Столярные, плотничные, стекольные и паркетные работы: Практическое пособие Костенко Евгений
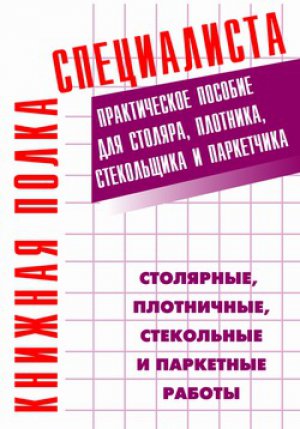
При наличии на предприятии четырехстороннего продольно-фрезерного станка с пятью ножевыми валами бруски обвязки переплетов, отливов, нательники можно изготовлять в кратных размерах по ширине, чтобы обрабатывать на станке одновременно по два бруска и, установив строгальную пилу на пятом горизонтальном валу, разрезать их.
Нащельники, отливы и раскладки по стеклу торцуют в размер на «ус» на круглопильном станке или на специальном станке для усования. Чтобы избежать образования сколов или трещин в нащельниках (при креплении шурупами), надо заранее выбирать отверстия с раззенковкой, причем диаметр отверстий должен быть меньше диаметра шурупа на величину резьбы.
Рис. 109. Приспособление для одновременного высверливания двух отверстий под нагели: 1 – рама каркаса; 2 – тележка; 3, 4 – кронштейны; 5 – направляющие стаканы; 6 – рычаг; 7 – электросверлильные машины; 8 – опорная траверса; 9 – шток; 10 – швеллер
На бруски оконных коробок пиломатериалы раскраивают на линии либо на позиционных станках, после чего их там же обрабатывают. Обработанные бруски створок, форточек и коробок проходят выборочный контроль и поступают на буферный склад, где их полностью укомплектовывают по размерам и назначению. Собирают оконные створки, форточки, фрамуги, коробки в сборочных станках (наймах) на клею, устанавливая в углах сопряжений заподлицо с плоскостью деревянные или металлические нагели, изготовленные из мягкого металла. Отверстия под нагели выбирают электросверлилкой либо специальным навесным приспособлением (рис. 109) сразу в двух-четырех углах створок. Приспобление состоит из металлической рамы, устанавливаемой на станке по сборке створок. К стойкам рамы крепят швеллеры, по которым перемещается тележка с расположенными на ней кронштейнами. К кронштейнам шарнирно прикреплен рычаг, с помощью которого тележка передвигается вперед и назад. К кронштейнам прикреплены направляющие стаканы, через которые проходят шторки, соединенные шарнирно с рычагом. На штоках расположена траверса с закрепленными на ней электросверлильными машинами. В зависимости от расстояния между высверливаемыми отверстиями электросверлилки могут перемещаться по траверсе. Оператор (рабочий) рычагом устанавливает электросверлилки в требуемое положение над створкой, затем опускает рычаг, и работающие электросверлилки выбирают отверстия.
После этого устанавливают нагели на клею в створки, фрамуги, форточки, коробки и укладывают на подстопное место для выдержки, необходимой для схватывания клея.
Перед навешиванием коробки фрамуги и створки обрабатывают по периметру для получения правильных геометрических размеров. Одновременно створки и фрамуги фальцуют для образование четвертей, необходимых для притвора.
Для сборки створок длиной до 1925 мм, шириной до 740 мм и толщиной до 60 мм применяют гидравлический сборочный станок ВГО-2, на котором их собирают.
Двери и оконные коробки длиной до 2360 мм, шириной до 1610 мм и толщиной до 180 мм собирают на сборочном станке ВГК-2.
Сборка фрамуг и форточек длиной до 460 мм, шириной до 1290 мм и толщиной до 55 мм производится на станке ВГФ.
Для сборки оконных створок больших размеров применяют станок ВГС, на котором можно собирать створки по длине до 2115 мм, ширине до 1660 мм, толщине до 55 мм.
Кроме того, оконные и дверные коробки можно собрать на станке ВГК-3, где собираются коробки длиной до 2755 мм, шириной до 2966 мм, толщиной до 174 мм.
Шаблон для фальцовки оконных переплетов (рис. 110, а) представляет собой деревянную рамку, собранную из фрезерованных брусков. Положение створок в шаблоне фиксируется упорами, а устойчивое положение – прижимами.
Шаблон для обработки дверных полотен с двух сторон (рис. 110, б) также представляет собой раму, собранную из брусков на клеевом шиповом соединении.
Шаблон для обработки оконных створок и форточек (рис. 110, в) состоит из рамки, скрепленной для большей прочности в углах металлическими угольниками. Положение створки в шаблоне фиксируют упорами. Крепятся в шаблоне створки, форточки прижимом. Обработка по периметру в этом шаблоне производится на фрезерном станке.
Рис. 110. Шаблоны: а – для фальцовки оконных переплетов; б – для обработки по периметру дверных полотен с двух сторон; в – для обработки оконных створок и форточек по периметру (в шаблоне укладывают правую и левую створки); 1 – угольник жесткости шаблона; 2 – ось вращения прижима; 3 – прижим; 4 – упоры; 5 – рамка
При обработке создают профиль, зеркальный профилю брусков створки и горбылька, поэтому при постановке на место форточка точно подходит к профилю брусков створки и горбыльков, дополнительных работ по пригонке форточки к створке не требуется. Провесы с плоскостей створок, форточек снимают на широком рейсмусовом или трехцилиндровом шлифовальном станке.
Паз под отлив выбирают на фрезерном станке, следя за чистотой обработки. Для постановки петель в створках и брусках коробок на станке с вибрационной головкой выбирают гнезда прямоугольной формы. Размеры гнезд должны соответствовать размерам петель.
Форточки в створки навешивают на рабочем столе после обработки по периметру и выборке гнезд под петли. Отлив на форточке не ставят, так как в нижнем бруске форточки отлив составляет одно целое с бруском.
Отлив и нащельники в наружной и внутренней створках ставят на рабочем месте до навешивания форточки в створку или после этого. Врезной отлив устанавливают на клею повышенной водостойкости и крепят шурупами либо шпильками; нащельник, прикрывающий щель, образуемую притвором створок, крепят к створке на клею и шурупами.
Изготовление оконных блоков со спаренными переплетами. Оконные блоки со спаренными переплетами изготовляют в основном из спецификационного пиломатериала. Технологическим процессом предусмотрено, что раскрой пиломатериалов производится на полуавтоматической линии ОК507. При отсутствии линии пиломатериалы раскраивают по длине на круглопильных станках для поперечного раскроя ЦПА-40, а по ширине – на круглопильных станках с гусеничной подачей ЦДК4-3.
Для производства деталей, оконных блоков рекомендуется использовать отходы пиломатериалов, сращивая их по длине на зубчатые соединения. Детали можно склеивать также по ширине и толщине холодным способом в сборочных станках либо на полуавтоматической линии. Поверхности, подлежащие склеиванию, предварительно профрезеровывают. Склеивают заготовки по пласти на линиях ДВ504.
Склеенные бруски коробок подвергают профильной обработке на линии ОК503, состоящей из питателя, фуговального станка, рейкоотделителя, четырехстороннего продольно-фрезерного станка. На ней можно обрабатывать бруски длиной 750–2210 мм, шириной 54–143 мм и толщиной 44–74 мм; производительность линии – 460 шт/ч.
