Столярные, плотничные, стекольные и паркетные работы: Практическое пособие Костенко Евгений
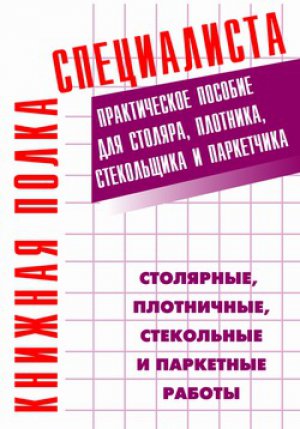
Рис. 39. Работа стамеской: а – зачистка подрезанных мест; б – поперечная подрезка; в – подрезка вдоль волокон; г – снятие долевой фаски; д – снятие фаски с торца; е – зачистка торца; ж – резание из-под плеча
Во избежание получения травмы при работе стамеской нельзя резать в направлении поддерживающей руки на себя, на весу, с упором детали на грудь и в том случае, когда деталь лежит на коленях. Оставлять долота и стамески лезвием к себе или на краю стола или верстака нельзя, так как при падении инструмента можно получить травму. Заточка долот и стамесок производится на точильных станках, правка – оселком.
Механическое долбление. Электродолбежниками выбирают гнезда прямоугольной формы, пазы и т. п. Режущий инструмент электродолбежников – непрерывная долбежная цепь, представляющая собой набор звеньев (резцов), связанных шарнирно.
Ручной электрический долбежник ИЭ-5601А (рис. 40) имеет встроенный асинхронный с короткозамкнутым ротором электродвигатель, в котором на конце вала ротора насажена ведущая звездочка, приводящая в движение режущую цепь, натянутую на направляющую линейку. Глубину долбления регулируют ограничителем хода. Головка с цепью перемещается по направляющим колонкам, установленным на основании. Цепь натягивается за счет перемещения с помощью упорного винта и линейки. Опускается головка при нажатии на рычажное приспособление – рукоятку, а поднимается автоматически цилиндрическими пружинами.
Рис. 40. Электродолбежник: 1 – цепь; 2 – направляющая колонка с пружиной; 3 – щит; 4 – электродвигатель; 5 – кожух; 6 – рычажное приспособление (рукоятка); 7 – винт; 8 – направляющая линейка; 9 – основание
В зависимости от размера выбираемых отверстий устанавливают линейки и цепи нужного размера. Ширина паза, получаемого за один проход, равна ширине цепи, а длина паза – сумме ширины направляющей линейки и двойной ширины цепи.
Для выборки пазов разных размеров требуется набор цепей и линеек. При выработке ряда последовательных гнезд по прямой линии можно образовать паз требуемой длины. Глубину выбираемого отверстия регулируют ограничителем хода, устанавливаемым на нужный размер. При опускании головки он упирается в основание.
Перед началом работы необходимо хорошо заточить цепь, затем надеть ее на звездочку электродолбежника. Электродолбежник устанавливают так, чтобы цепь находилась над гнездом, которое выбирают. Обрабатываемый материал или деталь кладут на стол и прочно закрепляют. Запрещается работать электродолбежником, если деталь не закреплена или находится на весу.
После включения электродвигателя нажатием на рычажное приспособление (ручку) электродолбежник опускают вместе с линейкой и натянутой на нее цепью вниз. Опускать цепь нужно ровно, без толчков, чтобы она внедрялась в древесину постепенно. Скорость подачи цепи зависит от размеров выбираемых гнезд, твердости обрабатываемой древесины. При выходе цепи из гнезда надо следить за тем, чтобы на кромках не было заколов, вырывов, которые получаются при быстром вынимании цепи из гнезда. Трущиеся части электродолбежника должны быть покрыты смазочным материалом.
По окончании работы цепь, звездочку и направляющую линейку промывают в керосине и смазывают машинным маслом.
Электродолбежник можно использовать как стационарный станок, прикрепив его к столу так, чтобы направляющая линейка с цепью была перпендикулярна плоскости стола, а плоскость линейки – параллельна кромке стола.
Если при работе корпус электродолбежника сильно нагревается, необходимо ослабить нажим и разгрузить электродвигатель, сменить тупую цепь или ослабить натяжение цепи. Если цепь бьет, необходимо ее натянуть. В том случае, когда цепь или линейка сильно нагреваются, нужно отрегулировать натяжение цепи, устранить возможные перекосы линейки. Если при долблении получается мелкая стружка в виде щепы, устанавливают новую цепь. Если гнездо, паз в процессе долбления получаются косыми, надо выверить и укрепить отходящую в сторону линейку. Размеры гнезд после долбления проверяют измерительным инструментом.
При работе электроинструментом нужно пользоваться защитными очками. Корпус электродолбежника должен быть заземлен.
Кроме этого, на линиях используются долбежные станки с применением гнездовых долбежных фрез для долбления прямоугольных гнезд.
Ручное сверление древесины. Круглые цилиндрические отверстия для круглых шипов, нагелей, болтов выбирают сверлами, состоящими из хвостовика, стержня, режущей части и элементов для отвода стружки. Для сверления применяют перовые, центровые, винтовые, спиральные сверла.
Перовые сверла (рис. 41, а) имеют желобочную форму: ими выбирают отверстия преимущественно под нагели. Желобок служит и для выброса стружки. Ввиду того, что он не может полностью выбрасывать стружку наружу, во избежание перегрева его приходится часто вынимать из отверстия. Поэтому отверстия получаются нечистыми и недостаточно точными. Сверла бывают длиной 100–170 мм, диаметром 3– 16 мм с градацией 1–2 мм.
Центровыми сверлами (рис. 41, б) сверлят сквозные и неглубокие отверстия поперек волокон. Сверлить глубокие отверстия этими сверлами трудно вследствие плохого выбрасывания стружки. Работают сверлами только в одну сторону. Сверло представляет собой стержень, оканчивающийся внизу режущей частью, состоящей из подрезателя, лезвия и направляющего центра (острия). Диаметр центровых сверл 12–50 мм, длина в зависимости от диаметра – 120–150 мм. При работе этими сверлами нужно делать нажим, иначе они не будут внедряться в древесину.
Сверла винтовые (рис. 41, в) применяют для сверления глубоких отверстий поперек волокон. Конец сверла имеет винт с мелкой резьбой. При сверлении ими отверстия получаются чистыми, так как по винтовым каналам стружка удаляется легко. Диаметр сверл 10–50 мм, длина 40–1100 мм.
Спиральные сверла (рис. 41, г) в зависимости от формы режущей части бывают с конической заточкой и с центром и подрезателями. Для отвода стружки в стержне имеются канавки, располагаемые по винтовой линии. Сверла с центром и подрезателем выпускаются диаметром 4–32 мм, а с конической заточкой – диаметром 2–6 мм (короткая серия) и 5–10 мм (длинная серия).
Сверла приводятся в действие с помощью коловорота и сверлилки. Коловорот применяют для сверления отверстий при выполнении плотничных и опалубочных работ, а также используют для завертывания и отвертывания шурупов при стекольных и других видах работ.
