом. Стеклорезы, оснащенные резками с криволинейной режущей кромкой (тип 2), применяют для резки стекла до 4 мм.
На поверхности алмаза (обработанной) не должно быть трещин, сколов и выкрашиваний на расстоянии от вершины 0,3 мм для природного алмаза, 0,15 мм – синтетического алмазного порошка зернистостью 630/500 и крупнее.
Алмаз крепят в державке резца-стеклореза путем пайки серебряным припоем.
Державка в стеклорезе, молоточек, трубка – стальные, а также трубка и молоточек могут быть латунными. Ручка из пластмассы – полистирола, фенопласта. На поверхности деталей стеклореза не допускаются вмятины, раковины, заусенцы и следы коррозии.
Универсальный стеклорез предназначен для резки стекла толщиной 3–10 мм при остеклении оконным и витринным стеклом. Корпус стеклореза – державка и ось – стальные, ручка – деревянная, из древесины твердых пород. Вращающаяся обойма в стеклорезе заменена неподвижной осью, на которой расположен один ролик, что дает возможность резать стекло толщиной до 10 мм и удлиняет срок работы стеклореза. Размер стеклореза 1283515 мм. Масса 82 г.
Для облегчения работ по переноске, транспортировке стекла применяют одно-, двух– и трехтарельчатые вакуум-присосы.
Однотарельчатый вакуум-присос (рис. 165, а) предназначен для извлечения листового стекла из тары, укладки его на стол и переноски при остеклении. Вакуум-присос работает на основе создания вакуума между плоскостью иста стекла и диафрагмой путем поднятия штока, связанного с диафрагмой и кулачковым механизмом. Диафрагма представляет собой круглую шайбу, армированную износоустойчивым, эластичным полиуретаном. При создании вакуума между диафрагмой и стеклом последнее притягивается к диафрагме, и его можно переносить в нужное место.
Двухтарельчатым вакуум-присосом (рис. 165, б) извлекают стекло из тары, укладывают его на стол, а также переносят листовое стекло к месту установки.
Принцип работы двухтарельчатого вакуум-присоса аналогичен принципу работы однотарельчатого вакуум-присоса. В диафрагме имеются стальные фланцы для соединения со штоком.
Рис. 165. Вакуум-присосы: а – однотарельчатый; б – двухтарельчатый; в – трехтарельчатый; 1 – корпус; 2 – механизм кулачковый для подъема диафрагмы; 3 – рукоятка; 4, 6 – диафрагмы; 5 – ручка корпуса; 7 – устройство для разгерметизации; 8 – фланцы; 9 – рамка жесткости; 10 – эксцентриковый механизм; 11 – ручка.
Трехтарельчатый вакуум-присос (рис. 165, в) служит для захвата, подъема, переноса и установки крупноразмерных стекол и стеклоконструкций при остеклении витрин и витражей. Представляет собой конструкцию из литого алюминиевого корпуса, трех диафрагм и эксцентриковых механизмов. Работает за счет образования вакуума между диафрагмами и стеклом.
Раскраивают и режут листовое стекло на специальных столах. Для раскроя и резки стекла небольшого размера применяют стол (рис. 166, а), состоящий из каркаса, настила, обрезиненых роликов и каретки для подъема стола.
Лист стекла надвигают на стол по выступающим из настила роликам, которые после укладки стекла опускают. Затем стекло размечают и режут. На этом столе можно разрезать стекло размером 18001200 мм с максимальной массой разрезаемого стекла до 23 кг. Производительность 100 м2 в смену.
Для механизированного раскроя крупноразмерного листового стекла в цехах централизованной заготовки применяют стол, показанный на рис. 166, б. На нем можно раскраивать стекло размером до 4500350010 мм с погрешностью до 0,5 мм. Каретка с роликом поднимается пневматически. Стеклорез перемещается в продольном направлении цепью с электрическим приводом, а в поперечном направлении цепью, но с ручным приводом.