Профильная обработка брусков створок осуществляется на линии ОК508, зарезка шипов в брусках коробок, обработка гнезд – на линии ОК505, а зарезка шипов и проушин в брусках створок и их сборка на линии ОК509. На одном шипорезном станке зарезают проушины в брусках, на другом – шипы. После зарезки на шипы клеенаносящим устройством наносится клей, после чего створки поступают в сборочный станок. На долбежном станке в вертикальных брусках выбираются гнезда для средних брусков. Собранные створки на подъемном столе собираются в стопу-пакет, а на механизированном складе они выдерживаются до полного схватывания клея. На линии можно изготовлять изделия длиной 690–2150 мм, шириной 300–1300 мм, толщиной 43–55 мм; производительность линии 125 шт/ч.
На тех предприятиях, где нет линии, оконные створки собирают в сборочных станках. В процессе сборки переплетов на станках нужно следить за тем, чтобы створки не имели перекосов, а в сопряжениях не было неплотностей. Точность сборки проверяют шаблоном с угла на угол.
Затем собранные створки обрабатывают по наружному периметру (контуру) на агрегате ОК213Р2.02, состоящем из двух станков для продольной и поперечной обработки кромок. Кромки обрабатываются фрезерными головками. В каждом станке есть узлы базирования, прижима для фиксирования створок и два подвижных суппорта. Помимо этого на станке для продольной обработки смонтирован механизм для перемещения створок.
На размер обрабатываемой створки агрегаты налаживают по заданной программе, что значительно сокращает время настройки станков. Станки агрегата закрыты шумопоглощающими кабинами. На агрегате можно обрабатывать створки длиной 345–1 395 мм, шириной 295–1070 мм, толщиной 32–42 мм.
Мощность электродвигателей – 44 кВт; производительность – 180 створок в час.
После обработки створок по наружному периметру на трехцилиндровом шлифовальном или широкопросветном рейсмусовом станке зачищают и шлифуют наружные плоскости створки, после чего ее кладут в шаблон и на фрезерном станке по периметру с трех сторон обрабатывают верхний горизонтальный брусок и два вертикальных.
После обработки по периметру во внутренних створках выбирают гнезда под врезные петли, а в наружной и внутренней – гнезда под врезную завертку и отверстия под ручку-завертку, в брусках коробки (импосте) – паз под запорную планку, а в створках и форточках гнезда под винтовую стяжку.
Для долбления гнезд, установки в них петель и замков (ручек-заверток) и закрепления их штифтами используют агрегат ОК213Р2.10. Для выборки гнезд на нем расположены долбежные головки, а для установки приборов (петель, замков) – высокопроизводительные автоматизированные агрегаты. Все работы по обработке гнезд и установка приборов ведутся автоматически.
Для настройки на нужную ширину обрабатываемой створки агрегат оборудован программным устройством. Скорость подачи бесступенчатая. На агрегате можно обрабатывать створки длиной 365–1395 мм, шириной 310–1070 мм, толщиной 42–52 мм. Скорость подачи штангового конвейера 6–30 м/мин, скорость подачи головок по выборке гнезд – 0,3–0,7 м/мин. На агрегате установлены четыре долбежные, две сверлильные головки и четыре головки по установке приборов. Агрегат обслуживают двое рабочих.
На предприятиях, где нет линий, заготовки коробок обрабатывают следующим образом: бруски, имеющие покоробленность и неровности, обрабатывают на фуговальном станке, а затем с четырех сторон с отборкой профиля – на четырехстороннем продольно-фрезерном станке.
В горизонтальных брусках коробок для двух– и трехстворчатых переплетов на центродолбежном или горизонтальном сверлильно-пазовальном станке выбирают гнезда для шипов вертикального импоста, а также пазы в импосте для постановки планки завертки замка. Зарезают шипы и проушины на шипорезных станках.
В вертикальных брусках коробки выбирают гнезда для петель, после чего на рабочем месте ставят полупетли. Имеющиеся в брусках дефекты (сучки) заделывают на станке. В нижнем горизонтальном бруске коробки для отвода воды прорезают пазы.
Оконные коробки собирают в сборочных станках ВГК-2, ВГК-3. При сборке коробок на клею шиповое соединение крепят нагелями, установленными на клею. Нагели ставят во всех углах коробки, а также в местах соединений импоста с горизонтальными брусками заподлицо с плоскостью коробки.
При сборке коробки надо следить, чтобы не было перекосов с угла на угол; правильность сборки проверяют линейкой и шаблоном. Шиповые соединения коробок должны быть плотными, без зазоров.
При сборке оконного блока навешивают створки, форточки на петли в коробку, подгоняют створки к коробке, устраняя дефекты и неточности. После сборки оконный блок окрашивают, а затем остекляют.
Технические условия на изготовление оконных блоков. Элементы оконных блоков должны иметь правильную геометрическую форму.
На лицевых поверхностях и по торцам соединений створок, фрамуг, форточек, клапанов и жалюзи провесы недопустимы.
Применять древесину разных пород в створке, коробке и т. п. нельзя. Заделка пороков и дефектов обработки пробками и планками должна производиться на клею, причем пробки и планки должны быть без пороков, одной породы с деталью и установлены плотно без зазоров, заподлицо с поверхностью.
На лицевых поверхностях деталей окон и балконных дверей под прозрачное отделочное покрытие не допускаются пороки и дефекты обработки древесины.
Непрозрачное покрытие должно выполняться масляными или синтетическими красками и эмалями.
2. Изготовление дверных блоков
Технологический процесс изготовления дверных блоков со щитовыми полотнами состоит из следующих основных операций: изготовление рамок и заполнителя, подготовка облицовочного материала, склеивание щитов двери, обработка щитов по периметру, постановка обкладок и раскладок, изготовление дверной коробки, установка (вгонка) дверей в коробку с навешиванием на петли.
Щиты дверей изготовляют, заполняя предварительно собранную рамку рейками, сотами, собранными из отрезков твердой древесноволокнистой плиты, фанеры, бумажными сотами или ломаными полосками из твердой древесноволокнистой плиты.
Для дверей толщиной 40 мм рамки изготовляют из брусков сечением 40–6032 мм, которые выпиливают по длине из пиломатериалов толщиной 40 мм, влажностью 9 ± 3 % на круглопильном станке для поперечного, а по ширине – на круглопильном станке для продольного раскроя. Соединяют их на шип или на металлические скрепки впритык. Соединение брусков на шипах повышает прочность рамки, но увеличивает расход древесины и трудоемкость изготовления рамки за счет ввода лишней операции (зарезание шипов). Скрепки ставят для того, чтобы рамка во время заполнения ее серединкой и закладки в пресс не расползалась.
Для изготовления остекленной двери используют две рамки: наружную и внутреннюю. Сечения брусков внутренней рамки должны быть такими же, как и сечения брусков наружной рамки. Полученные заготовки обрабатывают в размер по толщине на рейсмусовых или четырехсторонних продольно-фрезерных станках. Бруски рамок не должны иметь гнили, кривизны, выпадающих, загнивших, гнилых и табачных сучков.
Заполнитель изготовляют из маломерных пиломатериалов и отходов производства (для сплошных и разреженных серединок), отходов фанеры и твердой древесноволокнистой плиты толщиной 4 мм (для сотового заполнения).