Коловорот с трещоткой (рис. 41, д) представляет собой коленчатый стержень, посередине которого находится ручка для вращения. На одном конце коленчатого стержня расположен патрон для крепления сверл, на другом – нажимная головка. Коловорот с трещоткой может вращаться вправо и влево, причем направление вращения устанавливается кольцом-переключателем. Кулачки патрона должны обеспечивать надежное закрепление инструментов. Коловоротом можно завертывать болты, шурупы, для чего в патрон вставляют соответственно гаечные торцовые ключи (квадратные и шестигранные), отвертки. В коловороте можно крепить сверла с диаметром хвостовика до 10 мм. Для завертывания шурупов в коловорот вставляют отвертки. Коловорот, состоящий из коленчатого стержня, четырехкулачкового патрона, кольца-переключателя, изготовляют из конструкционной стали. Все детали коловорота имеют защитно-гальваническое покрытие.
Отверстия диаметром до 5 мм высверливают сверлилкой. Сверлилка (рис. 41, е) представляет собой стержень с винтовой нарезкой, на который надета ручка. На одном конце стержня имеется патрон для установки сверл, а на другом – головка. Стержень, а вместе с ним и сверло, вращают путем передвижения вверх и вниз нарезной ручки.
Для сверления глубоких отверстий используют бурав (рис. 41, ж), представляющий собой стержень с ушком для ручки, расположенной в его верхней части, и с винтовым сверлом на другом конце (в нижней части).
Неглубокие отверстия в древесине твердых пород под шурупы сверлят буравчиком (рис. 41, з), имеющим диаметр 2–10 мм. Во избежание раскола древесины буравчик периодически вынимают из отверстия и очищают от стружки.
Рис. 41. Сверла ручные и сверлильные инструменты: а – перовое сверло; б – бурав; в – винтовое сверло; г – спиральное сверло; д – коловорот; е – сверлилка; ж – центровое сверло; з – буравчик; 1 – нажимная головка; 2 – коленчатый стержень; 3 – ручка; 4 – кольцо-переключатель; 5 – механизм храповой; 6 – патрон; 7 – головка; 8 – нарезная ручка; 9 – стальной стержень; 10 – патрон; 11 – подрезатель; 12 – центр (острие)
Отверстия сверлами выбирают по разметке или шаблону, центр отверстия предварительно накалывают шилом. До начала работы сверло надо хорошо заточить напильником с мелкой насечкой или на специальном станке, а затем прочно закрепить в патроне коловорота или сверлилки. Приемы сверления показаны на рис. 42.
Рис. 42. Приемы сверления коловоротом: а – горизонтально уложенного материала; б – закрепляемого в тисках верстака вертикально
При работе надо следить за тем, чтобы ось вращения коловорота или сверлилки совпадала с осью отверстия. При сверлении вертикальных отверстий нажимную головку коловорота держат левой рукой, а правой – вращают ручку.
Глубокие сквозные отверстия сверлят по разметке с двух сторон детали. При сверлении отверстия с одной стороны детали перед выходом на другую сторону нажим на нажимную головку коловорота надо ослабить, чтобы не образовалось откола, отщепа или трещины в детали. Под деталь, в которой сверлят отверстия, подкладывают доску.
Работают коловоротом так: укладывают заготовку-деталь на верстак и размечают точку отверстия. Затем ручку коловорота охватывают пальцами правой руки, а нажимную головку – пальцами левой руки. При сверлении левой рукой нажимают на головку, а правой – вращают коленчатый стержень.
Коловорот или сверлилку нельзя держать так, чтобы сверло было обращено в сторону работающего. Нажимать на нажимную головку коловорота, сверлилки нужно только руками. Работать сверлами, имеющими трещины и другие дефекты, нельзя.
При некачественном сверлении возникают следующие дефекты: невыдержанный размер (диаметр) отверстия, вызванный биением сверла вследствие неправильного закрепления его в коловороте; рваная поверхность отверстия – при сверлении тупым или неправильно заточенным сверлом.
Механизированное сверление древесины. Для механизированного сверления применяют ручные электрические сверлильные машины, состоящие из корпуса, электродвигателя, редуктора, выключателя с курковым приводом, токоведущего кабеля и штепсельного соединения. На конце шпинделя имеется патрон для крепления сверл.
Для сверления отверстий электрическими машинами применяют в основном спиральные сверла. Перед работой машину тщательно осматривают и проверяют, после чего в патрон вставляют сверло и прочно его закрепляют, а затем нажимом на пусковой курок включают электродвигатель. В течение 1–2 мин работают вхолостую; если электродвигатель работает нормально, приступают к работе.
При сверлении отверстий нажим должен быть равномерным, при выборке сквозных отверстий в конце сверления во избежание заедания нажим следует несколько ослабить.
При работе сверлом диаметром до 9 мм скорость подачи должна быть не более 0,7 м/мин. Если при включении электродвигатель не работает, значит отсутствует напряжение либо неисправен выключатель. При излишнем нагреве редуктора надо проверить наличие смазки. Если при прикосновении к корпусу сверлилки «бьет» током, проверяют заземление.
Для завинчивания винтов, болтов, гаек, шурупов используют электрический шуруповерт ИЭ-3601Б. Им можно завинчивать шурупы диаметром до 6 мм.
При выполнении столярных работ целесообразно пользоваться индивидуальным набором ручного инструмента для столяра строительного ИН-18, в который входят столярный молоток, топор, клещи, ножовки, коловорот, рубанки с одиночным и двойным ножом, зензубель, отвес, деревянная киянка, разводка для пил, плоские стамески, отвертка, столярное долото, отвертка для шурупов с крестообразными шлицами, трехгранный напильник, реечный рейсмус, строительный уровень, угольник, шлифовальный брусок, складной деревянный метр. Рабочий инструмент размещается в ручном деревянном чемодане-футляре размером 535450115 мм. Масса набора 10 кг.
Глава 3
СТОЛЯРНЫЕ И ПЛОТНИЧНЫЕ СОЕДИНЕНИЯ
1. Плотничные соединения
Для получения строительных элементов требуемых размеров лесоматериалы соединяют по длине, ширине, толщине и высоте посредством врубок. Врубки применяют при изготовлении балок, ферм, строительстве рубленых и брусчатых домов. Врубки на строительстве выполняют по разметке вручную и по шаблонам с помощью ручного или электрического инструмента. Ножовкой или электропилой выпиливают излишки древесины, после чего стамеской зачищают это место. При выпиливании нужно следить за тем, чтобы пилой не выходить за пределы разметки.
Соединения должны быть надежными и прочными в процессе эксплуатации, технологичны в изготовлении, выполнены аккуратно и тщательно, с пригонкой на месте монтажа. Зазоры и неплотности в соединениях, а также сучки в местах сопряжения не допускаются. Эти дефекты необходимо устранить.