Рис. 166. Столы для раскроя стекла: а – небольшого размера оконного; б – витринного; 1 – каркас стола; 2 – настил; 3 – ролик; 4 – ручка подъема каретки; 5 – направляющая; 6 – электродвигатель с редуктором; 7 – конечный выключатель; 8 – суппорт; 9 – стойка каретки
Рис. 167. Стол для резки стекла: 1 – основание стола; 2 – деления, нанесенные на линейку; 3 – крышка стола; 4 – рейка для зажима войлока или сукна; 5 – рейсшина-линейка; 6 – войлок или сукно
На стройках в основном применяют стол, показанный на рис. 167. Крышка стола должна быть ровной и прямоугольной. Обычно крышку делают из рамки, на которую сверху наклеивают фанеру толщиной 6–8 мм либо из древесностружечной плиты толщиной 19 мм. Крышку покрывают двумя-тремя слоями мешковины, поверх которых кладут войлок или сукно. Это покрытие служит для амортизации стекла при нажиме на него во время резания. По периметру крышки сукно или войлок крепят шурупами с помощью рейки. К передней части крышки крепится линейка с нанесенными на нее делениями для определения размеров нарезаемого стекла.
Для перевозки и хранения оконного листового стекла на рабочем месте стекольщика применяется различная тара: ящик-контейнер, ящик дощатый решетчатый, пирамида.
В ящик-контейнер (рис. 168, а) упаковывают стекла площадью более 0,3 м2 разных размеров. Зазоры между стопками стекла, стенками, дном и крышкой заполняют древесной стружкой. Ящик-контейнер собирают на гвоздях из брусков, дощечек преимущественно хвойных пород.
В ящик дощатый решетчатый (рис. 168, б) упаковывают стекло площадью более 0,3 м2. Для сохранения стекла в процессе перевозки вместо древесной стружки используют амортизаторы из гофрированного картона. Элементы ящика изготовлены из древесины хвойных пород и скреплены гвоздями.
Пирамида (рис. 168, в) также служит для перевозки стекла и хранения его на рабочем месте стекольщика. Изготовлена она из металлического уголка и досок хвойных пород. Пирамида устанавливается на тележке и легко перевозится в пределах стройки.
Для выполнения стекольных работ предназначен индивидуальный набор инструментов. Он состоит из 20 предметов, расположенных в чемодане-футляре размером 550350110 мм. Масса набора 6 кг. В состав набора входят: роликовый стеклорез, гаечные ключи, ручная щетка из проволоки, столярный молоток, кусачки, складной метр, измерительная рулетка и др.
Рис. 168. Тара для хранения и транспортировки стекла: а – ящик-контейнер дощатый; б – ящик дощатый решетчатый; в – пирамида для стекла; 1 – головки; 2 – планка головки; 3 – крышка; 4 – планка боковой стенки; 5 – доска боковой стенки; 6 – брусок дна; 7 – торцовая планка; 8 – крепежная планка; 9 – вертикальная стойка; 10 – поперечная планка; 11 – амортизатор; 12 – тележка; 13 – основание; 14 – рама; 15 – прижим
2. Раскрой и резка стекла
Нарезка стекол производится по заданным размерам с разметкой и складыванием их в стеллажи. Заготовку стекол и приготовление замазок, как правило, следует производить централизованно в мастерских, при этом стекло должно поставляться на строительство по требуемым размерам комплектно с уплотнителем, герметиками, а также установочными и крепежными материалами.
Заготовленное стекло в контейнерах, скомплектованных на определенный объект – здание или секцию жилого дома, централизованно поставляется на стройку.
Раскрой стекла нужно вести рационально, чтобы как можно меньше было отходов – отрезков и боя стекла.
При раскрое стекла следует учесть, что размер стекла по ширине и длине должен быть меньше размера между внутренними гранями фальца на 4–6 мм, т. е. на каждую сторону на 2–3 мм. Это необходимо для того, чтобы стекло легко можно было вставить в переплет и, кроме того, чтобы при разбухании древесины переплета стекло не сжималось и не ломалось.
Металлические переплеты при низкой температуре воздуха сжимаются, и зазор в 2–3 мм между стеклом и фальцем также предотвратит поломку стекла.