Влажность отходов древесины, получаемой при раскрое пиломатериалов для столярных изделий, составляет примерно 15 %.
Перед заполнением серединки их необходимо высушить до влажности 9–10 % в сушильных камерах.
Для помещения с относительной влажностью воздуха более 60 % делают двери со сплошным заполнением деревянными рейками. После сборки рамки на нее накладывают фанеру или твердую древесноволокнистую плиту, предварительно намазанную клеем, и прикрепляют к рамке мелкими гвоздями длиной 20–25 мм. В дверях со сплошным заполнением допускается толщина облицовки из твердой древесноволокнистой плиты в 3 мм.
После закрепления облицовки рамку поворачивают и все внутреннее пространство заполняют рейками толщиной, соответствующей толщине рамки. При укладке реек надо следить за тем, чтобы они были плотно прижаты одна к другой, поверхность их была ровной, а стыки располагались вразбежку.
После заполнения рейками рамку закрывают сверху вторым облицовочным листом, предварительно намазанным клеем, и прикрепляют его мелкими гвоздями с четырех сторон. При изготовлении щита с разреженным заполнением рамку заполняют не сплошь, а с промежутками.
Щит двери с заполнением в виде сот состоит из рамки с уложенными в ней сотовыми решетками. Соты собирают из полосок фанеры или твердой древесноволокнистой плиты толщиной 4 мм, шириной 32 мм.
В полосках через 40 мм прорезают пазы шириной, равной толщине полосок плюс 1 мм, и глубиной, равной половине ширины полосок плюс 1 мм. Из полосок с прорезями набирают решетку в виде сот с ячейками размером 4040 мм. Рамку щита заполняют двумя или тремя сотами.
К внутренним дверям облицовочный материал приклеивают карбамидным клеем, а к наружным – клеем КБ-3 (водостойким).
При небольшом годовом объеме производства дверей для склеивания применяют механические прессы. Склеивание щитов в механических прессах состоит из следующих операций: формирование щита двери, образование пакетов и запрессовки их, выдержка пакета под давлением для схватывания клея, выдержка щитов дверей (акклиматизация).
Формируют щиты дверей так: на рабочий стол, расположенный около пресса, кладут заранее собранную рамку, а на нее – прирезанный лист фанеры или твердой древесноволокнистой плиты с предварительно нанесенным на одну плоскость клеем. Клей равномерно распределяют по всей плоскости листа, слой не должен быть толстым, иначе под давлением в прессе будут выжиматься излишки клея, что затруднит разборку пакетов. Облицовочный лист укладывают намазанной стороной на рамку. Его концы должны выступать за рамку равномерно со всех четырех сторон. Уложенный лист закрепляют по углам мелкими гоздями или шпильками, затем рамку переворачивают и заполняют серединку щита брусками, сотами и др. Вплотную к середине продольных брусков кладут два бруска сечением 3250–70400(700) мм, причем бруски длиной 400 мм ставят для дверей высотой 2000 мм, а длиной 700 мм – для дверей высотой 2300 мм для того, чтобы в дверь можно было врезать замок независимо от того, какой навески она будет – правой или левой, и установить ручку.
Сотовое заполнение должно заполнять все внутреннее пространство рамки, а концы полосок одних сот свободно входить в свободное пространство между концами полосок других сот.
После заполнения середины щита рамку покрывают другим облицовочным листом, предварительно смазанным клеем, и закрепляют его в углах мелкими гвоздями. Затем собранный щит снимают с рабочего стола и переносят в пресс. В пресс укладывают 18–20 щитов толщиной по 40 мм. Щиты должны быть уложены строго один над другим, без смещения; сверху их накрывают массивным трехслойным деревянным щитом, аналогичным основанию. Затем включают приводной механизм пресса и пакет сжимается. После склеивания щитов, т. е. через 6–12 ч, готовый пакет разбирают, щиты укладывают стопками для свободной выдержки в течение 12–24 ч в помещении с нормальной влажностью (до 60 %) и температурой 18–20 °C. В горячем гидравлическом прессе щиты склеивают в той же последовательности, что и в механическом, но формируют их на металлическом поддоне.
Давление при склеивании должно быть 0,5–0,8 МПа, причем меньший предел относится к щитам с сотовым и разреженным заполнением, а больший – со сплошным заполнением.
После склеивания и выдержки щиты обрабатывают по периметру, а затем устанавливают обкладки, раскладки. Обработка по периметру включает в себя опиловку щита до необходимого размера и шлифование поверхностей щита. В остекленных дверях ставят раскладки по стеклу.
Изготовляют коробку и вгоняют полотно в нее так же, как и в филенчатых (рамочных) дверях.
Линия по изготовлению дверных полотен состоит из ряда последовательно расположенных механизмов. На ленточный конвейер кладут облицовочный лист твердой древесноволокнистой плиты толщиной 4 мм, намазанный с сетчатой стороны клеем. На этот лист помещают два вертикальных бруска рамки и бруски под замок, после чего полученный пакет передают на следующую позицию, где на него кладут две поперечные планки рамки, которые по углам крепят скрепками. Затем заполняют середину либо брусками (для дверей со сплошным заполнением), либо сотами.
На следующей позиции пакет накрывают листом древесноволокнистой плиты, на сетчатую сторону которого предварительно наносят клей. В углах лист наживляют мелкими гвоздями. Собранный пакет двери цепным конвейером подается в загрузочную этажерку. После загрузки всех 15 этажей этажерки механизмом подачи пакеты полотен подаются в пресс П-797-6. Склеивание производится карбамидными клеями (КФ-Ж) в течение 6–8 мин при температуре плит пресса 115–120 °C. После склеивания пресс размыкается и включается загрузочный механизм, который загружает очередную партию полотен с этажерки в пресс и одновременно с этим частично выталкивает склеенные полотна на разгрузочную этажерку. Для полного выталкивания полотен из пресса в разгрузочную этажерку включается разгрузочный механизм, который выталкивает каждое полотно в разгрузочную этажерку, а оттуда передает на подъемный стол-накопитель, откуда полотна поступают на неприводной напольный конвейер. На этом конвейере полотна выдерживают в течение 24 ч для выравнивания напряжений.
Обработка полотен дверей по периметру происходит следующим образом: стопа склеенных дверных полотен после выдержки поступает на гидравлический подъемник с автоматическим загрузчиком, откуда каждое полотно поочередно подается на форматный концеравнитель, на котором обрабатываются сначала продольные кромки, а затем поперечные; одновременно фрезами на кромках образуется необходимый скос. При выходе из станка полотна дверей покрывают олифой со всех сторон на специальном приспособлении. После олифования через роликовый конвейер полотно поступает на станок, на котором выбираются гнезда под полупетли. Затем каждое полотно подается на подъемный стол-накопитель, где образуется стопа дверных полотен. По мере образования стоп нужной высоты они двухцепным напольным конвейером подаются к механизму выдачи, из которого каждое полотно подается к первому сверлильному станку для выборки в продольной кромке гнезда под корпус замка или защелки. На втором сверлильном станке выбирается гнездо под планку замка и отверстие под ручку замка. Обработанные полотна по роликовому конвейеру поступают для установки в коробки.