Соединение отрезков более крупных размеров по длине для получения деталей нужных размеров называются сращиванием. Сращивание производится вполдерева, косым прирубом, прямым и косым накладными замками, прямым и косым натяжными замками, впритык. При сращивании в полдерева (рис. 43, а) длина соединения должна быть равна 2–2,5 толщины бруса. Соединение скрепляют нагелями (при строительстве брусчатых домов).
Соединение косым прирубом с подрезкой торца (рис. 43, б) делают равным 2,5–3 толщины бруса и крепят также нагелями.
Соединение прямым (рис. 43, в) или косым накладным замком (рис. 43, г) используют в конструкциях, в которых возникают растягивающие усилия. Соединения в прямой накладной замок располагаются на опоре, а в косой накладной замок – у опор.
Соединения в прямой (рис. 43, д) или косой натяжной замок (рис. 43, е) являются прочными, однако их изготовление сложно, кроме того, при усыхании древесины ослабляются клинья, поэтому для ответственных деревянных конструкций применять натяжные замки не рекомендуется.
Сращивание впритык (рис. 43, ж) производится в тех случаях, когда два бруса своими концами ложатся на опору. Концы брусьев соединяют вплотную, а затем крепят скобами.
Рис. 43. Сращивание: а – в полдерева; б – косым прирубом; в – прямой накладной замок; г – косой накладной замок; д – прямой натяжной замок; е – косой натяжной замок; ж – впритык; S – высота бруска.
Угловые соединения. Брусья, бревна соединяют под углом при возведении брусчатых и рубленых стен, устройстве верхней и нижней обвязок в каркасных домах и других деревянных конструкциях. Основными видами плотничных соединений являются соединения в полдерева (рис. 44, а), в полулапу (рис. 44, б), шиповое (рис. 44, в), угловое соединение сковороднем (рис. 44, г).
Врубку в полдерева выполняют путем вырубки или срезки половины толщины на концах соединяемых брусьев. После вырубки концы соединяют под прямым углом. Соединение в полулапу получается при зарезке на концах брусьев наклонных плоскостей. Обработанные концы брусьев плотно соединяют. Врубку угловым сковороднем выполняют так же, как и врубку в полдерева, но дополнительно в одном из брусьев выпиливают часть древесины.
Рис. 44. Соединение брусьев под углом: а – в полдерева; б – в полулапу; в – шиповое; г – угловое сковороднем
Крестообразные соединения. Этот вид соединения брусьев (рис. 45) применяют при строительстве мостов и изготовлении других деревянных конструкций. Такие соединения выполняют в полдерева, в треть и в четверть дерева, а также с зарубкой одного бруса.
Соединение по высоте. Соединение по высоте называется наращиванием. Этот вид соединения применяют при устройстве столбов, мачт и др. Наращивать бревна и брусья можно впритык с потайным шипом (рис. 46, а), впритык со сквозным гребнем (рис. 46, б), в полдерева с креплением болтами (рис. 46, в), в полдерева с креплением полосовой сталью (рис. 46, г), в полдерева с креплением хомутами (рис. 46, д), косым прирубом с креплением хомутами (рис. 46, е), применяемым в ответственных сооружениях, впритык с накладками и креплением болтами (рис. 46, ж). Длину стыков делают обычно равной двум или трем толщинам соединяемых брусьев или двум или трем диаметрам соединяемых бревен.
Рис. 45. Крестообразное соединение брусьев: а – в полдерева; б – в треть дерева; в – в четверть дерева; г – с зарубкой одного бруса; S – высота бруска
Рис. 46. Соединение бревен при наращивании: а – впритык с потайным шипом; б – впритык со сквозным гребнем; в – в полдерева с креплением болтами; г – в полдерева с креплением полосовой сталью; д – в полдерева с креплением хомутами; е – косым прирубом с креплением хомутами; ж – впритык с накладками и креплением болтами; d – диаметр бревна.
2. Столярные соединения
Бруски столярных изделий соединяют между собой шиповым соединением, состоящим из двух элементов – шипа и гнезда, или проушины. Шип – выступ на торце бруска, входящий в соответствующее гнездо или проушину другого бруска. Шипы бывают одинарными (рис. 47, а), двойными (рис. 47, б), многократными (рис. 47, в), т. е. более двух.
Цельный шип – это шип, составляющий одно целое с бруском. Вставным шипом называют шип, выполненный отдельно от бруска. Шип с поперечным сечением в виде круга называется круглым (рис. 47, г).
Шип «ласточкин хвост» (рис. 47, д) имеет профиль в виде равнобедренной трапеции с большим основанием на торцовой грани типа; односторонний шип «ласточкин хвост» – в виде прямоугольной трапеции на торцовой грани шипа (рис. 47, е).
Зубчатый шп имеет профиль в виде треугольника или трапеции, меньшее основание которого является торцовой гранью шипа (рис. 47, ж), двукосый зубчатый шип (рис. 47, з) – равнобедренного треугольника.
Одинарные и двойные шипы применяют при изготовлении окон, рамочных дверей, мебели; шип «ласточкин хвост» – при изготовлении ящиков, коробок; зубчатые шипы – при клеевом соединении деталей (сращивании) по длине.
Для того, чтобы образовать шип, проушину, гнездо, обработанные бруски, простроганные с четырех сторон на требуемый размер, предварительно размечают (рис. 47, и, к, л, м).
Рис. 47. Виды шипов: а – одинарный; б – двойной: в – многократный; г – круглый; д – «ласточкин хвост»; е – односторонний «ласточкин хвост»; ж, з – зубчатые; и – гнездо; к, л – проушины; м – глухой шип; н – шип в потемок; о – шип в полупотемок.
Кроме этого, применяют шипы круглые вставные при соединении делянок (заготовок) по ширине. Шипы в потемок (рис. 47, н) и полупотемок (рис. 47, о) используют при изготовлении рамок, мебели и др.
Шип в потемок делают не только при концевом соединении, но и в тех случаях, когда требуется, чтобы края гнезда были незаметны, так как получить ровные края гнезда не всегда удается. Чтобы скрыть этот дефект, у шипа вырезают потемок, т. е. снимают часть шипа по ширине с одной или обеих сторон.
Конструктивные части и элементы столярных изделий. Столярные изделия имеют следующие основные конструктивные части и элементы (рис. 48). Брусок – простейшая деталь; бывает разных размеров, сечений и формы. Узкая продольная сторона бруска называется кромкой, а продольная широкая – пластью, линия пересечения пласти с кромкой – ребром. Концевую поперечную сторону бруска, образованную при торцовке под прямым углом, называют торцом.
При изготовлении оконных и дверных блоков бруски малых сечений (вертикальные, горизонтальные горбыльки створок) выполняют из цельной древесины, а бруски больших сечений (коробки) делают клееными.
Раскладками называют бруски, предназначенные для крепления стекол в створках, дверях или филенок в дверных полотнах рамочной конструкции.