До резки стекло должно быть очищено от пыли, грязи, не иметь пузырей, неровностей, трещин. Резать холодное и мокрое стекло нельзя, его необходимо прогреть, протереть, а потом приступать к резке стекла.
До начала раскроя стекло берут из ящика и с помощью вакуум-присоса укладывают на стол.
Режут стекло алмазным (рис. 169, а) и роликовым (рис. 169, б) стеклорезом из твердых сплавов. Алмазный стеклорез благодаря высокой прочности кристалла режет более качественно и служит дольше. Для качественной резки стекла и длительной работы алмазного стеклореза необходимо резать стекло по чистому и сухому месту, матовое и рифленое стекло – по гладкой поверхности. Влажное, грязное стекло затупляет стеклорез, поэтому место реза надо очистить сухой тряпкой. Обычно влажное, пыльное, грязное стекло протирают с двух сторон и устанавливают до резки для просушки. Резать стекло нужно по линейке, шаблону, обязательно плотно прижимая их к стеклу без сдвигов. Линейка для резки стекла должна быть ровной, строго прямолинейной и иметь толщину порядка 8–10 мм.
При резании стеклорез держат так: берут его правой рукой, большим и указательным пальцами держат за молоточек, затем стеклорез устанавливают на место реза. Стеклорез при резке устанавливают вертикально или с небольшим наклоном к плоскости резания стекла, причем усилие резания должно быть небольшим. Необходимый наклон стеклореза к плоскости стекла определяют путем опытных, пробных резов. При правильной установке стеклореза к плоскости стекла и нужном нажиме в месте надреза должен появиться ровный след на стекле в виде тонкой лнии. При резании стекла стеклорезом слышен ровный звук с небольшим специфическим потрескиванием, что говорит о том, что резание ведется качественно.
При некачественном резании, неправильной установке стеклореза и сильном нажиме вместо тонкой линии получается грубая линия – царапина с образованием стеклянной пыли, вследствие чего стекло ломается не по линии надреза. Алмазный стеклорез нужно держать так, чтобы острый угол, образующийся между алмазом и плоскостью стекла, был в направлении резания.
После образования тонкой линии надреза стекло надламывают, причем узкие полоски стекла (5–10 мм) надламывают при помощи молоточка-стеклореза (рис. 169, в), в паз которого вставляют надламываемую часть стекла. По окончании резания стекла для облегчения надлома с противоположной стороны молоточком слегка и аккуратно простукивают до получения начальной трещины, после чего отрезок надламывают. Можно также ломать узкие полоски стекла плоскогубцами, губки которых обертываются эластичным материалом (резиной).
При резании стекла со смазкой поверхности места реза керосином или скипидаром качество резки улучшается, причем не образуются сколы, стружка. Кроме того, стекло легче ломается по резу.
Ломку обрезанных концов стекла производят также о край стола (рис. 169, г), для чего стекло укладывают так, чтобы обрезаемый конец свешивался. Для облегчения надлома с нижней стороны стекло по линии надреза аккуратно простукивают до образования трещины (начальной), затем правой рукой, одетой в рукавицу, берут за свешиваемый конец, а левой прижимают к столу и производят ломку стекла, чтобы отделение отрезка шло по линии надреза.
Следует учесть, что с течением времени грани алмаза тупятся, вследствие чего нажим стеклореза на стекло при резании увеличивается. Причем нажим приходится доводить до того, что стеклорез колет тонкое стекло и им можно резать только толстое стекло.
Во избежание преждевременной порчи стеклореза в конце надреза (3–5 мм) нужно несколько снизить, усилие нажима на стеклорез, чтобы не допустить резкого схода его со стекла и повреждения режущей грани алмаза о кромку стекла. Производить повторный рез стекла по одному и тому же месту нельзя. В том случае, когда необходимо по одному и тому же месту произвести рез, нужно несколько отступить от старой линии реза примерно на 0,5–1 мм. Категорически запрещается подвергать алмазный стеклорез ударам. По окончании реза его нужно очистить от стеклянной пыли и уложить в футляр.