Поток по сборке дверных блоков состоит из двух линий: I – сборки и транспортирования коробок, II – сборки и транспортирования блоков.
На линии I работа проводится следующим образом. Бруски коробок, изготовленные в деревообрабатывающем цехе, поступают на тележке к двухпильному станку, на котором прорезаются гнезда под петли. На рабочем месте рабочий загоняет в прорезь полупетлю и крепит ее штифтами или шурупами, после чего бруски с шипами, смазанными клеем, собираются в коробку в сборочном станке. Собранные на клею и нагелях коробки поступают на двухцепный конвейер-накопитель, на котором происходит естественное отвердевание клея. По мере потребности с этого конвейера коробки передаются на линию по сборке блоков.
Линия II расположена под прямым углом к линии I и состоит из одноцепного напольного конвейера, перемещающего дверные полотна в вертикальном положении. Вдоль конвейера расположены рабочие места. На первых двух наживляют полупетли шурупами на полотне, на третьем рабочем месте окончательно завертывают шурупы шуруповертом, на четвертом – навешивают (вгоняют) полотна в коробку. Рабочий, занятый довертыванием шурупов, управляет педальными упорами, с помощью которых дверь устанавливают в нужном месте для выполнения рабочих операций.
Технические условия на изготовление дверей. Двери изготовляют в соответствии с ГОСТами и рабочими чертежами. Отклонения от номинальных размеров дверных блоков и сборочных единиц (полотна, коробки) должны соответствовать существующим нормативным документам.
На лицевых поверхностях полотен, коробок провесы деталей, не имеющих фасок в местах сопряжения, не допускаются. Двери повышенной влагостойкости изготовляют из древесины хвойных пород: сосны, ели, пихты, лиственницы и кедра. Применять древесину разных пород в дверном полотне или коробке не допускается, за исключением сосны, ели, пихты и кедра (под непрозрачную отделку).
Двери в основном изготовляют с непрозрачными покрытиями. Прозрачным покрытием отделывают двери, изготовленные из древесины твердых лиственных, хвойных и ценных пород, подобранной по качеству, цвету и текстуре.
Приборы одного типа и назначения устанавливают в дверях на одном уровне. Перевозят двери и окна в контейнерах (рис. 111).
Рис. 111. Контейнер для перевозки оконных и дверных блоков: 1 – рама; 2 – стойка; 3 – выдвижная штанга; 4 – прижимная балка; 5 – зажимный винт; 6 – прорезиненная лента
При хранении и транспортировании столярных изделий их следует защищать от механических повреждений, загрязнения, увлажнения и прямых солнечных лучей.
3. Изготовление столярных перегородок и тамбуров
Столярные перегородки изготовляют в виде щитов по технологии, аналогичной технологии изготовления рамочных дверей.
Щиты столярных перегородок делают шириной 600, 1200 мм, высотой от 2300 мм и более, толщиной 54, 64, 74 мм. На стройку щиты поступают в собранном виде с филенками и переплетами.
В столярных перегородках устанавливают одинарные глухие (неоткрываемые) створки, фрамуги, которые служат для освещения одного помещения от световых проемов (окон) другого.
Филенку устанавливают в пазы брусков обвязки. Если по условиям эксплуатации требуется звуконепроницаемая перегородка, то делают более утолщенную обвязку, а филенку склеивают из твердых древесноволокнистых плит, прокладывая межу ними мягкую древесноволокнистую или минераловатную плиту.
Перегородки собирают также из профильных досок толщиной 27–35 мм, шириной 64–140 мм в четверть или в паз и гребень. Доски изготовляют на предприятиях и поставляют на стройку погонажем либо в прирезанном виде.
Тамбур представляет собой деревянный каркас, к которому крепят щиты ограждений. В зависимости от нагрузок каркас тамбура делают из брусков сечением 44–5474–94 мм.
Бруски поставляют на строительство погонажем влажностью до 18 %, а на строительстве их прирезают по месту. Щиты тамбура представляют собой рамки, облицованные с обеих сторон фанерой повышенной водостойкости или сверхтвердой древесноволокнистой плитой толщиной 6 или 8 мм со сплошным заполнением в середине деревянными рейками. Высота и ширина щитов зависят от размеров тамбура, толщина должна быть не менее 40 мм.
Щиты изготовляют по технологическому процессу, аналогичному процессу производства щитовых дверей.
Для тамбуров в общественных уникальных зданиях применяют щиты, облицованные шпоном из древесины ценных пород либо отделанные бумагой, имитирующей текстуру древесины ценных пород.
4. Изготовление встроенной мебели
Встроенные шкафы, антресоли состоят из дверных и антресольных блоков, боковых и промежуточных стенок, плинтуса, наличника, монтажного бруса.
Дверные и антресольные блоки (щитовые) изготовляют по технологическому процессу, аналогичному изготовлению дверей щитовой конструкции.
Полотно двери шкафа, антресоли обкладывают в паз и гребень деревянными обкладками, поливинилхлоридным профилем или облицовывают кромочным пластиком. Крепят обкладки на клею.
При изготовлении дверей шкафов из древесностружечной плиты последнюю раскраивают на круглопильных станках, после чего на кромках на фрезерном станке выбирают паз для крепления обкладок. Обкладки крепят в сборочных станках или хомутах. После выдержки, необходимой для схватывания клея, плоскости щитов дверей шлифуют на трехцилиндровом шлифовальном станке. Двери могут быть покрыты шпоном из древесины ценных пород или оклеены поливинилхлоридной пленкой, боковую щит-стенку делают из древесностружечной плиты и облицовывают шпоном из древесины ценных пород либо покрывают поливинилхлоридной пленкой.
Промежуточную стенку изготовляют из двух твердых древесноволокнистых плит, склеенных между собой сетчатыми сторонами внутрь. После склеивания необходимо выдержать плиты в течение суток уложенными в стопы в цехе при температуре 18–20 °C и относительной влажности воздуха 60 %, после чего их опиливают по периметру, а затем кромки во избежание увлажнения покрывают (до окраски) олифой. Переставные полки длиной до 800 мм делают из фанеры, а длиной более 800 мм – из древесностружечной плиты, наружную кромку которой облицовывают деревянной обкладкой.
Раскраивают плиты, фанеру для полок на круглопильном станке, уголки выпиливают по разметке или шаблону на ленточнопильном станке. Поверхность полок шлифуют на шлифовальном станке.
Элементы шкафов, отделанные древесиной ценных пород, покрывают лаком, а неотделанные окрашивают нитроэмалью или масляной краской.
При транспортировании для предохранения от порчи элементы шкафа упаковывают попарно лицевыми поверхностями друг к другу, прокладывая между ними бумагу. Хранят элементы шкафов в горизонтальном положении в сухих складах, а перевозят в контейнерах или крытых вагонах.
На строительство шкафы поставляют комплектно с приборами, уложенными в отдельную тару.
5. Изготовление плинтусов, наличников, досок пола, поручней, обшивки
Изготовляют детали по следующему технологическому процессу: сушка древесины, раскрой пиломатериалов по длине и ширине на круглопильных станках, заделка дефектов с последующей выдержкой, необходимой для схватывания клея. Заделывают дефекты на станке для высверливания и заделки сучков, обрабатывают с четырех сторон (фрезеруют) с созданием профиля – на четырехстороннем продольно-фрезерном станке, прирезают в размер – на торцовочном станке. Затем доски пола антисептируют. Детали поставляют прирезанными длиной 2100 мм и более.