Рис. 48. Форма обработанных брусков: а – фаска; б – штаб (штап); в – закругленные ребра; г – галтель; д – фалец-четверть; е – калевка; ж – шип; з – проушина; и – кромка с профильной обработкой; к – брусок; л – гнездо; м – раскладка; н – платик; о – свес; 1 – заплечики; 2 – боковая грань шипа; 3 – торцовая грань шипа; 4 – филенка; 5 – кромка; 6 – торец; 7 – пласть; l – длина; b – ширина шипа; s – толщина шипа.
Филенки представляют собой щит прямоугольной формы, изготовленный из столярной, древесностружечной или древесноволокнистой плиты. По форме филенки бывают плоские, со скошенными кромками и с профильной обработкой кромок. Филенку в рамках дверей устанавливают в паз, фальц и крепят раскладками или накладывают на бруски и крепят шурупами.
Фальцем называют прямоугольную выемку в бруске. Если выемка имеет равные стороны угла, то она образует четверть.
Платик – уступ, образованный для скрытия зазора; его применяют в тех случаях, когда пригонка детали заподлицо затруднена. Использование пластика упрощает сборку изделий. Его применяют при изготовлении мебели.
Свес – выступ за пределы основания. Его применяют при изготовлении мебели.
Галтелью называют полукруглую выемку на кромке или пласти детали. Рамка состоит из четырех брусков, образующих квадрат или прямоугольник. Отдельные рамки имеют, кроме того, внутренние бруски – средники (рамочные двери, оконные створки с горбыльками).
Рамки собирают на шиповом соединении. Небольшого размера рамки собирают на одинарный открытый сквозной шип, шип с полупотемком или потемком. При изготовлении столярных изделий применяют преимущественно рамки прямоугольной формы, очень редко (для уникальных изделий) – многоугольные или круглые. Оконная створка, форточка, фрамуга, коробка – все это рамки.
Все соединения в оконных блоках выполняют на шипах. Прочность шипового соединения определяется его размерами и площадью склеиваемых поверхностей. Для увеличения прочности шипы делают двойными (в окнах).
Щиты изготовляют массивными (дощатыми) или с пустотами. Массивные щиты во избежание коробления следует набирать из узких реек (деталей) шириной не более 1,5 толщины, с подбором волокон, влажностью до 10 ± 2 %.
При склеивании деталей по ширине одноименные (заболонные) пласти соединяемых реек должны быть обращены в противоположные стороны, а одноименные кромки – друг к другу.
Стыковать рейки по длине допускается, если стыки расположены вразбежку и расстояние между ними в смежных рейках не менее 150 мм.
В щитах, предназначенных для несущих конструкций, рейки по длине не стыкуют. Из щитов изготовляют панели стеновые, тамбуры и т. п.
Во избежание коробления щиты делают со шпонками (рис. 49, а), с наконечниками (рис. 49, б), с вклеенными (рис. 49, в, г) и наклеенной рейками (рис. 49, д). Шпонки в щитах делают заподлицо с плоскостью или выступающими. На каждый щит ставят не менее двух шпонок. Щиты со шпонками предназначены для дверей временных зданий и т. п.
Кроме дощатых, изготовляют многослойные шиты, склеенные из трех или пяти однослойных щитов с взаимно перпендикулярным направлением волокон (рис. 49, е).
Рис. 49. Виды щитов: а – со шпонками; б – с наконечниками в паз (шпунт) и гребень; в – с вклеенной рейкой в торец; г – с вклеенной треугольной рейкой; д – с наклеенной треугольной рейкой; е – многослойный
Массивные щиты склеивают на гладкую фугу (рис. 50, а), на рейку (рис. 50, б), в четверть (рис. 50, в), в паз и гребень (рис. 50, г, д) и в «ласточкин хвост»
Рис. 50. Способы соединения щитов: а – на гладкую фугу; б – па рейку; в – в четверть; г – в паз и гребень; д – треугольный гребень; е – в «ласточкин хвост»
Соединение деталей из древесины. Сращивание отрезков по длине может быть торцовым, на «ус», зубчатым, ступенчатым.
Торцовое клеевое соединение (рис. 51, а) – это клеевое соединение торцовыми поверхностями склеивания. Под торцовым клеевым соединением на «ус» (рис. 51, 6) понимают клеевое соединение плоскими поверхностями склеивания, расположенными под острым углом к продольной оси заготовок.
Клеевое соединение на ступенчатый «ус» (рис. 51, в) – это соединение, в котором поверхности склеивания имеют выступ, препятствующий смещению заготовок в продольном направлении при растяжении. Соединение, в котором скошенные концы заготовок имеют затупление, препятствующее смещению заготовок в продольном направлении при растяжении и сжатии, называют соединением на ступенчатый «ус» с затуплением (рис. 51, г).
Зубчатое клеевое соединение (рис. 51, д) – это соединение профилированными поверхностями в виде зубчатых шипов, вертикальное зубчатое соединение (рис. 51, е) – соединение с выходом профиля шипов на пласть заготовки. В горизонтальном зубчатом соединении (рис. 51, ж) профиль шипов выходит за кромку заготовки. Зубчатое клеевое соединение на «ус» (рис. 51, з) – соединение на «ус» профилированными поверхностями склеивания в виде зубчатых шипов.
Рис. 51. Клеевые соединения брусков, досок по длине: а – торцовое; б – на «ус»; в – на ступенчатый «ус»; г – на ступенчатый «ус» с затуплением; д – зубчатое; е – вертикальное зубчатое; ж – горизонтальное зубчатое; з – зубчатое на «ус»; и – ступенчатое; – угол скоса; L – длина уса шипа; t – шаг соединения; k – зазор; b – затупление; В – толщина заготовки; i – угол шипа
Ступенчатое клеевое соединение (рис. 51, и) – торцовое соединение профилированными поверхностями склеивания в виде ступеньки, высота которой равна половине толщины заготовки.
Наиболее прочным является клееве соединение на зубчатый шип. Этот вид соединения применяют для сращивания брусков створок, фрамуг, оконных и дверных коробок и других строительных элементов. Склеиваемые заготовки не должны отличаться по влажности более чем на 6 %. В зоне соединения заготовок не допускаются сучки более 5 мм. Параметр шероховатости поверхности склеивания зубчатых шипов Rmmax не должен превышать 200 мкм.
Размеры шиповых соединений приведены в табл. 1.
Таблица 1
Размер типовых соединений
Сплачивание заключается в соединении брусков, досок, делянок по ширине кромки в щиты или пластями в блоки. Каждую заготовку, соединяемую в щит, называют делянкой.
Соединение по кромке в зависимости от назначения изделий рекомендуется производить на рейку, в четверть, в прямоугольный паз и гребень и на гладкую фугу.
При выполнении соединений на рейку К-1 (рис. 52, а) следует при l, равном 20–30 мм, делать l1 на 2–3 мм больше; S1 принимают равным 0,45S0 для реек из древесины, а для реек из фанеры S1 делают 0,25S0; размер S1 принимают равным ближайшим размерам пазовой дисковой фрезы, т. е. 4, 5, 6, 8, 10, 12, 16, 20 мм. На кромках допускаются одно– и двусторонние фаски.