При затуплении одного режущего ребра стеклореза типа 1 нужно алмаз (резец) повернуть и включить в работу новое острое ребро. Для этого ослабляют стопорный винт, аккуратно вынимают из молоточка резец, поворачивают его на 90°, вставляют в прежнее место так, чтобы кристалл алмаза выступал из корпуса молоточка на 1–3 мм. После чего завертывают винт и закрепляют алмаз в рабочем положении.
Рис. 169. Приемы резания стекла по линейке: а – алмазным стеклорезом; б – роликовым стеклорезом; в – обломка отрезка стекла молоточком-стеклорезом; г – обломка стекла рукой
При резании стекла роликовым стеклорезом его надо держать перпендикулярно к плоскости стекла, причем стеклорез держат в правой руке между большим и средним пальцами или между большим, средним и безымянным, прижимая сверху указательным пальцем (см. рис. 169).
При резании роликовым стеклорезом усилие (нажим) больше, чем при работе алмазным стеклорезом. Как указывалось ранее, каждым роликом можно резать до переточки до 350 погонных м, после чего его заменяют.
При резании стеклорезом необходимо, чтобы стекло лежало плотно на столе, при резании по шаблону последний прижимают к стеклу левой рукой, а правой держат стеклорез, а при резании по линейке ее прижимают к стеклу также левой рукой.
Резку небольших стекол производят по шаблону, изготовленному из того же стекла. Длину и ширину уменьшают против требуемых размеров стекла на половину ширины оправы стеклореза. Резку стекла по стеклянному шаблону производят так: кладут шаблон на лист стекла, пользуясь гранями шаблона как линейкой. Разметку, резку стекла производят на столах.
Резание стекла можно вести путем интенсивного нагрева стекла по линии разреза, в результате чего оно лопается точно по намеченной линии.
Резка стекла электростеклорезом. Резка стекла вручную является трудоемкой работой. Более прогрессивной является резка стекла посредством электроустановки ЭРС-1.
Электроустановка (рис. 170) представляет собой металлический стол, состоящий из рамы прямоугольной формы, к нижней части которой в углах приварены муфты диаметром 22 мм, в которые на резьбе ввинчиваются ножки, изготовленные из труб. Для создания жесткости конструкции ножки связаны раскосами – связями. Поверхность стола покрыта листовой сталью толщиной 2 мм. Во избежание коробления или перекоса при нагреве электроспирали рама с рабочей стороны усилена металлическими уголками 5050 мм.
Рис. 170. Электроустановка для раскроя листового стекла типа ЭРС-1: 1 – стол; 2 – электропривод с клеммой; 3 – нихромовая спираль; 4 – рейка асбестоцементная с пазом; 5 – размерная линейка; 6 – направляющие стержни; 7 – упорная линейка; 8 – керамический изолятор; 9 – ножки; 10, 11 – связи жесткости – раскосы
На столе размещена асбестоцементная рейка, в пазу которой расположена нихромовая спираль. Концы спирали соединены с зажимами – контактами, вставленными в керамические изоляторы, на концах которых имеются пружины возврата. Во избежание касания стекла спираль должна находиться на расстоянии 0,2 мм от верхней кромки рейки.
Для раскроя стекла на требуемый размер на поверхности стола размещен шаблон, состоящий из двух стержней диаметром 12 мм и направляющих трубок, соединенных с упорной линейкой. До начала работы стекло, подлежащее раскрою, должно быть очищено от пыли, грязи, стружек и т. п. Работа на установке производится следующим образом: шаблон устанавливают на требуемый размер стекла, чтобы расстояние от упора до спирали было равно размеру стекла, и крепят его в этом положении посредством зажимов (барашек), после чего установку подключают к электросети. Когда спираль нагреется до слабого свечения, на нее накладывают раскраиваемое стекло так, чтобы оно одной гранью подошло вплотную к упорной линейке, а плоскостью легло на спираль. Вследствие резкого перепада температуры стекло точно лопается по линии нагрева, после чего установку отключают от электросети.