Глава 2
СТОЛЯРНО-МОНТАЖНЫЕ РАБОТЫ НА СТРОИТЕЛЬСТВЕ
1. Общие сведения о монтаже и монтажном оборудовании
Монтаж деревянных конструкций ведется различными способами: отдельными элементами, частями или сборочными единицами конструкций. Способ монтажа столярных изделий зависит от размера устанавливаемых изделий и методов их подъема.
Монтаж деревянных конструкций рекомендуется вести укрупненными элементами или блоками, собираемыми на предприятиях или строительных площадках.
При монтаже деревянных конструкций весь процесс расчленяют на отдельные этапы, состоящие из подготовительных работ, сборки и установки конструкций в проектное положение.
Подготовительные работы предусматривают проверку: правильности размеров проемов, в которые монтируют конструкции; прочности и устойчивости монтируемых деревянных конструкций; рабочего состояния инструмента и механизмов для подъема, подмостей, сигнализации.
До установки на место деревянные конструкции следует тщательно выверить, а также проверить, все ли сделано по защите их от увлажнения, поражения грибами.
Места строповки изделий отмечают краской. Проверяют точность сборки конструкций, соответствие ее рабочим чертежам, а также допущенные отклонения. Необходимо тщательно проверить места установки конструкций, устранить имеющиеся неровности или отклонения.
Установка конструкций на место заключается в строповке, подъеме и установке в проектное положение, выверке и окончательном их закреплении.
Деревянные конструкции монтируют по заранее утвержденным технологическим картам, а если они отсутствуют – по утвержденной схеме.
Для монтажа деревянных конструкций применяют монтажное оборудование – краны, лебедки, блоки, тали и различные монтажные приспособления – стропы, траверсы, захваты. Указанные машины и приспособления используют также для погрузочно-разгрузочных работ.
Краны. В строительстве широко используют поворотные краны, представляющие собой подъемно-транспортные машины, с помощью которых можно производить подъем, горизонтальное и наклонное перемещения грузов, а также поворачивать их вокруг вертикальной оси колонны (башни) крана.
Для монтажа строительных конструкций применяют самоходные стреловые краны – пневмоколесные, гусеничные, автомобильные и др. Эти краны имеют большую подвижность, на их установку и передвижение не требуется рельсовых путей.
Лебедки. Различают лебедки специальные и общего назначения. Специальные лебедки используют в кранах для подъема и опускания грузов (грузовые) и для изменения положения стрелы (стреловые). По способу установки различают стационарные и передвижные лебедки. Лебедки общего назначения бывают с ручным и механическим приводом (от электродвигателя или от двигателя внутреннего сгорания).
Лебедки с ручным приводом используют для монтажных работ с малой скоростью перемещения грузов, а также для оттягивания грузов при их подъеме. Лебедки с механическим приводом подразделяют на редукторные, реверсивные и фрикционные.
Стальные канаты используют для подъема, опускания и перемещения грузов, изготовления стропов, вантов, оттяжек. Ими оборудуют грузоподъемные механизмы – краны, лебедки, полиспасты, тали и т. д.
Рис. 112. Стропы для строительства: а – одноветвевые 1СК; б – двухветвевые 2СК; в – трехветвевые 3СК; г – четырехветвевые 4СК; д – кольцевые СКК; е – двухпетлевые СКП; ж – схема строповки двумя стропами СКК; з – схема строповки грузов двумя стропами СКП; 1 – разъемное звено; 2 – уравнительное звено; 3 – уравнительная нить; 4 – канатная ветвь; 5 – захват
В процессе эксплуатации нужно постоянно следить за состоянием канатов.
Стропы. Для строповки строительных грузов, панелей перекрытий, стен, балк, ферм, оконных и дверных блоков применяют стропы грузовые канатные. Выпускаются стропы (рис. 112) с прямолинейными ветвями для подъема и транспортирования с монтажными петлями одноветвевые – 1СК, двухветвевые – 2СК, трехветвевые – 3СК и четырехветвевые – 4СК. Помимо этого имеются стропы без монтажных петель кольцевые – СКК и двухпетлевые – СКП. Грузоподъемность стропов с прямолинейными ветвями, кольцевых и двухпетлевых 0,32–32 т.
Канатные ветви стропов изготовляют из целого каната без сращивания.
При строповке грузов надо правильно подобрать строп и надежно прикрепить его к грузу. Строп не должен иметь крутых изгибов, петель или перекручиваний.
Для захвата конструкций, которые надо строповать в двух точках и более, применяют траверсы, представляющие собой обычную балку, изготовленную из труб с подвесками. Такелажные приспособления в виде траверс, стропов, захватов крепят к рабочим органам грузоподъемных машин кольцами, крюками, петлями.
2. Сборка оконных и дверных блоков на строительстве
На строительную площадку оконные и дверные блоки поступают большей частью заранее собранными, с навешенными на петли створками, форточками, фрамугами, полотнами. Лишь в отдельных случаях на строительстве собирают оконные и балконные блоки из элементов. В проектное положение оконные и балконные блоки, как правило, устанавливают в виде готовых блоков с навешенными элементами.
Сборка оконных блоков. Работы по сборке оконных блоков состоят из подгонки и навески форточки в створку (рис. 113, а), подгонки с прифальцовкой створок между собой и к коробке с установкой нащельников (штапиков) (рис. 113, б), установки полупетель на створках и коробке (рис. 113, в), установки отлива (рис. 113, г), навешивания створки в коробку (рис. 113, д). После этого прирезают приборы (завертки, ручки-скобы). До установки в проем оконный и балконный блоки олифят и окрашивают.
Элементы оконных блоков собирают на месте. После сборки элементы блока выдерживают в течение 1–3 ч для схватывания клея, а затем устанавливают петли, отлив, нащельник и т. д. Гнезда под петли размечают с помощью шаблона Павлихина. Для образования гнезд под врезные петли можно использовать набор из трех стамесок (рис. 114). Одну карту врезной петли вколачивают в брусок коробки, а другую – в брусок обвязки внутреннего переплета. В отличие от обычных врезные петли крепят шпильками.
Навешивают створки на специальных столах.
Прифальцовка створок заключается в том, чтобы в месте створа отобрать фальцы, образующие притвор. Прифальцовка может быть выполнена механизированным или ручным инструментом. Для пристрожки притвора в окнах без съема их с петель используют доборный рубанок (рис. 115). При подгонке створок тщательно проверяют правильность притвора, т. е. плотность прилегания их к четвертям коробки. Во всех притворах между створками и коробкой оставляют зазор 2–4 мм для последующего покрытия створок слоем краски и свободного открывания и закрывания створок.
Рис. 113. Последовательность сборки оконных блоков с раздельными переплетами: а – вгонка форточки; б – подгонка створок с установкой нательника; в – установка полупетель; г – установка отлива; д – навешивание створок в коробку, установка раскладок по стеклу; 1 – створка; 2 – форточка; 3 – коробка
Рис. 114. Стамески для выборки гнезд под врезные петли: а – шириной 44 мм; б – шириной 30 мм; в – шириной 32 мм; 1 – ручка; 2 – лезвие
Рис. 115. Доборный рубанок: 1 – нож; 2 – упор ножа; 3 – крепежный болт; 4 – корпус рубанка; 5 – гайка
Затем створки навешивают на петли, следя за тем, чтобы они свободно и плавно открывались, не пружинили и были неподвижны в любом положении после открывания.