Для соединений в четверть по кромке К-2 (рис. 52, б) h0 = 0,5, S0 – 0,5 мм, а b находится в следующей зависимости от S0, мм:
S0 12–15 15–20 20–30 30
b 6 8 10 16
Для соединения в паз и гребень типа К-3 (рис. 52, в) (табл. 2) радиус закругления r делают 1–2 мм, а размер l1 – на 1–2 мм больше размера l. На кромках допускаются одно– и двусторонние фаски.
Размеры соединений К-4 (рис. 52, г) приведены в табл. 3.
Размеры пазов и гребней соединения К-5 (рис. 52, д) определяют по табл. 4.
Шов, образуемый при соединении делянок, называют фугой. Делянки, из которых склеивают щит на гладкую фугу типа К-6 (рис. 52, е), должны иметь гладкие и ровные кромки, образующие с плоскостью (пластью) прямой угол по всей длине. Если при соединении делянок нет просветов, то прифуговка (пригонка) их выполнена качественно. Склеивают щиты в стяжных хомутах, ваймах, прессах.
Рис. 52. Схемы соединения досок (делянок) по кромке: а – по кромке на рейку К-1; б – в четверть по кромке К-2; в – в прямоугольный паз и гребень по кромке К-3; г – по кромке в прямоугольный паз и гребень К-4; д – трапецеидальный паз и гребень по кромке К-5; е – на гладкую фугу по кромке К-6
Таблица 2
Размеры соединений К-3, мм
Таблица 3
Размеры соединений К-4, мм
Таблица 4
Размеры соединений К-5, мм
Кроме склеивания, щиты можно собирать из делянок на круглые вставные шипы, при этом диаметр шипа должен составлять 0,5 толщины делянки, а длина должна быть 8–10 диаметров. Шипы устанавливают с шагом 100–150 мм.
Соединение в паз и гребень, а также в четверть производят путем отборки по всей длине кромки (делянки) с одной стороны паза или четверти, а с другой – гребня или четверти. Это соединение применяют при изготовлении щитов, настилке дощатых полов, устройстве столярных перегородок, подшивке потолков. Соединение на гладкую фугу более экономично, чем соединение в четверть или в паз и гребень.
При соединении на рейку вдоль кромок делянок выбирают пазы, в которые вставляют деревянные или фанерные рейки.
3. Шиповые соединения столярных изделий
При производстве столярных изделий основным видом соединений является шиповое, состоящее из двух элементов: шипа и гнезда или проушины. В зависимости от толщины изделий, требуемой прочности бруски соединяют на один, два и более шипов. Увеличение числа шипов повышает площадь склеивания.
Шиповые соединения брусков бывают угловые концевые, серединные и ящичные.
Угловые концевые соединения брусков выполняют на шипы: открытый сквозной одинарный УК-1 (рис. 53, а), открытый сквозной двойной УК-2 (рис. 53, б), открытый сквозной тройной УК-3 (рис. 53, в), несквозной с полупотемком УК-4 (рис. 53, г), сквозной с полупотемком УК-5 (рис. 53, д), несквозной с потемком УК-6 (рис. 53, е), сквозной с потемком УК-7 (рис. 53, ж), несквозные и сквозные на круглые вставные шипы УК-8 (рис. 53, з), на «ус» со вставным несквозным круглым шипом УК-9 (рис. 53, и), на «ус» со вставным несквозным плоским шипом УК-10 (рис. 53, к), на «ус» со вставным сквозным плоским шипом УК-11 (рис. 53, л). Размеры шипов и других элементов угловых концевых шиповых соединений приведены в табл. 5, а виды угловых соединений и угловых ящичных соединений – на рис. 54 и 55.
Таблица 5
Размеры шипов и других элементов угловых концевых соединений
Рис. 53. Угловые концевые соединения: а – на шип открытый сквозной одинарный УК-1; б – на шип открытый сквозной двойной УК-2; в – на шип открытый сквозной тройной УК-3; г – на шип с полупотемком несквозной УК-4; д – на шип с полупотемком сквозной УК-5; е – на шип с потемком несквозной УК-6; ж – на шип с потемком сквозной УК-7; з – на шипы круглые вставные (шканты) несквозные и сквозные УК-8; и – на «ус» со вставным несквозным круглым шипом УК-9; к – на «ус» со вставным несквозным плоским шипом УК-10; л – на «ус» со вставным сквозным плоским шипом УК-11
Размеры шипов и других угловых серединных соединений должны быть следующие. В соединении УС-3 S1 = 0,4S0; S2 = 0,5(S0 – S1); b – не менее 2 мм; l1 = (0,3–0,8)В; l2 = (0,2–0,3)B1. В соединениях УС-1, УС-2 допускается двойной шип, при этом S1 = 0,2S0; R соответствует радиусу фрезы. Для соединения УС-4 S1 = S3 = 0,2S0; S2 = 0,5[S0 – (2S1 + S3)]. Для соединения УС-5 S1 = (0,4–0,5)S0; l = (0,3–0,8)S; S2 = 0,5(S0 – S1); b – не менее 2 мм. Для соединения УС-6 l = (0,3–0,5)S0; b – не менее 1 мм. Для соединения УС-7 d = 0,4; l = (2,5–6)d; l1 > l на 2–3 мм. Для соединения УС-8 l = (0,3–0,5)B1; S1 = 0,85S0. Полученный размер следует округлить до ближайшего размера фрезы (13, 14, 15, 16 и 17 мм), но не менее S0.
Расчетные толщины шипов и диаметры шкантов соединений типа УС округляют до ближайшего размера фрезы (4, 6, 8, 10, 12, 14, 16, 20 и 25 мм), а угол устанавливают в зависимости от конструкции изделия.
Размеры углового ящичного соединения УЯ-1: S1 = S3 = 6, 8, 10, 12, 14, 16 мм; l = S0; S2 должно быть не менее 0,3S0. В соединении УЯ-2 S1 = 0,85S0, причем полученный таким образом размер округляют до ближайшего размера фрезы (13, 14, 15, 16, 17 мм); S – не менее 0,75S ;
S3 = (0,85—3)S0; l = S0, = 10°.
В этом соединении допускается шип «ласточкин хвост» в полупотай.
Рис. 54. Угловые серединные соединения: а – на шип одинарный несквозной УС-1; б – на шип одинарный несквозной в паз УС-2; в – на шип одинарный сквозной УС-3; г – на шип двойной сквозной УС-4; д – в паз и гребень несквозной УС-5; е – в паз несквозной УС-6; ж – на шипы круглые вставные несквозные УС-7; з – на шип «ласточкин хвост» несквозной УС-8
Рис. 55. Угловые ящичные соединения: а – на шип прямой открытый УЯ-1; б – на шип открытый «ласточкин хвост» УЯ-2; в – на открытый круглый вставной шип (шкант) УЯ-3
В соединении УЯ-3 d = = 0,4S0; полученный размер шкантов округляют до ближайшего размера фрезы (4, 6, 8, 10, 12, 16, 20 и 25 мм); l = = (2,5–6)d; l1 более l на 1–2 мм; b – от 0 до dmin.
Для столярных изделий угловые шиповые соединения делают концевыми – на сквозных прямых шипах; серединными вертикальными – на сквозных прямых шипах или шкантах; серединными горизонтальными – на несквозных прямых шипах или шкантах. Типы шиповых соединений в зависимости от толщины соединяемых деталей даны в табл. 6.
Шиповое соединение должно быть выполнено с величинами натягов и зазоров в пределах 0,1–0,3 мм, т. е. практически плотным.
Основными недостатками в шиповом соединении являются: невыдержанность размеров шипа по длине, толщине, непараллельность поверхностей шипа или проушины, сколы, вырывы, неплотности в шиповом соединении и др.
Таблица 6
Шиповые соединения столярных изделий
4. Выработка шипов и проушин
При выработке шипов и проушин выполняют следующие операции: размечают шипы и проушины, запиливают, выпиливают заплечики и выдалбливают проушины. В соответствии с рабочим чертежом определяют размеры соединений, после чего приступают к разметке.
Разметка углового концевого соединения на открытый сквозной одинарный шип УК-1 для брусков толщиной 42 мм и шириной 65 мм приведена на рис. 56. Для соединения УК-1 Sl = 0,4S0; S2 = 0,5(S0 – S1), где S0 – толщина бруска, равная 42 мм. Отсюда толщина шипа S1 = 0,4S0 = = 0,4 · 42 = 16,8 мм (округленно принимаем равной 16 мм), S2 = 0,5(42 – 16) = 13 мм. В соответствии с этими данными размечают шипы. И шипы, и проушины можно размечать используя шаблоны, с помощью которых на торцах бруска наносят риски.
Запиливают шипы и проушины лучковой пилой очень тщательно, так как перекос шипа приведет к перекосу створки. Если шип толще проектного размера, то при посадке в проушину он может расколоть брусок, а если тоньше, то соединение получится непрочным, так как оно будет без плотной посадки.
При пилении следят за тем, чтобы пила проходила около риски, только в этом случае получится точный размер шипа или проушины. При выработке шипов пилят только с наружной стороны риски, а при выработке проушин – с внутренней.
Рис. 56. Разметка шипов и проушин: а – разметка линейной высоты шипа; б – нанесение риски длины шипа угольником с карандашом; в – разметка толщины шипа линейкой; г – нанесение риски рейсмусом; д – разметка концевого соединения; е – проушина; ж – шип; 1 – риска; 2 – линия пропила; 3 – линия разметки; 4 – заплечико; 5 – удаляемая часть древесины
При начале пиления для быстрого углубления пилу ставят на ребро под углом 15–20° и, сделав несколько движений на себя, без нажима углубляют пилу, после чего пилят равномерно без нажима и рывков. После запила срезают плечики. Проушину после запила выдалбливают долотом с киянкой и зачищают стамеской.
5. Соединения элементов на нагелях, гвоздях, шурупах
Нагели представляют собой деревянные или металлические стержни цилиндрической или крестообразной формы. Их применяют как дополнительное крепление в угловых и серединных шиповых соединениях для предохранения шипа от выворачивания. Соединяют детали нагелями по расчет у, размечая места установки в соответствии с чертежом, и по шаблонам.
Отверстия под нагели выбирают сверлами. Места отверстий до начала сверления размечают по шаблону. Сверлить отверстия нужно так, чтобы сверло шло без отклонений по заданному направлению.
Нагель ставят таким образом, чтобы он был перпендикулярен боковым граням шипа и проходил сквозь оба соединяемых бруска, т. е. через шип и проушину. Заменять деревянные нагели обычными гвоздями в шиповом соединении не допускается, так как гвозди портят соединение и не дают той прочности, что нагель. Деревянные нагели в шиповом соединении ставят на клею.
Гвоздевые соединения определяют расчетным путем, а в некоторых случаях количество гвоздей устанавливают конструктивно, например, при настилке полов, установке встроенного оборудования, устройстве перегородок, подшивке потолков и т. п.
В гвоздевых соединениях конструкции, изготовляемых из древесины лиственницы и твердых лиственных пород (береза), гвозди диаметром более 6 мм следует забивать в заранее просверленные гнезда, причем диаметр гнезда должен составлять 0,9d (d – диаметр забиваемого гвоздя), а глубина – 0,6 длины гвоздя.
В соединении элементов из досок хвойных и мягких лиственных пород гвозди независимо от диаметра забивают без предварительного рассверливания гнезд.
Расстояние между осями гвоздей (вдоль волокон) для сколачивания деревянных элементов (досок) должны быть 15d при толщине пробиваемого элемента большей 10d и 25d при толщине пробиваемого элемента равной 4d. Это же расстояние между осями гвоздей для элементов, не пробиваемых насквозь гвоздями, должно быть равно или больше 15d.
Расстояние между осями гвоздей (поперек волокон) при условии прямой расстановки гвоздей должно быть 4d, а при забивании гвоздей в шахматном порядке или под углом меньшем 45° расстояние между продольными рядами гвоздей уменьшают до 3d.
Расстояние от продольной кромки элемента до крайнего гвоздя должно быть не менее 4d. Диаметр гвоздей не должен быть больше 0,25 толщины наиболее тонкой пробиваемой доски.
Забивать гвозди в деревянные конструкции следует по шаблону, кондуктору, в которых места забивания гвоздей должны точно соответствовать чертежам. Шаблоны изготовляют из фанеры или кровельной стали.
В конструкциях, в которых гвозди работают на выдергивание, длина защемленной части гвоздя должна быть не менее двух толщин пробиваемого деревянного элемента и не менее 10 диаметров гвоздя.
При встречном забивании гвозди не должны пробивать насквозь все доски (паркет). При сквозном забивании концы гвоздей следует загнуть поперек волокон. Допускаемое отклонение в расстоянии между центрами гвоздей с той стороны, с которой их забивают, составляет ±2 мм.
Если при забивании гвоздь изогнулся, его необходимо выдернуть и заменить новым. Забивать гвозди в мерзлую и сырую древесину не рекомендуется, так как они коррозируют (ржавеют), что снижает прочность соединения. Гвозди надо забивать в здоровую часть древесины. Не следует забивать их в сучки и трещины.
При креплении наличников, плинтусов, досок пола головки гвоздей утапливают и перед окраской шпаклюют для укрытия возможных вмятин.
Шурупы в столярных изделиях используют для крепления нащельников, приборов – петель, ручек, заверток, замков и т. п. При этом преимущественно используют шурупы с потайной головкой. Соединения на шурупах применяют при сборке встроенной мебели, когда соединяемые элементы трудно склеить, а таже в том случае, когда отдельные элементы нужно сделать разборными (ремонт приборов, нательников, отливов и др.).