Места постановки прибора размечают с помощью шаблонов. Простейший шаблон – тонкая доска или фанера с вырезанными контурами приборов, по которым делают разметку карандашом. Размечать места для постановки приборов можно, очерчивая по контуру карандашом сами приборы. Гнезда под приборы выбирают долотом или стамеской так, чтобы глубина их по всему контуру прибора была одинаковой. Приборы врезают заподлицо с поверхностью древесины. Допускаемое отклонение должно быть не более 0,5 мм. Оконные и дверные приборы крепят к изделиям шурупами с потайной головкой. Размеры шурупов должны соответствовать размерам отверстий в приборах. Примерный порядок установки приборов на окнах и балконных дверях приведен на рис. 116.
Рис. 116. Порядок установки приборов в столярных изделиях: а – оконные блоки ОС18-18В; ОР18-18В; б – оконные блоки ОС12-1, ОСП5, ОС12-13,5; в – балконные двери БС28-9, БР28-9; г – оконные блоки ОС18-13,5; ОР18-13,5; 1, 3 – петли; 2 – фрамужный прибор; 4 – упор; 5 – фиксатор; 6 – завертка; 7 – стяжка.
Для запирания окон со спаренными переплетами применяют оконную завертку-стяжку врезную ЗР1, завертку врезную ЗР2. Обычно на каждую створку ставят по две завертки на расстоянии, обеспечивающем равномерное примыкание створки к коробке, и с учетом возможности открывания переплетов с пола без применения подставки.
Для створок окон высотой до 1100 мм со спаренными или раздельными переплетами используют накладной шпингалет ШН2, а для створок окон высотой более 1100 мм и балконных дверей со спаренными или раздельными переплетами или полотнами – накладной шпингалет ШН1. Задвижку накладную ЗТ применяют для запирания створок окон жилых и общественных зданий.
В окнах с раздельными переплетами для жилых и общественных зданий для открывания створок применяют ручки-скобы типа PC. Эти же ручки можно использовать и в балконных дверях. Створки окон фиксируют фиксаторами (рис. 117).
Рис. 117. Фиксатор типа ФК1 (а) и его установка (б)
Для запирания одного из полотен двупольных балконных дверей с раздельными полотнами применяют шпингалеты типа ШВ. Подвижные части их должны открываться плавно, без больших усилий. Дверные (верхние) шпингалеты устанавливают на высоте 1,8–1,9 м, чтобы их можно было открывать с пола. Для ограничения открывания створок и предотвращения их удара о стену с внутренней стороны наружной створки блока с раздельными переплетами устанавливают оконный упор типа УО. Для фрамуг общественных зданий со спаренными и раздельными переплетами шириной до 1300 мм используют фрамужный прибор ПФ1, а для фрамуг шириной до 830 мм – прибор ПФ2.
В изделиях из древесины, вызывающей коррозию (дуб и т. д.), следует применять шурупы с антикоррозийным покрытием.
Сборка дверных блоков. Работы по сборке дверных блоков состоят из сборки коробки, отборки фальцев полотен по створу, подгонки двери к коробке, врезке петель, замка и других приборов, установки нащельников, навешивания полотен, олифования и окраски. Коробки собирают в сборочном станке (вайме).
Полотно однопольной двери нужно тщательно подогнать к четвертям коробки. При работе вручную сначала подгоняют кромку одного вертикального бруска, второго и затем горизонтального бруска.
У двупольных дверей сначала отбирают фальц по стволу полотен и после подгонки полотен складывают их таким образом, чтобы горизонтальные бруски (рамочных дверей) совпадали, т. е. находились на одном уровне. Затем подгоняют оба полотна, они должны плотно прилегать к четвертям коробки по всему периметру, не выступая за плоскость бруска коробки и не западая. Навешивают полотно на две или три петли, причем бауты верхней и нижней петель должны быть на одной вертикальной оси. Отверстия под замки в дверных полотнах выбирают при помощи кондуктора (рис. 118), и также можно выбирать гнезда и на навешенных дверных полотнах. Выбирают гнезда под замки в дверях следующим образом. Открывают дверь примерно под углом 75° и закрепляют ее в этом положении, установив два клина под нижнюю часть полотна. Затем размечают место установки кондуктора. Кондуктор устанавливают по разметке и винтами закрепляют на двери.
Рис. 118. Кондуктор для выборки отверстий под замок в дверях: 1 – зажимные пинты; 2 – дверь; 3 – рейка; 4 – гвозди
Фиксировать положение кондуктора можно рейкой, прибиваемой гвоздями к кромке полотна сверху. Размер рейки по длине должен соответствовать положению замка от верха двери.
Отверстия в двери по кондуктору выбирают электросверлилкой. Вначале выбирают отверстие для ручки, отверстия и паз для ключевины, затем – паз для замка.
Для закрывания входных дверей в квартире, а также отдельных помещений общественных зданий применяют врезной цилиндровый и замок с засовом ЗВ1 (рис. 119, а).
Замки вставляют в вертикальные бруски. При установке замков с ручками необходимо, чтобы ось ручки совпадала с осью ключевины. Планки замков и личинки врезают заподлицо с поверхностью брусков обвязки и коробки.
Для закрывания шкафов применяют запоры (рис. 119, б, в), а для открывания комнатных глухих и остекленных дверей – ручку-скобу (рис. 119, г). Крепят скобу к двери на расстоянии 950–1000 мм от пола. На дверях ванн, санузлов устанавливают ручки-кнопки (рис. 119, д). В дверях, которые не запираются, применяют простые защелки и ручки-кнопки. Для защиты от проникновения кухонных запахов в комнаты в дверь кухонь устанавливают врезные защелки.
Рис. 119. Приборы для столярных изделий: а – замок врезной для дверей цилиндровый с засовом ЗВ1; б, в – запоры для шкафов; г – ручки-скобы типа PC; д – ручка-кнопка РК-2; 1 – запорная скоба; 2 – ручка шпингалета
При установке окрашенных оконных и дверных блоков в проемы на поверхности появляются заколы и другие дефекты, которые зашпаклевывают и окрашивают.
3. Монтаж оконных и дверных блоков
При возведении крупноблочных, кирпичных и деревянных бревенчатых, брусчатых и каркасных зданий оконные и дверные блоки устанавливают в основном в процессе возведения стен. Блоки подают к месту установки подъемными механизмами.
До установки в проем поверхности оконных и наружных дверных блоков, примыкают к каменным стенам, их антисептируют и защищают рулонными гидроизоляционными материалами (толем, рубероидом). При антисептировании оконных и дверных коробок по периметру на строительстве их обрабатывают антисептическими пастами с помощью гидро– или краскопультов. Пасту следует наносить равномерным слоем без пропусков. При температуре окружающего воздуха ниже 0 °C пасту подогревают до температуры 30–40 °C.