В древесину шуруп завертывают коловоротом с отверткой или электрошуруповертом, а не забивают. При забивании шурупа в древесину молотком винтовое соединение получается непрочным, так как сминается нарезка и нарушается древесина в месте прохождения шурупа. При этом соединение теряет до 40 % силы, удерживающей шуруп в древесине.
При завертывании шурупа в древесине образуется естественная гайка, благодаря чему соединяемые элементы прочно стягиваются.
Прочность соединения шурупами зависит от плотности древесины, размеров и количества шурупов, глубины их завертывания (завертывать шуруп надо до отказа), направления волокон.
В древесину твердых пород шурупы следует завертывать в заранее просверленные отверстия. Диаметр отверстия должен составлять 0,9 диаметра ненарезанной части шурупа, а длина отверстия – от 1/2 до 3/4 длины шурупа. При завертывании шурупов в древесину дуба во избежание коррозии их предварительно смазывают тавотом. Во влажную древесину шурупы завертывать не рекомендуется, так как они будут быстро коррозировать (ржаветь). При соединении строительных элементов шурупами расстояние между осями вдоль волокон должно составлять 10d, между осями поперек волокон и от продольной кромки – 5d (d – диаметр шурупа).
6. Склеивание древесины
Основные требования к процессу склеивания. В столярном деле широко применяется свойство древесины хорошо склеиваться различными клеями. При этом прочность деталей увеличивается, коробление уменьшается, а древесина получает запас прочности больший, чем в массиве.
В основном процесс склеивания в столярном производстве проходит по следующей схеме: на плотно прифугованные поверхности наносят клей и под давлением сжимают эти поверхности. При высыхании клеевого раствора склеивание считается законченным.
На прочность склеивания влияет не только разновидность клеевого состава, но и его качество, правильность приготовления, режимы склеивания, влажность древесины, состояние воздуха в помещении, давление при склеивании, температура среды и т. д. Если под действием нагрузки произошло разрушение по клею, то прочность склеивания низкая, если по древесине – высокая.
Брак при склеивании должен быть исправлен, так как при наличии брака изделие или предмет может прийти в негодность. Дефекты образуются за счет неправильно приготовленного клеевого состава, а также в результате некачественной подготовки склеиваемых поверхностей, неравномерного нанесения клея, чрезмерного или недостаточного давления при запрессовке, несоблюдения температурного режима, повышенной влажности и запыленности помещения, в котором выполняют склеивание.
К процессу склеивания необходимо подходить со знанием дела и не торопясь. Брак легче предупредить, чем потом исправить. Небрежное отношение к технологии склеивания обрекает начинающего мастера на неудачу.
Подготовка древесины к склеиванию. Поверхности, подлежащие склеиванию, должны быть точно подогнаны. Особенно это касается открытых плоскостей, где поверхности прифуговываются или шлифуются. В мозаичных работах по дереву это особенно важно, так как в наборе применяется шпон разной толщины.
Склеиваемые поверхности должны быть сухими. Влажность древесины не должна превышать 12 %, а облицовочных материалов (строганного и лущеного шпона) – 8 %.
ДСП и фанеру перед склеиванием шлифуют крупнозернистой наждачной бумагой. Поверхность столярных плит должна быть без волнистости, которая является следствием коробления при хранении.
При подготовке деталей и плоскостей для склеивания применяют обезжиривание и обессмоливание, при необходимости заделывают торцевые поверхности. Для склеивания на глютиновом и казеиновом клеях применяют цинубление, что дает хорошее качество шва. В домашних условиях цинубление можно заменить шлифованием крупнозернистой наждачной бумагой. Если поверхность имеет вырывы, сколы, вмятины и другие дефекты, то ее шпатлюют. В конце подготовки с поверхности убирают пыль, желательно с помощью пылесоса или щетки. Руками убирать (смахивать или сдувать) пыль не рекомендуется.
После предварительной подготовки пропитка поверхности клеевым раствором будет качественнее, значит прочность сцепления между двумя соединяемыми поверхностями (адгезия) – выше. Кроме того, адгезия зависит и от состояния клеевого раствора: чем выше его концентрация, тем прочнее соединяются плоскости.
Характеристика клеев и режимы склеивания. Склеивание производят сразу после подготовки поверхности, так как с течением времени ее качество ухудшается: она покрывается пылью, подвергается короблению и т. п. Поэтому соблюдение правил подготовки поверхностей к склеиванию, а также режимов склеивания обеспечит получение клеевых соединений высокого качества.
Исходным материалом при склеивании деталей и заготовок является клей. Применяются природные (в основном животного происхождения) и синтетические клеи. В домашних условиях используются костный, рыбий и мездровый клеи, которые объединяются под названием коллагеновые, или глютиновые, а также казеиновый клей. Из синтетических клеев применяются ПВА, наиритовые (особенно удобны для облицовывания) и др. В мозаичном деле используются клеи «Киттификс», «Мекол», «Суперцемент», «Момент-1».
Костный и мездровый клеи приготовляют из костей и мездры животных. В продаже он бывает под названием «Клей костный», «Клей мездровый» и т. д. На качество склеивания глютиновым клеем влияет прежде всего его чистота: чем он светлее, тем лучше. Для приготовления клея используют его свойство переходить в жидкое состояние при невысокой температуре плавления: костный – при 30, мездровый – при 40 °C. Цвет плиток клея – от светло-желтого до темно-коричневого. Клей выпускают не только в плитках, но и в виде гранул размером 3–4 мм, что очень удобно, так как он быстрее растворяется.
Для приготовления раствора клея раздробленные плитки или гранулы складывают в чистую посуду и заливают водой комнатной температуры (на одну часть клея по массе две части воды) так, чтобы вода полностью покрывала клей. Когда клей разбухнет (через 6—12 ч), его разогревают до температуры 80 °C в емкости на водяной бане (рис. 57). Если клей разогревать на открытом огне, он будет пригорать и терять свои качества. Для приготовления мездрового клея требуется больше воды, чем для костного.
Рис. 57. Разогрев клея: 1 – емкость для клея; 2 – емкость для воды
Клеи наносят на плоскости соединяемых деталей при помощи лубяной кисти быстрым движением руки. При применении вязкого раствора клея или при недостаточно высокой температуре воздуха в помещении склеиваемые поверхности соединяют сразу после нанесения клея во избежание его преждевременного остывания (древесина хорошо впитывает горячий клей). При жидком клее и высокой температуре необходима выдержка.
При облицовочных работах склеиваемые поверхности выдерживают под давлением в течение 6–7 ч, при всех остальных работах – в течение 2 ч. Выдержка деталей после распрессовки – 48 ч. После этого детали и облицованные плоскости можно подвергать дальнейшей механической обработке.
Расход костного клея: для облицовочных работ – 450, для соединений в паз и гребень – 800, на гладкую фугу – 500–800 г/м2. Мездрового клея расходуется в 1,5 раза меньше, чем костного.
При склеивании глютиновыми клеями необходимо соблюдать концентрацию и вязкость раствора. Для склеивания деталей концентрация раствора костного клея должна быть 45–50, мездрового – 35–40 %. Для облицовывания строганым шпоном приготовляют костный клей концентрацией 52–55, мездровый – 40–45 %. С увеличением концентрации клеевого раствора увеличивается и вязкость клея. А если его вязкость большая, то качество склеивания будет низким. Наиболее густой клеевой состав применяют при облицовывании шпоном, так как жидкий клей будет просачиваться сквозь шпон. Для крупнопористой древесины применяют клей средней вязкости и густой, для мелкопористой – жидкий.
Казеиновый клей приготовляют из молочного белка – казеина (обезжиренного творога), вводя в него добавки и растворяя в воде. Продают клей с примесями щелочей и антисептиков под названием «Клей казеиновый» в виде порошка.
Казеиновый клей приготовляют без подогрева, поскольку уже при 40 °C он становится непригоден – свертывается клеящее вещество (казеин). Приготовленнный клей долго хранить нельзя, а тем более под водой, так как он вбирает много воды, в результате чего ухудшаются его клеящие качества. Расход клея на 1 м2 – 200–350 г сухого порошка или 400–700 г клеевой массы.
Для приготовления клеевого состава берут одну часть порошка по массе и смешивают с двумя частями воды при комнатной температуре до полного исчезновения комочков. Затем клею дают отстояться 20 мин. Перед употреблением с него надо снять пену. Пользоваться раствором можно в течение 5–7 ч.
Следует помнить, что при облицовывании такими породами, как дуб, каштан, красное дерево, орех и т. д., клей может вызвать изменение окраски древесины из-за наличия в этих породах достаточного количества дубильных веществ.
При склеивании древесины казеиновым клеем покрывают обе склеиваемые поверхности. Давление пресса не влияет на прочность склеивания, а только выдерживает поверхности в сжатом состоянии. Под прессом выдерживают в течение 8 ч, а после распрессовки – 24 ч. Казеиновый клей дает прочные соединения и не боится сырости.
Синтетические клеи широко применяются в столярном производстве, так как их соединения отличаются прочностью, водо-, тепло– и биостойкостью.
В домашних условиях с успехом используются следующие клеи: поливинилацетатные – ПВА, ПВА-А, ПВА-Б, ПВА-М, ЭПВА; эпоксидные – «Эпоксид-П», «Эпоксид-ПБ», ЭПО, ЭДП и др.; каучуковые – 88Н, 88НП, «Стилит»; нитроцеллюлозные – «Суперцемент», «Мекол», «Киттификс» и др.
Клеи бывают готовыми к употреблению (например, ПВА) и двухкомпонентными (эпоксидные).
Наиболее распространенным является клей ПВА, который клеит надежно, быстро и чисто. Применяют его обычно без разбавления водой, но тщательно перемешанным. Наносят клей ПВА на поверхности, слегка смоченные водой (для повышения адгезии), щетинной кистью. Режим склеивания: под прессом – 6 ч, выдержка после распрессовки – 8 ч. Полное время схватывания – 24 ч. Клеем ПВА можно склеивать не под прессом, а с помощью нагретого утюга через влажную ткань. Расход клея при холодном способе – 180–260, при горячем – 110–180 г/м2.
Клеи на основе синтетических смол приготовляют по рецептам, которые приводятся на упаковке или в прилагаемой аннотации.
Столяры широко применяют клей НТ (наиритовый), который дает возможность облегчить процесс склеивания, так как при этом нет необходимости ни в запрессовке, ни в притирании. Схватывается он мгновенно и держит надежно. Наиритовый клей (белый или красноватый) представляет собой однородную сметанообразную массу со специфическим запахом. Долго хранить его не рекомендуется из-за постоянно протекающей полимеризации, в результате которой через 30–45 дней клей становится непригодным.
При наклеивании мозаичного набора клей наносят тонким слоем на чистую обезжиренную поверхность основы с помощью тампона из холстины и ваты. На мозаичный набор также наносят тонкий слой клея. Через 15 мин после нанесения к мозаичному набору прикладывают основу и поверхность слегка приглаживают колодочкой, на которую намотана ткань. Основу, на которую наклеивают шпон, можно подогреть электроутюгом, проводя им над слоем клея основы на расстоянии 10 мм. При этом следят, чтобы на клеевом слое не образовались пузырьки воздуха. При соприкосновении холодной и горячей поверхностей склеивание будет более надежным.
Наиритовый клей не проникает в поры древесины, вследствие чего клеевой шов несколько слабее, чем, например, при склеивании ПВА или эпоксидными клеями. Применять красноватый наиритовый клей в мозаичных работах не рекомендуется. Для этого следует использовать только белый клей.
Для подклеивания вставок в наборе вместо гуммированной ленты рекомендуется применять клей «Киттификс», который наносят на торцы гнезда или на края вставки. Он хорошо держит набор, не давая ему рассыпаться. Клей при застывании прозрачен; кристаллизируется под влиянием воздушной среды в течение 30–45 с. Удобен этот клей еще и тем, что при его применении процесс шлифования значительно упрощается (лицевую сторону набора слегка шлифуют наждачной бумагой № 15). При пользовании клеем тюбик постоянно следует держать закрытым, иначе клей загустеет и перекроет канал для выхода. Если нет клея «Киттификс», применяют «Мекол». Но время загустевания этого клея несколько продолжительнее, чем время кристаллизации «Киттификса».
Запрессовка и притирание склеенных поверхностей. При облицовывании изделий и наклеивании набора на поверхность применяют струбцины, клиновые или винтовые прессы, притиры и т. д.
В домашних условиях используют ручные механические прессы, изготовленные из металлических пластин или плотных пород дерева (дуба, бука). Пресс с хомутовыми струбцинами изготовляют с таким расчетом, чтобы им одновременно можно было зажать несколько деталей или мозаичных наборов. Размеры основания пресса зависят от размеров набора, подлежащего склеиванию, или детали. В одном случае удобным будет пресс с клиновым зажимом, в другом – на стяжных болтах.
Запрессовку мозаичного набора в хомутовых струбцинах или в металлическом прессе, состоящем из двух металлических пластин (верхней и нижней) и зажимных болтов с гайками, производят следующим образом. На основании (цулаге) размещают основу набора (по размерам цулага должна быть больше основы) с нанесенным клеем. На основу кладут набор, затем лист газеты для впитывания проступившего клея, резиновую прокладку для прижимания всех вставок набора и вторую цулагу. Сверху все прижимают или верхней металлической пластиной (если клеят в металлическом прессе), или хомутовыми струбцинами. Для каждого вида клея необходимо знать режим склеивания и неукоснительно его придерживаться. Отступление от соблюдения этого правила неизбежно приведет к браку при склеивании.