После нанесения пасты и высыхания ее по периметру к коробке мелкими гвоздями крепят полосы рубероида, толя шириной, равной или несколько большей ширины коробки. Створки или полотно двери до подъема блока в проектное положение следует закрепить, чтобы в промонтажные крюки (при штучном подъеме). Поднимают блоки двухветвевым стропом. На некоторых стройках блоки комплектуют на квартиру и поднимают краном в контейнере.
Для направления блока в проектное положение используют тонкий стальной или пеньковый канат, который временно крепят к вертикальному бруску коробки. Блок необходимо поднимать осторожно, без рывков, а опускать к месту установки плавно. Повороты стрелы не должны быть резкими. После установки оконную коробку выверяют по горизонтали и вертикали уровнем и отвесом (рис. 120). Оси оконных и дверных блоков должны совпадать с осями проемов. Совпадение осей блоков и проемов проверяют отвесом по отметке оси проема, сделанной на верхнем его откосе, причем шнур должен пройти точно через точку пересечения диагоналей коробки блока. Перекосы блока устраняют с помощью клиньев.
Оконный блок ставят в проем свободно, после чего его выверяют и заклинивают клиньями в проектном положении. Усилия заклинивания должны действовать только на торцы коробки. При этом нельзя допускать перекосов коробки, иначе створки, полотна будут плохо открываться и закрываться. До монтажа необходимо проверить, хорошо ли открываются и закрываются форточки, створки, фрамуги, дверные полотна. Зазоры после установки между створками, полотнами и коробками не должны превышать 2 мм, между внутренними дверями и полом – 5–8 мм, между дверями и полом в санузлах – 12 мм.
Рис. 120. Проверка правильности установки оконной коробки в проем: 1 – железобетонная перемычка; 2 – клинья; 3 – оконная коробка; 4 – зазор для конопатки; 5 – отвес
При монтаже оконных и дверных блоков все одноименные элементы располагают на одной линии, например, на фасаде многоэтажного здания вертикальные бруски переплетов должны находиться на одной вертикальной линии.
При установке дверного блока в проем его выравнивают по уровню и отвесу как в плоскости стены, так и поперек, чтобы коробка блока не выступала за плоскость стены, если стены не штукатурятся. При оштукатуренных стенах коробка должна выступать за плоскость стены на толщину штукатурки, чтобы наличник прилегал к стене и коробке.
Перед креплением блока проверяют, не перекошена ли коробка. Для этого блок измеряют по диагоналям, натягивая шнур из одного угла в противоположный. Перекос коробки можно проверить также угольником с отвесом.
Коробки, устанавливаемые в проемы наружных стен, должны отстоять от плоскости стены внутрь здания по всему его фасаду на одинаковом расстоянии.
Коробки оконных и дверных блоков к каменным стенам и перегородкам крепят шурупами или стальными ершами, которые забивают в деревянные антисептированные пробки, заложенные в стены. Вертикальные бруски коробок прикрепляют к проемам не менее чем в двух местах, причем расстояние между шурупами и ершами должно быть не более 1 м. С деревянными перегородками коробки соединяются гвоздями.
После установки в проем и закрепления блоков зазоры между коробкой и кладкой наружных стен необходимо проконопатить теплоизоляционными материалами. Конопатят стальными конопатками. В жилых зданиях оконный и балконный блоки обычно устанавливают в общий проем. Для лучшего крепления блоков желательно в верхней части проема (откоса) в местах стыка блоков ставить дополнительную пробку или металлический закладной элемент.
Оконный и балконные блоки скрепляют между собой гвоздями, прокладывая между блоками рейку толщиной 10–20 мм на половину ширины коробки, чтобы оставшийся зазор можно было в дальнейшем проконопатить.
Для герметизации окон и балконных дверей, а также стыков в наружных панелях в домах повышенной этажности применяют мастику герметик из полиизобутиленстирола. Мастика хорошо скрепляется с поверхностью древесины и бетона; при положительной температуре воздуха мастику можно применять без предварительного подогрева.
Дверные блоки в проемы кирпичных стен устанавливают с помощью крана. Вертикальные бруски дверной коробки крепят ершами, забиваемыми в деревянные антисептированные пробки, уложенные при кладке стен.
В блочных и панельных зданиях коробка крепится в закладные деревянные антисептированные пробки размером 5080120 мм. На отдельных строительствах дверные блоки устанавливают в процессе кладки стен. Для лучшего крепления коробок к кладке по высоте к вертикальным брускам прибивают отрезки проволоки, которые затем закладывают в швы и заделывают раствором.
При установке дверных коробок в стенах (рис. 121, а, б) нужно следить за тем, чтобы коробка не была перекошена. При установке дверных блоков в перегородках (рис. 121, в) желательно, чтобы они не выступали из плоскости перегородки. Ввиду того, что перегородки имеют толщину около 80 мм, для установки в проем применяют коробки шириной 74 мм.
В стенах деревянных домов (рубленых, брусчатых) в проемах на бревнах, брусьях нарезают гребень, после устанавливают коробку, которая в наружной стороне имеет паз, входящий в гребень. Зазор, образующийся между коробкой и стеной, конопатят снаружи и изнутри помещения.
Рис. 121. Примеры установки дверных блоков во внутренних стенах и перегородках: а – в кирпичных стенах; б – стеновых панелях; в – в перегородках; 1 – вариант со штукатуркой; 2 – наличник; 3 – рейка
Рис. 122. Установка оконных блоков в проемы каменных стен жилых и общественных зданий: а – со спаренными переплетами; б – с раздельными переплетами; 1 – наличник; 2 – пробка деревянная; 3 – ерш; 4 – конопатка; 5 – герметизирующий материал
Установка оконных блоков в проемы каменных стен жилых и общественных зданий показана на рис. 122. Оконные блоки с раздельными переплетами можно устанавливать сразу целиком или раздельно: сначала наружный блок, а затем – внутренний. Надо следить за тем, чтобы между наружной и внутренней коробками не было зазоров, т. е. они должны быть плотно пригнаны одна к другой и прочно скреплены гвоздями.
Порядок установки дверных коробок в стандартных домах каркасной конструкции показан на рис. 123. В наружной стене (рис. 123, а, б) коробка примыкает почти вплотную к стойкам каркаса. После закрепления и проконопачивания зазоров коробку закрывают с обеих сторон обкладкой.
В перегородках (рис. 123, в, г) коробку после установки отделывают наличником или наличником и обкладкой.
Установка коробки к печи показана на рис. 123, д. Коробку при установке изолируют от печи огнестойким материалом.
Рис. 123. Установка дверных коробок в деревянных домах каркасной конструкции: а, б – в наружной стене; в, г – в перегородках; д – примыкание к печи; 1 – брусок дверной коробки; 2 – листы гипсовые обшивочные; 3 – плотная бумага (воздухоизолятор); 4 – разреженная деревянная обшивка; 5 – рама каркаса; 6 – деревянная обкладка; 7 – войлок, смоченный в глине; 8 – наличник; 9 – твердая древесноволокнистая плита; 10 – минеральный войлок (утеплитель); 11 – битуминизированная бумага (пароизолятор); 12 – мягкая древесноволокнистая плита; 13 – наружная обшивка
После крепления коробки к стене полотно двери снимают с петель, чтобы не повредить его во время отделочных (штукатурных) работ. Концы вертикальных брусков коробки заделывают в пол на проектную глубину. Зазор, образуемый между коробкой и стеной проема, конопатят, а откосы штукатурят.
После выполнения отделочных работ полотно двери вновь навешивают на коробку, проверяя пригонку ее к четвертям коробки.
Притворы окон балконных и наружных дверей уплотняют эластичными прокладками, закрепляемыми после окраски и остекления блоков.
Воздухонепроницаемость оконных и балконных блоков, особенно со спаренными переплетами и полотнами, можно предотвратить, применяя приборы, обеспечивающие их натяжение.
Для плотного прилегания к стенам или перегородкам наличники крепят с напуском не менее 10 мм. Правильность установки наличников проверяют отвесом, уровнем и угольником. Крепят их к коробке гвоздями со слегка втопленными шляпками. В углах их соединяют на «ус». Наличники из древесины ценных пород (дуб, красное дерево, палисандр и др.) крепят шурупами. Наличники, установленные в одном помещении, должны иметь одинаковый профиль. Оконные и дверные блоки остекляют после их окрашивания.
Деревянные подоконные доски устанавливают преимущественно в деревянных домах, но делают их и в каменных зданиях после осадки и выполнения штукатурных и санитарно-технических работ.
В одном помещении подоконные доски должны находиться на одном уровне. Нижняя поверхность подоконных досок, примыкающая к каменным поверхностям, должна быть антисептирована и изолирована от кладки стен войлоком. Во избежание задержания влаги верхняя поверхность подоконных досок должна иметь уклон внутрь помещения на 1 %. В каменных зданиях торцы досок, заделываемых в стены, антисептируют и изолируют от кладки толем, рубероидом или другим гидроизоляционным материалом. Длина торцов подоконных досок, заделываемых в стены, составляет около 40 мм.
4. Монтаж столярных перегородок
Перегородки устанавливают после настила полов, санитарно-технических и электротехнических работ, оштукатуривания стен и остекления окон.
Столярные перегородки из готовых щитов рамочной (филенчатой) конструкции устанавливают на дощатую прокладку, уложенную непосредственно на пол.
Перегородка может быть равна высоте помещения или несколько ниже. Перед установкой щиты должны иметь ровные кромки, т. е. должны быть хорошо прифугованы. Щиты соединяют на вставных шипах и шурупах, завертываемых под углом к месту соединения. Число шипов зависит от высоты перегородки: меньше трех шипов не ставят. Места соединения щитов закрывают раскладками, прикрепляемыми к щитам шурупами или мелкими гвоздями с утоплением шляпки.
К полу перегородки крепят шурупами, а к стенам – закрепами. Места соединения перегородок со стенами и полом закрывают плинтусом. Если перегородка доходит до потолка, ее обкладывают фигурным карнизом.
Перегородки, изготовленные из древесины ценных пород, после установки покрывают лаком, а из хвойной древесины – окрашивают масляными или эмалевыми красками. При установке перегородок следят за тем, чтобы они имели вертикальное положение. Вертикальность установки перегородок проверяют отвесом. Отклонение от вертикали не должно превышать 3 мм на 1 м, а на всю высоту помещения – не более 10 мм.
Перегородки из гладких щитов устанавливают аналогично. Каркасную перегородку собирают из изготовленных на заводе брусков в горизонтальном положении на полу у места установки, а затем поднимают в вертикальное положение и крепят к полу гвоздями, а к стенам – ершами или гвоздями, после чего облицовывают с обеих сторон фанерой, покрытой шпоном из древесины ценных пород, окрашенными древесноволокнистыми плитами или плитами с рисунком, имитирующим древесину ценных пород. Если по условиям эксплуатации перегородка должна быть звуконепроницаема, внутри каркаса кладут один или два слоя мягких древесноволокнистых или минераловатных плит. После сборки и установки отвесом проверяют вертикальность перегородки. При креплении перегородки к каменным стенам в них заранее устанавливают антисептированные деревянные пробки. Плиты или фанера, предназначенные для облицовки перегородки, должны иметь ровную поверхность без впадин и выпуклостей. Плиту, фанеру крепят к каркасу гвоздями. Стыки смежных плит перекрывают профильными раскладками.
5. Монтаж панелей, тамбуров. Установка профильных деталей
Панели (отделочные) устанавливают в помещениях, в которых выполнены санитарно-технические и штукатурные работы, а также высушены стены.
До установки панелей на стенах размечают места установки брусков каркаса, исходя из размеров щитов, а также помещения. Каркас (бруски) крепят шурупами или ершами к установленным в стенах антисептированным деревянным пробкам. Каркас состоит из брусков сечением 2580 мм. Шаг расположения брусков зависит от размера панели (ширины). Влажность досок каркаса должна быть не более 15 %.
Панели могут собираться на рейку, в паз и гребень и в четверть. Собранный каркас должен быть строго выверен по вертикали.
Панели устанавливают на пол. Облицовку стен панелями начинают с угла помещения, прижимая к каркасу панель и проверяя при этом вертикальность боковых граней, а затем ее прибивают к брускам каркаса гвоздями длиной 40 мм с шагом 300–400 мм. Гвозди сначала наживляют под углом в паз, а затем молотком добивают и добойником утапливают шляпки. Затем в паз вгоняют шпонку (рейку) (рис. 124, а) и устанавливают следующую панель. При креплении панелей в паз и гребень (рис. 124, б) первую панель устанавливают и крепят так же, как описано ранее. Вторую панель устанавливают вплотную к каркасу и загоняют гребень в паз ударом молотка, а с другой стороны паза крепят ее гвоздями к каркасу. Панели плотно подгоняют друг к другу.
Крепят панели раскладками так, как показано на рис. 124, в. Прикрепляют их гвоздями к каркасу строго вертикально, оставляя небольшой зазор, а после проверки вертикальности в шов вставляют раскладки и крепят их к панелям гвоздями или шурупами. Щиты в местах соединений должны быть тщатльно подогнаны один к другому. Стыки (соединения) щитов перекрывают раскладками – нащельниками. Сверху панель отделывают карнизом, которым закрывают зазор между панелью и стеной. Карниз крепят шурупами или шпильками к брускам каркаса. Снизу панель отделывают плинтусом.
Тамбуры в основном монтируют из готовых панелей-щитов. До начала монтажа надо разметить места установки элементов тамбура. Монтаж панелей обычно начинают с установки одной из боковых стен, затем дверного блока и второй стены, панелей потолка.
При большой высоте тамбура и навешивании массивных дверей сооружают каркас, к которому затем крепят панели-щиты боковых стен, потолка и дверной блок. Каркас тамбура или щиты (без установки каркаса) крепят к стенам закрепами или угольниками.
Панели-щиты, дверной блок выверяют по вертикали и фиксируют, а затем крепят. Между собой панели крепят шурупами или металлическими креплениями, дверной блок со щитами – также шурупами.
Полы тамбуров устраивают после монтажа стен. Зазоры между стенами и щитами-панелями закрывают раскладками.
Рис. 124. Схема установки панелей: а – крепление рейкой; б – крепление в паз и гребень; в – крепление в четверть с раскладкой; 1 – шпонка-рейка; 2 – гвозди для крепления панелей к каркасу; 3 – стена; 4 – гвозди для крепления брусков каркаса к пробкам; 5 – брусок каркаса; 6 – панель; 7 – раскладка